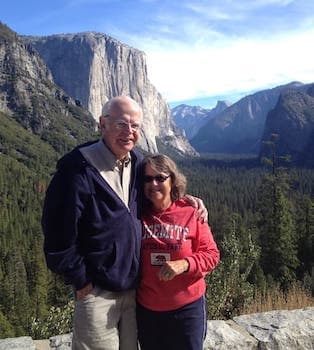
Curated with aloha by
Ted Mooney, P.E. RET
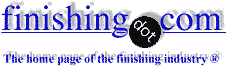
The authoritative public forum
for Metal Finishing 1989-2025
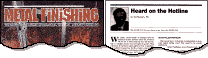
-----
Alocrom / Alodine 1200 RoHS compliance
2006
Q. I am sure that many aspects of RoHS compliance for chromate conversion coatings to MIL-C-5541 (Alocrom / Alodine 1200 in this instance) have been covered in other letters, however I would be interested in opinions on the following.
Customers for our commercial division are beginning to ask questions regarding the compliance of Alocrom / Alodine 1200 coatings. As such one of our QA guys asked the question of the chemicals distributor. The answer was a data sheet containing some guidance notes. The following is an excerpt from this document.
<< Gold and Clear Alocrom coatings have reaction mechanisms that utilise Hexavalent Chromium but the resultant items meet the directives for the following reasons.
a. The electrical conductivity of the conversions requires coating weights from about 40 to 300 mg/m,sq, with the hexavalent chromium component making up not more than 15% (MSDS data). The remainder of the conversion comprises trivalent chromium, aluminium, oxygen etc.
b. For such conversions to be effective they must be fully integrated with the metal surface and so cannot be readily removed by either physical or chemical means, except by using highly aggressive techniques, which will also remove the underlying substrate. Metal removal rates would need to be less than 17µ (significantly less than 1 thousandth of an inch) before the limit of 0.1% w/w might be exceeded for the clear conversion this figure would be much less.
c. Sensitive tests on a random 12 examples of golden chromate conversion from actual production lines, using the classic spot test for hexavalent chromium, showed negative results in every case. The reduction of the hexavalent chromium, when the surface has been fully dried, is such that none effectively remains.
In addition to the above, it must be appreciated that a large proportion of commercial alloys contain significant amounts of both cadmium (in Zinc) and chromium (in steels and Aluminium alloys). Extraction processes for analysis often easily digest these contaminants. >>
The text above is a word for word excerpt from the supplied document. It should also be noted that the document also states that Henkel endorses this advice.
At first glance my QA guy's thoughts were, 'great, ok we have a document explicitly stating that the coatings comply with RoHS, i.e., "but the resultant items meet the directives for the following reasons". Not only that but the advice is endorsed by the conversion systems manufacturer. QA then passed the info on to me for my take on the issue prior to getting back to our customers with a 'yes we comply'. I have to say I was surprised and alarm bells began to ring. All the info I have seen to date would indicate that Hex chrome coatings do not meet the directives. However prior to putting the cat amongst the pigeons. I would appreciate some advice and opinions to the validity of the above statements.
Thanks in advance for any advice and opinions offered.
Wow!~
I believe what it boils down to is their interpretation of what is a
"homogeneous" material. I would agree to their interpretation to a point- Unfortunately it seems the rest of society will argue that the chromate coating is not homogeneous to the aluminum and not RoHS compliant.
In practice we have determined that the purposeful presence of Hex Chrome is not permitted by the meaning of the RoHS and those products not in compliance.
My 2 cents.
metal finishing - San Jose, California
2006
First of two simultaneous responses --
Conversion films are not homogeneous to the part being processed. That's like saying a wrapper is homogeneous to gum. From our perspective, it's pretty easy to remove the coating once applied. A little sandpaper and you've got hex-chrome everywhere.
Justin Crisp2006
Second of two simultaneous responses -- 2006
A view from this side of the pond...your suppliers (and Henkel for that matter) are taking a very dangerous stance about the interpretation of the legislation.
I would be very doubtful of a successful defence of this stance in a court of law (which, if you breach the regulations, you will end up in).
