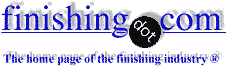
-----
Galvanizing Kettle melted -- why?

Q. I am looking at a HDG kettle where there is heavy pitting (1/2" to 1.0") on the inside wall.
- Katy, Texas
January 6, 2022
![]() |
A. Dear Doug Theall Gunatit Builders ![]() Manjalpur, Vadodara, Gujarat ![]() January 20, 2022 A. The kettle wall gets eroded by dissolving in the zinc it is containing. ![]() Geoff Crowley, galvanizing consultant Crithwood Ltd. ![]() Bathgate, Scotland, UK ![]() January 24, 2022 |
January 25, 2022
Thanks, Ilesh,
I am aware that there are variables that could be the root cause for the pitting. But considering that the steel is per material spec, no dross since the kettle was new and was in the process of the initial charge when the temperature controls apparently failed and the pitting was noticed, and the furnace design is OK (with the exception of the temperature control failure) since it has been in service for many years with no problems. The one noticeable issue was the apparent out-of-control temperature.
Geoff,
Thank you for your reply. It is interesting that there would be such a big difference in metal loss for a seemingly or comparatively small difference in temperature. But that is what I was wondering. With this i know there is more information to be had to support the reason for the pitting.
- Katy, Texas
A. Thanks Mr. Doug Theall for your reply.
As mentioned by you, temp. controller fails....
There is also chances of poor quality of materials as it's not easy to erode steel plate so fast at initial stage. Better check quality of steel plate also.
If temperature goes up, you will notice that by visualizing also but you couldn't know quality of steel plate without inspecting.
Gunatit Builders

Manjalpur, Vadodara, Gujarat
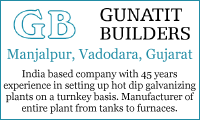
January 27, 2022
⇩ Related postings, oldest first ⇩
Is it possible to electrolytically slow the corrosion of a galvanizing kettle?
A Guide to process Selection & Galvanizing Practice"
by M. J. Hornsby
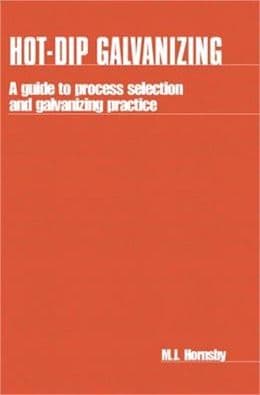
on eBay or Amazon
or AbeBooks
(affil link)
Q. Hi, we are Hot dip galvanizers of small articles in large numbers and use conventional and traditional methods not exactly perfect though. Just an idea ... we also have the problem of the steel pot slowly getting eaten away by the zinc due to dross formation. Is it possible to slow the reaction of dross formation by some electrostatic or electrolytic means? E.g., by applying a voltage across the zinc and the pot?
Dipesh Guptaengineer - Chd, Uttar Pradesh, India
2003
A. How much life are you getting out of your current kettle and how much due you hope to get? Improving your burner system would probably be the best way to extend kettle life. I assume your kettle is made from steel with the proper steel chemistry (kettle steel). Impressing a current to the kettle may not be possible with the high temperatures.
Mike Stroiagalvanizer - Canton, Ohio
2003
A. Regular dross removal and agitation is essential (every 2 weeks minimum). Kettle must be ultra low Si content. Low iron level in flux solution (<1%) helps.
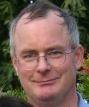
Geoff Crowley
Crithwood Ltd.
Westfield, Scotland, UK
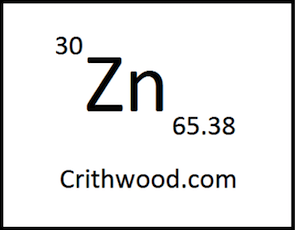
2003
Locating cracks in galvanizing kettle
Q. I am a material science student of university of Lagos, Nigeria. I am presently doing my industrial attachment with galvanizing industries limited. The galvanizing kettle has cracked and it takes a long process to determine the cracks (6days). Is there anything like a crack detector which can tell the exact places of the cracks immediately.
