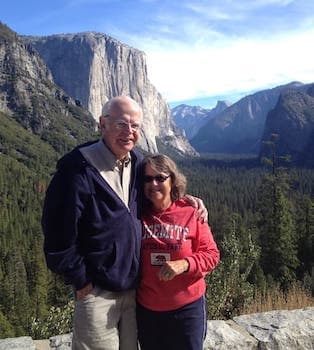
Curated with aloha by
Ted Mooney, P.E. RET
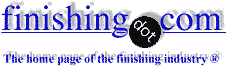
The authoritative public forum
for Metal Finishing 1989-2025
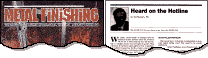
-----
How to Detect presence of Clear Chromate
Q. I work for a medical manufacturer in Denver, CO. We continually question if an aluminum part that calls out for a MIL-C-5541 Class 1A finish is chromated or not. We will get parts in that have been yellow dyed, then all of sudden we will get parts that look bare.
Is there any quick test that we could do to verify chromate exists on the part? When we take the part and rub it on a sheet of paper it leaves a line like lead would, leading us to believe that there is no chromate. Is this a valid test? Is there some other quick and easy test that we could do?
A quick response to this question would be appreciated as we are holding product until I can verify.
- Lakewood, Colorado
2001
A. The best thing to do for the future is to specify an iridescent yellow chrome with a color standard, so that light finishes can be rejected.
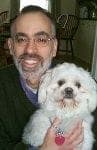

Tom Pullizzi
Falls Township, Pennsylvania
(2001)
A. Hi, folks. Tom's advice to Jay was excellent at the time, and it could still be considered good with some provisos ... but things have changed. The world has moved away from hexavalent chromating, and the only chromates that are both hex-free and which meet MIL-DTL-5541
[⇦ this spec on DLA] are the NAVAIR-developed so called TCP (tri-chrome passivation) finishes.
TCP is thin and almost clear, and it is generally believed that dyeing them greatly reduces their corrosion resistance. So what you need these days is a test for the TCP finish. Please read on for claims that such tests exist and, further, that a well trained eye can see the TCP finish. Good luck!
Regards,
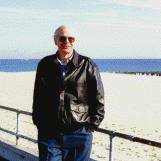
Ted Mooney, P.E.
Striving to live Aloha
finishing.com - Pine Beach, New Jersey
May 24, 2008
Q. We are looking for an Alodine replacement that is not clear. So far this is all we have found. We are doing Alodine primarily on Aluminum. We like the golden color we get right now. We use it as an identifier that the Alodine has been done as well. Are there any other colors which can be produced from an Alodine replacement with no hexavalent?
Ken Pokigoelectronics - Angola, New York
2006
A. Hi, Ken. Adding yellow dye can be done with some of the thicker types of hex-free conversion coatings -- but the MIL-C-5541 approved TCP processes cannot be dyed (the film is too thin); attempts to dye it have all reduced the corrosion resistance.
The characteristic golden color of hexavalent chromium is not a dye; it is the natural color of the toxin, and it's what allows us to instantly recognize that handling the object will expose us to carcinogenic hexavalent chromium.
So this blowhard (me) gets to say it again: Why make parts look like they are toxic, carcinogenic, and forbidden by the EU, even though you have invested the time, effort and extra cost to make sure they are actually safe and "green"?
It seems at least possible to me that the EU may decide that testing for hex chrome is so burdensome and expensive for inexpensive fasteners that they may address this via the timesaver of applying the simple preliminary filter that "if it's golden color it must be rejected".
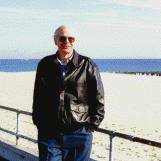
Ted Mooney, P.E.
Striving to live Aloha
finishing.com - Pine Beach, New Jersey
2006
A. I've come across a few that have an inherent color (other than gold) - I don't remember which though. And I know that most can be dyed. But, what Ted says makes sense - if you are going to dye it, why dye it to match an older process that is on the way to being phased out? Why not blue, or green, or anything other than gold?
