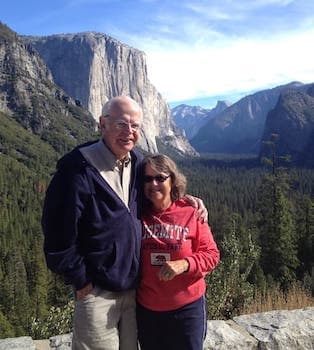
Curated with aloha by
Ted Mooney, P.E. RET
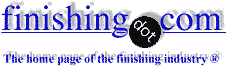
The authoritative public forum
for Metal Finishing 1989-2025
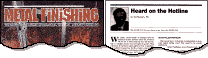
-----
Does the substrate hardness affect the hardness of the chrome plating?
Q. What are the possible substrates for chromium plating especially Cr VI and typical coating thicknesses that are used in this application?
Sia, Watertown, MA
- Bedford, Massachusetts
2007
A. Hello Mashalah. We have an FAQ on Chrome Plating that may be of some help regarding substrates and thicknesses. Required thickness depends on the type of load and the hardness of the substrate. The plating on hardened hydraulic cylinder rods can be very thin, whereas the chrome plating on a copper roller must be quite thick. Thanks.
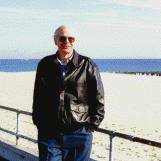
Ted Mooney, P.E.
Striving to live Aloha
finishing.com - Pine Beach, New Jersey
2007
Q. We are using chrome plating for our product. Previously we were asked for 650 Hv hardness after plating. Due to the sudden customer requirement for 850 HV hardness we're having a hard time getting that hardness.
We are Chrome plating over 21-4N and EN-52 materials. Diameter of the material varies from 6 mm to 10 mm. And we are hardening the material before chrome plating to 30 HRC. Chrome plating thickness varies from 3 microns to 7 microns.
Can you tell me whether the parent material over which chromium is plated will cause any effect on hardness of chromium plated over that material? And whether plating thickness causes any effect on hardness of chromium plated. And can you tell me what parameters we should be concerned about while plating to get fair hardness?
Thanks in advance
Process Shop - India
2005
A. Hardness of chrome plate is independent of hardness of base material. Hardness of BOTH makes the real (total) hardness that the part will exhibit against external stress. Think of chrome as a sheet of glass. You can lay it on the floor and it will stand you on it. But if you lay it on a bed?
Guillermo MarrufoMonterrey, NL, Mexico
2005
A. If you are using a microhardness tester, the substrate makes absolutely zero difference. If you are talking about deformation while in use, it makes all of the difference in the world.
Your hardening is rather (very) soft, why so low?
To plate at 850, you will need to do some research of bath compositions. With considerable care and the right bath, you can plate to 850. Some will go higher. I would work with the customer to see why the massive jump in hardness. 750 or even 800 is a lot easier to repeat on a daily basis than 850.
With that little chrome on the part, it is extremely difficult for me to see the need. More chrome probably would work better.
Low phos EN might be an option.
Harder parent metal might also solve the customer's problem.
Can you find out the reason for the additional hardness and get back to this site?
- Navarre, Florida
A. Dear Mr. Balaji,
Actually you are measuring the hardness of the deposition not of the substrate.
It is also not clear what type of chrome electrolyte you're using.
Please check the ratio between chromic acid and sulfuric acid, also it is necessary to check your plating parameters (current density, temperature etc.). Check for any contaminations.
Regards,
- Mexico City, Mexico
2005
2005
A. The base material hardness has nearly no effect on the chrome hardness.
For such a thin thickness of layer you need a hardened base material to avoid getting a destruction of the layer due to penetration at high loads - to reinforce the system to resist a high load.
It seems that you make the hardness measurement on the surface and not in the cross section.
The thickness of layer is very thin and the load is too high. You don't measure the hardness of the layer, you get a mixed value of base material and layer hardness.
You have to make a cross section and to measure the hardness only in the layer. Be careful with the load, not to measure too close to the interface and the surface.
Nice for you but not correct: you need a very low load to be able to make the measurement ("microhardness"). The lower the load, the higher the hardness value is measured on the same sample.
Best regards,
Switzerland
2005
To check the coating hardness you will need to use a microhardness tester. Plate a sample to a thickness of 0.003-0.005" to give a good surface to test.
If you use a normal Rockwell or Vickers hardness tester you are testing the composite hardness of the coating and the substrate (and with a thickness up to 7 microns, mainly substrate), so this will not be a true reflection of the coating hardness.
Hard Chrome plating can usually surpass 850Hv (we ourselves normally get a hardness between 950 and 1000Hv) and I have seen figures quoted up to 1100Hv.
Aerospace - Yeovil, Somerset, UK
Q.
Mr. Marrufo, as per your statement the hardness of the chrome will not change with respect to parent material. Only the testing method make it seem to so, am I right?
