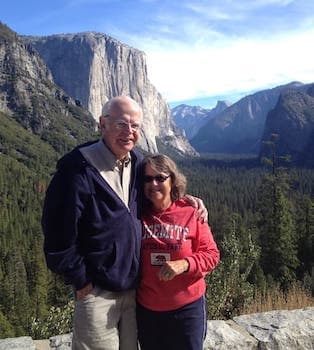
Curated with aloha by
Ted Mooney, P.E. RET
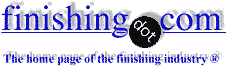
The authoritative public forum
for Metal Finishing 1989-2025
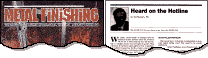
-----
Water immersion test for stainless steel passivation
Q. Hello all,
Is RO water acceptable for a passivate water immersion test? Since starting at my current job, we've always used RO water, but after looking into the specs more, I am now second guessing this. I am not sure how we decided that RO is acceptable, but can anyone please verify?
Thank you,
- Denver Colorado
September 19, 2023
A. Zander,
It really depends on which standard you are looking at, since the wording tends to vary, but I think typically the immersion test is said to use "distilled" water.
My guess is that you'll get very similar results with RO water as you do with distilled, but if you're under a high degree of scrutiny for compliance to the standard, it's usually better to follow the "letter of the law".
Again, depending on the standard, I know there's been some effort lately to genericize the purified water, i.e. ASTM D1193 "reagent water" has moved away from purification METHOD as a classification and more towards quantifiable water quality metrics. So in the future you may find less reliance on "distilled" per se and more a focus on water that is distilled-quality.
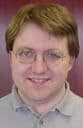
Ray Kremer
Stellar Solutions, Inc.

McHenry, Illinois
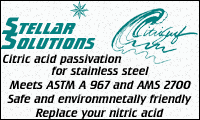
September 21, 2023
⇩ Related postings, oldest first ⇩
Q. DI vs Distilled Water for Passivation Immersion Test?
We do passivation to AMSQQP35
[canceled], with a 24-hour water immersion test per MIL-STD-753
[⇦ this spec on DLA / cancelled] [replaced by AMSSTD753], Method 100, as called out.
Mil-Std-753 says to use "distilled water". Given that Nadcap auditing sometimes comes down to a matter of semantics, is DI water an acceptable alternative? My researches on the web seem to indicate there's no practical difference. Any thoughts?
Plating job shop - Inglewood, California
2005
A. David:
I hate to present technicalities but in the case of Distilled or Deionized water, they are made by two completely different processes and are technically not the same. For practical purposes they are the same entity.
If the cleanliness of the water is specified correctly you should be able to use either. The best way to avoid problems with your auditor is to measure important attributes of the Distilled water and use DI water that meets those attributes. Keep the data to show your auditor that they are, in fact the same material. If your auditor objects, get him/her to call his/her engineering department to rule on your data.
Some things I have found important in water purity:
1) resistivity (the best, and most expensive, water is around 18 megohms),
2) clarity,
3) silicon/dissolved solids content
4) biological content.
There are others but that's all my simple brain can remember right now.
Ernie James- Vista, California
Re-using DI water for "water immersion test
We currently use the water immersion test after passivation. Our unit is not plumbed and therefore needs to periodically be drained and filled with fresh DI water. Knowing how important detailed procedures can be during NADCAP audits, I need to document an appropriate interval for changing the water. I am wondering what that interval would be. Prior to the water immersion test the parts and their baskets are rinsed with DI water - so we should not be introducing any foreign contaminates that way. We do not perform a lot of passivation and often test only one small group of parts at a time, so I would like to avoid the need to flush the tank after every test.
Thank you.
turbine/nozzle component mfgr - Des Moines, Iowa, USA
2006
A. Does your spec state what the quality of the DI water should be? If so, that would be the simplest way, just have a pre-determined conductivity/resistivity #, and once the water quality goes "out of spec", it's time to dump.
DI water will lose its quality very quickly, (especially just sitting in a tank, exposed to atmosphere) even if you are rinsing with DI just prior to putting your parts in the tank. If you really want to minimize the dumping of the tank, a simple, continuous filtering through a unibed should keep your quality in good shape, and minimize dumping.
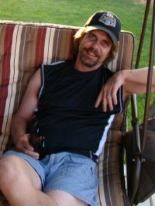
Marc Green
anodizer - Boise, Idaho
A. Hi Brigitte,
To establish an interval you could measure the conductivity of the water (ionic compounds dissolved in water). If your water has to be 18 megohm or less, a good in-tank conductivity probe w/ readout would be an option. Hand held meters are available and normally require frequent calibration. The tank would have to be stirred well before a sample is taken, or a reading taken from the in-tank unit. With the tank being unplumbed and aside from ionic contamination, you also run the risk of building up organics, unless you have alternate methods of agitation. Hope this helps.
process engineer - Malone, New York
Q. Need water immersion test equipment for passivation of stainless steel per AMS2700 or ASTM A967.
Thanks
plating shop - Schomberg, Ontario, CANADA
January 5, 2010
Ed. note: This RFQ is outdated, but technical replies are welcome, and readers are encouraged to post their own RFQs. But no public commercial suggestions please ( huh? why?).
Rusting during water immersion in passivation
Q. I HAVE BEEN HAVING TROUBLE WITH PARTS RUSTING DURING THE WATER IMMERSION PROCESS OF PASSIVATION. I CAN'T BLAME IT ON THE MATERIAL DUE TO IT IS A VARIETY, 416, 17-7, 15-5, ANY SUGGESTIONS ON WHERE TO GO FROM HERE I HAVE CHECKED AND RECHECKED AND CAN NOT COME UP WITH A SOLUTION.
PAM ALEXANDERSHOP EMPLOYEE - CLEVELAND, Ohio, USA
July 20, 2010
A. When you refer to rusting in the water immersion process, may I assume you mean the water immersion test after passivating?
Since your refer to different alloys, they must be tested separately. If they are combined, you can get selective galvanic corrosion.
Otherwise, any rusting/pitting is an indication that the surface is not passive, which can be due to several causes. Please let us know what type solutions you are using, as well as analytical controls that you have in place.
In general, corrosion of SS indicates iron particles remain on the surface. So what part of your processing either leaves them or restores them?
- Chicago, Illinois
Q, A, or Comment on THIS thread -or- Start a NEW Thread