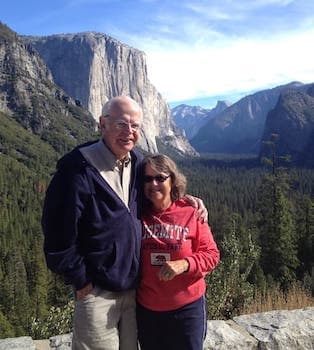
Curated with aloha by
Ted Mooney, P.E. RET
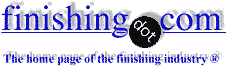
The authoritative public forum
for Metal Finishing 1989-2025
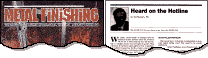
-----
Controlling hot dip galvanized steel production for dullness or shine
Q. Sir, after wire galvanizing we are making barbed wire. Afterwards material dullness -- please advise what to do?
Bikram kumar dasEmployee - Nagpur Maharashtra
December 16, 2021
? Hi Bikram. I have to ask the same question as all the way back to the beginning ... what are you doing regarding a chromate dip or quench? ... it is an answer to short-term brightness. David notes additional brightening approaches but he notes, as does Geoff, that all galvanizing quickly dulls.
Luck & Regards,
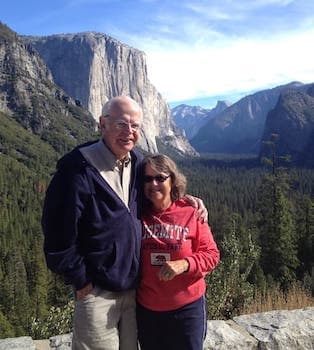
Ted Mooney, P.E. RET
Striving to live Aloha
finishing.com - Pine Beach, New Jersey
December 2021
⇩ Related postings, oldest first ⇩
Q. We are manufacturing Galvanized Iron Flexible Conduits. After a month or so of storage, the conduits catch dust, grease etc to form dull gray thin film. Or develop white rust or at least lose its bright shine. Given the formation of the conduit, its not possible to restore the finish using buffing or sanding or using wire brush. Is there any solution or chemical to remove the contaminants /thin film/ white rust and restore the finish.
Gaurav GargManufacturer - Delhi, India
2004
A. What do you do for chromate dip?
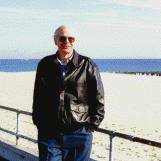
Ted Mooney, P.E.
Striving to live Aloha
finishing.com - Pine Beach, New Jersey
2004
Q. Dear Ted,
The product in subject is flexible armored conduits like electric conduits, shower hoses, etc. The conduits are manufactured out of Galvanized Iron Strips which are slitted from full-width coils to required size . As you may judge, the slitted edge is not galvanized but it has rarely been any problem.
Gaurav Garg [returning]Manufacturing - Delhi, India
2004
A. The dullness, being zinc oxide is what provides the lasting protection. Bright zinc will oxidize quickly. If it stays bright, maybe it didn't need protection? If it dulls quickly it needs the galvanizing, and it is doing its job.
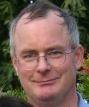
Geoff Crowley
Crithwood Ltd.
Westfield, Scotland, UK
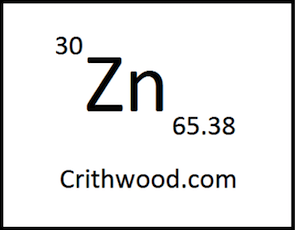
2004
Multiple threads merged: please forgive chronology errors and repetition 🙂
Q. We hot dip galvanize different steel products but they lose their shininess in one or two weeks. How can we retain its shininess in the long run? Can we put some chemicals in? Thank you.
Boran KAYA- Ankara, Turkey
2005
by Kuklik & Kudlacek
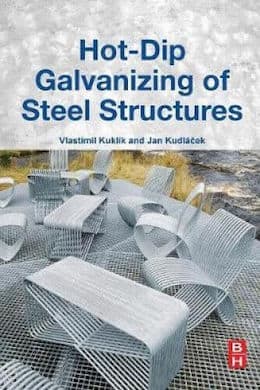
on AbeBooks
or eBay or
Amazon
(affil links)
by NACE
[only rarely available]
on AbeBooks
or eBay or
Amazon
(affil links)
A. The shiny coating appearance you are getting right out of the zinc bath is going to be temporary. Hot dip galvanizing is for corrosion protection. It is a sacrificial coating that oxidizes and slowly dissolves over time. The initial oxidation usually occurs soon after the product is exposed to moisture. The dull gray is a normal appearance, and won't be stopped.
