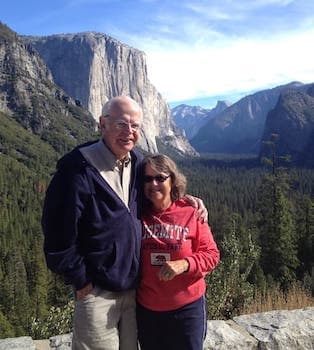
Curated with aloha by
Ted Mooney, P.E. RET
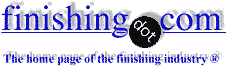
The authoritative public forum
for Metal Finishing 1989-2025
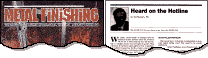
-----
Problems in Acid Chloride Zinc Plating

< Prev. page (You're on the last page of this thread)
Q. WHAT IS THE SOURCE OF IRON CONTAMINATION IN ACID ZINC PLATING OF CAST IRON?
WHAT IS THE RELATION OF IRON CONCENTRATION WITH pH?
THE BEST pH FOR THE LEAST IRON?
CROUSE CO - tehran,iran
June 17, 2017
A. Hi Asghar. The largest source of iron is usually a part which has fallen off the plating rack and is sitting at the bottom of the tank, dissolving in the acidic plating solution. I could be wrong but I don't think people tweak their pH up and down to try to control the iron content in an acid zinc plating bath.
You perhaps need to fish parts off the tank bottom, make sure no burrs of cast iron are being knocked off your parts in the plating tank, clean your filters to make sure no iron particles are dissolving in them, and do a peroxide treatment? Good luck.
Regards,
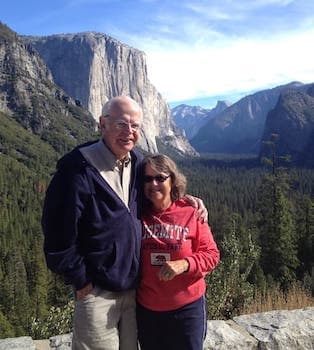
Ted Mooney, P.E. RET
Striving to live Aloha
finishing.com - Pine Beach, New Jersey
Q. Hello Sir,
Can we achieve 10 micron filtration with acid zinc chloride filters using horizontal discs instead of cartridge filters?
Best Regards,
Aditya V. Guptawire & allied industries - Punjab, India
February 4, 2018
Q. What is oilout phenomena in acid ammonium chloride mix zinc bath? I am plating castings in this bath. Bath capacity is 1300 ltrs.
How to treat this and avoid recurrence?
Will this have any effect on Salt Spray Test?
- Pune, Maharashtra, India
April 22, 2018
A. Hi Ramnath. Please see our on-line library article "Improving Your Chloride Zinc Plating Operation" where Stephen Schneider tells us the causes and preventions for oilout, including excessive temperature and putting your additions all in one spot, resulting in over-concentration.
As for salt spray testing, its purpose is to alert you that the process got out of control; since you already know that it has, conducting a salt spray test doesn't seem helpful. If you are asking whether parts which were processed wrong will still pass, sorry, I don't know if salt spray testing is sensitive enough to catch this problem :-)
Regards,
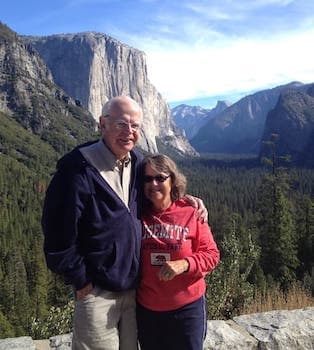
Ted Mooney, P.E. RET
Striving to live Aloha
finishing.com - Pine Beach, New Jersey
April 2018
Hull Cell/Barrel Line Disconnect
Q. My situation: We have a chloride zinc barrel line (potassium) that shows normal quality brightness of stampings, yet the hull cell shows a uniform dullness that presents as severely low brightener.
Since the hull cell calls for brightener, operators add it, and the parts quickly become flaky and blistering, which is a sure sign of high-brightener.
What situations could explain this disconnect?
Are there normal contaminants that could act as a brightening agent?