Bukky Lawalstudent - Lagos, Nigeria
2005
A. X-Ray
Tom Gallant- Long Beach, California, USA
2005
Safely emptying the galvanizing kettle
Q. Hello Sir. Our zinc kettle is reported for leakage at several points. We now want to empty the kettle. What is the best and safe technique for this? Once we tried via buckets and then dipping those buckets in water and after that taking the solidified zinc out of the buckets, but it's taking so much time and blasts are also reported when dipped in water.
Khuzafa Rauf- Dammam, Saudi Arabia
December 6, 2011
A. Buckets are NOT a safe way to empty a kettle. You need a pump and if you have holes it needs emptying quickly.
Its a specialist job, and several such specialists exist, some advertise on this site.
And don't cool molten zinc with water. You risk lives being lost!
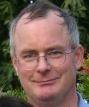
Geoff Crowley
Crithwood Ltd.
Westfield, Scotland, UK
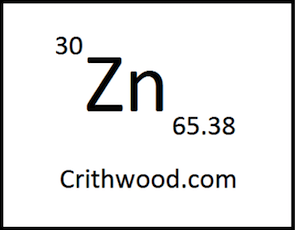
December 8, 2011
Q. Thank you so much for the kind reply sir. Our kettle has been emptied and now we are planning to replace it with the new one. You told me not to solidify zinc with water, apart from the blasts and splashes, is there any other effect on the zinc quality by doing so? Can you kindly refer some book/literature about this very issue (regarding maintenance in HDP) I am a very new person in galvanizing industry and would really love to learn from you. Thanks a lot again for your kind help!
Khuzafa Rauf [returning]galvanizing - Dammam, Saudi Arabia
December 26, 2011
December 26, 2011
Q. Sir:
How many years did your galvanizing kettle last?
Regards,
Galvanizing Consultant - Hot Springs, South Dakota, USA
A. The reason to not solidify molten zinc with water is to avoid trapping water beneath zinc where it can explosively vapourise, forcing the zinc to violently splash.
Zinc so cooled by water is not damaged, and is reuseable, but there are much higher losses due to the higher surface area, and resultant oxidation on re-melting.
So the reason not to solidify with water is mostly a safety one not so much a metallurgical one.
After solidification, water could be used very carefully to speed up cooling, but not too cold or you risk water inclusion in the ingot, and on re-melting this could explode.
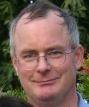
Geoff Crowley
Crithwood Ltd.
Westfield, Scotland, UK
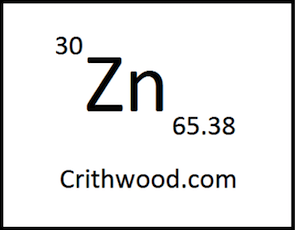
December 28, 2011
by NACE
[only rarely available]
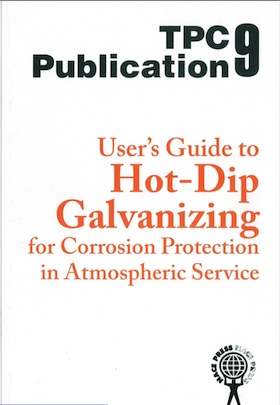
on eBay or Amazon
or AbeBooks
(affil link)
Q. Sir there is a leakage in our galvanizing kettle, we solidified the zinc in that kettle, now we are are going to repair it via weld, is it technically right? your suggestion please
Khizer Abbas- Pakistan
May 5, 2012
Steel galvanizing kettle melted
Q. Dear sir,
Our galvanising kettle inside plate melted during the galvanizing process. For what reason the kettle melted we did not find out. Kettle is manufactured from dead soft quality steel plate. Thickness of plate 40 mm. Please advise me of reason.
- Dhaka, Bangladesh
June 10, 2013
A. There's not enough information in the question to give a meaningful answer.
What tonnage galvanized by this kettle?
What operating temperature?
How many times frozen? For how long?
What actual grade of steel was the kettle?
What material being galvanized? At what rate?
How long a life did the kettle give?
What drossing procedure? (how often, how much)
What flux type?
How heated?
What furnace design?
All this info is relevant, but even then an answer might not be obvious. Answering these "might" reveal a suggested cause.
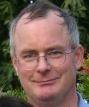
Geoff Crowley
Crithwood Ltd.
