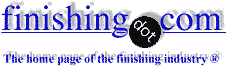
-----
Wheelchair finishing & refinishing: Paint/powder coat, chrome, aluminum
Quickstart:
As many know, preparation is at least half the job when painting or powder coating aluminum. Ideally the manufacturer did chromate conversion coating before painting. Chromating is beyond most consumers ability, but they should at least remove any loose or flaking paint and apply a primer designed for aluminum before their final finish coat.
Q. I use a wheelchair. It has aluminum rims. The paint has flaked off and my hands are black from the oxidization (if that's the word.) I need an inexpensive way to handle this problem. the chair is only one year old and this is not in the warranty. I was told about powder coating... rah rah rah ...and am told that will cost an arm and a leg, about 1/3 of what I paid for the chair and have also been told that it isn't a permanent solution. The rims will still nick and the aluminum will be there again.
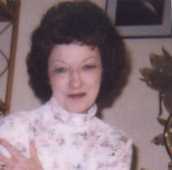
Mae Tennisco
Canada
2000
A. Unfortunately, it may very well cost 1/3 the price of the chair to powder coat the rims, as you have been told. The problem being that when an item is mass-produced, dozens or hundreds done at a time, so the labor cost is low; but when one or two of something need powder coating, the cost of labor involved is very significant and costly.
We in the metal finishing industry the problem you are having an embarrassment. People are not supposed to make garbage and then hide behind small-print warranty exclusions. If paint comes off in your hands they probably weren't pretreated properly.
If you mail us (523 Springfield Ave., Pine Beach, NJ 08741) photocopies of the relevant documents (manufacturer contact info, receipts, and the warranty exclusion), we'll be happy to write them and enclose a copy of this web page. We're not experienced consumer advocates and can't promise results, but we'll be happy to try, and to publicize the results.
If you prefer to paint them yourself, get the old paint off as best you can (assuming they're not raw aluminum), then apply a primer made for aluminum. After the priming, you can paint it in the finish color of your choice.
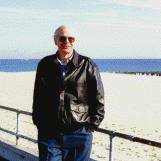
Ted Mooney, P.E.
Striving to live Aloha
finishing.com - Pine Beach, New Jersey
Q. I am service development manager at a company which reconditions wheelchairs. We remove all of the old paint finish via a shotblasting process, prior to a respray in polyester powder coat finish. Is it necessary to carry out any further pre-treatment after shotblasting to ensure a good 'key' for the powder coat?
Alan J. DoddsRemploy - Coventry, West Midlands, UK
2001
A. Dear Mr. Dodds,
Normally, a blasting operation is a good preparation for powdercoating. Some points to consider:
- Blasting should be done with angular-shape material in order to get enough surface profile (Saw-tooth shape)
- De-dusting after blasting must be done very thoroughly
- Be aware: since you have no conversion-coat (i.e. phosphating) the corrosion resistance would be fairly poor, but this will be probably no problem with wheel-chairs
Hope to have helped you,
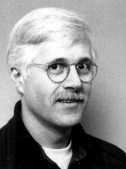
Remmelt Bosklopper
- Enschede, The Netherlands
A. It's nice to see companies that refurbish and/or reuse resources. Blasting is a good way to clean and prepare the surface of the substrate. You must remember that blasting media (abrasive material) can potentially reintroduce oils, soils and other contaminants to the surface. Liquid topcoats generally are more forgiving when dealing with these contaminants, however, powder coating is not as forgiving. For optimum durability and customer satisfaction, the substrate should be at least washed thoroughly and if possible be phosphated.
![]() Bob Utech Benson, Minnesota |
![]() Ed. note: Bob is the author of: "High Performance powder Coating" on eBay or AbeBooks or Amazon [affil links] |
RFQ: I am looking for a Co to do decorative chrome on a small part for a wheelchair. Quantities will be in the 5 to 10,000 per year. Please contact me.
David Keller- Odenville, Alabama
2004
Ed. note: This RFQ is outdated, but technical replies are welcome, and readers are encouraged to post their own RFQs. But no public commercial suggestions please ( huh? why?).
Q. I am disabled and have 2 aluminum ultralight wheelchairs. The one I am working on now is a Quickie XTR⇨
I want to go on the beach this year but there are no wheelchairs designed to go through sand, so I made one. This one has big mountain bike tires on the back and ski's on the front. My question is, what is the easiest way to strip off the existing paint, what do I use to repaint it, and what can I use to protect it from the sun, sand, and salt water? will a simple coat of clearcoat do? what if I don't want to paint it, how do I keep it shiny and protected? I will post pics when it's done if you guys are interested
Castle Hayne North Carolina
2006
A. Aircraft Stripper is noxious stuff, Jerry, but it's made for removing paint from aluminum. But if the existing paint is adhering well, it's better to paint over it than to strip it.