Consultant - Versailles, Kentucky, USA
July 2, 2018
A. Hi. I think the most likely thing is something wrong in the Hull Cell plating procedure like a defective rectifier for the cell, a miscalculation of required amperage, etc. This is a standard 267 ml cell?
Regards,
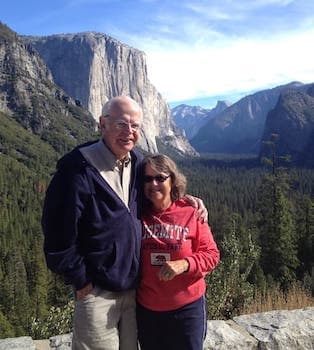
Ted Mooney, P.E. RET
Striving to live Aloha
finishing.com - Pine Beach, New Jersey
July 2018
Q. No issue with the Hull cell operation. The panels respond correctly as additives are adjusted. As-is solution reflects no brightener at all.
Keith Bowers [returning]- Versailles, Kentucky, USA
July 2, 2018
Ammonium chloride + zinc chloride coating problems
July 29, 2018Q. Hello,
There are 5 tanks, except passivation and oil rust removal tanks.
Prescription:
Ammonium Chloride: 165 gr / lt.
Zinc Chloride: 65 gr / lt.
Carrier: 4%
Brightener: 2%
Due to the misting and adequate coverage of the products, I made a new tank in accordance with the prescription in a university thesis. (I found a similar recipe on the forum). New recipe:
Ammonium Chloride: 135 gr / lt.
Zinc Chloride: 22,5 gr / lt.
Carrier: 4%
Brightener: 0.2%
But now the problem of fogging has increased much more. Completeness problems began to emerge. I saw black burns in the areas where there was a low level of entrainment when the product exited the passive.
I increased the amount of carrier slightly (0.7%). But I could not solve the problem of assertiveness again. I now increase the amount of zinc chloride by 0.8%.
(click on thumbnails for higher rez pics)
Now these black burns appear before passivation.
I need your referrals on the subject.
- Oryol / Russia
A. Hi Axmet (apologies but your name came through with Russian language characters that our English e-mail and browser system made a mess of).
Thanks for the photos. It looks to me like you are zinc plating assembled step ladders, or something similar, and that the problems are in the paint tray area. Am I understanding it properly? Is there a possibility that the current flow to this area comes only through the rivets or hinge pins and they are not reliably conducting?
Unless it's just the lighting, it looks like half of the plating in two of the pictures is charcoal grey instead of bright, which is definitely a problem occurring in the plating tank, whether it be formulation or inadequate current to those areas. I can't easily identify other defects, with the exception of the large 'black spot' which could be a burn from the component touching the anode; but there also looks to be small black spots, which per my guess, would indicate that inadequate cleaning or pickling is also a problem (perhaps again due to poor contact during electrocleaning).
Please research the subject: "Hull Cell" on this site or other sites. It's usually not a good idea to make up or adjust the concentrations in large tanks from theoretical or book knowledge. Rather, you probably should use a Hull Cell to make up a tiny 267 mL volume, then electroplate small sample plates, and see how they look across the whole current density spectrum, make necessary adjustments, and then scale up those results. I think Hull Cell testing is your fastest way out of this problem short of possibly trying an electrical jumper to the paint tray area. Good luck.
Regards,
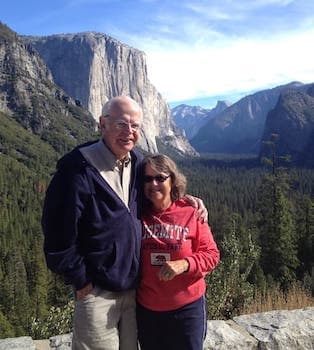
Ted Mooney, P.E. RET
Striving to live Aloha
finishing.com - Pine Beach, New Jersey
July 2018
Remove titanium contamination from acid zinc plating bath
Q. I service an ammonium chloride zinc barrel line that has been severely over-rectified recently, creating organic burned (oiled)-out and dissolved titanium anode baskets.
