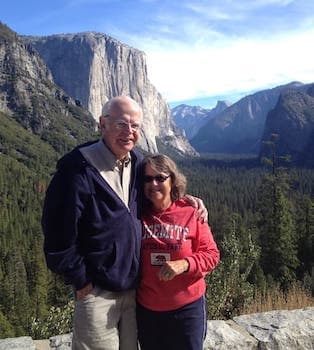
Curated with aloha by
Ted Mooney, P.E. RET
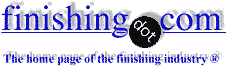
The authoritative public forum
for Metal Finishing 1989-2025
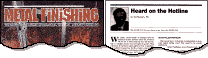
-----
Tin plate Blistering & Peeling

this text gets replaced with bannerText
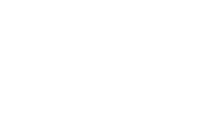
Q. We had a problem in bright tin jigging, the steel material was plated, after finishing plating and packing, bubbles appeared in the material area both at high current and at low current. We tried to peel off the bubble and we measured its thickness, from the results of checking the copper layer was also peeled off. We have tried various methods but cannot avoid the bubble. We have adjusted the parameters of each chemical and additive to the standards, we have anticipated any suspicions of over-additives by carrying out a dummy, we have anticipated any suspicions due to sediment in the plating tank with a filter. How do bubbles appear? I really need help or advice to solve this problem.
Thanks
Chemist Lab - Batam, Indonesia
February 16, 2024
A. Hi Astri,
Please read the earlier posting here and the linked thread to assure yourself that the problem is truly blisters rather than blobs. If it is blisters, scrub a few parts with a pumice
⇦ this on
eBay or
Amazon [affil links] and detergent solution and a tampico scrub brush
⇦ this on
eBay or
Amazon [affil links] before putting them into your process line as a way of proving that it's not a cleaning problem.
Luck & Regards,
Ted Mooney, P.E. RET
Striving to live Aloha
finishing.com - Pine Beach, New Jersey
⇩ Related postings, oldest first ⇩
Q. Copper strips plated with 100-300 micro inches of pyro-copper then pure tin plated parts pass tape-bend-blast test but when a teflon coat is applied the tin lifts off heated to 350 ° for teflon, the copper is black when tin is removed with teflon but if you strip the tin, copper is nice looking.
Daniel Caseyplating shop - EVERETT, MASS, U.S.A.
2005
A. I waited a while to respond, hoping that some more qualified metallurgist would sound off. I am a little out of my area here but in absence of any other advice here is my 2 cents:
At the temperature you are curing the Teflon the copper and tin and organic plating additives are fusing and cooking together to form some sort of brittle and black intermetallic that is falling apart when you peel.
Try a nickel or palladium diffusion barrier between the copper and the tin, but be careful as tin will also diffuse into nickel.
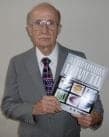
Robert H Probert
Robert H Probert Technical Services

