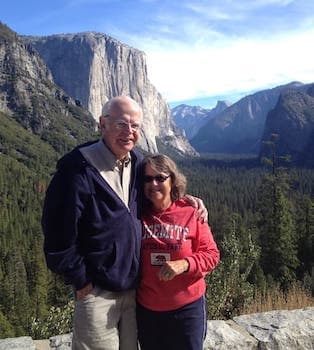
Curated with aloha by
Ted Mooney, P.E. RET
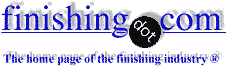
The authoritative public forum
for Metal Finishing 1989-2025
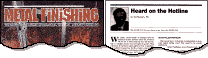
-----
Problems in nickel-chrome plating on brass
Q. Salt spray failure on brass.
Nickel and chrome plating on brass we observe green corrosion in acetic acid salt spray ... but in same batch, same rack of 2 pieces, 1 is ok and 2nd is not ok. Any advise for this problem?
- Gujarat, India
September 29, 2024
A. Hi Yash,
Although it would be nice if there were a conclusive answer to such a situation and with no other data available, that is unfortunately not the case..
It is possible, of course, that the salt spray cabinet is giving inconsistent results due to misadjustment, with one piece being exposed to a far more corrosive situation than the other piece. Although possible, it's rather unlikely. so you might send a few sets to another test lab, or, if the salt spray cabinet is in-house, start logging the location within the cabinet of parts which passed vs. parts which failed.
Another possibility would be a similar inconsistency within the plating operation, such that specific locations within the plating tank suffer some sort of electrical shading preventing sufficient nickel and or chrome plating on parts in those positions. Again, possible, but probably unlikely.
What would seem more likely would be inadequate plating on some parts due to poor rack contact. This should be guarded against by statistically valid thickness testing and by insisting that the plating racks be kept in good clean shape.
Another possibility is that the cleaning and activation prior to plating is simply not robust, such that if one part happens to arrived at the plating line rather clean and another one dirtier or more oily, the cleaning and activation steps are only adequate to prepare the cleaner one.
The short answer is that, to my knowledge, there is unfortunately no 'smoking gun' which can be identified from this single test of one part passing and another part failing. Rather, I suggest slowly 'walking the line' to see if the parts appear in uniform condition before the process starts, whether racks or DC bussing is well maintained such that current breaks do not occur, that there is nothing obvious which sometimes happens and sometimes does not, etc. In addition, other tests including thickness testing will probably prove necessary to narrow in on the problem.
Larry Durney's "Trouble in Your Tank" ⇦ this on
Amazon
[affil link] offers priceless information about troubleshooting a plating operation, such as "Obey the Letter of the Law": only when all parameters on the plating line are exactly and reliably within specification can you make real troubleshooting progress. If 3 or 4 things are varying, with people saying "oh, that one doesn't really matter", you may never solve it :-)
Luck & Regards,
Ted Mooney, P.E. RET
Striving to live Aloha
finishing.com - Pine Beach, New Jersey
⇩ Related postings, oldest first ⇩
Q. We do bright chrome plating over bright nickel plating on parts of max 4 dm2 surface area. Small milky points appear on our plated surfaces at the areas which the last water drops leaves the part when the bar is waiting over the tanks. This deposits can be removed by further polishing after plating process. Thinking that the potential reason is the activation process, we have made experiments on activation but no positive results are achieved.
Thanks for your interest,
Ozkan Bekiroglu- Bozuyuk, Bilecik, TURKEY
2002
? Are you using Demineralized water in rinse?
Payal Mag - Charlotte, North Carolina We use demineralized water for rinsing between nickel and chromium baths.
- Bozuyuk, Bilecik, TURKEY
A. Hi Ozkan.,
Your milky spot can be from a high level of wetting agent from the nickel solution.
Regards,
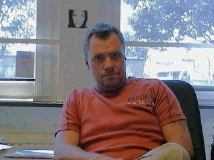
Anders Sundman
4th Generation Surface Engineering
Consultant - Arvika,
Sweden
Hi Anders;
The wetting agent concentration of the nickel solution is between the limits according to our analysis. We have achieved a different result during our experiments. We have shaken the parts 2 times in the demineralized water rinse tank just before the chrome activation process and the ratio of the faults decreased but did not totally disappear.
Regards,
Ozkan Bekiroglu [returning]- Bozuyuk, Bilecik, TURKEY
A. Ozkan,
I still believe this problem you have is what we call "withe hourse". Are you sure that deionized water is clean and free from contamination from your nickel solution additive. Did you have the possibility to make a rinse dip in water solution with a little contents of sulfuric acid 1.5 percent before chromium plating. Also did you have this problem for other materials?