We've recovered from the oil, but still find high levels of titanium (33 ppm). My question is twofold:
1. Will this amount of titanium create any plating issues, defects, or efficiency changes?
2. How can I remove it efficiently?
Technical Service - Versailles, Kentucky USA
September 19, 2018
Q. What happens if my zinc chloride is at 60 g/l and it rises to 80 g/l?
Luis bacastudent - tijuana mexico
January 9, 2019
A. Hi Luis. We might be having some language or translation difficulties but -- although you may add zinc chloride to the bath -- you wouldn't normally titrate or analyze for "zinc chloride", you analyze for zinc and you analyse for chloride. I'm not sure quite what 60-80 g/l of zinc chloride in the analysis would mean ... surely you have at least several times as much chloride in the bath as those numbers translate to?
Maybe you are expressing the zinc content in terms of what it would be if all the zinc were zinc chloride, in other words, 48% x 60 to 80 = 28.8 to 38.4 g/l of zinc = 3.84 to 5.12 oz/gal of zinc? Please try your best to explain your actual situation, what actually happened, rather than posting a hypothetical. Usually acid zinc has the rather opposite problem of growing in volume rather than concentration. Thanks!
Regards,
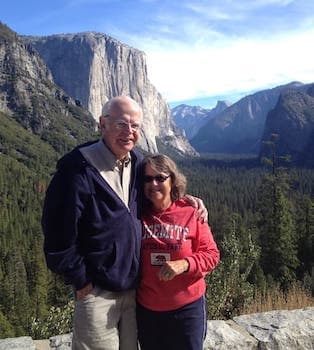
Ted Mooney, P.E. RET
Striving to live Aloha
finishing.com - Pine Beach, New Jersey
January 2019
How to analyze/titrate a mixed ammonium chloride & potassium chloride acid zinc bath
Q. Hi,
I want to ask how to calculate by volumetric/titration method the mixed ammonium chloride and potassium chloride in acid zinc bath. Because our customer has an acid zinc bath consisting of zinc chloride, ammonium chloride mixed with potassium chloride. We want to know a procedure to calculate each of the components in their bath solution by titration method. Thanks
Chemical analyst, SCA PT., - Jakarta, Indonesia
February 15, 2019
White layer forms during acid zinc plating but not on Hull Cell panels
January 9, 2020Q.
Hi, I write from Italy.
In my company we have an acid zinc bath 12000 lt.
For a month now our problem has been that during the electrodeposition a white layer forms on the piece that we are unable to remove.
Our problem is that in the laboratory the Hull Cell does not show any problems.
Has anyone happened?
Thank you for taking the time, for those who will read and reply.
- MODENA, ITALY
A. Hello Anna, have you tried cleaning your zinc anodes in the plating bath? How is the thickness of the deposit when this problem occurs? Has your pre - clean process changed and are all chemicals within spec? Unfortunately many times the cause of a plating problem cannot be zeroed in on one particular defect in the process. You can also send out some parts to a reputable lab that has XRF capabilities. It's also possible that your zinc supplier can get it done for you. Good Luck and hope you get your problem solved.
Mark BakerRetired - Winston Salem, North Carolina USA
January 10, 2020
A. First try entering the plating tank "hot". Then, in case where other racks are already in the tank, look for galvanic voltage on the new rack just before it makes contact. Then with an ohmmeter, check each anode connection.
Finally, if more than one rack is in the tank, watch the ammeter and note if one rack is not continually making contact and thus causing a "bi-polar" effect on the rack with the white film.
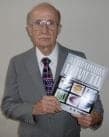
Robert H Probert
Robert H Probert Technical Services

Garner, North Carolina
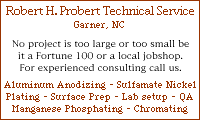
January 16, 2020
January 17, 2020
Q. Thank you gentlemen for replying.
We tried them all. We started with 25 kg of potassium permanganate
⇦ this on
eBay or
Amazon [affil links] to drain the tank from any impurities.
We cleaned the zinc baskets and replaced the bags around them.
Replaced current rectifiers. Having never had the problem we went for exclusion.
Ironically, my brother tried to put 5 liters of ethanol into the tank.
The coating has improved but we have not understood if ethanol helped to bind some crazy molecule or improved the wettability of the pieces or it was a coincidence.
