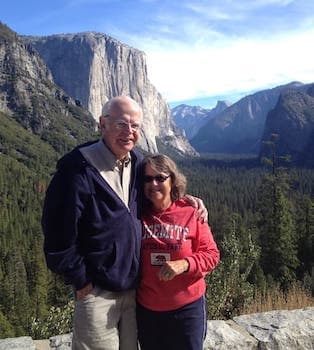
Curated with aloha by
Ted Mooney, P.E. RET
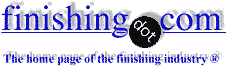
The authoritative public forum
for Metal Finishing 1989-2025
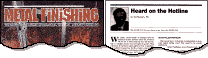
-----
Tin Plating on Aluminum -- is intermediate layer of copper needed?
Q. Our current process on Wrought aluminum includes 1) Caustic treatment 2) Zincate Dipping 3) Copper Plating 4) Tin Plating.
I have a question whether copper plating is really necessary for Tin adhesion on Aluminum (Wrought condition)?
We are not doing the process of electroless strike of nickel. Can you please help me elaborate on the process?
Our requirement is bright finish Tin plating on wrought aluminum.
Also I want to know should we add another process for bright finish?
Hoping for your comments...
- India
2005
A. Hello Mr Charu,
The copper is required to protect the zincate as the zincate may strip off in the acidic tin bath. Yes you may consider it a necessary step.
Best,
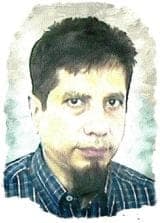
Khozem Vahaanwala
Saify Ind

Bengaluru, Karnataka, India
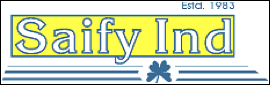
A. Hello Mr. Charu,
You can try Nickel in place of copper after zincate. The nickel will give brightness to the tin layer.
- MUMBAI, India
I don't know, Mr. Ramesh. Copper plating then nickel plating is okay. But nickel plating will (in my limited experience) strip off the zincate.
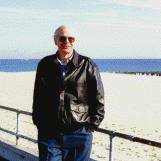
Ted Mooney, P.E.
Striving to live Aloha
finishing.com - Pine Beach, New Jersey
A. Hi,
You can use either copper or nickel, both will dissolve the zincate. I believe only alkali EN nickel will be plated over zincate. If you use copper plating over aluminum you must have the right pH-range.
Regards,
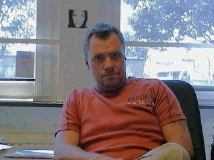
Anders Sundman
4th Generation Surface Engineering
Consultant - Arvika,
Sweden
A. I beg to differ with Ted, I have successfully used a zincate treatment on aluminium alloys and plated nickel onto it. Furthermore, it has withstood excessive thermal cycling as an engine bearing without failing. In my opinion, you can use nickel or copper with zincate.
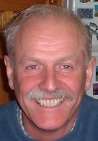
Trevor Crichton
R&D practical scientist
Chesham, Bucks, UK
My error, Trevor, thanks! I'm personally only familiar with using either alkaline copper plating or alkaline electroless nickel as the first layer on top of zincate, but just because I haven't seen nickel plated directly on zincate doesn't make it undoable :-)
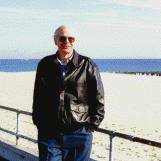
Ted Mooney, P.E.
Striving to live Aloha
finishing.com - Pine Beach, New Jersey
A. The common process of tin plating on aluminum is mild caustic treatment - zincating - copper plating and finally tin plating.
Arjun singh- Haridwar, uttrakhand, India
February 13, 2014
Immersion plating in Stannate in lieu of Zincate
Q. We are a leading switchgear company at Saudi Arabia. We currently make our panel board neutral bars with brass having tin plating. We want to move to Aluminum 6061 T6 with tin plating. I believe we would need to do a zincate layer, followed by a copper plating layer and then finally Zinc ^ tin. Can any of you please advise, what should be the thickness in microns for each of the layers.
- Riyadh, Saudi Arabia
February 27, 2012
A. Let's "keep it simple", and just use stannate instead of zincate, then go right on top with bright tin.
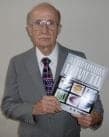
Robert H Probert
Robert H Probert Technical Services

Garner, North Carolina
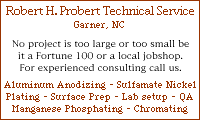
That's thinking right, Robert. Thanks. You made me recall visiting a large GE aluminum bus bar factory using Atotech's Alstan process to plate miles of bus bar. Although I think Alstan usually had a bronze plate between the immersion tin and the electrolytic tin.
Regards,
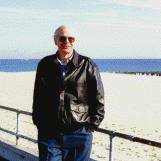
Ted Mooney, P.E.
