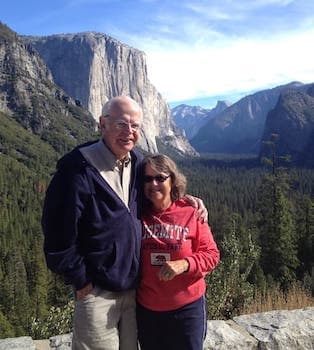
Curated with aloha by
Ted Mooney, P.E. RET
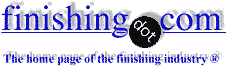
The authoritative public forum
for Metal Finishing 1989-2025
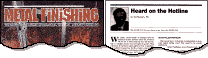
-----
Polishing Stainless Jewelry in Vibratory Tumbler
Q. I have 410SS sheet metal parts. They are small. Several bends. The parts come from heat treat satin silver. Can you polish them to bright shiny finish?
KJ Ramm- Maricopa Arizona
August 26, 2022
privately respond to this RFQ
Ed. note: As always, gentle readers: technical replies in public and commercial replies in private please (huh? why?)
A. Hi KJ. Although the several bends may make manual polishing difficult, in general it is possible to tumble or vibratory finish to a reasonably bright finish -- so we appended your inquiry to a good thread on the subject.
Sorry, but it isn't clear to me whether you are looking for technical information about how to do it yourself, or for quotes from a polishing shop. But if the latter, they'll probably need to know quantities and required schedule.
Luck & Regards,
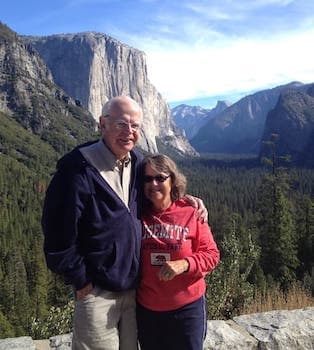
Ted Mooney, P.E. RET
Striving to live Aloha
finishing.com - Pine Beach, New Jersey
⇩ Related postings, oldest first ⇩
Q. I am starting a small business making stainless steel jewelry. I plan to start with laser cut parts and finish them to a nice luster (if not polish) I believe that the route for me would be to tumble (or vibrate) deburr the parts and then continue do refine the media until I have a good finish. Could someone tell me if this is a good strategy and if so what sort of media I should use. (I am completely new to this field and need some basic advice).
The parts will be made of .1 inch SS and will be about the size of a fifty cent piece.
Thanks,
Erik Haugaard- Seattle, Washington
2001
A. Sounds good. Vibratory or centrifugal finishing systems are the normal way to go for polished finishes. Vibratory equipment less expensive but takes a little longer. Media depends on your existing surface finish. I suspect RMS of raw material at 35 RMS, but edge cut maybe be rougher; therefore, you may have to start out with a fast cut ceramic and switch over to either a medium or fine cut. Then you have to options to burnish with either steel or porcelain or pretreated dry organic polishing materials.
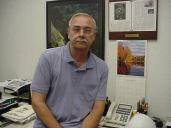
AF Kenton
retired business owner - Hatboro, Pennsylvania
Multiple threads merged: please forgive chronology errors and repetition 🙂
Polishing stainless steel muffler end caps
We need to find the best possible solution to polish our t-304 stainless steel muffler end caps to a mirror like finish. We need to remove minor scratches and minor forming marks. The component is elliptical with edges formed at 90 degrees. At present we are using a buffing process but have been told to perhaps look at vibratory or rumbling process.
Mark [last name deleted for privacy by Editor]manufacturer of after market motorcycle mufflers - Wellington., nth island, New Zealand.
2003
Yes, a mirror finish can be achieved with mass finishing equipment; however, it may only be 95% or a hand buff finish. Then again that maybe acceptable considering the labor cost savings. Can't tell you much more until I know the volume of parts to be processed and in what time frame. Meaning there are options and cost of equipment and supplies involved.
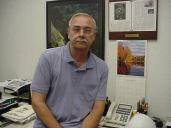
AF Kenton
retired business owner - Hatboro, Pennsylvania
Thank you for your response A.F, the volume would be approx. 50-120 units per week at present, the size of the part is 130 mm X 100 mm X 18 mm high. The time taken is not an issue as the most important factor is to have a consistent finish. We have a tumbler but we have to find the best possible solution.
Mark [returning]manufacturer - Wellington
Based upon the size of the part and volume, I think this can be done in our 1 cu.'ft.'. vibratory machine system. Maybe 10 pounds per batch. You may require a 2 step process. I forgot to ask you what the surface finish of the materials are before processing. If you need assistance, we can run some samples to develop the process and/or media.