We have replaced the passivation at the end of the line.
At the moment we have not yet resumed our work rhythms but we are getting closer.
I am attaching some photos of our works.
Thank you all and sorry for my english.
- MODENA, ITALIA
September 25, 2020
Q. Hello
I am a manufacturer of fasteners. The problem I am facing is related to acid zinc plating. After parts come out of barrel are bright and shiny but Post trivalent dip and drying, they appear dull and lose their brightness. And also develop film of white powdery type which can be wiped with a slight touch. These parts when sent to customer and when opened are found to be heavily rusted.
Please guide where am I going wrong and help me with the solution.
Thank you
- Hyderabad Telangana, India
A. Hi Kapil. The parts being rusted when received indicates that either they were not packaged fully dry, or the packaging material is improper, or the plating is not thick enough. It looks like you are packaging the fasteners in large plastic (visqueen?) bags, which will hold in any moisture if they aren't bone dry.
There could be a number of causes for an appearance problem after chromating but not before: from excessive brightener to badly made up trivalent, to bad post-chromate sealer, to possibly a need for a nitric acid dip before chromating, etc. But I think the first issues are how thick is the zinc plating (nominal, minimum measured)? And have you done, or can you do, a Hull Cell panel to see if it gives a clue about brightener levels/residues?
Luck & Regards,
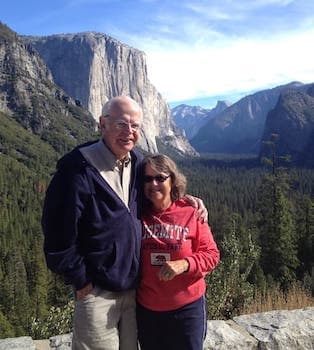
Ted Mooney, P.E. RET
Striving to live Aloha
finishing.com - Pine Beach, New Jersey
September 2020
Q. I think that the most likely cause is that the rivets - which have a blind hole - weren't fully dry. A 'quick and dirty' test is to put some of the finished parts in a Ziplock (r) bag, seal it and let it sit for a few hours. Or in an oven for a few minutes. Condensation on the inside of the bag is a very, very bad sign.
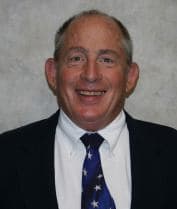
Tom Rochester
CTO - Jackson, Michigan, USA
Plating Systems & Technologies, Inc.

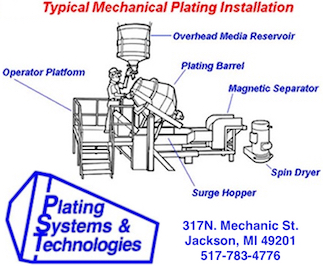
September 28, 2020
Q. I am plating some small parts with acid zinc plating, I am controlling all the parameters and trying to go with vendor's instructions. Until today everything was working fine, but today I was barrel plating a Disc shape part, the deposit looked shiny, the thickness was correct as predicted, but I had some problem with the edges of the part which was not coated.
The part is like a quarter coin. Any suggestion or idea?
Thanks for your help
- Austin, Texas
October 9, 2020
A. Hi Hamid. In general, edges should plate as much as the faces, maybe more. Please tell us what the substrate is -- low carbon steel or what? Is there a possibility that these disks were laser cut, or that there is some other explanation for the character of the edge to be different than the character of the faces? It sounds to me like the edges may not be in plateable condition.
Luck & Regards,
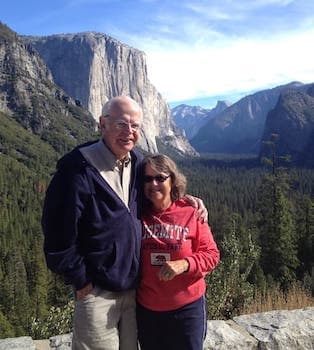
Ted Mooney, P.E. RET
Striving to live Aloha
finishing.com - Pine Beach, New Jersey
October 2020
October 9, 2020
Q. Hi,
Thank you for your kind response.
The part is a magnet composed of Rare earth elements mostly Fe.