Clearcoating will not be nearly as successful as painting because you can't do proper preparation under a clearcoat because proper prep steps discolor the aluminum, they don't leave it shiny. Considering the corrosive environment, clearcoating will not hold up long on a beach, although a two-pack clear coat sprayed by a body shop is probably better than single component clear coats. If it must be shiny aluminum color you probably should send it to an anodizing shop for anodizing. Good luck.
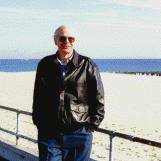
Ted Mooney, P.E.
Striving to live Aloha
finishing.com - Pine Beach, New Jersey
Tech help for finishing of steel push-rims
I need ideas on a difficult steel finishing problem affecting wheelchair riders in developing countries. I've listed the design requirements and past ideas below, with the questions at the bottom. Thanks in advance.
REQUIREMENTS:
A wheelchair pushrim (the large ring attached to the rear wheel for propulsion by the wheelchair rider's hands, often made of 19 mm mild steel tubing with 1 mm wall thickness) has the following requirements for finishing:
1) corrosion resistance
2) impact and abrasion resistance (pushrims are the widest point on wheelchairs and frequently bang and scrape against doorways etc)
3) "coolness" during braking (when a rider coasts down a hill, the rider must be able to let the rim slip rapidly through the fingers, then grip strongly at the end of the ramp or hill to slow the wheelchair. If the rider cannot "brake" both strongly and evenly, the wheelchair may get out of control and the rider may crash.
4) safety against cuts
5) safety against toxicity (skin contact)
6) residue on hands (some finishes i.e., hot-dip galvanization leave hands black)
7) appearance (over and over we have learned that when people are proud of the appearance of their wheelchair, they will have more confidence to use the wheelchair in public, and they will maintain the wheelchair better).
8) cost (wheelchairs in developing countries are often purchased by donors or governments who want lowest cost)
9) worker / environmental health
(note: I have left out "gripping friction", which is a requirement for riders with low hand strength. however this is usually accomplished by adding an additional layer of rubber or similar material, rather than a finishing)
PAST IDEAS AND PAST PROBLEMS
1) Nickel-Chrome: good abrasion resistance and "coolness" but when it "flakes" / delaminates, the resulting razor-sharp flakes cause serious injury to fingers. these (often deep) cuts are extremely inconvenient for wheelchair riders who must use their hands to propel, and present an infection risk for poor people without good access to nutrition and medicine who may be living in unhygenic environments. Toxicity concern for workers and people who live near factories (serious concern in under-regulated countries).
2) Powdercoating: looks great when new, and never cuts fingers even when worn. However can cause severe friction burns (even deep burns with blistering) when a rider descends a steep hill too quickly. Riders without the pain tolerance to grip the rims anyway may lose control and crash. Abrasion resistance is not very good, usually there is visible steel (and often rust) after a few months of use. Low-cost and non-toxic.
3) Stainless steel pushrim (alternative to plating): works well, has excellent abrasion resistance, but is expensive. use of thin-wall stainless to save cost results in brittle failure of welds.
4) Plastic pushrim (alternative to plating): similar problems to powdercoating plus poor abrasion resistance and fragility.
5) Anodized aluminum pushrims (alternative to plating): This is the standard in wealthy countries where people can afford to replace damaged pushrims
QUESTIONS:
--How can we assure nickel-chrome will not flake and cut fingers, especially from low-cost producers? what method (steel/nickel/chrome, steel/copper/nickel/chrome, steel/nickel layer 1/nickel layer 2/chrome) provides best adhesion? what are "warning signs" of improper steel prep to look for during factory visits? In general is it reasonable to expect well-applied nickel chrome to take a beating without flaking--ie is the flaking we've seen in the field because of poor manufacturing QC, or is chrome a poor design choice for this application?
--what other technologies (chrome substitutes i.e., cobalt alloys, nickel-only plating, passivated zinc, black oxide, ?) might meet the requirements above?
Many, many thanks on behalf of all the wheelchair riders in the world with burned or cut fingers.
product designer - Cape Town, South Africa
May 30, 2009
A. As a powder supplier to wheelchair mfgrs. in the UK I understand that they do not seem to have the problems you mention. They apply tinted clear powder lacquers (red, blue, green etc) over a chrome finished substrate. This finish is not only appealing to the purchaser but... as you state, hard wearing, non toxic and, maybe because the powder contains no pigments or extenders, does not have the abrasive properties you describe.