Regards,
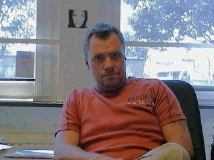
Anders Sundman
4th Generation Surface Engineering
Consultant - Arvika,
Sweden
A. Try dipping the work in the chrome dragout tank immediately before entering the chrome tank
Tim Strickland - Auckland, New ZealandWe will try your both suggestions and write about the results as soon as possible.
Regards,
Ozkan Bekiroglu [returning]- Bozuyuk, Bilecik, TURKEY
Q. Rinsing the tank into a %1.5 sulfuric acid rinse tank before chrome activation process did not solve the problem.
Dipping the parts into the chrome dragout tank before chrome plating didn't solve the problem.
I could not clearly understand the question about the material, but if the subject is the base metal, we see the fault only on the plated brass parts.
The concentration of our chrome dragout tank is high. Maybe the problems occur because of that reason?
Ozkan Bekiroglu [returning]- Bozuyuk, Bilecik, TURKEY
A. If you turn some of the components upside down after they come out of the nickel and some different ones upside down after the nickel rinses just prior to chroming what happens to the white spots. Are they still all on the bottom of the work or are some on the top of the pieces you turned.
Tim Strickland - Auckland, New ZealandQ. The hanging style does not change the place of the defects. They still occur at the bottom points of the parts where the last drops leave the part.
Regards,
Ozkan Bekiroglu [returning]- Bozuyuk, Bilecik, TURKEY
A. Try spraying the plated articles with DM water after Nickel plate and may be avoid nickel dragout.
Jeevan [last name deleted for privacy by Editor]- Ujjain, MP, India
A. 1. Add 3:1 ratio of wetter/additive to the brightener ratio to the nickel plating bath.
2. Try to transfer the Nickel to its dragout and rinse tanks before the water dries as a spot. Maintain the bath temperature at 50 °C instead of 60 °C which makes parts dry .
3. I do hope the parts stay under clean water after Nickel till they are chromed ?
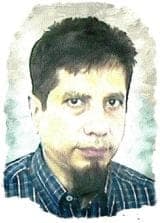
Khozem Vahaanwala
Saify Ind

Bengaluru, Karnataka, India
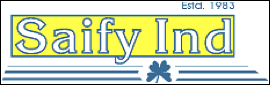
A. Dear Ozkan,
We faced the same problem in our Ni-Cr automatic plating line, in which the air exposure time is 30 seconds when arm shift to next position. We were also using the de-mineralized water in rinses between the Nickel & Chrome. We also know that demineralized water is strongly recommended in all plating lines. I suggest trying normal water of TDS-350 to 400 and pH 7.0 to 7.5. This is some reaction which occurs due to air exposure time.
Q. We are looking for alternatives to Nickel/Chrome over brass that is aesthetic as well as durable. We are open to all suggestions. One of the components is a brass ferrule that will be crimped and the finish must adhere after this process. This component is .850 ID with a wall thickness of .025 and the length is .625 with a hole pierce of .550. We would like the finish to be a yellow color. The other component is approximately 2.250 L x 13/16 W. This has internal threads at 1 end and a 1-piece stem on the other to be crimped on hose. Again this must withstand crimping. We are currently using a commercial Zinc plate for this. The finish needs to resemble the clear Zinc yet provide better resistance to the elements. As is always the case we are looking to beef up both without the added cost. Total yearly volume could exceed 500,000 pieces.
Mack McPeetersfire protection industry - Greensboro, North Carolina, USA
2004
A. Electroless Nickel.
Todd Osmolski- Charlotte, North Carolina, USA
A. How about electro-catalytic nickel. It has almost no stress, good corrosion resistance, great appearance, and less cost than electroless.
Dan Weaver- Toccoa, Georgia
A. Hi Mack.
I think there is a wrong assumption in your plan in that nickel-chrome plating or electroless nickel plating are not necessarily more corrosion resistant --and in fact may be pless corrosion resistant, especially when crimping after plating will be done. The reason is that nickel and chrome are 'barrier layer' platings whereas zinc plating offers cathodic protection. If brass is exposed due to porosity, flaking, or pinholes in the plating, caused by crimping or anything else, the zinc will preferentially corrode to protect the brass. Nickel does the reverse, i.e., it accelerates corrosion of the brass in order to protect itself.
Further, nickel-chrome and electroless nickel are significantly more expensive than zinc plating. The path forward is probably simply to increase the thickness of the zinc plating, or if that is not possible for some reason, to switch to alloy zinc plating (zinc-nickel or zinc-iron) which offer greater corrosion resistance than zinc plating while still offering cathodic protection, and which are significantly less expensive than nickel-chrome or electroless nickel.