Westfield, Scotland, UK
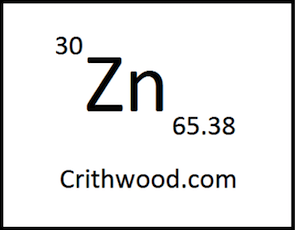
Q. Hi,
A project has been assigned to me on "Fabrication of a Galvanizing Setup". Please can anyone give me suggestions about the materials used for galvanizing kettle?
Student - Karachi,Sindh,Pakistan
January 12, 2015
Q. Hello ! Our new zinc kettle manufactured by steel of CGL is is cracked during initial heating up. The temperature was raised up to 487 °C. What may be the reasons of cracking the new pot ? Please answer.
Saiful IslamMaking CI sheet - Dhaka, Bangladesh
January 12, 2017
Q. Sir,
our zinc kettle was detected leaking in December 2016. the zinc has been evacuated and the leakage points/area have been identified. we gouged (using gouging electrodes) the leaking points/area and fill up the area using super quality welding electrodes imported from india. My questions are:
1. what is an estimate quantity of LPG (Liquefied Petroleum Gas as source of heating the zinc kettle) required to melt the evacuated zinc and new zinc ingots that will be added?
2. how long (days) will it take to melt the zinc for production to start sine we are starting all over again?
3. what is the expected life span of this repaired zinc kettle if we galvanize 40tons of steel per day?
many thanks
- sagamu, ogun, nigeria
January 30, 2017
Your questions appear straightforward, but actually are quite difficult to answer.
1. what is an estimate quantity of LPG (Liquefied Petroleum Gas as source of heating the zinc kettle) required to melt the evacuated zinc and new zinc ingots that will be added?
Many factors can influence this. The efficiency of your burners; insulation effectiveness of furnace, insulation effectiveness during meltout of the surface of the zinc;
2. how long (days) will it take to melt the zinc for production to start sine we are starting all over again?
This is the wrong question, and that you are asking suggests a reason for the kettle leak.
You should be asking what rate of temperature increase should I maintain in a melt-out profile. The answer might be somewhere in the region of 5-17 °C per hour, but with some stopping (hold) points at the two main critical temperatures during this operation.
3. what is the expected life span of this repaired zinc kettle if we galvanize 40 tons of steel per day?
That's like asking "How long will my tyre now last with the puncture repaired? There are so many variables involved that the answer could be from weeks to years.
For example these factors: Residual kettle thickness; zinc chemistry; flux practice, hours of operation; temperature of normal operations; chemistry of typical steel; drossing practice; ashing practice; rate of immersion; rate of withdrawal; stability of temperature; shape of burner flame; existence of protection plates; layout of kettle insulation inside the furnace and so on...
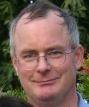
Geoff Crowley
Crithwood Ltd.
Westfield, Scotland, UK
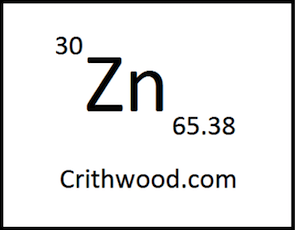
March 28, 2017
Q. Dear Sir,
We were commissioning a new galvanizing plant. Our kettle dimensions 2000 mm width, 2000 mm length, and 4000 mm depth; 50 mm steel thickness with 6 burners.
The representative of the manufacturer of the kettle led our team to do cross fired two burners two hours at one side then off for an hour again; do the same for the other side for two days; then four burners at the third day two hours firing and then one hour off.
On the fourth day midnight the zinc started leaking from kettle bottom. What could be the reason of kettle failure?
The kettle inside walls were rusted before startup. Does it indicates wrong steel grade for Galvanizing kettle?
Regards
- Jeddah, Saudi Arabia
A. Dear Mr. Farooq
Superficially it looks that the Zinc Kettle has gone from its bottom welding. The kettle manufacturing and first few firing is a very sensitive issue. Sometimes Furnace design is also faulty, maybe made localized heating.
My submission:
1. The Zinc Kettle has to be made by [deleted by editor] only.
2. in such a deep furnace, advise to use Flat Flame Burners better to take Furnace from [deleted by editor]. Do not try here and there.
3. Hire a consultant.
- Delhi, India
April 6, 2017
Thank you for your generous suggestions, Mr. Dalela, they are a continuing help. You are welcome to your belief that there is but one competent kettle manufacturer and but one competent furnace manufacturer in all the world, and they're welcome to advertise anywhere they wish, including here, but comment spam is a curse and we cannot post testimonials to, nor slams of, vendors in this forum for a long list of reasons (why?) which we've bored our readers to tears with :-)
Thanks again for the other help.
