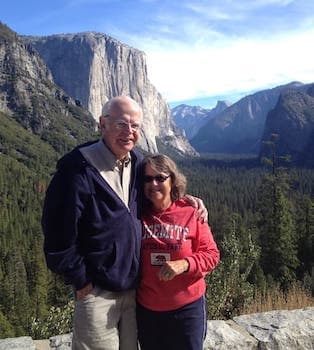
Curated with aloha by
Ted Mooney, P.E. RET
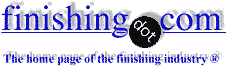
The authoritative public forum
for Metal Finishing 1989-2025
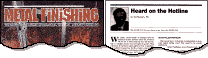
-----
Immersion copper coating of MIG welding wire
Q. WE ARE LOOKING FOR CuSO4 CHEMISTRY TO COAT STEEL WIRE WITH COPPER, AT THE OUTPUT OF STEEL WIRE DRAWING MACHINE WHICH DRAWING THE WIRE AT 30 METERS PER SECOND. THIS HIGH SPEED WIRE DRAWING APPLICATION NEED A FAST ACTING COPPERING SYSTEM AS WELL.
WE WOULD APPRECIATE YOUR HELP.
SINCERELY YOURS,
DR. MEIR F [last name deleted for privacy by Editor]- MAZKERET-BATIA, ISRAEL
1998
A. Hi, Dr. Meir. I assume you are talking about an immersion copper process when you say it should be CuSO4-based. I would assume proprietary immersion coppering processes are available, but certainly the higher the concentration of copper, and the warmer, and the more active the agitation, the faster it will plate.
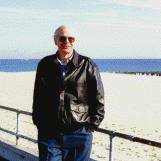
Ted Mooney, P.E.
Striving to live Aloha
finishing.com - Pine Beach, New Jersey
1998
A. I think that there is a process for immersion copper plate. It is used to copper plate ground rods for houses, etc. I doubt that any immersion process will be able to meet that speed requirement. I sort of doubt that an electrolytic process can meet it. It would require a very long tank or awesome agitation and an extremely high current and probably warmer tank temps.
James Watts- Navarre, Florida
1998
A. Our Company designs and manufactures equipment for surface treatment in a variety of industries. We have worked in the CO2 weld wire industry. Your requirement is extremely challenging and requires optimal performance from several interdependent variables such as chemistry, drawing equipment, dies, cleaning, lubrication, and surface treatment equipment. Theoretical possibilities are not always practical on the factory floor. Good luck.
Walter Yost- Leetsdale, Pennsylvania
1999
A. IT IS CONVENTIONALLY POSSIBLE TO COAT ANY STEEL BY METHOD OF DEPOSITING COPPER BY DIPPING IN copper sulphate ⇦ this on eBay or Amazon [affil links] SOLUTION. MY EXPERIENCE IN COATING INDUSTRY FOR CO2 WELDING WIRE, SAW WIRE, TIRE BEAD WIRE WITH SYSTEMS FROM GERMANY, ITALY, FRANCE. ENGLAND, JAPAN AND USA DOES NOT GUARANTEE A SYSTEM WHICH CAN RUN AT A SPEED OF ABOVE 25 MTRS /SECOND .
THE SYSTEM OF COATING DEPENDS ON HOW CLEAN THE WIRE SURFACE IS, HOW GOOD THE COATING CHEMICALS AND ADDITIVES, AND HOW MUCH COATING IS REQUIRED ON THE SURFACE EXPRESSED IN GRAMS. AND ALSO ON THE SIZE OF THE WIRE, VIZ., DIAMETER OF WIRE.
HAVING WORKED IN THIS LINE FOR MORE THAN 25 YRS AND ESTABLISHED GOOD RESULTS IN INDIA AS WELL AS INDONESIA OF PLANTS IN THE ORDER OF 3000 TONS PER ANNUM CAPACITY WOULD LIKE TO SHARE MY EXPERIENCE: I
I HAVE REALLY YET TO COME ACROSS A SYSTEM WHICH CAN CONSISTENTLY RUN AT HIGH SPEED IN INDUSTRIAL SETUP WITHOUT UPSETTING THE QUALITY OF END PRODUCT.
WITH BEST WISHES.
R.SREEDARAN,- mumbai India
2000
August 10, 2012
Hi
Chemetall manufactures coppering processes suitable for coating wire at low and high speeds.
Best regards
Milton Keynes, Bucks, UK
1999
Q. Dear sir,
Is there any passivation compound available for copper coated steel wire to increase its shelf life without affecting its weldability?
Is it possible to give strike solution with dipping process before the wire enters the main copper coating tank? Does it help in improving the coating?