Looking at it from a more practical side, wouldn't it be better to change to one of the hexavalent free coatings and offer this as standard? Then you wouldn't fall foul of the legislation.
Ed. note: I believe that we've only heard 3rd or 4th hand that Henkel endorses that position, Brian, and I would doubt very seriously that they actually do. Certainly it would not be in their economic interest since Henkel is one of the four licensees of the TCP hex-free process.
2006
Thanks for the responses so far.
I would agree that the chromate conversion coating is not homogeneous with the aluminium, and the statement that it is very difficult to remove is incorrect.
Also, if an acceptable definition of homogeneous is 'material that can not be mechanically disjointed into different materials' then the fact that the underlying substrate may be damaged is neither here or there, re the suppliers statements in the first post. However if there is no Hex chrome present in the 'removed' coating why does the finished coating not comply with RoHS ? Is this statement in fact true ? How accurate is 'the standard spot test' ? I am sure I have heard or seen somewhere that the spot test is not conclusive.
The following is an e-mail response directly from Henkel which would include Alodine 1200.
"Our Alodines listed on the QPL-81706 are not RoHS because they contain chrome. We do offer the Alodine 5200 and the 5700 that are RoHS compliant. Please let me know if you need anything else.
Thank you for your interest in Henkel products!
[name deleted], Technical Customer Service Specialist"
Luke Engineering & Mfg. Co. Inc.

Wadsworth, Ohio
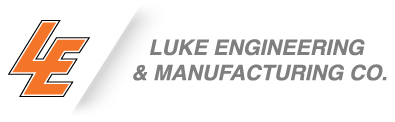
2006
2006
Further to my previous post,
letter 40022 deals with various statements made by our Alocrom 1200
(Alodine in the US), supplier. In short our supplier is stating that the conversion coatings comply with ROHS.
As can be seen from the follow up posts, (thanks to all who replied by the way) and to other similar posts, many state that this is simply not the case as the treatment system is hex chrome based.
However no one touched on the following statement.
"Sensitive tests on a random 12 examples of golden chromate conversion from actual production lines, using the classic spot test for hexavalent chromium, showed negative results in every case. The reduction of the hexavalent chromium, when the surface has been fully dried, is such that none effectively remains"
I would appreciate some opinions on this statement, as if this is true and there is no Hex chrome remaining in the finished conversion coat. Then surely any product with an Alocrom finish would comply i.e., no hex chrome.
From what I have read previously and my gut feeling is that the statement is incorrect. However I am not a chemist and would appreciate some opinions on the issue.
Thanks in advance.
Reference all the discussions regarding RoHS compliance and Alodine. We are currently researching alternatives that are RoHS compliant and OSHA compliant with regard to the new Hexavalent Chromium levels that have just been set in place.
Does anyone know if the Henkel Alodine 5200 or 5700 can meet the salt spray requirements in MIL-C-5541?
2006
It is my understanding from discussions with both Henkel and NAVAIR, that Alodine 5200 and 5700 WILL NOT pass a bare salt spay test as outline in Mil-C-5541. The only way these products will pass is by application of a corrosion resistant primer and topcoat.
Justin Crisp2006
As a follow-up to my last post. Henkel, CST-SurTec, Luster-On and Metalast all have licensed versions of the US Navy's Trivalent Chromium Pretreatment which will pass a bare salt-spray test.
Justin Crisp2006
2006
Please ref the RoHS compliance of Alocrom 1200 (Alodine in US).
All the info I have gleaned regarding the RoHS compliance of Alocrom
1200 coatings suggests that the resultant coatings DO NOT comply.
However our Alocrom supplier has repeatedly informed us that if the coating is applied in accordance with the manufacturers instructions and correctly dried then the coatings DO comply. Their reasoning behind this is that once the coating has been cured / dried then there is no hex chrome in the final coating. As such you could scrape off an Alocrom conversion coating, test for Hex chrome and obtain a negative result. Therefore the coating complies as no hex chrome is being passed onto the customer and the recycling chain.
Please also note that our supplier specifically states that Henkel endorses this information.