Jim GorsichCompton, California, USA
2006
Q. The answer to the question of why you would want a RoHS gold Alodine replacement with the same coloration is simple, because your customers like it!
Also, if it turns out to be so simple for the EU to identify and "reject" parts for the presence of chromium by, "it looks gold", then so be it. I'll be glad to accept all the gold plated parts they can filter out for me!
electronics - Angola, New York
2006
A. Gold chromate will never be mistaken for gold, Ken :-)
'Product stewardship' was a crucial part of 'mission statement' last decade, But management themes come and go, and I guess responsibility isn't particularly "in" so far this decade. Leadership is always in, and if ever there was a right time for we in the industry to work to get our customers to understand and to think fresh instead of dyeing non-toxic finishes the inherent, characteristic color of the toxin, now would be the time.
The new "TCP / I can't see" replacement technology is colorless and very thin and my understanding is that attempts to dye it yellow or black so far have significantly reduced the corrosion resistance. Pastels are pastel because they lack saturation, so they may be more doable with these very thin coatings. If pastel pink or pale violet or light spring green were a quick and reliable indicator of the presence of a toxin-free TCP coating, we'd have the win-win situation we need :-)
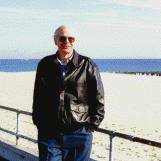
Ted Mooney, P.E.
Striving to live Aloha
finishing.com - Pine Beach, New Jersey
2006
In line with what Ted said - While the customer is always right, that doesn't mean that they are always educated or unwilling to be persuaded. Dyeing the parts yellow is just silly - silly from an environmental perspective in that it makes them much harder to tell apart from hex-chrome containing parts when it comes to recycling and such and silly from a business perspective with it making it impossible to brag about how "my parts are better for the environment -- just look at the color! (rather than that old toxic yellow)"
Yeah, the customer may want gold colored parts right now; that is no reason why we shouldn't be encouraging them to change.
Compton, California, USA
2006
Q. The non-chromium replacements for MIL-C-5541 chromate conversion coatings I have seen are all clear. A very legitimate question is how does one assure the quality or even the existence of a coating one cannot visually inspect. Historically, the "golden" color is the only quick indication of a quality conversion coating on aluminum. Are there non-chromium replacement products that can be inspected visually or are there other simple quality tests available?
Chris Jurey, Past-President IHAALuke Engineering & Mfg. Co. Inc.

Wadsworth, Ohio
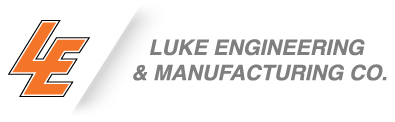
2006
----
Ed. note: In our podcast of April 9, 2007, Kim Price discusses a purportedly simple test that Luster-On has developed for their TCP process. You may want to follow up with her. The interview with Kim starts at 2 min 45 sec into the podcast. There is also a company called Trivalent Tester LLC which claims to have a test. The larger suppliers like Macdermid surely have or can guide you to test kits.
A. We have been using TCP for a year now. I can tell you that it is not entirely colorless, but you won't a good gold out of it. When properly applied, TCP should have a very, very, very light tinge of brown. You have to know what your looking for. As to the dye, I've had numerous discussions with the folks at NAVAIR. The problem with dye is that it contaminates the bath to the point that salt spray failure occurs. NAVAIR has been working on this aspect for a few years but to no avail.
Justin Crisp- Indianapolis, Indiana
2006
Q. We currently have many parts that have the gold color. I believe a clear is acceptable if we have the ability to verify the plating at the incoming inspection.
Are there any platers out there that have tried to add a fluorescent to the process so the parts can be verified under a black light source? This is common use on PC boards to verify the application of clear conformal coat. I do understand this is more of a painting process. thanks
- Santa Rosa, California
2006
A. Trivalent Tester LLC has recently developed a drop test kit to enable verification of the presence of TYPE II Trivalent Chromium Conversion Coating on an aluminum substrate.