Mukesh AgarwalRFQ: I HAVE SUCCEEDED ON COPPER COATED WIRE DRAWING PROCESS. IT'S AN ELECTROLYTIC METHOD. FOR THE ABOVE DRAWING WE USED CONVENTIONAL WIRE DRAWING MACHINE, SO THE PRODUCTIVITY IS VERY LOW. BUT WE ACHIEVED VERY HIGH QUALITY. WE ARE LOOKING FOR WIRE DRAWING MACHINE PARTICULARLY COPPER COATING ONLY. EXPECTING YOUR ADVICE. THANK You.
M.ILANGO- tamil nadu state, coimbatore, India
2000
Ed. note: This RFQ is outdated, but technical replies are welcome, and readers are encouraged to post their own RFQs. But no public commercial suggestions please ( huh? why?).
RFQ: Dear sir,
I am a production manager of CO2 manufacturing company, I need your help. Where can I purchase your additive acid? i.e., candor additive acid for copper coating process? Five years ago we were using your candor acid, but my former purchaser cannot purchase at the moment, I don't know why, if you have this product, please respond to me.
Thank you
G.SUBRAMANIAM- MALACCA, MALAYSIA
2001
Ed. note: This RFQ is outdated, but technical replies are welcome, and readers are encouraged to post their own RFQs. But no public commercial suggestions please ( huh? why?).
Q. What could be the possible reason(s) for copper particles coming off from CO2 copper coated MIG welding wire conforming to ER 70S 6. The fine copper grains (particles) chokes the liner of the MIG welding machine and has to be cleaned after every 3-4 hours. Is it some problem with wire or machine setting parameters?
Ebadullah- Jubail, Saudi Arabia
2002
A. Dear Sir,
Normally the copper coated wire having 0.25-0.35%. Some of the wire manufacturer not maintaining the copper coating % and more % gives copper choking in the liner. This is not a machine problem, it is wire problem only. Change to another supplier to sort out this problem.
Thanking you,
V.KANNAN- Pondicherry, India
2002
Q. I want to know more about the co2 wire coating. Maybe say I want to know how to procedure the best of best CO2 wire.
Vishal Suresh Jagottamanufacture - Nashik, Maharashtra, India
2004
Q. Hello,
My search for free advice has brought me to this forum! Our plant in Pakistan is manufacturing special stick welding electrodes for a couple of years. We are looking at extending our product range. Our next range of products include CO2 MIG wire and stainless steel MIG wire. Currently I am looking for equipment providers and also advice on each step of the process e.g. starting from MS wire drawing to pickling, copper coating and precision winding in case of CO2 MIG wire. I know I am asking for free advice but would appreciate helpful guidelines.
Best regards
- Lahore, Punjab, Pakistan
2005
Ed. note: This RFQ is outdated, but technical replies are welcome, and readers are encouraged to post their own RFQs. But no public commercial suggestions please ( huh? why?).
2005
A. Hi, Jawwad.
This site is about metal finishing, so it doesn't cover wire drawing or precision winding, but it will include advice for pickling through copper coating. You can find vendors in our Capital Equipment directory if they don't contact you. I don't know enough about the CO2 process to be able to help you, but hopefully another reader will.
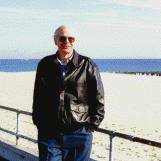
Ted Mooney, P.E.
Striving to live Aloha
finishing.com - Pine Beach, New Jersey
Q. I am a chemical supplier to a company making copper coated welding wire. I'm not a fundi on the process, however I am trying to help them with their weldability problems (burn-back and nibbling), which they originally thought was due to deposition of metals (especially manganese) on the wire before coating. The water used in the baths for Caustic, rinse, and sulfuric acid is town water with high TDS and metals. We have changed the entire bath to demineralized water and still get a black slimy deposit on the wire, and poor weldability. My feeling is this is not from the water but rather from drawing soaps, oils, dust etc which is not cleaned properly from the wire. Please advise on what steps to take to get to the route cause of our problem.
Steven LeaImprochem - Johannesburg, South Africa
2005
A. Your trouble seems to be popular. I don't think it is related with copper plating process. Your guess is right, it is probably caused by such residuals drawing soap, micro fine iron powder, other contaminants. But please doubt cleanliness of steel's surface. If wire rod is mechanically descaled (not acid cleaned), scale and sub-scale remain heavily. After copper plating it becomes rust. Rusty wire gets feed-ability incredibly worse and causes severe abrasion of contact tip. If you want to check rust of finished wire, give 4.0-5.0V(+) to finished wire in 5% salt water and observe floating substance. If it looks brown, the tested wire is rusty. I hope my information will help you. Thanks
Koichi Nomura- Kakogawa, Hyoggo, Japan
2006
A. Mn deposits on the wire cannot affect welding results on MiG/ MAG welding.
I have observed similar effects due to faulty water cleansing. I mean the pH of the finish water bath and in consequence the wire.