Obviously this causes some confusion, especially given the following statement which is reported to come from a technical representative from Henkel. (Re post 40022)
"Our Alodines listed on the QPL-81706 are not RoHS because they contain chrome. We do offer the Alodine 5200 and the 5700 that are RoHS compliant. Please let me know if you need anything else.
Is the confusion arising due to the fact that, whilst the conversion system does not comply the resulting coating does ? Does anyone know enough about the chemistries involved to comment on the 'no hex chrome in the final conversion coat' ?
If the statement is true and there is no hex chrome in the final coating, should it not be possible to sell an aluminium component with an Alocrom coating and state that the part complies with ROHS?
Thanks in advance for any replies.
Rich
2006
Richard, a fellow smarter than me once told me: "If you have to talk yourself into it . . ."
You have learned that point after point of your supplier's letter are not reliable interpretations (the homogeneous part, Henkel's stand, etc.)
You have learned that the entire industry, from the smallest jobshops to the billion dollar suppliers to the U.S. Navy, has been in the upheaval of restructuring for several years to make this change because everyone strongly disagrees with your supplier's take from top to bottom.
You also know that the final dried coating is honey yellow--which color presumably came from hex chrome and is not the color of tri-chrome.
So you can accept your supplier's interpretation (which may have been based on a mimeographed sheet authored decades ago) and live dangerously; or you can run the spot tests yourself on your own parts rather than relying on a supposedly representative aliquot (and live dangerously because no matter how you insist that your sample is representative, a single part in the field that fails RoHS compliance could spell disaster); or you can accept that it's time for change without demanding an impossibly high standard of proof. Good luck.
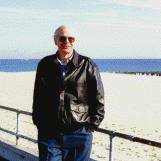
Ted Mooney, P.E.
Striving to live Aloha
finishing.com - Pine Beach, New Jersey
2006
Thanks Ted,
I sort of get the impression I am labouring the issue :-)
However its not me that needs convincing, given my own experience and that of a large number of highly experienced people, many of which post to this site, I am quite convinced that a tri chrome system is the way to go. Indeed once a tri chrome system is qualified to 81706 then I would be pushing towards a change for our aerospace and defence product (my area of influence).
What I am trying to do is get some advice from various sources to back up my own experience in order to convince 'others' on our more commercial side, not to take a dangerous 'head in the sand' stance.
In my colleagues defence you must appreciate their point of view. On the one hand there is a piece of legislation that has undeniably caused significant confusion and upheaval throughout industry. On the other there is a supplier and a manufacturer essentially saying there is no problem. If statements like 'there is no hex chrome in the final coating' are bandied about by the chemical systems manufacturer, then maybe it's the rest of industry that have missed something (their view, not mine). Given how busy we are these days in our day-to-day working lives the path of least resistance is clear. In addition, given the documents from the supplier etc, the proverbial buck can be passed.
However, back to the 'labouring the point' statement. Maybe I have done enough and it's time, for me at least, to stop worrying about it. I have passed on my views and the evidence I have collected, if others wish to take a different view then so be it.
Thanks to all,
I am a distributor of furniture component parts and want to know if under the RoHS guidelines if just the zinc plating is considered a homogeneous material or if the steel component with the zinc plating on it is considered a homogeneous substance. If the former is true then my parts are not in compliance but if the later is true then the concentration of hexavalent chromium would be less than the 0.1% limit and my parts would be compliant.
Thanks,
2006
While 5541 is being revised to incorporate the Cr(6) free type conversion coating, MIL 81706 B was revised in Oct 2004. It specifies "Type II - Compositions without hexavalent chrome" MIL 81706 is the basis for 5541.
Unfortunately the 5541 revision lagged behind, but it is understood that it will issue shortly. The performance requirements, bare corrosion resistance, electrical contact resistance will remain the same.
A QPL according to 81706 B was issued in May 2006 to the CST-SurTec TCP process, based on the Navair trivalent chrome TCP process. SurTec is one of the Navair's licensees in North America for this technology.
Although 5541 new revision is not out yet, meeting MIL 81706 B covers the same requirements.