Jim SavoySr Quality Engineer - Columbia, Maryland
April 13, 2009
Q. My name is Vinoo and I work as Quality Assurance inspector in a Electro-mechanical process manufacturing company. I have some aluminum sheet part with "RoHS clear chromate conversion such as Alodine 5200 or equivalent."
I would like to know that after this process on aluminium 5052-H32 sheet will have surface be conductive or nonconductive? Surface finish appears clear, so how would one differentiate from clear chromate conversion process is done or not done?
Please guide me on this subject.
Thanks
QA Inspector - Marlboro, Massachusetts
April 9, 2010
A. Hi Vinoo. We appended your inquiry to a thread which answers most of your questions. Although chromate conversion coatings are not conductive per se, if the process is performed to the MIL spec, the sheet should be sufficiently conductive as the spec calls for conductivity. But this is not an absolute, and my understanding is that pressure must be maintained to insure it.
Regards,
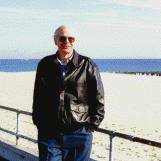
Ted Mooney, P.E.
Striving to live Aloha
finishing.com - Pine Beach, New Jersey
December 2013
November 2, 2010
Q. I am investigating the use of SurTec 650 as an alternative to Alochrom 1200 hexavalent chemical conversion treatment for 2000 and 6000 series aluminium alloys.
I have had samples treated with SurTec 650 and about to launch a salt spray test on machined and welded parts.
The lack of visibility of this treatment is a real issue for my company; how do you verify on a day to day basis whether incoming parts have been treated?
These parts are fitted to civil and military aircraft platforms, hence the corrosion performance and electrical connectivity are a critical issue for us.
I am now reviewing the use of SurTec 650V which has a colour trace added. The Henkel data sheet claims 'produces colourful and visible layers which are blue-grey to yellow iridescent'. I need to know the availability in the UK and whether I can read across tests carried out on standard SurTec 650 to the 650V. Also, where suppliers have quality approvals, do they have to gain another approval for the use of this variant?
Has anyone else trod this pathway?
Thanks
- Fareham Hants United Kingdom
A. Hi John. Justin seems to imply that what you need for the new colorless trivalent chromates is an inspector with experience and a really good eye. That's certainly a point worth investigating as we are all jointly taking a serious risk in using 'invisible' surface treatments. As for visible 'tracers', the thing is, if the product is listed in the QPL, it's listed; and if it's not, it's not, and can't be used for MIL-DTL-5541 parts.
Regards,
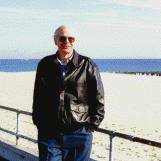
Ted Mooney, P.E.
Striving to live Aloha
finishing.com - Pine Beach, New Jersey
Surface Chromium Increase for MIl-DTL-5541 Expected?
Q. Hello,
We've run into an issue in which we suspect our Tier 2 supplier is not properly applying the MIL-DTL-5541F chem. conversion coating as we have requested (Type 2 Class 3).
I am well versed in the actual MIL std. requirements (required chemical tests, salt spray tests, etc.), but as an interim 'quick check', we used a SEM to look at chromium content in the base material (5051) and on the surface.
On a known "good" sample we saw a significant increase (~0.2" ^0.2% in the matrix and 0.5" ^0.5% on the surface), whereas from the "suspect" supplier we did not see any increase between the matrix and surface.
My question is - would you expect to see an increase of chromium content on the surface as a result of the chemical conversion process, or is this merely an un-related observation?
Thank you!
- Bothell, Washington
May 19, 2017
Q. Sorry for any confusion - the numbers above are percent's, not inches! The matrix was measuring approx. 0.2% chromium - the known good sample was measuring approx. 0.5% chromium at the surface whereas the suspect parts had no increase in the surface chromium content.
Brian Wolz [returning]- Bothell, Washington
May 22, 2017
Q, A, or Comment on THIS thread -or- Start a NEW Thread