Regards,
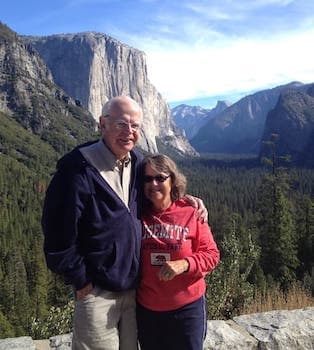
Ted Mooney, P.E. RET
Striving to live Aloha
finishing.com - Pine Beach, New Jersey
April 2017
A. Dear Mr. Mohammed Farouk Abdallah
As mentioned by you, your Kettle Punctured within couple of days, it means Either Furnace Design or Manufacturing of Galvanizing kettle plate or its Design or Welding electrodes or workmanship was too poor.
Better you should consult some of better consultant for the same or hire some better supplier of Galvanizing Kettle and Furnace Constructor.
Gunatit Builders

Manjalpur, Vadodara, Gujarat
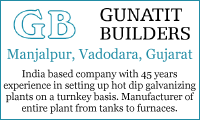
April 22, 2017
April 23, 2017
Q. Dear sir,
We found the leaking point at side wall of kettle. It s 1.3 m from bottom in the sheet itself not at the joint.
Attached hole pictures.
Warm regards,
- Jeddah, Saudi Arabia
Dear Sir.
It looks like your furnace design or Materials for Kettle may be wrong.
Otherwise it will not happen so fast.
Gunatit Builders

Manjalpur, Vadodara, Gujarat
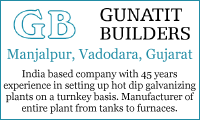
May 21, 2017
December 16, 2017
by NACE
[only rarely available]
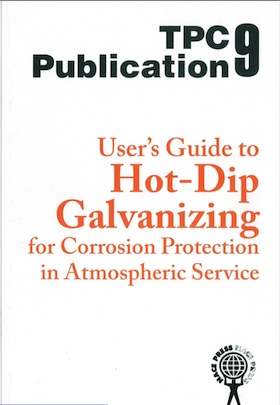
on eBay or Amazon
or AbeBooks
(affil link)
Q. Dear sirs
I need some advise re. HDG process: how to design zinc kettle tank and temperature control methods. And any other methods used in pre-treatment, degreasing, rinsing. Could you please help me.
design - Tamil Nadu, India
Hi cousin Gubendiran. Unfortunately, I don't think your question is actually reasonable...
As a professional engineer I spent 40 years designing metal finishing plants & equipment but, because I don't have experience specifically in hot dip galvanizing, I would not attempt to design galvanizing equipment. Most galvanizing equipment lead designers and consultants have decades of experience in that specific field. And even they encounter problems, as you are reading on these pages.
I think realistically you will need to buy your equipment from a proven source or retain an experienced galvanizing consultant because it isn't possible to compress decades of experience into the 2 or 3 paragraphs appropriate for a public forum. But you can get a few galvanizing books from the library for starters, and we'll leave your question on line and see if readers can suggest starting points. Good luck.
Regards,
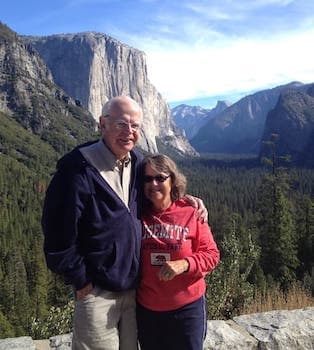
Ted Mooney, P.E. RET
Striving to live Aloha
finishing.com - Pine Beach, New Jersey
December 2017
A. Dear Gubendiran Singaram.
Better you consult some good consultant for Plant and machinery designing of galvanizing Plant.
Its difficult for you to design and do the job -- it's not easy job.
Gunatit Builders

Manjalpur, Vadodara, Gujarat
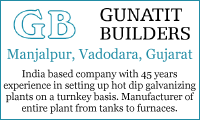
December 27, 2017
Q, A, or Comment on THIS thread -or- Start a NEW Thread