Terry HicklingBirmingham, United Kingdom
A. Hi Matt.
I think the anodized aluminum or the stainless will prove best..
Luck & Regards,
Ted Mooney, P.E.
Striving to live Aloha
finishing.com - Pine Beach, New Jersey
Q. I have a disabled friend that has a problem similar to the one posed by a woman who wrote in about getting black oxidation on her hands from her wheelchair rims. My friend ends up with black streaks all over his face by the end of the work day, almost every day. Like most wheelchair users, he is not able to replace every part each time some little thing happens. And even though the black marks are an annoyance, the rims are still in decent shape and usable. So, as an outsider to those who are bound to wheelchairs, I would like to see if a viable inexpensive alternative coating has been arrived at that these people can use to solve what seems to be a very common and yet costly problem. I know nothing about what would work well that would bond to aluminum, but there must be something out there that could be applied without too much trouble or cost. Would something like Rhino liner work? Thanks on behalf of everyone I could hope to help.
Curt FloryLubbock, Texas
February 17, 2010
Hi Curt. I would think that good, heavy anodizing would hold up well. That's probably not something that you could do yourself though.
Cleaning and sanding, followed by epoxy primer, followed by polyester or latex spray paint would probably be quite good.
Luck & Regards,
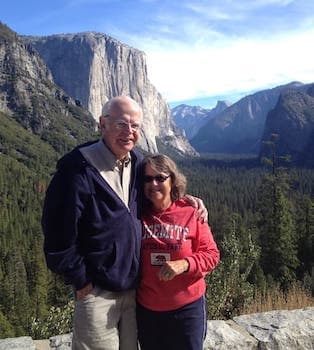
Ted Mooney, P.E. RET
Striving to live Aloha
finishing.com - Pine Beach, New Jersey
Q. Hi,
We have an application where two 6061-T6 aluminium parts are assembled together with M3 black oxide flat head screws. The aluminium parts are not coated. The application concerns wheelchair components which can from time to time be exposed to outdoor weather (rain, snow, moisture, freezing). Most of the time, the components are inside a house.
We have some problems with the flat head. After a few weeks of operation, they rust. We have consider using stainless steel screws but I think galvanic corrosion could occur after some time.
1. I believe if we had some electroless nickel plated screws we would resolve the rust problem. Do you think it would be a good solution?
2. I tried to find some suppliers of such electroless plated screws without success. Any suggestion where to look for it?
Thank you, Tony
Product Designer - Quebec, Canada
October 20, 2011
A. Actually, SS screws are more compatible with both the Ni and the aluminum than coated steel parts. The SS should be cheaper than plated ones and coating failures are N/A with SS.
James Watts- Navarre, Florida
A. Hi Tony,
James offers good advice; all that I would add is that raw uncoated, non-anodized aluminum is a poor material of construction from several viewpoints, but aluminum screws are available.
Luck & Regards,
Ted Mooney, P.E. RET
Striving to live Aloha
finishing.com - Pine Beach, New Jersey
Q. Can you advise me on the best type of paint to re-spray my wheelchair with please? I want to re-spray it to sell it. Thanks
Phillip Taylor- Manchester England
January 12, 2021
A. Hi Phillip. That is a bit vague. Presumably you're talking about the metal, not the vinyl (which would not use paint, but vinyl dye ⇦ on eBay or Amazon [affil links] ? When you say "re-spray" you're implying aluminum that is already painted or powder coated not bare or chrome plated? If pre-painted all you have to do is wash and lightly sand, then any spray paint made for metal: Krylon, Rustoleum, etc. But the sun's UV rays are very bad for epoxy, so avoid epoxies like appliance enamel if it will be in the sun a lot.
Luck & Regards,
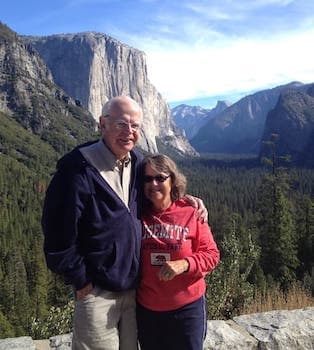
Ted Mooney, P.E. RET
Striving to live Aloha
finishing.com - Pine Beach, New Jersey
Q, A, or Comment on THIS thread -or- Start a NEW Thread