Luck & Regards,
Ted Mooney, P.E. RET
Striving to live Aloha
finishing.com - Pine Beach, New Jersey
Multiple threads merged: please forgive chronology errors and repetition 🙂
Q. Hello.
I am a engineer in plating part at plumbing fixture factory.
I got trouble with Ni-Cr plating on faucets (brass substrate).
When buffed condition, there was no prominent defects are found on the surface.
After plating, hazed surface appeared and it was parallel with buff direction.
There are so many opinions in our factory.
...Because of not removed buff compound...
...Because of excessive heat when buffed...
...Bright nickel layer are not sufficiently deposited...
and so on.
Please give me help! Sorry about my poor English.
Jeahyon Joetrading co. - Incheon City, Incheon, South Korea
2005
A. Sounds to me like you may have some residual buffing compound that is not being removed sufficiently prior to nickel plating. You don't describe your cleaning process but you might try solvent cleaning the parts prior to your regular alkaline cleaning process.
Also, you could have organic contamination in your nickel. Do you see any evidence of the hazing in your Hull cell panels? If so, you can narrow it down to nickel pretty quickly. If not, you could have a cleaning and pretreatment problem.
Have you gone a long time since you have dumped cleaners? Are your rinses contaminated? Do you have good quality water?
You have a lot of unknowns present that make it difficult to diagnose your problem. You should go to your chemical suppliers too and have them help you!
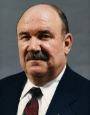
Daryl Spindler, CEF
decorative nickel-chrome plating - Greenbrier, Tennessee
2005
A. Dear Mr. Joe,
I think some of your colleagues are right, most of the probability is the buffing compound film that could not be removed during pretreatment and then become haze underneath of your nickel chrome layer. Please check your pretreatment sequences and pretreatment Chemistry whether getting old or not enough.
Are you running a new plating line?
Good luck
Best regards,
Tony L. Chandra- Jakarta, DKI Jaya, Indonesia
Q. Thank you for the kind answers.
I think there is no problem in our precleaning process.
We did a simple test.
With new paper buff we tried buffing without buff compound.
And we got same hazed surface in our product.
So we made decision that there was lack of buff compound during buffing.
But still there is a problem.
How can I explain this?
Sharp buff edge can make invisible scratch to brass?
And it can appear after plating?
Dear Tony,
It's not a new plating line.
Thank you.
Best regards.
Jaehyun Joe [returning]trading co. - Incheon City, South Korea
A. HAZED SURFACE AFTER NICKEL PLATING.
INADEQUATE CLEANING INCLUDING ACID DIP.
IN NICKEL TANK,ORGANIC CONTAMINATION, PH OUT OF RANGE, CLEANER PERFORMANCE CAN BE CHECKED BY WATER BREAK TEST.
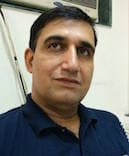
Ajay Raina
Ludhiana, Punjab, India
A. Hi,
Believe cleaning problem be sorted out, if you see the buffing lines even after plating it means the leveling in nickel is poor and if you are looking for the best leveling go for acid copper with the best leveling organics in acid copper and nickel.
Thanks,
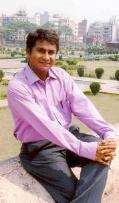
Praveen Kumar
plating process supplier
Mumbai, India
Problems & confusion over nickel-chrome plating of brass golf clubs
Q. After Ni-Cr coating our brass putters, pits and white spots appear on over 50% of the parts (25+ out of 50):
The Ni-Cr coating people said the brass has a problem:
Other Ni-Cr coating people say the Ni-Cr coating was not done properly -- either poor cleaning or a power problem. We are just the customer, so we don't know the plating process. As a result, we have begun to ask questions and the issue has become more confusing.
First, we're told we must do Ni-Cr coating before tin and 24k IP. This is in order to achieve good adhesion, hardness and brightness.
Next, some say we can get away with nickel coating only (no chrome) followed by tin [ed note: we believe that Lane means TiN, titanium nitride, not tin plating] and 24k IP [ed note: Ion Plating?] and achieve the same final result as doing both Ni-Cr coating before IP:
Our first question is whether or not this is the case and if so, then why do the Cr coating unless it has some benefit. Or is it the chrome coating process that is to blame for the pitting; hence, best to avoid chrome coating and accept the lesser adhesion, hardness and brightness? Does chrome definitely improve the adhesion, hardness and brightness but the risk is pitting?
We cannot understand why 50% of the brass putters developed severe pitting after Ni-Cr coating. Could it be the raw material even though none of pits appeared before the coating process begun? Or, is it, as some say, the parts were either not cleaned properly or the power used was not controlled properly; hence, damaging the surface of the brass resulting in the pitting. How do we know or confirm what is the cause for the pitting?