I have seen a galvanizer spray a clear coat over some indoor furniture (used in his own home)that held a shine for several years, but I don't know of any practical coatings to keep it shiny. If you read about the alloy layers that develop during the galvanizing process, you will see that the outermost layer is almost pure zinc. This layer actually becomes more durable over the 1st year as it is "weathered"
There are additives for the zinc bath such as brightener bars, nickel, bismuth, tin, and aluminum that will create larger, more distinct spangles as well as brighter coatings, but they all become dull over time.
Houston, Texas
2005
A. It's difficult to maintain shiny surface on galvanizing coating it's a metallurgical reaction b/w steel and hot molten zinc (sacrificial coating). Shiny surface can be maintain with adding by nickel but for temporary (3 month) basis . It will lose it bright when it come in contact with air (oxygen) it becomes weathered galvanized but it gives long lasting protection against corrosion.
And normally you cannot get cosmetic finish on galvanized surface because brightness will also depend on composition of silicon content and phosphorus content in steel.
industrial coating - Dubai, UAE
2005
A. What about clear chromate? Won't that help extend the shiny appearance?
Ron Kmiecik- Chicago, Illinois, USA
2005
Q. 1. We get hot rolled steel sections such as Channels, etc., fabricated and hot dip galvanized from South East Asia. The galvanized finish is dull compared to what we get in Australia. Could there be a quality problem? How do we check the quality of galvanizing in such parts? What is the best method to establish that the suppliers follow the specified galvanizing standards?
2. We also get 6mm thick HU-300 steel parts fabricated, hot dip galvanized and then powder coated. At times we have a problem of adhesion of powder to the gal surface. We do understand that the pre-treatment process is key to good adhesion. Is Zinc phosphate pre-treatment better than iron phosphate pre-treatment? Is it better to have a mild whip-blast done after gal and before powder coating?
Importer - NSW, Australia
2006
2006
A. Sir:
Regarding your first question. It is likely that the South East Asia steel is high in silicon and phosphorus and is very reactive toward zinc. Thus the alloy coating migrates to the surface as the steel cools giving a dark grey coating with no "free" zinc on the outside. You may also find thick zinc brittle coatings that may be subject to impact. One reason could be bad flux solution thus requiring longer kettle times and giving thicker zinc. Another possibility could be that the galvanizer is not using aluminum to brighten the product. These grey coatings could be perfectly good and the thicker they are the longer the steel protection (as long as they do not flake off). In my view hot dip galvanizing is an excellent steel protecting coating but may not at times be all that decorative. With proper methods hot dip galvanizing can produce very decorative coatings.
I do not know the answer to your second question.
Regards,
Galvanizing Consultant - Hot Springs, South Dakota, USA
Q. One of our clients want dull and blackish uniform surface appearance after hot dip galvanizing process. Steel which is being galvanized has a chemistry as C%- less than 0.25%, Si - .15 to .25%, P- 0.02 to 0.045% and Mn- 0.6 to 1.3%. With this chemistry how to achieve dull blackish color in hot dip galvanizing process. Galvanizing coating thickness shall be in the range of 100 to 125 microns. Request to share your knowledge and experience for mass production.
Jayant [last name deleted for privacy by Editor]transmission towers hot dip galvanized steel items - Maharashtra, India
2007
A. Galvanizing is a series of layers of Zinc metallurgically bonded to the steel. But the outermost layer is most commonly pure zinc, which is colored (initially) silvery grey. That's the color of zinc. As it oxidizes though, it will turn dull grey. (Under some conditions of steel reactivity it will be dull grey right from galvanizing, as its alloy of Fe and Zn on the surface).
Your client is asking for a natural element to be an unnatural color. That's not an unusual request, but most commonly satisfied by another coating put there for this purpose.
Your options are: paint (solvent based), powder coating, or similar overcoating of the zinc.
You could react something with the zinc, such as zinc phosphate, which will leave a dull nearly black color, but this is not a permanent finish and with time will erode to leave dull grey again.
It would be interesting to know why they want this color finish. That might lead you to suggest a better solution.
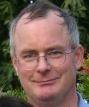
Geoff Crowley
Crithwood Ltd.
