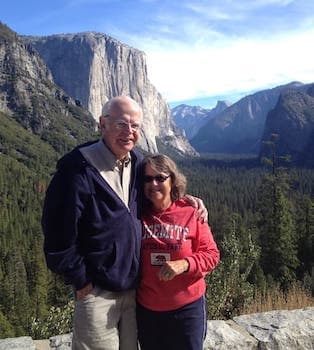
Curated with aloha by
Ted Mooney, P.E. RET
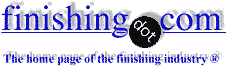
The authoritative public forum
for Metal Finishing 1989-2025
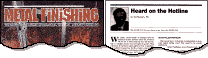
-----
Problems in Acid Chloride Zinc Plating

Hi Experts ,
I am running an Acid Chloride zinc plating shop of 15000 ltr. capacity in barrel application. Doing plating on sheet metals. My question is ...
During the nitric activation I observed some white sticky material develop in nitric acid activation after 5 sec of the dip time and if we continue the dipping for 15 sec. it disappeared and after passivation layer looks perfect. After some time plated parts become white or milky in appearance and get rejected in quality inspection. Please refer to the below operating parameters.
pH of plating bath .. 4.6 to 5.3
Zinc metal .. 28-35 gpl
Total Chloride .. 120-130 gpl
Boric Acid ... 30-35 gpl
Operating temperature.. 25-30 °
Current Density .. 0.4-0.5 A/sqdm
Process Sequence .. Hot degreasing, Anodic Cleaning 1, Cascade Water Rinse 2, Acid Pickle - Cascade water rinse 2, Anodic 2nd, Cascade Water Rinse 2, Acid Activation, Cascade water rinse 2, Acid Chloride zinc plating - Drag Out- Cascade water rinse 3- Nitric Activation (10 - 25 ml/l) - water rinse- Bright passivation - Cascade water rinse 2- dehydrator - Oven Dry (15 minutes @ 100 °C )
(good part)
(bad part)
Sanjay Yadav
- Gurgaon, India
June 16, 2023
A. Hi Sanjay, my first thoughts are:
1. your zinc plating tank is too hot, and too variable. What does the technical data sheet from the supplier say the temperature should be? Oil-out of brighteners sounds like a possibility.
2. your dryer is too hot; 65-70 °C sounds more appropriate to me.
Luck & Regards,
Ted Mooney, P.E. RET
Striving to live Aloha
finishing.com - Pine Beach, New Jersey
Hi Ted,
Thanks for your valuable input . Below are for your reference
1- As per chemical supplier Technical Data Sheet ,the operating temperature should be 20-30 °C. This also coming after batch treatment (done on 16th June).
2- Dryer temperature adjusted to 60 °C but the issue is the same.
(24 hours after plating)
What else are the factors to create such kind of defects?
A- Is TOC play the role in it ?.
B- We are running a bright passivation having 1.5 g/l of trichrome after makeup. Is it possible with low Tri-chrome concentration as some of the bright passivation have more trichrome ?
C-We are using commercial Nitric Acid Activation with 10-20 ml/l of concentration for 15 minutes of dip time. Generally we use Nitric Activation in Alkaline Non Cyanide zinc but i am not able to activate the Acid Chloride zinc below this concentration . Is it correct?
D.I am also wondering if it is happening with solvent based Additive ? Any relevance either its water based or solvent based ?.
Waiting for your further inputs!
Regards,
- GURGAON, India
June 19, 2023
A. Hi again. I remain concerned with your zinc plating temperature because in my very limited experience, 25 °C is a bit higher than I am used to seeing, 30 °C is a lot higher, and a looseness which allows a 5 °C range seems like insufficient control.
Do you have Hull Cell panels indicating that things are okay? The very obvious and noticeable reaction you are seeing in your nitric acid dip seems to be an indication that things are not right as the work exits the plating tank. And the fact that the chromating doesn't work without nitric acid seems to be yet another indication of a problem with the zinc tank.
A. If you just did a batch treatment I can't see TOC being a problem.
B. Trivalent chromates are highly proprietary and I would not be able to hazard a guess for the right concentration for the one you are using. The supplier must tell you.
C. 10-20 ml/l of nitric acid does not sound excessive at all, but surely 15 minutes is a typo and you mean 15 seconds?
D. Again, addition agents are proprietary and aside from supplier instruction, Hull Cell panels are probably your only indication whether the additives are functioning appropriately.
A final thought that arose from paging through Geduld's "Zinc Plating" [on
Amazon,
AbeBooks affil links] is the possibility of lead or cadmium contamination. If a friend or university library has this book it has a 29-page chapter on "Hull Cell Control of Bright Zinc Plating Baths".