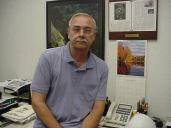
AF Kenton
retired business owner - Hatboro, Pennsylvania
I would go with AF's answer of working your components on a vibratory bowl. The required finish may be obtained 2-3 steps. The minor scratches and minor forming marks can be removed using some kind of abrasive media and then polishing can be done either using S.S. balls or plastic media. To further achieve higher finish it may be run in corncob or maize (dry natural media).
Niranjan S. KulkarniFinishing Machines - Thane, Mah, India
Multiple threads merged: please forgive chronology errors and repetition 🙂
Polishing Stainless Steel Bolts in Vibratory Tumbler
Q. I am trying to polish stainless steel bolts and washers in vibratory tumblers. We are a relatively small production shop polishing 15000 pieces per week. We are not having much success using a single step polishing process using a polishing media known as Dri-Shine. I would like to process 1200 pieces in a 8 to 12 hour period using a 6 quart capacity machine. The machine has a weight capacity of 22 to 25 pounds maximum load and at that weight produces 3000 vibration cycles per minute.
My question is, If I would like a near mirror finish from a naturally supplied bolt finish, what compound or compounds should I be using to achieve this?
Thank you for your help in advance.
- Eau Claire, Wisconsin
2006
A. Lots of luck with your equipment and time cycle. I make industrial systems that still can not achieve the results you are looking for in that time frame. Close but no cigar. You are under powered with machine you mentioned and good polishing results require about 24 hours or more unless you use centrifugal systems which we also make. Even with a high energy system, you may still not achieve the same results you will get from a hand buffed finish. Again close, but no cigar, but it will be closer to 8 hours instead of 24. Media is not as important as heat and rouge. Also you may be able to speed up the times in all processes by going to a 2 step process. SS hardware is a lot rougher than you think. You need a cut down media first or one step and excessive wear, tear , and time.
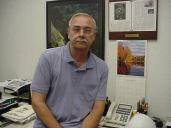
AF Kenton
retired business owner - Hatboro, Pennsylvania
Q. Understood. I can accept a 24-hour cycle from raw stainless to completed product. I might be able to accept somewhat longer than that. Can you provide some recommendation for a cut down media and second process media as well as approximate processing time for each?
I am willing to experiment a bit and adjust times. I do not expect to achieve Mirror Finish, But I am looking for a good appearance with a brilliant shine. If time in the equipment must be longer, that is acceptable. Finish product in the greatest concern.
Any help and direction that you can provide would be greatly appreciated.
- Eau Claire, Wisconsin
A. We spoke via telephone and I sent you some more aggressive media. Please advise how you made out.
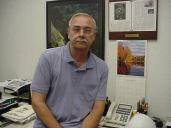
AF Kenton
retired business owner - Hatboro, Pennsylvania
Multiple threads merged: please forgive chronology errors and repetition 🙂
Vibration Finish(Non-directional finish) on Stainless Steel
Q. Hi, I am a stainless steel fabricator. I am looking forward to develop the vibration finish on Stainless steel Flats. These flats are normally 100mm wide and 4 meters long. Also, the raw finish of these flats is H/R (hot-rolled finish). Can someone guide me how to obtain the Vibration Finish on these kind of surface or normal 2B finish surface. Please advise me if there is some machine manufacturer who can give this kind of finishing machine.
Vinod SahayStainless Steel Fabricator - Mumbai, Maharashtra, INDIA
July 31, 2008
Ed. note: This RFQ is outdated, but technical replies are welcome, and readers are encouraged to post their own RFQs. But no public commercial suggestions please ( huh? why?).
A. As you should know, a 2B finish is a rolled finish produced by the steel mill. It would be easier to purchase that than to try to duplicate that finish and it would be more costly. A wide belt sander might be able to do the job, but again time and materials would be more costly than to purchasing it as is. There is no acceptable vibratory system that can do that large of a part/sheet.
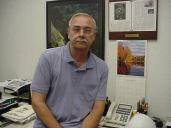
AF Kenton
retired business owner - Hatboro, Pennsylvania
Q. How did things come out? I too need to polish a few stainless parts that I had water jetted. I plan to use a rotary tumbler to clean them up. Time is no issue but I have no idea what media to use. I have a pound of small parts at a time and want to get a decent finish on them before brazing s they will polish up afterwards.