Westfield, Scotland, UK
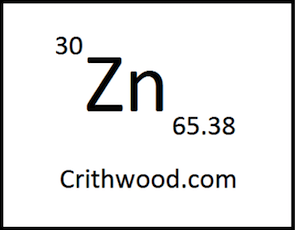
2007
Q. Hi I am quality manager of a engineering company and the problem is that after welding 3 components together we have them galvanized but the middle component is shiny silver the 2 other outside components is a dull finish is this because of the high silicon content or the manganese silicon ratio?
Many thanks Jim
Jim Matthewsquality - Welwyn Garden City, England
2007
2007
A. The cause of varying brightness on new galvanizing is that what you are seeing is different. In the case of dull color, its an alloy of zinc and iron (perhaps about 3-5% Fe rest Zn) and this alloy is dull. In the case of bright shiny silver its 100% Zn you see.
On dipping a steel piece (or fabrication in this case), the Fe in the steel reacts with the Zn to form alloys. The speed of this reaction depends on the Si content (and to a lesser degree the P, but not normally the Mn)
See http://www.hdg.org.uk/203_The_Coating.php and scroll down for a graph.
With the critical Si level, the speed of reaction is fast, as long as the coating is molten, so all the thickness of the coating becomes alloyed.
In slower reactivity steels, the outer layer of the coating is pure Zn, not getting time to turn to dull alloy before the item cooled below melting point.
There is no difference in the corrosion performance between dull and bright.
With time all will turn dull anyway, as Zn reacts with oxygen and carbonates in air/water to form a layer of "patina" on surface, comprising oxides and carbonates of zinc. Its this layer that really does the protection, as zinc is really quite reactive, but this layer isn't.
The difference is largely aesthetic.
If you need to avoid this issue, then you need steels of similar composition. Not just same grade, as the spread of allowable composition within a grade can be wider that this issue demands.
You didn't say if you see this as a problem, or if its just a case of understanding why its occurred. Above is why. If this is a problem, only you can tell, and the only real issue is a visual question.
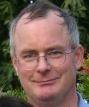
Geoff Crowley
Crithwood Ltd.
Westfield, Scotland, UK
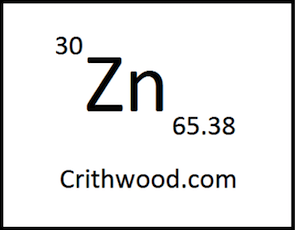
October 20, 2010
Q. I am producing heliostats for a solar field. The public is concerned about the shininess of the finish of our pedestals, which are the base for our heliostats.
Our manufacturing partners are hot-dip galvanizing all the metal parts, but I want to be sure I get a very flat gray finish, rather than a shiny one. I have received three pedestals and they are VERY shiny.
Is there a spec that would ensure the finish I am looking for?
Thanks.
A. To get dull grey galvanizing there are several options.
1. Use steel of suitable chemistry. (not so easy)
2. Increase galvanizing temperature (galvanizer won't want to do this)
3. Retain the steel at high temperature after galvanizing. So long as the steel is at or above about 450 °C then the alloys that form (which are grey) will continue growing throughout the thickness of the coating and this forms a dull coating.
4. Heat the galvanized steel afterward to about 440 °C and hold it there but without excessive oxygen available to oxidize the coating.
5. Wait 6 months and it'll go grey anyway (easiest)
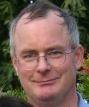
Geoff Crowley
Crithwood Ltd.
Westfield, Scotland, UK
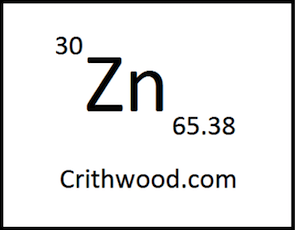
October 21, 2010
A. Dear Gary,
I've read about a Japanese company using Zinc Phosphate or permanganate to reduce the glossiness of the galvanized area. Phosphate will give a rough, uniform grey finishing while permanganate gives a smoother, darker finishing.
Perhaps you can ask your partner to do some R&D on it.
- Selangor, Malaysia
November 28, 2010
Q. Hi,
We need help to solve a problem. We galvanized same parts but their appearances aren't the same. Some are shiny but some are dull. These are parts with 250 cm length, 25 cm diameter and 1 cm thickness. They are all made of same steel. Any help will be appreciated. Thanks in advance.
- Istanbul, Turkey
February 6, 2013
A. This is because of the time taken after withdrawal from the bath and quenching where you dip it into the water. Whenever time taken will be more it will give you a dull finish.