Striving to live Aloha
finishing.com - Pine Beach, New Jersey
A. I'm not sure whether or not this will meet your requirements, but aluminum pistons were often immersion tin plated directly in a mildly alkaline bath containing polyphosphates. If this process is good enough for your parts, then it would be much simpler than a multi-step process that starts with zincating.
Lyle Kirmanconsultant - Cleveland Heights, Ohio
March 1, 2012
Thanks for the reminder, Lyle. Now I remember seeing that at the Ford engine plant in Cleveland there many years ago.
Luck & Regards,
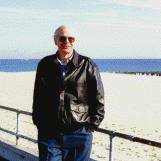
Ted Mooney, P.E.
Striving to live Aloha
finishing.com - Pine Beach, New Jersey
Tin plating discolors and blisters at 360 °F
Q. We specify tin plating .0002 to .0007 thick on 6061 T651 aluminum rod. The plating is to withstand 275 °F for 2 hours with no blistering or removal with a tape peel test. In actual use the rods will experience a series of thermal conditions: 180 °F for 2 hours, to ambient for up to two weeks, 200 °F for up to 8 hours, 300 °F for 6 minutes in a mold, cool to ambient for undefined period, 360 °F for 2.25 hours in natural gas oven.
We experience blue discoloration and blistering of the tin plating after the 360 °F for 2.25 hours.
Obviously our specification is suspect.
Is it possible for tin plating to withstand 360 °F when heated in a natural gas oven. If so, what are the proper plating process requirements i.e., cleaning pretreatments, strikes, etc.
Manufacturing Engineer - Pewaukee, Wisconsin, USA
May 1, 2012
A. The only inorganic tin that is black is SnO. Since the melting point of pure tin is 446 °F There is a high probability it is the oxide of tin.
They only way to prevent this is to do it in a reducing atmosphere or a vacuum furnace.
- Navarre, Florida
A. It is possible that the aluminium is forming a eutectic alloy with the tin. I do not believe that Al-Sn forms a true intermetallic compound, but tin is "soluble" in aluminium and it has a eutectic with a melting point of 227 °C (441 °F). Alloys of metals have different colours to the pure metal constituents, so that could give the blue appearance, but it will not account for the blistering.
It is possible that as the tin layer is depleted by its migration into the aluminium, it is allowing the aluminium to oxidise and undermine the tin-aluminium interface - this could cause blistering.
I am of the view that a barrier layer is needed to prevent tin migration; this can be achieved by using a zincate process on the aluminium and then deposit a layer (~5 um) of either nickel or copper. The tin will form an intermetallic with both copper and nickel, but it should stop migration into the aluminium and subsequent broad failure.
I would also suggest that before spending too much time on trying to resolve the blistering, do some basic analyses and find out why the tin layer is blistering. You can get a lot of information from simple SEM studies, coupled with EDX.
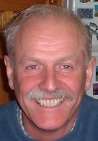
Trevor Crichton
R&D practical scientist
Chesham, Bucks, UK
Tin plating on copper plating on aluminum loses adhesion in shipment
Q. We are a company based in India manufacturing electrical assemblies for the US market. Our product requires a variety of parts including zinc coated mild steel sheet parts and extruded aluminum (6061 T6) parts coated with tin. We are facing a peculiar problem in our plating process.
Last year, all the parts that we exported during the monsoon season in India (June to August) were rejected by the customer due to rusting of steel parts and poor adhesion on the tin plated aluminum parts. We did not change any process of coating these parts but all shipments sent during the monsoon season were rejected.
We changed our plating supplier and got parts plated which were promising. The steel parts were showing a salt spray result of 300 hours for red rust. The tin plated aluminum parts were showing excellent adhesion. Unfortunately, our first container from the monsoon season has reached the US and has been rejected for the same issues. Thankfully, we have kept samples from each batch produced. When we checked the parts we had, they still are showing excellent adhesion on the tin plated parts.
To counter the rust issue, we are now vacuum packing the parts and are sure that this will sort out the rust issues on the plated steel parts. However, we are not sure what improvements we need to do on the tin plating.
We use double zincating process, followed by copper plating (1.5-2 microns), followed by tin plating (8-10 microns). These parts are rack plated.
Are we doing something wrong in processing these parts? Is the high humidity and rusting of steel parts affecting the adhesion on the tin plated parts?
Please help.
Manufacturer - Nasik, Maharashtra, India
September 5, 2012
A. Need more information related plating time and type of copper salt you are using. I think you should use lacquer-based anti-tarnish which protects tin plating from salty atmosphere. Such types of products are available in the market which are conductive also.