- Martinez, Buenos Aires, Argentina
August 4, 2013
Q. The copper coating process used by us is plain Chemical Coating. I.e., it is not electroplating.
The problem faced by us is that after coating, when the wire is further drawn, sometimes the shining on the wire is not glossy. The color also changes.
This problem is very regular. We have been informed by some reputed manufacturer that some chemical additives are to be used in copper sulphate bath to enhance the gloss & finish of Copper Coated wire.
Can you lend us some help in this matter.
precision wire - Nagpur, Maharashtra, India
2005
A. I hope you are adopting copper sulphate coating process in an acidic medium using sulfuric acid to maintain pH around 2.0 to 3.0. The copper sulphate that you intend to use should be pure grade not a commercial one which contains impurities and low strength.
Regards,
- Chennai, India
March 22, 2012
Q. During producing wire for CO2 welding the wire gets coated with copper but when it is drawn quickly bright appearance doesn't occur. How to increase the copper coating as well as speed of wire drawing?
Karthikeyan rstudent - Chennai, Tamilnadu, India
April 9, 2008
Q. Dear Sir,
We would like to know if there are any additives which are added into copper sulphate for manufacturing CO2 Mig Wire Coating.
MANUFACTURER - AMRAVATI, India
October 17, 2011
Q. Is there is any additive mix with copper sulphate to get better shine in MIG welding wire
Hanish Mohindru- India
January 28, 2012
Q. We manufacture copper coated mild steel wire (MIG welding, SAW welding wires).
We notice that the coating is not uniform sometimes, and have complaints about the consistent adhesiveness of the copper coating (due to which wire has feeding problems).
What could be the possible reason?
Is wire not cleaned properly before entering the copper bath, or do we need to add some additives in the copper bath to get proper adhesion or maybe some other issues?
- Delhi, India
October 3, 2012
May 6, 2014
Q. Dear Sir,
I want to test our wire as per your advise, but I need a few clarifications (Pardon me).
1) The wire to be tested is after copper plating.
2) 4-5 V + to the wire in 5% (NaCl) salt water.
We are currently using only mechanical descaling. Should we prefer wire rod brushing post descaling or go for chemical pickling?
We are not using borax or phosphate coating either.
- Muzaffarnagar, UP, INDIA
Is copper coating on steel wire possible?
Q. We want 1.5 mm low tensile copper coated ms wire. How is it possible?
raman vk- vellore, tamilnadu, India.
November 9, 2014
November 2014
Hi Raman. Your inquiry is a bit too brief. Are you having difficulty finding anyone in the world who will sell you this, or just anyone in Vellore? Or have you found the steel wire but want to do the copper coating yourself? As we often say here, please make your question longer than the answer you want :-)
Thanks and Regards,
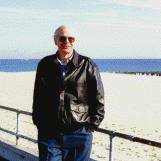
Ted Mooney, P.E.
Striving to live Aloha
finishing.com - Pine Beach, New Jersey
Q. Have you ever found the solution to your problem as we are experiencing the same problem? Could you let me know.
Terence
welding - South Africa
January 21, 2015
January 2015
Hi Terence. While it's clear to you, with many different questions in this thread we don't know if your "same problem" is your wire losing its shine when you draw it, or if you are suffering inconsistent & inadequate adhesion, or you're having difficulty finding low tensile copper-coated MS wire, or what, because there are several open questions here. Do you have any advice for any of the other situations while we're waiting for an answer for you? Thanks.
Regards,
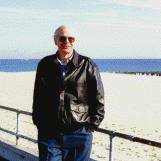
Ted Mooney, P.E.
Striving to live Aloha
finishing.com - Pine Beach, New Jersey
September 26, 2016
Q. Hi,
We are facing the same problem as Devendra. Our process is the same, i.e., Chemical Coating (immersion plating).
We realized that with the increasing iron concentration in the bath, the appearance of the wire started to get less copper-plated and bright.
I would like to know if there is a relationship between the iron concentration in the bath and the appearance of the wire and what we should do to reduce this iron concentration (a regular bath renovation, for example)?
Regards,
- Porto Alegre, Brazil
Q. Hi. I want to know how to directly cover steel wires with high speed copper solution?
shiba ash- iran
March 4, 2019
See also topic 56043, "Plating copper onto MIG wire"
Q, A, or Comment on THIS thread -or- Start a NEW Thread