I had some good deposit on rectangular and cube shape parts and had no problem on the edges.
I am thinking to reduce the rotation speed of the barrel.
I run the Hull Cell test and all were good.
Thanks and best regards
- Austin, Texas
Q. Reduce zinc chloride in chloride zinc bath?
The zinc chloride level has risen to 6.5 oz/gal in our chloride (ammonium/potassium) plating tank (25 oz/gal). The anode baskets are quite heavy and can't be removed easily to stop the leaching of the zinc balls when not running. Besides cutting the solution to dilute the zinc is there a way to filter or chemically treat the tank to lower the zinc solution?
Nico Cottone- Cincinnati Ohio
April 5, 2021
April 12, 2021
Q. We are facing white patches in our plating bath, and in order to overcome that we have given zinc dust ⇦ this on eBay or Amazon [affil links] treatment, carbon treatment and hydrogen peroxide -- but still the issue remains. Even the pH is within range and all the chemicals are in range. Those patches when dry are forming a foggy stain on the part. Please suggest a solution to overcome this issue.
- Chennai, Tamilnadu, India
A. Hi cousin Arun. I understand a feeling of frustration when you feel that everything is in spec but the result isn't right ... but it can leave readers thinking "if everything is already correct, how can I possibly help? :-)"
So it's probably worthwhile to give us more data. What is the material we're looking at, what is the plating thickness and is that calculated or measured? You say "when dry" but is that a day later or are you using ovens of XXX °C for the drying, or applying some other technology to the drying. Are there any specs on the conductivity or other parameters of the final rinse? Have you tried to observe any parts before chromating? Is there a nitric acid dip before chromating? Are any Hull Cell test panels available? Thanks!
Luck & Regards,
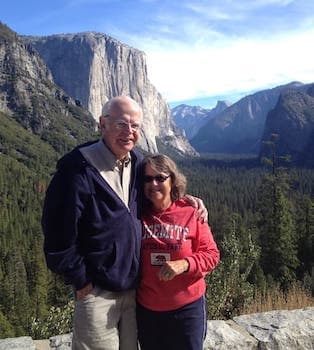
Ted Mooney, P.E. RET
Striving to live Aloha
finishing.com - Pine Beach, New Jersey
April 2021
Q. The material is sheet metal and expected thickness is 8 to 14 microns, little confused with what could be issue for such fogginess in appearance. Because this happened just in the plating bath itself.
- Chennai Tamilnadu, India
April 15, 2021
May 21, 2021
Q. Hello everybody. I'm actually a bit frustrated, because I can't remove this condition in my high-density zone in the hull cell.
Believe me the parameters are fine. I have my pH at 5.7, Boric Acid 33 gr / lt, Total Chlorides 155 gr / lt and my zinc metal at 34 gr/lt.
I did the Hull Cell test because I have this problem on my line.
Add approximately 100 grams of potassium permanganate to a 2800 liter tank. and I saw no changes. Then add about 100 grams of activated carbon to see if it was an organic contaminant. and I didn't see any difference either ...
The temperature of my bathroom runs between 26 to 30 °C.
Someone to give me advice or know what I'm doing wrong.
Thank you all. Erick Cruz
- MatamorosvTamaulipas Mexico.
A. Erick,
Great introduction to explaining and sharing parameters if the bath. However, you are not describing the condition of the plating? Based on the photos I am assuming you have a cloudy/milky deposit? Do you see this condition before or after Chromate/Passivate? Are you using a 'sour dip' prior to Chromate? All general rules of thumb for bright aesthetic zinc, and obviously rinsing is key. If you feel as if all parameters shared are within optimum range fir your operation, I would suggest kicking in a large dose of brightener. The disadvantage to most acid zinc solutions is loss of brightener by drag out, amp-hour consumption, and just simple dissipation by air, idle-time, & the big one 'temperature'. Even the high temp brightener systems tend to lose concentration over time. 7 times out of 10, a nice slug of brightener does the bath some good. Try it in a Hull cell first, of course. It doesn't appear that you are battling organic contamination, but a carbon polish will always benefit any plating solution. Good luck! I will try to keep an eye on this thread, I know some folks down your way that can help if you haven't gotten this under control.