Garner, North Carolina
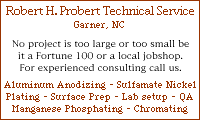
A. There is not enough information here to really answer the problem. However, it could be that the tin layer is too thin and porous. You do not say what type of tin you are putting down or whether it is flow melted, etc. Unless it is pore free, it will allow gases to seep through onto the copper and react there, especially if the metal is heated to 350 °C. Secondly, tin has a melting point of 232 °C, so heating it this high will cause the diffusion of tin into the copper to go very quickly. This will form an intermetallic compound of Cu-Sn, which could also account for the blackening. This compound will be quite brittle.
I suggest you try this: take your tin plated copper and put it through the PTFE process, but DO NOT put any PTFE down. Then heat it to 350 °C for the same time and see how the adhesion and bend tests stand up. If the same problem occurs, it will be the processing; if it doesn't, the problem lies with the PTFE. Perhaps more information will be beneficial to solving your problem.
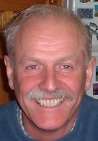
Trevor Crichton
R&D practical scientist
Chesham, Bucks, UK
2005
Q. Why do you think that the tin plating is too thin? What is its correlation with plating peel off?
Lea Cabelizaemployee - Sto. Tomas, Batangas
October 12, 2021
for engineers, shops, & specifiers
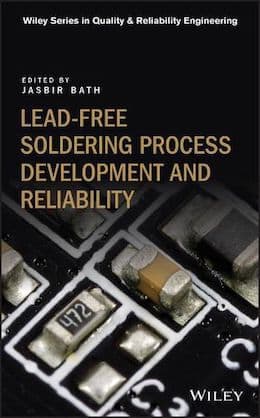
avail from eBay, AbeBooks, or Amazon
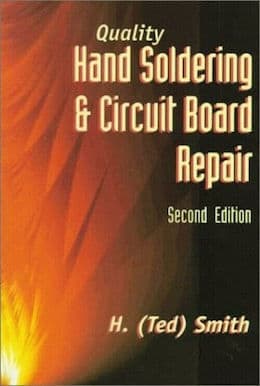
avail from eBay, AbeBooks, or Amazon
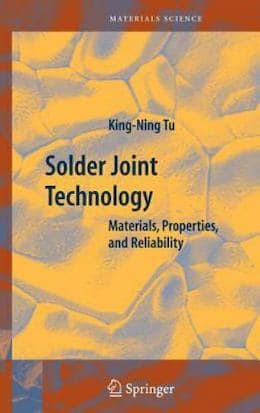
avail from eBay, AbeBooks, or Amazon
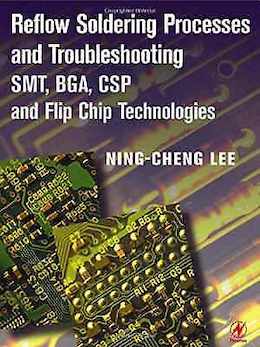
avail from eBay, AbeBooks, or Amazon
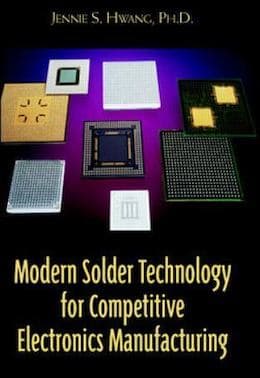
avail from eBay, AbeBooks, or Amazon
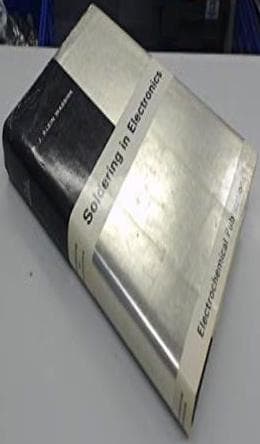
avail from eBay, AbeBooks, or Amazon
(as an Amazon Associate & eBay Partner, we earn from qualifying purchases)
Q. Hello out there.
We are having problems on a tin electroplated breather tube which is soldered to a terne coat fuel tank.
The tube is steel with a copper flash deposit followed by a tin plate of 15 microns. When soldering, using oxyacetylene and solder wire, the plating adjacent to where the solder is applied blisters into bubbles of tin depleting the surrounding areas. The final result looks like sweat drips.
Previous parts used a thinner coating of tin which did not experience this problem.
Is the blistering a function of coating thickness?
Is it caused by dissolved gas or porosity?
Would it be beneficial to drop the copper flash?
Thanks in advance for all replies.
Melbourne Victoria Australia
2006
A. Hi Graham, I tried to answer a very similar question on thread 49424, only to learn from Mike Berrier a lot more than I taught :-)
The first thing to determine, as you will see on that thread, is whether you are actually seeing blisters or you are actually seeing blobs -- because the causes are different. If it's blobs, it's most likely an excess of brighteners/organics in the tin plating ... and it makes sense to me that thicker plating will probably involve more organics based both on just more of it with thicker plating, and the fact that more organics may be required or perceived to be required to get smooth bright plate when it's thicker. Good luck!
Regards,
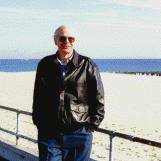
Ted Mooney, P.E.
Striving to live Aloha
finishing.com - Pine Beach, New Jersey
Multiple threads merged: please forgive chronology errors and repetition 🙂
Bad adhesion of tin plating on copper plating
Q. I am plating nuts that get .0003 in. of bright tin; my under plate is acid copper. I run these in a barrel at 5 ASF. Every time I plate these parts I have tin or copper flaking and what not. Can you help to solve this problem?
Ryan Smithplater - Coon Rapids, Minnesota
2007
A. If I read your question correctly, you have a problem with the cleaning and activation of the part or of the copper. If the copper flakes off with the tin, the problem is the copper plating cycle. If not, it is the activation of the copper for the tin plate.
James Watts- Navarre, Florida
2007
Q. I am a plating engineer in IC manufacturing. Our process is pure tin plating using rack automatic plating machine. Sometimes we are experiencing plating peel-off on our work, but what surprises me is that in a 2016-unit lot, there are only 2-4 units with peel-off. To think that these 2016 units underwent the same process and pre-treatment is very strange.
Please comment on this post if you are/have experienced this before and what were your actions to prevent such.
plating engineer - Clark, Philippines
June 24, 2011
A. Hi Charie,
Not sure peel off is happened right after tin plating or trim & form. If peeling around lead bending area after trim & form, then could be due to too small and/or irregular tin grain size arise from imbalance of additives and/or organic/metallic contamination inside tin plating solution.
If peeling right after tin plating, then you may focus on pretreatment esp. mold deflash & mild etch to ensure IC substrate is free of mold flash and/or other residues prior tin plating.
Regards,
David
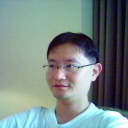
David Shiu
- Singapore
Q. Hello.
In the plating process Ni-Cu-Sn I experience big problems with weak adhesion between Cu and Sn. I am using cyanide copper. After new setting the adhesion between Cu-Sn is very good, but after some time (approx. 1885 m2 of treated area) the adhesion suddenly falls.
Any ideas what causes this phenomena?
Thank you in advance
Ziva
- Ljubljana, Slovenia
November 29, 2013
A. Hello Ziva,
If this problem is strictly the Sn peeling from the Cu underplate, I would suspect that either the Cu is allowed to oxidize before Sn plating, or there is insufficient rinsing between the cyanide Cu plate and Sn plate. As you know, cyanide solutions leave a slick film on parts that must be removed. You didn't mention what type of Sn plate pre - dip you are using, or the type of Sn bath. If you could list your process steps we may be able to help you more.
Process Engineer - Malone, New York, USA
December 9, 2013
A. Copper is a serious contaminant to alkaline tin plating. For years I have tried to convince people that a "tin strike", acting as a "sewer" to leave the copper behind, would pay for itself, but all those guys who know more than me will not do it.
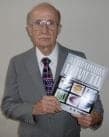
Robert H Probert
Robert H Probert Technical Services

Garner, North Carolina
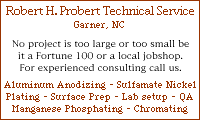
Q, A, or Comment on THIS thread -or- Start a NEW Thread