V. Ranga Bhuvana BalajiProcess Shop - India
2005
Q. I FACE THE SAME PROBLEM. Please HELP
AMIT KUMAR MISHRA- GURGAON, Haryana, India
2005
A. There is a huge difference between chromium at 650Hv and 850Hv; firstly the 850 Hv would be normally regarded as hard chromium, whilst the 650 Hv more of a decorative finish. secondly, they come from different process conditions. A hardness of 850 is well in the range of hard chromium, so it looks like your customer has changed overall specification. As far as thickness and hardness measurement is concerned - the thickness is very important IF you are not using a microhardness tester. If you are, you need to be careful you do the tests on the crystallites and not in any micro cracks as this will give varying results. Using a conventional hardness tester will put an indent into the chromium. The depth of that indent will depend on the load applied, so you need to be very careful that you use the correct load for the thickness of metal. I would personally recommend a thickness of about 600microns for a hardness of 66Rc, but with Vickers testers you can probably get away with 150 microns (perhaps less) if you use a suitably reduced load. For full specification on Vickers hardness testing look in ASTM E92-82 (1997) or BS EN ISO 6507 (1998).
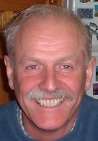
Trevor Crichton
R&D practical scientist
Chesham, Bucks, UK
2005
Ed. note: ASTM E92-82 has been superceded by ASTM E384
Q. First of all I thank to all of you who all shared their experience and knowledge to my problem get solved. Really the problem is with my testing method. Actually we have some standards that describes the minimum thickness of specimen required to measure corresponding to maximum hardness to be measured and load used. Actually I got this idea from your statements only. i.e When you use Vickers hardness tester and Vicker intender to measure hardness, to measure 850 HV hardness using 15 gram load you need at least 7 micrometer thickness specimen. And if you go for Knoop intender the corresponding values may change. I am right now trying for Knooop intender. So I thank you all once again. Mr. Amir, please you go through the conversation. So that you can easily get some relevant message regarding your problem.
V. Ranga Bhuvana BalajiProcess Shop - India
2005
Q. Constant reading for Vickers tester?
Dear all,
when using the vickers hardness tester with a test specimen "252HV10", it gives a reading of 945 though the impression is clear and if I rotate the curves to wrong positions on the impression, I always get the same reading "945" and sometimes "141".
What do you think the problem is?
Thanks in advance.
- Alexandria, Egypt
2006
Can't get HV1100-HV1250 in hard chrome plating
November 27, 2014Q. Hi,
Reading with interest peoples views and opinions re. the hardness of Hard chrome.
We are a Hard chrome plating and grinding company and are having issues achieving a very specific hardness for one of our customers.
They are specifying a minimum hardness of HV1100-HV1250.
The finished deposit is 0.003" thick.
We have supplied 3 samples for Vickers microhardness testing and all have fallen short of HV1100.
The first sample we submitted was just over HV1000 and after adding catalyst in an attempt to get it over the minimum I was surprised to see the second sample measured softer at around HV925.
Another sample was plated in a different catalysed solution but this one was even worse according to the test (around HV880)
My concern is that we will not be able to reach the minimum our customer is asking for.
Not knowing enough about the testing method and it's accuracy at this range (most Vickers scales I've seen end at HV900) I'm sending another sample to a different testing center to double check the result but wondered if anyone on here had any thoughts on this?
Chris
- Sheffield, England, UK
A. Hi Chris,
1100-1250HV is really on the high end of the hardness scale for hard chrome plating. To consistently reach this level I suspect you will need some specialist chemistry. You could try the usual suspects who manufacture proprietary chemistries to see what they have (Atotech, MacDermid, etc).
From a standard chrome tank you will really struggle to get over 1100HV, so it is no surprise that just adding catalyst didn't do the job, it's rather more complex than that.
Aerospace - Yeovil, Somerset, UK
December 4, 2014
Q. Hi Brian,
Many thanks for your response. You've more or less confirmed what I was thinking, unfortunately someone in their wisdom didn't think to check first before committing to this specification.
I believe we have secured a concession for the items we have processed and longer term need to get the spec. re-written to a hardness more consistently and realistically achievable (800-1000Hv)
It has also raised the question over how we monitor our solutions (or not in this case!) I've now installed a porous pot to try to bring the mixed metals content under control. From analysis results and twaddle readings it appears we have a lot of stuff in them that is not chromic acid, which won't help.
Thanks again for your reply.
Chris
- Sheffield, England, UK
December 11, 2014
A. I have been told that using a mixed catalyst, sulphate/boric acid produces a harder deposit. Sorry, but I have no info on concentrations.
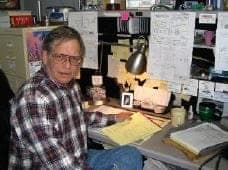
Jeffrey Holmes, CEF
Spartanburg, South Carolina
December 11, 2014
Q. SIR,
We are confused about the hardness of material after hard chrome coating. Please give me specified criteria of hardness after hard chrome coating (coating layer hardness after coating).
Thank you.