- North Carolina
May 27, 2021
June 17, 2021
Q. Hi everyone, I hope you can help me solve my zinc acid bath problem.
A new zinc bath is generally done with
70 gr / l of zinc chloride
170 gr / l of potassium chloride
30 gr / l of ammonium chloride
The problem is created for me by working, that is zinc chloride always tends to increase its concentration even exceeding 100 gr / lt and this involves great difficulty in electroplating the material and I am forced to make a "cut" by eliminating the 20 / 25% of the zinc bath to bring the values back to normal, about once a year.
Is there any way to avoid this?
- Emilia Romagna Italy
Q. My Zinc plating bath pH was at 6.53 so I asked supplier advice on acid add to reduce pH. He suggests adding concentrated HCl mixed in water and add to tank, but not an amount. He says it's not an exact science, add a little and give time to mix, check pH, adjust. So I looked through our historical data and see they have added 150mL concentrated HCl previously in a 738L tank. So I add 150mL HCl at end of day and check the next morning (12+hours to mix), take sample, pH 6.76. EMail supplier to inquire "Is this normal?" "what can cause this to happen?" he answers "sometimes the pH goes up before it comes down, add more HCl and check again". Added additional 150mL concentrated HCl end of day, come in this morning, pH 6.55
Can you help me understand what's happening in my small tank? We have larger tanks and 40mLs of a weak acid can blow out the tank, how can 300mLs CONCENTRATED HCl not affect this tank and in fact raise the pH?
lab tech - Blairsville [Pennsylvania]
October 22, 2021
A. Hi TinaMarie. Is it possible that parts have fallen off a rack and are dissolving? If not, is this a lined steel tank in which the lining has possibly become compromised? Is it possible that there is a second shift running that it doing something and not reporting to you?
Luck & Regards,
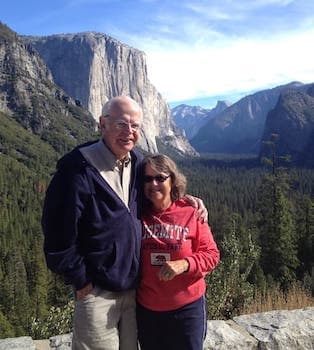
Ted Mooney, P.E. RET
Striving to live Aloha
finishing.com - Pine Beach, New Jersey
October 2021
October 22, 2021
Thank you for your quick response.
Q. No parts have fallen off (to the best of my knowledge) and that line gets shut down after daylight, so no second shift action.
My boric acid buffer is at 3.2 (range 3.0-4.0), could this affect my pH misbehavior?
lab tech - Blairsville [Pennsylvania]
A. Hello,
Many times it happens that the pH meter is not working properly, or not calibrated, or calibrated with the wrong pH Buffer solutions. Check into that.
Also you may want to double check your boric acid content. This pH is way too high for an acid zinc bath.
Chemical Engineer - Bucharest
November 1, 2021
Q. My first time to use acid zinc/potassium chloride. I am seeing plated items look whitish oxide on surface after drying, why? Also, consumption of brightener is extremely high, why?
Harrison mwangi muturi- Nairobi _ kenya
December 1, 2021
A. Hi Harrison. Re. "whitish oxide" please tell us about your chromating step and your drying step because it sounds like corrosion (although I suppose it's vaguely possible that it could be precipitated boric acid).
? You say that consumption of brightener is extremely high, so why are you choosing to add so much? What is your indication that you need to add the amount that you are adding?
Luck & Regards,
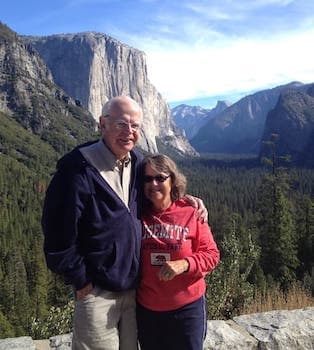
Ted Mooney, P.E. RET
Striving to live Aloha
finishing.com - Pine Beach, New Jersey
December 2021
Tip: Readers want to learn from Your Situation 🙂
(little can be learned from abstract questions, so many readers skip them)
Q. Anyone suggest me about role of boric acid and chloride pH in acid zinc bath solution?
Krishan Kant PachoriHobbyist - Agra, up, India
December 21, 2021
A. Hi cousin Krishan. Much of this thread has been about that for 20 years now :-)
But please introduce us to the details of your specific situation and your problem and I'm confident that the readers can help.