Thank you all for your consideration in giving us your best advise.
Regards,
lp
- Laguna Niguel, California, USA
July 7, 2012
Patches on nickel-chrome plated brass parts
Q. I am facing an unusual problem of patch on Ni-Cr plating (of brass substrate). The cleaners seem to do well when it comes to water break test, the cleaner sequence is normal soak cleaning, ultrasonic, hydrosonic, periodic reverse cleaning (which is at present being operated only in anodic for about 20 seconds). Each cleaner has a rinse in between.
Finally we have acid activation, followed by Ni and Cr.
The parts, which are wiped properly, do not show any problem as compared to the parts which are not cleaned (not cleaned parts show complete rejection). During the summers same parameters were maintained without changing anything, rejection was about 2%. Now, during the monsoons, maintaining the same parameters the rejection is 100%.
Cleaners are dumped on a frequency of 15 days and filters are changed every day. Difficult to find the root cause.
plating line - gurgaon, haryana, India
September 5, 2014
? Hi Rahul. A problem I am having is I don't know what exactly you mean by "problem of patch". Is the area lacking nickel plating? Is it lacking only chrome plating? Is it just a discoloration? Can you please describe these patches or, better yet, send photos to mooney@finishing.com?
Also, I am not quite understanding what you mean by "wiped properly". Do you wipe the the parts with solvent before the cleaning process, or wipe them with a clean towel between cleaning and acid dip? Please help us more clearly understand your situation. Thanks.
Regards,
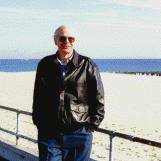
Ted Mooney, P.E.
Striving to live Aloha
finishing.com - Pine Beach, New Jersey
Q. We are doing bright nickel plating followed by decorative chrome plating, we are getting this Haze as seen in the pics, how to remove this.
We think this is from chrome.
Sulphate in tank was less but even after maintaining proper ratio problem is still there.
- Ludhiana Punjab, India
January 21, 2021
Ed. note: This appears to be a long-running problem which about which Yogesh posted 1-1/2 years ago.
A. Hi,
ALL different parts are come out hazy or only one kind of part hazy?
Try the piece out after nickel plate -- if it is hazy that means no problem in your chrome tank,; not hazy after nickel but chrome plated part is hazy check your chrome for sulphate, catalyst and ratio.
If part comes out hazy after nickel plate, run the hull cell panel, adjust the brightener, pH and concentration of nickel bath.
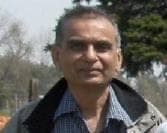
Popatbhai B. Patel
electroplating consultant - Roseville, Michigan
Q. Hi,
My company is manufacturing large volumes of brass products that are decorative nickel-chrome plated. We constantly face major issue with pitting on brass sheet parts.
If anybody has suggestions then please let me know.
Plating for nickel is approximately 20 minutes, temperature is maintained at 58 °C-60 °C and current is 5 A/dm2
Plating for nickelchrome is approximately 2 minutes, temperature is maintained at 43 °C-44 °C and current is 10-11 A/dm2
Any help would be great! If anybody has suggestions on polishing process for brass sheet that would also be of great help!
- Gujarat, India
June 8, 2022
A. Hi Samyak. There are different types of pitting and different causes. The most common is probably "gas pits / hydrogen pits". Are your pits hemispherical and shiny? If so, what is the surface tension in your nickel plating bath? Do you have vigorous air agitation in your nickel plating bath?
I have heard some platers claim that overheating of scotchbrite pads during polishing can leave residue that can seed those gas pits but I don't have enough experience with that to know whether to accept or dismiss such claims.
Luck & Regards,
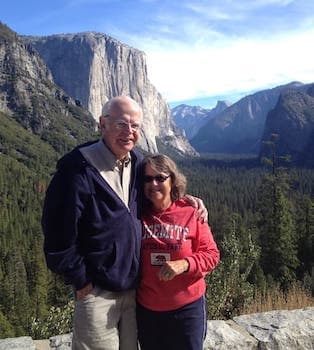
Ted Mooney, P.E. RET
Striving to live Aloha
finishing.com - Pine Beach, New Jersey
A. Hello, Samyak
I agree with Ted about the surface tension.
You should first check if the pitting really appears after the nickel layer.
If so, the cause might be a high surface tension that prevents the gas bubbles from detaching from your parts, causing the pitting. If that's the case, a small dose of your anti-pitting/wetter agent should fix it.
Regards,
Chemical Engineer - Nova Friburgo, Rio de Janeiro, Brazil
Q, A, or Comment on THIS thread -or- Start a NEW Thread