Hopefully someone with more hands-on acid zinc plating experience than me will be more perceptive about the likely cause :-)
Luck & Regards,
Ted Mooney, P.E. RET
Striving to live Aloha
finishing.com - Pine Beach, New Jersey
⇩ Related postings, oldest first ⇩
Brown sticky slime on surface of chloride zinc plating tank
Q. We have made a few changes to our acid chloride zinc rack plating line. Increased our chloride to 20 oz/gal from 17 oz/gal. Increased our brightener additions from 1 gal every 25,000 amp hours to 1 gal every 8,000 amp hours based off of hull cell testing. Lowered our pH from 5.0 to 4.5 with diluted hydrochloric acid. Increased our bath temperature from 60 °F to 80 °F. Added more uniform air agitation. Our boric acid level is 3.3 oz/gal. Our zinc has increased from 5.6 oz/gal to 6.6 oz/gal in the last 7 months. Iron usually runs between 20 - 35 ppm. However, our parts look very good in appearance with no rejects since all of our changes. We conduct "non-air agitated" Hull Cells daily.
My question: Initially we noticed a very "dark" brown material across the surface of our bath - this stuff is extremely sticky - what could it be? Also, just recently the "dark" brown material seems to have changed to a lighter brown material.
mfgr - Robinson, Illinois, USA
2006
A. The bath is out of recommended range. First, pH should be 5.0-6.0. The crap on top of the tank is probably the wetter (carrier) portion that has "kicked" out at pH 4.5. Normally it won't at 4.5, right on the edge. When adjusting pH it is possible it was lowered to 4.0 or less. As you have found, it will not re-solubilize. Keep running and changing the filter.
The zinc metal content should be 3.0-5.0 for a rack bath. When the zinc rises above 6.0, the efficiency goes down ,i.e., when the bath is right, plate thickness is 6:1, high CD to low CD on the part. Metal above 6.0 may be 12:1 or higher high to low. You may be experiencing brittle plate with high zinc. You should decant the bath to reduce zinc.
To check for brittleness, run a 2 amp-30 minute Hull Cell, no agitation, do not nitric bright dip it. Just dry, and bend a corner over and back to see if it cracks.
Boric should be 4.0-6.0 oz/gal. When the zinc metal gets to 5.0-5.5 keep the boric at 6.0. No benefit to have boric higher.
Iron is good at 0-50 ppm. Is still OK at 50-100 ppm.
Chloride should be 17.0-19.0 oz/gal. When zinc is close to 6.0 oz/gal., chloride of 20.0-21.0 is OK.
The bath is most efficient at temperature 70-90 degrees F, 80 degrees is the best.
I don't know what brightener system (company) you use, but I am sure the salesman is smiling at a brightener add of 1 Gal. every 8,000 amp hrs.
Recommend you discuss with your vendor all the above. They should check for total organics, (wetter-carrier), this should be 4-6 %/vol.
tech svc. w/ chemical supplier - Grand Rapids, Michigan
A. Hello Travis
It is possible that with the increase of Chloride in solution the wetter part of your brightener system is unable to " HOLD" in all the brightener that you have now started adding.
This phenomenon is sometimes called " Brightener Kick Out or Oiling out '
This question cannot be completely answered by this forum. Connect with your Brightener supplier and ask for service.
The only answer is to use a stable Brightener system that can work under your conditions mentioned .
Regards,
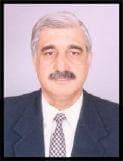
Asif Nurie [deceased]
- New Delhi, India
With deep regret we sadly advise that Asif passed away on Jan 24, 2016
Q. Thanks for the comments - Our supplier has been notified - they always stress "consistency" and keeping the bath in "balance." We have had some different employees in and out of our shop which might have contributed to what's happening. Bill made mention of the pH maybe lower than the 4.5. I would have to agree that this is a strong possibility. We only add acid at the beginning of each day.
In regards to pH - Can you purchase a controller to constantly monitor the bath pH & automatically feed in acid to maintain a set pH? I've been told not to check pH while work is being plated - then I've been told it is ok?
Again, thanks for your comments.