Nitesh Agarwal- Mumbai, India
February 23, 2013
Q. Dear Sir,
How to avoid the shine of galvanising getting dull? I have a HDG plant in Kanpur India. The problem that I am facing is that the shine on the galvanised product which is kept nearer to pickling tank (approx. 5 meters away) gets dull very soon. Secondly, after rubbing the product with luke warm water, 50% of the shine is regained. Kindly help me out.
Thanks & Regards
- Kanpur, Uttarpradesh India
March 6, 2013
Bright, non-weathered metallic zinc surface is required
Q. How can I get the hot dip galvanized surface which is weathered and dark looking like a new (bright,unweathered metallic zinc surface is required)?
Regards,
Mekhty
- Azerbaijan
February 12, 2014
February 13, 2014
A. Galvanizing is not primarily an aesthetic coating, it's a corrosion protection coating that has a rather industrial appearance.
It protects in several ways. Firstly it's a coating, hiding the steel from the air.
But it is more reactive that steel, so if exposed to air it reacts with oxygen in air forming zinc oxides. That's physics, and can't be altered.
Now once the zinc oxidizes a little, its surface going dull, that oxide is what the air "sees", and that doesn't react so fast. This is why galvanizing lasts long as it does. And if any oxides get dislodged, more form pretty quickly.
But in a similar way to how the zinc protects the steel, it's possible to protect the zinc, by another coating.
If you want to see the zinc, you'll need a clear coating. This might be varnish-like, or clear powder coating.
Problem is, that to get the coating to adhere to the zinc, you need some pretreatment, and that pretreatment makes the zinc look discoloured again.
So, I don't think there's any easy answer.
If your fresh galvanized is kept close to a pickle tank in a galvanizing plant it will be corroded ultra quickly by HCl in the air. Move it away.
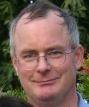
Geoff Crowley
Crithwood Ltd.
Westfield, Scotland, UK
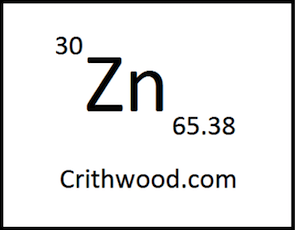
We are not chromating after galvanizing
Q. Dear Sir,
We are not doing any post galvanizing treatment like dichromating. Is it really necessary, or we can continue doing like that?
Can we add the dichromate directly into the cooling water?
Kindly Help.
Thanks & Regards
Aman
- Punjab, India
September 14, 2014
A. It's better to be have separate tank for Chromating.
Chromating is dependent on your client whether they are required or not.
Gunatit Builders

Manjalpur, Vadodara, Gujarat
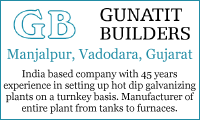
November 16, 2014
A. Passivation (chromate) after galvanizing gives shinier brighter galvanizing and gives some protection from white rust.
If you want your galvanizing to look better than others, then do it.
If your customers want it, then do it.
You do not need separate tanks. If you have a cooling tanks now, the two processes can be combined, provided the tank is capable. Advantage? One step process of cooling and passivation, and run at far lower concentration.
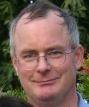
Geoff Crowley
Crithwood Ltd.
Westfield, Scotland, UK
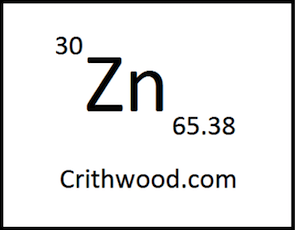
December 2, 2014
Q. Dear sir,
I am a mechanical engineer and also I am newer in the galvanizing field. Sir my question is "How to control on the dull appearance of galvanizing coating". It is most important for me because our cliant wants shiny appearance of zinc coating
- Nagpur, Mahareshtra, India
April 16, 2015
A. Hi Laxmikant. As has been noted previously on this page, galvanizing is a functional coating judged by its corrosion resistance, not a decorative coating to be judged by its shininess. But chromate can deter the dulling for a while, and careful engineering of the coating can result in greater initial brightness. Dr. Cook's "Niftygalv" is very bright, but some of the knowledge of how to achieve this is proprietary rather than generic.
If your client truly wants "shiny appearance" they might consider nickel-chrome plating which, if done really right, to automotive specs, can stay bright for decades.
