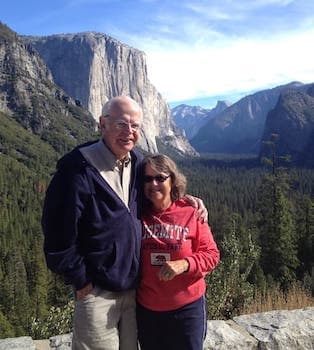
Curated with aloha by
Ted Mooney, P.E. RET
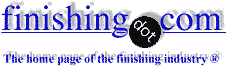
The authoritative public forum
for Metal Finishing 1989-2025
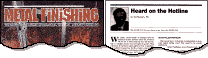
-----
Tin plating over copper blisters at 240 °C
July 23, 2008
Requirement is Sn plating over Ni plating over CuSn6
Tin 3 micron
Ni 3 micron
Phosphor-Bronze 0.15 mm
But when used at 240 °C surface has blistering
How to solve this problem?
What is the best method for this plating job?
Customer - Lamphun, Thailand
Hi, Aviruth.
If you or I were asked to "Design a very easy quality control test that will quickly locate all poorly plated parts, regardless of whether the problem be due to poor substrate condition, inadequate cleaning, lack of activation, excessive brightener in the nickel or tin plating tank, overstressed nickel plating, or anything else", the closest we could get to such a quick universal test would probably be to bake the parts to 240 °C and look for blistering :-)
A. So, when you see that the parts are blistering and you'd like to know where the problem lies, you can see that the trouble could be nearly anywhere. Probably the first question should be at what interface is the blistering occurring? Carefully break some blisters and look at the back of the blister and the base underneath the blister.
Does the blister occur between the copper and nickel or between the nickel and tin, or a bit of both? Is there any peculiarity about the location of blisters on the parts? Are they everywhere, or only on flat surfaces or only on edges and corners, or top or bottom surfaces. Unfortunately, while blistering tells you that you have a problem, it doesn't tell you at what step. Good luck and get back to us with more detail.
Regards,
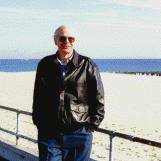
Ted Mooney, P.E.
Striving to live Aloha
finishing.com - Pine Beach, New Jersey
July 23, 2008
A. I would recommend first confirming that what you are seeing is in fact blisters. As Ted noted, you may see this with high organic matter in the nickel or tin. If there is high organic matter on the surface when the tin reflows, which it will at that temperature, it will cause tin pooling or puddling. This is a blob of tin that accumulates like a water drop on the surface but looks just like a blister. I would use a scalpel to pull back the "blister" and see if it flakes, it not, it is probably more likely the problem that I described.
Mike Berrierselective - Addison, Illinois
July 25, 2008
Q. Actually, yes this is a blob of tin that accumulates like a water drop on the surface but looks just like a blister Mike Berrier is correct.So can you advise what is the root cause?
Aviruth Piwkao- Chiangmai, Thailand
July 27, 2008
A. You have too much organic in your bath. There is a high amount of carbon in the deposit and when the tin reflows you are getting puddling in the areas that concentrate the carbon. The organic in the tin plate is grouping together. Your best bet is to lower the organic in the bath. Try aggressively carbon filtering the bath and then plating. Talk to your additive supplier and see if he has recommendations. Maybe he has a lower organic additive that can give you a more pure deposit.
Mike Berrierselective - Addison, Illinois
July 29, 2008
Very I nsightful answers, Mike! Thanks.
Regards,
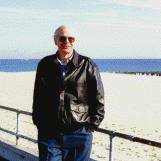
Ted Mooney, P.E.
Striving to live Aloha
finishing.com - Pine Beach, New Jersey
Q. Hi All,
Recently we have encountered very frequent blistering on our product. We are doing tin plating over copper based leadframe in strip to strip form. Blisters were seen only after baking process 165 °C and the position was always localized at the bottom row that is opposite the gripper or belt clip position. We are using alkaline electrolytic deflash, followed by acid descaler and cathodic acid dipping prior to plating cell. Could you advise what is the problem here. Thank you
- Jakarta, Indonesia
December 28, 2012
![]() |
A. "Cathodic acid dipping" is probably loaded with tin and copper which is deposting and not bonding. Recommend you make up a new pre-acid dip and do not use any current. Also a "tin strike" to cover up the copper would help prevent leaving copper in the tin solution. ![]() Robert H Probert Robert H Probert Technical Services ![]() Garner, North Carolina ![]() December 31, 2012 A. Hi Rika, ![]() David Shiu - Singapore January 2, 2013 |
Tin plating defect
Q. My situation:
Pure tin plating on copper leadframe. There was some bubbles made on the plated leadframe. But the defect rate is 3/200 leadframes plated.
Sorry if there is lack of info I shared but any of you faced this problem before?
- Perak, Malaysia
July 18, 2018
July 21, 2018
A. Dear Farisha,
Please investigate further with defected parts.
Possible causes & remedy as below.
1) Poor cleaning - Improve pre treatment
2) Electrical contact disturbance - Check the electrical contacts
3) May raw material composition - rarely improper material composition may cause.
Thanks
- Electronics City, Bangalore, India
Rejects vs. defects
Question:
Hi all, just wonder is unit with plating blister/blob reject or a defect?. Anyone can share the general defect criteria? Thanks in advance.
- Batam, Indonesia
June 19, 2019
A. Hi Andrew. Thanks for the interesting question from which I hope to learn as well. To me, a 'defect' is anything which is not exactly the way it is supposed to be. Any blister or blob is certainly a defect. A 'reject' is something that you have decided is sufficiently defective that you will not ship it (sometimes called an internal reject) or that your customer will not accept (sometimes called an external reject). I think all blistered parts should be internally rejected but would need clarification on 'blobs'.
I googled "reject vs. defect" to check semantic differences, the approaches in other industries, etc., and I didn't immediately see any reason yet to change my mind.
Let me relate an old story to clarify. A bigwig at a power tool company decided that a component of the power tool which was made of diecast aluminum with a deep hollow should be nickel-chrome plated instead of powder coated as an anniversary celebration. The plating shop could not do it with sufficient reliability for a number of reasons like cold shuts in the diecastings, inability to remove all the swarf in the deep recesses, etc. I sat at the conference table -- with the plating shop saying they could not possibly ship these blistered parts, but the tool company project manager insisting they were shippable as long as the blisters were on the "B" surface ... and of course the "A" surface grew ever smaller and the "B" surface ever larger as he resolved to meet the bigwig's orders. This was an example of parts which were very seriously defective, and did not pass the internal reject test, but were shipped anyway because they met the customer's needs. Hopefully it helps clarify what the words mean :-)
Regards,
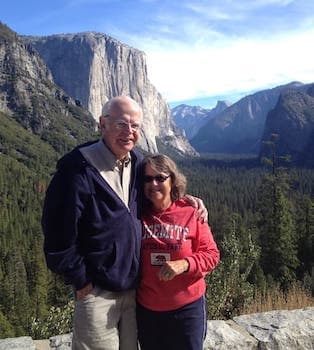
Ted Mooney, P.E. RET
Striving to live Aloha
finishing.com - Pine Beach, New Jersey
June 2019
Q, A, or Comment on THIS thread -or- Start a NEW Thread