- Robinson, Illinois, USA
A. The temperature of 80° will cause "oiling out" in older standard baths.
You could also be overloading the wetter side of your brightener system.
plater - Charlotte, North Carolina
A. There was a great deal of information in the previous replies that is true and some which may not be quite so.
Firstly, zinc metal does tend to rise in chloride zinc solutions since the drag out is less that the drag in and the high anode efficiency leads to increasing metal. Most platers have to decant solution periodically. Secondly, it would seem that for a rack bath you are using an excessive amount of brightener from any vendor. Reduce brightener additions by at least half, treat the bath with potassium permanganate
⇦ this on
eBay or
Amazon [affil links] and carbon filter. The material you see on top of the bath is probably unsolubilized brightener. With most brightener systems you need to increase the quantity of carrier (aka starter, wetter) to provide enough solubilizer for the higher amount of brightener. This situation would be readily apparent if you ran a cloud point on your bath. Cloud point is a good indicator of low carrier and/or high total organics. You also should be having problems with yellow chromate adhesion at this high brightener loading. Finally, the suggested level of 4 to 6 oz/gal of Boric Acid is high since I believe this is beyond the solubility of boric acid at this operating temperature. If you wish to run boric acid at the high end of solubility (to help prevent burning and for improved conductivity) take an extra anode bag and fill it with boric acid, it will dissolve as much as possible for the temperature you are operating at. One caveat: if the temperature drops, the now insoluble boric acid will precipitate out and if not picked up by the filter will cause roughness.
One last thought, I hope you are running continuous filtration with a turn over rate (real time) of a minimum of 2.
- Great Neck, New York
Operating temperature for acid zinc plating
Q. Hi, this is Danish. We manufacture sheet metal components and also electroplate them. What would be the optimum temperature for acid zinc plating if the capacity of tank is 500 ltr and per batch 25-30 kg material is plated? For a total of 6 tanks. Any advise will be highly appreciated.
Thanks and cheers,
- Karachi, Sindh, Pakistan
July 13, 2012
A. Dear Danish,
-
The advised optimum temperature for acid zinc potassium electroplating bath is 22 °C. Over 28 °C there are (commonly) problems of over-consumption of brighteners, under 15 °C there are problems to level, low conductivity and low solubility of potassium chloride and boric acid (addition of these may be troublesome).
For 30 kg of material, 500 lt of bath seems good. If you have some small refrigeration equipment you may have no problems.
Best regards!
fasteners manufacturer - Cañuelas, Buenos Aires, Argentina
pH Rises Even Though Boric Acid Is Right
Q. My question is that after having boric acid in range in acid zinc electroplating even then pH raises from 4.8 to 5.2 and above why? Please if you are capable tell the answer.
Dharmendra ChauhanChemist - Ludiana, Punjab and India
June 27, 2013
A. Hi Dharmendra. It is normal for the pH to rise, and it is expected that you will need to add acid to maintain it. The plating is not 100% efficient, but releases some amount of hydrogen gassing at the cathode. When hydrogen gas is released from water, it leaves OH- in solution, so the pH rises.
Regards,
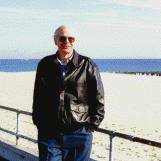
Ted Mooney, P.E.
Striving to live Aloha
finishing.com - Pine Beach, New Jersey
Calculating / Analyzing Potassium Chloride in Acid Zinc Plating Bath
Q. We have a 17,000gal acid chloride zinc plating bath. I'm looking for a formula to help calculate the level of potassium chloride in the bath. I've been given a couple different formulas from but they produce completely different results. Hopefully a formula exists where we can input numbers from a quick titration rather than relying on an outside lab.
Thank you.
- Cleveland, Ohio USA
November 4, 2014
A. Titrate the chloride via the silver nitrate method with chromate indicator. Determine the zinc content via EDTA titration. Calculate the ZnCl2 concentration by simple math...then get to the KCl concentration by subtraction. Helpful hint: run that KCl as high as you can get away with. (limitation, the KCl solubility) It helps improve the "throw" of the bath.
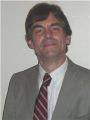
Dave Wichern
Consultant - The Bronx, New York
Q. How to check the zinc metal and total chloride in a zinc acid bath. Please tell me the procedure of checking in chemical, and also a shortcut to check.
naval dhiman- Chandigarh , India
November 25, 2016
A. Hi Naval. As you see, we appended your inquiry to a thread where it is answered. If you have additional questions, please continue the discussion. But please tell us who you are and your situation (rack, barrel, or continuous plating; approx. tank size; what method you've used to date, etc.) so people can more immediately help you rather than having to concern themselves with all of the possibilities raised by abstract questions. Thanks!