Luck & Regards,
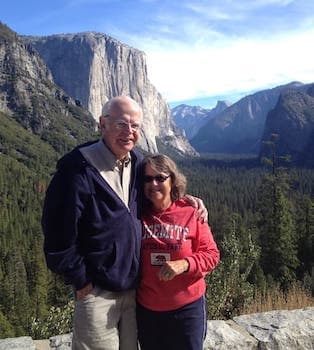
Ted Mooney, P.E. RET
Striving to live Aloha
finishing.com - Pine Beach, New Jersey
December 2021
Q. Am running 24/7. I would like to maintain mirror finish in all charges. After running for 8 hours the finish changes to cloudy finish and non-responsive especially brightener consumption goes high, etc . Also the product looks dull ... roofing nails appear to have different colors of coating.
Harrison m. MuturiEmployee - Nairobi
February 25, 2022
A. Hi Harrison. Ideally the supplier of your acid zinc plating process should be supplying technical help. If that is not practical in your situation, the absolute minimum requirement for maintaining an acid zinc plating bath is accurate temperature control, ability to titrate for concentrations of all the ingredients, and a Hull Cell and experience with using it.
But we need further description of the problem because I can't make sense of it :-(
If you are running 24/7 I can't understand what you mean by "after running for 8 hours". After 8 hours from when -- a brand new bath makeup? What temperature are you operating at and how are you controlling it please? You're not going to be able to run an acid zinc process designed for low temperature operation without cooling coils, especially a barrel plating line.
Luck & Regards,
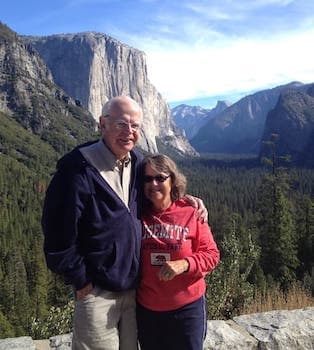
Ted Mooney, P.E. RET
Striving to live Aloha
finishing.com - Pine Beach, New Jersey
Q. Good day.....
I am having a problem with my acid zinc plating bath, I have listed the steps below followed by a couple questions.
I have made up a 25 gal acid zinc bath as follows,
Zn .58 lbs per gal, 14.5 lbs
KCl 1.7 3lbs per gal, 43.25 lbs
boric acid .28 lbs per gal, 7 lbs
carrier 4% vol
brightener .05% vol
After dissolving all salts, prior to adding brighteners, i noticed a brown residue floating around, i decided to treat the bath with potassium permanganate, however a miscalculation led to 4x the recommended amount, filtering would not be enough to clear the problem, so i had to resolve to hydrogen peroxide at 500ml to clear the problem, followed by carbon filter and PP filter until the solution was clear, i then proceeded to add the carrier and brightener. dummy plating was done for approx. 60mins,
rack plating results were good, however i find that HCD burning takes place easily.
Basket plating however suffers with a blackish zinc color or a dull brightness (it resembles what tarnished silver looks like), sulfuric acid bath brightens the "blackish/dull" areas and it looks bright after passivation, however from my previous bath performance i know something is off.
I sent the solution to the lab for testing and results are as follows:
zinc metal .18 oz/gal
KCl 13.48 oz/gal
pH 3.8
cloud pt 15.8F
Can the addition of too much potassium perm or hydrogen peroxide cause such a drastic depletion of the zinc chloride?
Can the solution parameters be resolved by adjusting the zinc, and chloride levels?
I am not certain but I do not believe there has been any organic contamination introduced to the bath to cause such a low cloud point, how could that be explained?
I appreciate your help !
Thank You
- Trinidad Port of Spain
October 31, 2022
Q, A, or Comment on THIS thread -or- Start a NEW Thread