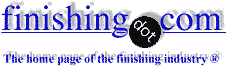
-----
Electroless nickel plating on zinc die castings
Q. Hello!
I have some issues on plating Zinc Die Casting part (Zamak Alloy 5). I called for 8-13um Cu and 10-12um EN (Electroless Nickel). My supplier mentioned that the Cu Cyanide solution used does not need a Copper Strike, it is straight away Cu plating. Can someone tell me what is the difference between Cu strike and Cu plating? I also need the thick Cu for better adhesion on the Alloy-5.
Sojourn [last name deleted for privacy by Editor]2002
A. What issues were you having? Is there a problem with the work as you have receiving it? Are you having an adhesion problem between the copper and zinc? I prefer using a low efficiency copper strike, followed by a full build, high efficiency copper plate (either copper cyanide or acid copper). If you are getting your thickness requirement and good adhesion and all that is being used is a copper strike, then you are getting what you pay for.


Tom Pullizzi
Falls Township, Pennsylvania
2002
Q. I am having some blistering problems for Cu 8-10um, EN 10-13um on the Die-cast part (Zinc Alloy ZAMAK#5). The adhesion between the Zamak substrate and Cu; and between Cu and EN is bad. How can I prepare the Zamak part for plating with good adhesion?
Sojourn [returning]2002
Zinc Casting Fails Salt Spray Test
Q. For the past few months I've tried numerous ways to enable my design to pass a 14 day salt spray test. However, the part has failed time and time again. The part is a small zinc casting with external threads (similar to a wheel lug nut with threads on the outside) which will be produced in high volume. The part must be a silver or grey color to match the other parts in an assembly. I chose to use a zinc casting due to its low cost; a stainless steel part would be far too expensive for this application. Here are the details: The base material is Zinc (Zamac #3). I have been trying different copper and nickel thicknesses anywhere from .0002" to .0007". However, the plating bubbles up and blisters after about 6 days. I've also tried electroless nickel, chromate platings (Cronack, Chromax, Chrome, etc..) and sealants. The SAE nickel spec recommends .001" nickel plating with a copper under-plate, however, the plater cannot plate .001" of nickel on the threaded portion of the part. I've looked into a selective plating process (for varying nickel thicknesses), but it is too expensive. Does anyone have any new ideas?
Thanks in advance.
Brett R [last name deleted for privacy by Editor]2003
A. First cover the surface junk on the die casting with electroplated zinc, then go to a 5 minute strike in alkaline electroless nickel, then top off with the heaviest thickness you can get out of a medium phos acid electroless nickel.
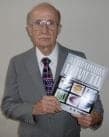
Robert H Probert
Robert H Probert Technical Services

Garner, North Carolina
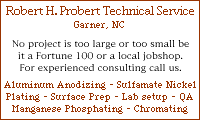
2003
A. Parting line porosity is most likely the culprit. Use a heavy copper strike and fill as much as possible. Maybe try a severe "Pre Bake" to de-gas the parts prior to plate. It sounds like they are small parts so a long pre-bake in a bulk basket may be somewhat efficient.
Andy P [last name deleted for privacy by Editor]2003
Electroless nickel plating on zinc die castings: found black spot
Q. Anyone know what's the reason after electroless nickel plating on zinc die castings, found some black spot on the surface. Some was appear only after 2-3 days.
Stewart Teoh2006
![]() |
A. Stewart, 2006 A. Check copper strike if you used this process John Hu2006 2006 A. There are probably pores in the coating over pores in the zinc that collected and then released small amounts of cleaners and plating bath, which caused the discoloration. ![]() Ron Duncan [deceased] - LaVergne, Tennessee It is our sad duty to note Ron's passing on Dec. 15, 2006. A brief obituary opens Episode 13 of our Podcast. |
Q. I'm using sodium cyanide, rinsing, and uniclean and rinsing for washing. after that acid etch for 30 second. follow by copper strike 30 second and copper plating and then sulfuric acid follow by nickel plating/EN plating.
Stewart Teoh [returning]2006
A. Hello again Stewart,
I agree with Ron Duncan on the cause of your problem. If this is a recurring problem you may want to pull some parts after Cu plating, put them under magnification and inspect for any voids in the copper. As you probably know zinc die-cast should be "sealed" in copper to eliminate open pores in the die cast. If the part configuration leads to any solution entrapment issues, rinsing techniques should be watched carefully. Good Luck!
2006
Q. We also notice this is cause by the pores from the casting. Anyhow, we are trying and thinking is there anywhere we can solve or minimize this at our plating side. Or this can only be done at casting side?
Stewart Teoh2006
Need Electroless Nickel Plating on Zamak 3 Diecastings per ASTM B733
RFQ: Hello,
We need a plater who can plate Zamak 3 castings per spec ASTM B733-04. Line 2.a would be performed at the caster.
March 28, 2008
Ed. note: This RFQ is outdated, but technical replies are welcome, and readers are encouraged to post their own RFQs. But no public commercial suggestions please ( huh? why?).
Q. Can Zamak 3 be plated using Electroless nickel?
Darryl McBrideSeptember 14, 2015
Hi Darryl. The short answer is "yes".
We appended your inquiry to a thread on the subject which introduces the issue that when it comes to industrial plating, the theoretical question of whether something "can be done" usually must yield to the bigger question of whether an adherent, fully functional coating can be applied in a robust & highly dependable fashion at a practical level of effort.
You may have to do a lot of mechanical pretreatment, and you may have to copper plate or zinc plate the casting first, and you may have to 'spark' it (do a few seconds of conventional electroplating first to build a catalytic layer on it). People who know much more about it than me are usually standing by in this forum if you can provide details of your situation. Good luck.
Regards,
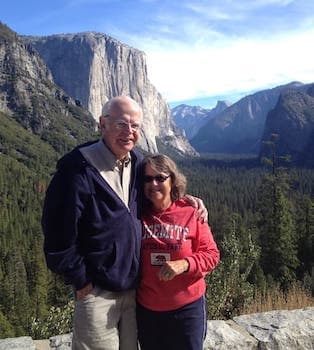
Ted Mooney, P.E. RET
Striving to live Aloha
finishing.com - Pine Beach, New Jersey
September 2015

Q, A, or Comment on THIS thread -or- Start a NEW Thread