Thanks
hobbyist/designer - Ames, Iowa
June 11, 2010
Q. Mr Kenton. You sound like the right person to talk to.
I am trying to start a small cutlery refurbishing business. I have build a vibrating polisher. I am using small porcelain beads but the result is not good. I can not get anyone to help me in getting the right advice on the correct media and compounds to use. Should I use stainless steal balls? from responds to other enquiries I gather that I will not be able to get a mirror finish. My stainless steal cutlery is dull after 7 years of use. I know I will not be able to remove deep scratches with the vibratory polishing. Can you please advise.
Thank you.
- Port Elizabeth, South Africa
August 26, 2011
Parameters for vibratory tumbling stainless 1/4" washers
Q. I have tried many things and steps and can't get anything to work.
I have a 18 lb vibratory tumbler. Please help.
Thank you.
Tom
hobbyist - Los Angeles, California, USA
September 8, 2010
A. You didn't say what you were trying to achieve; however, my interpretation of your question is that you want to achieve a bright or reflective finish. If that is the case, you want to select a media that has no abrasive. That means mostly steel or porcelain with a good lubricating compound or treated dry organic media. Your 18# machine won't process steel. Need more info for more specific process.
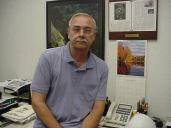
AF Kenton
retired business owner - Hatboro, Pennsylvania
? Info required: size and type of machine, part to be processed (material, size, quantity), desired effect. Then I can answer.
Robin Thedemetal finishing - Toronto, Ontario, Canada
Multiple threads merged: please forgive chronology errors and repetition 🙂
Q. Dear all,
We have stainless steel sheet mirror finishing plant. We regularly process stainless steel 304 grade stainless steel sheets to mirror no.8 finish. Recently we tried to polish slightly rusted stainless steel 410 grade sheet.For polishing we use water + nitric acid + red oxide solution.However after polishing stainless steel 410 slightly rusted sheet we observed that the almost complete sheet gets mirror polished but same part of the sheet where the sheet was slightly rusted gets completely black. Please help me to know the exact reason why sheet gets tar black and how it can be avoided from getting black.
Regards,
Amit Kulkarni
Director
Polisher - New Delhi, Delhi, India
June 29, 2011
A. My dear Amit the process which you are doing is wrong. Red oxide will get dissolved in nitric acid, and the acid will help the rust to increase. I suggest you to use following three steps for rusted sheets. Step 1 buff the sheet with Crown 2011 polishing compound, Step 2 buff the sheet with Crown 2015 this two steps will remove the rust from the sheet and will make the surface plain and in Step 3 buff the sheet with Crown 4020 and you will get the bluish mirror finish.
Mahedu Dharmendrasinhabrasives - Jamnagar, Gujarat, India
----
Ed note: thank you for the suggestions, Mahedu, but please give grit size, or other generic information on these polishing compounds, not proprietary model numbers ( huh? why?)
Polishing flat stainless steel motorcycle bottle openers
April 3, 2017Q. Hi guys, I had a company laser cut from stainless steel a motorcycle bottle opener that I designed. This was over 5 years ago. The problem I ran into was when they were run in a tumbler they smacked into each other causing pits in the pieces. Perhaps I had a sharp edge on the piece? Any suggestions on deburring and polishing these pieces???
Thanks,Dan Daly
- Lee, New Hampshire
A. Hi Dan. The parts don't need to tumble. As one alternative, you could vibratory finish them.
Regards,
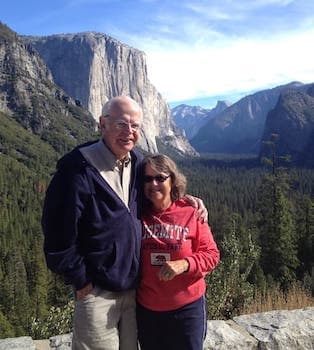
Ted Mooney, P.E. RET
Striving to live Aloha
finishing.com - Pine Beach, New Jersey
April 7, 2017
A. Flat parts present a special SOB of a problem when trying to mass finish them, especially with a wet process. Water forgets it is water and acts/behaves like glue. Normally you will not get a uniform finish on all parts per batch. It is best to run them in a dry process; however, it is a very slow process. To speed that process you can go to dry burnishing.
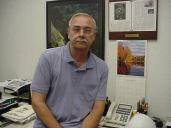
AF Kenton
retired business owner - Hatboro, Pennsylvania
April 2017
Q, A, or Comment on THIS thread -or- Start a NEW Thread