It should be noted though that the requirements of MIL 81706 for bare corrosion resistance are twice those of 5541, and used primarily for qualification purposes. (e.g. 336 hrs to NSS v.s 168 hrs for alloys
2024 T3) - An applicator is expected to meet the 168 hrs to conform to 5541.
2006
February 17, 2010
My project is supplying parts which ultimately are fitted to Airbus airframes.
The hexavalent chromium based Alocrom 1200 which is a process we have used for many years is now on the B/T/R list (Banned / Targeted / Restricted).
Unlike your previous posts, this is a through-life toxicity consideration. The Chromate solution is used in the manufacturing process, in the product and as a field/service repair. There is toxicity risk at each stage.
My concern is the corrosion resistance performance of alternatives
(no paint finish is specified), and also the electrical conductivity performance of the type 3 and the degradation of conductivity performance with service life.
Any information here would be of great interest.
Thanks
Hi, John. These postings were from 2006 and the situation now is that the TCP (trivalent chromate passivation) process is now MIL approved under MIL-DTL-5541
[⇦ this spec on DLA], and is available from Henkel, CST-SurTec, Luster-On and Metalast (and possibly others). So it's a matter of contacting your supplier and requesting the TCP process. Good luck
Regards,
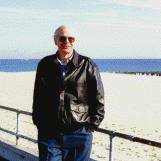
Ted Mooney, P.E.
Striving to live Aloha
finishing.com - Pine Beach, New Jersey
February 17, 2010
September 29, 2010
Thanks Ted; I didn't expect an answer to my mail thread within 24 hours! I haven't been back to this web site for a while: good information, thanks.
Looking through MIL-DTL-81706B, this is a very comprehensive document specifying the testing and test requirements for chemical conversion treatments. One can look up the QPL-81706 for free (!) to find which manufacturers are qualified. However, I am having to qualify parts made from 2014-T6, 6082-T4 and 6082-T6 (not specified in the SURTEC technical leaflets) with specific interest in electrical bonding faces.
These faces have to provide a specified electrical contact resistance throughout the component life, which may be 25 years on wing. The QPL listings are of interest and the SURTEC 650 product (TCP; Tri-Valent Chromium Product) is favourite to do the job.
Because of the criticality of this surface finish, a full qualification programme has to be carried out for this aerospace programme using actual machined parts. Salt spray testing will be to RTCA-DO160.
The negative of this TCP surface treatment is that it is a clear, almost invisible finish. We have to be able to verify that the process has been done. Alocrom is easy; it is yellow! SURTEC have a coloured option (brown!) however, this limits our options of which supplier to use.
Thanks again for the info.
John Grant
Hi,John.
Yes, the lack of visibility of the TCP process is a definite downside. Some people claim that a trained operator can see it (letter 39839, for example), and there are spot tests (although that is obviously not a really good answer). Sorry that your qualification efforts will be so much work, but it does make us all more confident of the integrity of our flying machines :-)
Regards,
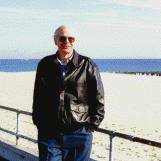
Ted Mooney, P.E.
Striving to live Aloha
finishing.com - Pine Beach, New Jersey
September 29, 2010
September 30, 2010
Thanks Ted for another rapid response!
Another detail which suppliers should consider when reviewing corrosion resistance:
The corrosion tests for qualification reported in MIL-DTL-81706B are specifically for flat sheet. The surface condition of rolled flat sheet is different to the surface condition of a machined billet.
Therefore, in considering a new surface treatment, machined parts representing the final component have to be salt spray tested to verify the suitability of the process.
I am planning to launch such a qualification test using the SURTEC 650 process.
Thanks again for the useful input.
John Grant
Q. Is Alodine 5992 a RoHS compliant process? Henkel has provided us with Trivalent Cr as an option to Hexavalent Cr. But still I have some doubts about it. And yes, I would also like to know how could they get rid of YELLOWISH colour with Alodine process. Does it involve dyeing process?
Thanks
May 15, 2012
Q, A, or Comment on THIS thread -or- Start a NEW Thread