Regards,
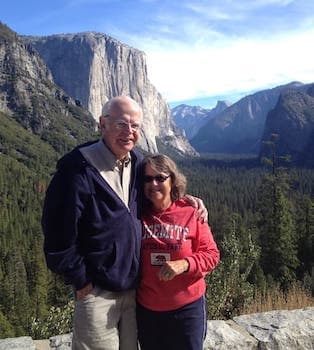
Ted Mooney, P.E. RET
Striving to live Aloha
finishing.com - Pine Beach, New Jersey
Q. SIR
AFTER DICHROMATING GALVANIZE MATERIAL BECOMES DULL. IS THERE ANY COLOURLESS DICHROMATE AVAILABLE IN MARKET WHICH CAN SOLVE THE PROBLEM OF WHITE RUST AND ALSO NOT AFFECT THE QUALITY OF PRODUCT?
HEAVY ENGINEERING - Pune, Maharashtra, India
July 17, 2015
A. If your chromating tank left you with a duller finish than you started with, I will guess that one or more of the following are off: chromate concentration, time, temperature or ph.
James Watts- Navarre, Florida
July 17, 2015
A. Sir:
The best clear dichromate that I know is:
500 ppm to 1000 ppm (0.05% to 0.1%) in both sodium dichromate and acetic acid
⇦ this on
eBay
or
Amazon [affil links] , and kept at pH 4.2 with HCl.
Chromic acid (chromium trioxide; flakes) badly stain the zinc coating in colors ranging from olive drab green to orange.
Regards,
Galvanizing Consultant - Hot Springs, South Dakota, USA
July 18, 2015
Q. Hello. Sir I have a galvanising plant and we galvanise pipes. Our pipes become dull and loose their shine. Here in Pakistan people want shiny pipes as it is considered that shiny pipes are only best galvanised tell me such type of tips that our pipes don't became dull till a month I will be thankful to you.
Sheikh tayyabPipe galvanising - Lahore Pakistan
December 16, 2015
A. You need to add aluminum to it.
Nitesh Kumar Agarwalindana steel - Kolkata, India
May 20, 2016
Q. Our Zinc Bath size 1.8 m x 2.6 m x 12.5 m. When we dip poles up to 800 mm diameter, then shine all over the pole is the same; but when do the 1500 mm or more diameter by colour effect is coming. Bottom only is not shining. Please advice how to overcome this problem. Raw material composition is also ok.
GALVANISING COMPANY - kolkata . India
April 16, 2018
A. It's not clear what the problem is. Are you concerned about different appearance of the galvanizing - between silvery and dull grey? There is no difference in the corrosion performance between the two colours, its only an aesthetic difference. Both colours meet ISO1461.
If aesthetics is what the customer wants then do something different, perhaps powdercoat or paint over galvanizing.
The difference is caused by zinc composition, steel chemistry, immersion time and some other factors including flux composition..
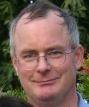
Geoff Crowley
Crithwood Ltd.
Westfield, Scotland, UK
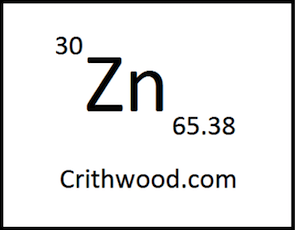
May 4, 2018
Q. Dear sir,
I am a manufacturer based in India of steel fabrication and also I am newer in the galvanizing field. Sir my question is "How to control on the dull appearance of galvanizing coating". It is most important for me because our client wants shiny appearance of zinc coating plus microns to be around 100.
We don't have our own hot galvanising plant but getting it done from outside, and I have tried 10-12 factories and found no solution yet
Ashoka International - Ludhiana, Punjab, India
February 15, 2019
Ed. note: This RFQ is outdated, but technical replies are welcome, and readers are encouraged to post their own RFQs. But no public commercial suggestions please ( huh? why?).
A. Hi cousin Nikhil. I think your customer is new to the galvanizing field also :-)
You've tried 10-12 different factories, and you've seen here 10-12 responses from experts, over a period of more than 10-12 years. As you see, there are things you can do to somewhat control brightness for a very limited period of time, but galvanizing isn't a decorative finish like chrome plating. Best of luck.
Regards,
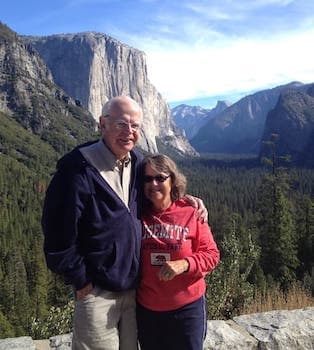
Ted Mooney, P.E. RET
Striving to live Aloha
finishing.com - Pine Beach, New Jersey
February 2019

Q, A, or Comment on THIS thread -or- Start a NEW Thread