Regards,
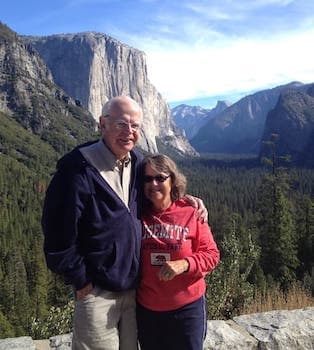
Ted Mooney, P.E. RET
Striving to live Aloha
finishing.com - Pine Beach, New Jersey
Removing organic contamination from acid zinc tank
Q. Hi all. I want to ask about how to remove organic contaminant in zinc solution tank. Size of tank is 7500 L; how many times we need to do cleaning for the tank if production is running 24 hours 7 days? Thanks.
best regards,
- perak malaysia
December 20, 2015
A. Dear mohd solehin,
According to your plant working period, you must refine the solution after max. 3 months by adding Hydrogen peroxide H2O2 0.1-0.5% of volume of tank, and give 48 hours for settling dissolved solids.
Electroplating Plant Engineer - Lahore, Pakistan
Q. I use a zinc/potassium chloride/boric acid plating tank of 800 liters to electroplate small items like bolts, nuts, washers etc. Even though I get fairly good deposit on the workpiece, I do notice excessive foaming sometimes in my tank without warning, after some time it disappears. This development baffles me and keeps me searching for ways to solve the puzzle. In as much as I cannot say for certain the exact values of the constituents because I have not done the analysis for a while now, their values run within these ranges: zinc metal -28 g/l; chloride -122 g/l; boric acid -10 g/l. pH -5.4; temp. -30 °C. For brighteners, I use 650M&R (Growel). I would appreciate it if you could suggest the possible causes of such excessive foaming.
Louis UMEOKOLIzinc chloride barrel plating of bolts and nuts, etc. - Igbo-Ukwu, Nigeria
April 28, 2016
A. Dear Louis,
You said zinc chloride composition is 28 g/L. It's very low composition. Your zinc anode, you might notice, will highly melt down or transfer high current, and solution temperature is also going to increase. This is causing foaming in solution. You should enhance composition of zinc chloride up to 60 g/l and boric acid composition up to 20 g/L. Your Foaming problem will be solved and finishing of product enhanced as well. Also maintain the composition of brighteners according to such composition.
Warm Regards
QAQC & Electroplating Engineer - Lahore,Punjab, Pakistan
"Black Tar" on surface of Acid Zinc Chloride bath
Q. I have a customer whose acid zinc chloride bath develops a tar-like substance that settles out atop the bath. The color is a dark brown, but the colloquial "in-house" term is "black tar".
This is a barrel plating operation in a shop that has a history of inconsistency, but is making very fast strides toward best-practices.
For the sake of spitballing, I'd like to ignore the inconsistency possibility and ask about the possible nexus of this substance.
Has anyone faced this substance? What is its nature? How can it develop? How can I advise them to eliminate it for now, and prevent it going forward?
Thanks to anyone who takes the time to reply!
Technical Service Engineer - Versailles, Kentucky, USA
March 2, 2017
A. You might consider having a lab do IR spectroscopy on the mystery tar.
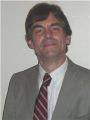
Dave Wichern
Consultant - The Bronx, New York
A. I would investigate possible gross overdosing with organic additive (brightener)
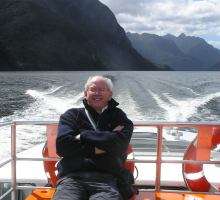
Geoff Smith
Hampshire, England
Q. The substance was analyzed, containing the following peaks in order of amplitude:
1. Carbon
2. Oxygen
3. Chlorine
4. Sulfur
5. Potassium
6. Zinc
7. Titanium
8. Iron
The corresponding solution contents are as follows:
Zinc: 3.04 oz/gal
Chloride: 20.34 oz/gal
pH: 5.85
Boric Acid: 1.65 oz/gal
Carrier: 7.62%BV
Iron: 17 PPM
Manganese: 3.0 PPM
Magnesium: 20.0 PPM
I have a conclusion of my own, but I'm interested in others' conclusions without influence of my own.
Thanks to all in advance!
Tech Svc Engineer - Versailles, Kentucky, USA
A. Hi,
I think it is too much of breakdown products from the the additive in the acid zinc and following rinses.
I suggest to do a analysis of these breakdown products.
Regards,
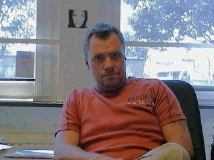
Anders Sundman
4th Generation Surface Engineering
Consultant - Arvika,
Sweden
(you are on the 1st page of this thread) Next page >
Q, A, or Comment on THIS thread -or- Start a NEW Thread