Gurudatta Thakur- Mumbai, India
September 14, 2012
QUICKSTART:
To avoid confusion, we should explain that there is a difference between "immersion plating" and "autocatalytic plating", and that to many people in the plating industry, "electroless plating" implies "autocatalytic plating", not "immersion plating".
Example: If you dip a steel component into copper sulphate, a thin layer of copper will form on the component and the deposition will stop when no more steel is left exposed -- this is called immersion plating.
But if you dip a catalyzed plastic circuit board into an "electroless copper" plating bath, the bath contains a reducing agent so that it is sort of "spring loaded" and is activated by copper itself as well as the original catalyzing agent -- so copper continues to deposit as long as the board remains in the tank; this is called "autocatalytic plating" or "electroless plating".
Can aluminum be electroless copper and electroless tin plated?
Q. Is it possible to do electroless copper and electroless tin deposition on aluminium surface?
Divahar Selvaraj- Chennai, India
October 8, 2014
A. Hi Divahar. Immersion tin plating on aluminum is both possible and practical. Please see Robert Probert's and Lyle Kirman's replies above. I'm not familiar with electroless copper on aluminum, but hopefully another reader will be.
Please use several sentences to describe your situation as it's not clear whether you want electroless tin deposited on top of the electroless tin, or whether you are asking two different questions in your one sentence. And I'm also not clear if your question is restricted to autocatalytic plating or includes immersion plating. Thanks.
Regards,
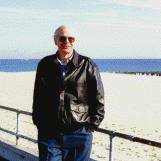
Ted Mooney, P.E.
Striving to live Aloha
finishing.com - Pine Beach, New Jersey
Alstan Plating on Aluminum Bus
Q. My Customer's specification requires Alstan plated aluminum bus bar: "...layer of Tin over a layer of cu or bronze..." and "...Zincate is not acceptable..." and "...shall have a bright uniform coating...". There seems to be confusion even with platers as to what exactly qualifies as Alstan. The trademark appears to have been established in the early 60s. I don't really find anything online where they sell the specific process chemicals. Any background on the process would be appreciated.
Al PruittElectrical Metering and Distribution Equip Manufacturing - Houston, Missouri USA
December 1, 2014
A. Hi Al. Alstan ("all tin") was an M&T Chemicals (now Atotech) process. I don't know if they still offer it, but that would be a good place to start. The process includes an immersion plating of tin instead of zinc (stannate instead of zincate) and includes a top layer of electrolytic tin plating -- but I think there was usually an electrolytic bronze plate between the immersion stannate and the electrolytic tin plating.
Regards,
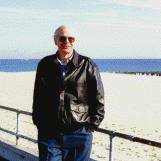
Ted Mooney, P.E.
Striving to live Aloha
finishing.com - Pine Beach, New Jersey
Q. Thanks for the response. I have a plater that reports they can provide matte Alstan but not bright. What is the basic difference in a bright Alstan and a matte Alstan process.
Al Pruitt [returning]Electrical Metering and Distribution Equip Manufacturing - Houston, Missouri USA
A. Hi again. According to some legal websites, but I don't know that their information is accurate and timely, the Alstan trademark is still held by Atotech, but the process is no longer offered in the USA. That would mean that you can't actually call it Alstan anyway. Google books has some short abstracts which seem to indicate that the Reynolds "Aluminum Finishes Process Manual" ⇦[this on eBay, AbeBooks or Amazon affil links] has good explanations of the many Alstan processes if you can get access to a copy (sorry, I don't have it).
Obviously, I don't know the dynamic between you and your customer, but I would suggest talking to them about this situation where they have specified an obsolete and unavailable, and largely unknown, process. Maybe they would be interested in updating their specs to something more modern and available. Good luck.
Regards,
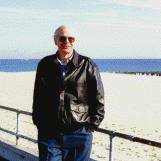
Ted Mooney, P.E.
Striving to live Aloha
finishing.com - Pine Beach, New Jersey
Thanks for your help on this subject. Much Appreciated!
Electrical Metering and Distribution Equip Manufacturing - Lebanon, Missouri USA
December 2, 2014
Q. Hi,
Good to see Aussies on this thread.
I have been working with two stroke pistons and many of them used tone tin plated I believe, and they wear so well in the motor too, but now apparently this coating over the aluminium is being phased out, which means to me that the motors do not last. So yeah, as I like quality and longevity, I am wondering who I can talk to to get this done on a batch of pistons, like maybe 100, not big of course
Cheers William
Chainsaw motor builder - WA AUSTRALIA
September 21, 2021
Ed. note: This RFQ is outdated, but technical replies are welcome, and readers are encouraged to post their own RFQs. But no public commercial suggestions please ( huh? why?).
Readers: Want more input on Tin Plating on Aluminum? See thread 4039
Q, A, or Comment on THIS thread -or- Start a NEW Thread