STEEL - Raigad.Maharashtra, India
December 10, 2014
A. Hi Vishal. It's the specifier's job to determine what he needs for the particular application, but if you follow the above discussion 850 to 950 Hv seem to be fairly typical hard chrome hardnesses. Good luck.
Regards,
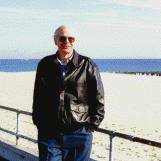
Ted Mooney, P.E.
Striving to live Aloha
finishing.com - Pine Beach, New Jersey
December 2014
January 5, 2015
Hi Chris,
as you have figured, adding more catalyst will actually have a negative impact on your hardness and you get a reverse action. However try to maintain a lower electrolyte temperature at 55-57 °C and see what you get. Additionally please share your analytic results including possible contaminants.
Thanks and good luck
- Rayong, Thailand
Q. Sir I have a hard chrome plant, and my problem is my hard chrome coating does not have hardness in it. Sir, can anyone please help me out what to do for hardness?
Aravind pbCOATING AND MANUFACTURING - New Delhi, Delhi, India
February 9, 2019
? Hi cousin Aravind. You'll probably need to supply some data for people to help you, but with many Q&A's about chrome hardness on this site, you added your question to this one about substrate hardness. I'm not sure if that was just random or you are implying that that you are applying the chrome to a soft substrate. Thanks.
Regards,
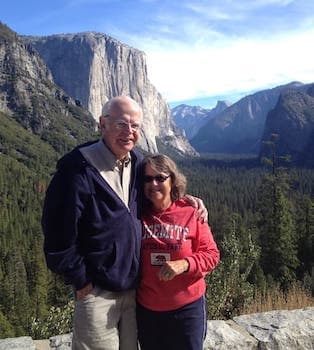
Ted Mooney, P.E. RET
Striving to live Aloha
finishing.com - Pine Beach, New Jersey
February 2019
Q. Sir, actually the thing is ... for testing I used 41b material then also the result is same: no hardness. Help me out for this sir.
Aravind pb [returning]- New Delhi,Delhi, India
February 20, 2019
by Robert K. Guffie
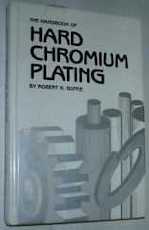
on AbeBooks
(rarely)
or eBay
(rarely)
or Amazon
(affil links)
A. Hi again Aravind.
I have 3 books just on chromium plating on the shelf next to my desk, plus another half dozen or more books with chapters on hard chrome plating. I'm just making the point that if you provide no data whatsoever -- not even the thickness or hardness, type of bath (Sergeant, mixed catalyst, HEEF), operating temperature, current density, concentration, or ratio -- it's hard to even know where to start. But Guffie's "Hard Chromium Plating" says in the troubleshooting chapter:
Ion exchange catalyst removal
High or low temperature
High or low concentration
High ratio
Insufficient deposit thickness
Regards,
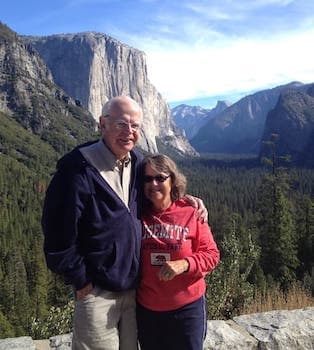
Ted Mooney, P.E. RET
Striving to live Aloha
finishing.com - Pine Beach, New Jersey
A. Hi,
Check the trivalent chrome it should be 1.5 to 3 gr/l
Regards,
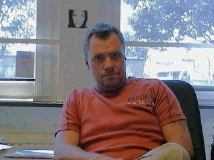
Anders Sundman
4th Generation Surface Engineering
Consultant - Arvika,
Sweden
May 16, 2019
A. Hi Aravind,
I'm really going to back up Ted's request for more information.
What investigations have you carried out so far? Have you analysed your tanks and made sure they are within operational limits? Have you "walked the line" and determined whether something has changed in the process?
From a personal experience, not long after I started in this industry, in the dim and distant past, the company I worked for had a similar problem with low hardness results. I walked the process, saw nothing obviously wrong with the plating process, so went and checked how they were testing the hardness. It turned out they were testing directly onto the chrome/base material, rather than sectioning the test piece and testing the chrome only. When they sectioned the test piece, polished it up and tested on the hard chrome, without the influence of the base material the results met the specification requirements! So, I can only encourage you to do something similar, look at everything, see if you can find the "smoking gun", which will give you a clue about how to solve the problem.
If after all of this you are still stuck, then come back to us with your findings and we'll see what else you could look at...
Aerospace - Yeovil, Somerset, UK
May 17, 2019
July 5, 2019
A. Hi Aravind,
I think you should give more information about plating parameters, thickness? expected hardness (? HV)
Normally, even conventional bath also can give at least 800 HV
More information, maybe someone can help you; with no information how to help you?
- Hanoi, Vietnam
Q, A, or Comment on THIS thread -or- Start a NEW Thread