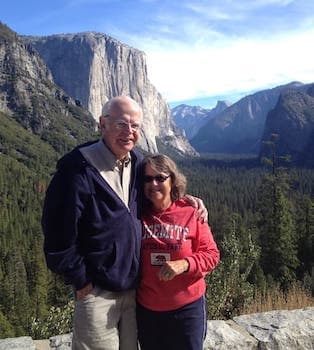
Curated with aloha by
Ted Mooney, P.E. RET
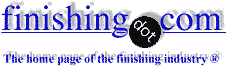
The authoritative public forum
for Metal Finishing 1989-2025
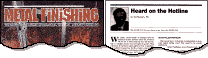
-----
Plasma powder spray coating or plasma sputtering? Tungsten Carbide
2000
RFQ: We are looking for the following items for our clients. Would you please quote us the FOB price at the earliest possible by fax or e-mail & send us the detailed information by mail
- 1. Monel Powder Monel 402 50 kg
- Composition: Carbon 0.12 %, Copper = 40 %, Magnes= 0.12 %, Rest = Nickel
- Particle size = 75 + 44 micron
- 2.Tungsten Carbide alloy 50 kg
- Composition: WC + 12 %, Cobalt aggregate = 50 %, Ni = 33 %, Cr = 9 %, Fe = 3.5 %, Si = 2.0 %, C = 0.5 %, B = 2 %
- Particle size = -56 + 15 micron
- 3.Stainless Steel Powder Type 316 50 kg
- Composition Cr. = 17 %, Ni = 12 %, Mo = 2.5 %, Si = 1.6 %, Carbon = 0.1 %, rest = Fe
- Particle size = - 53 + 10 micron
- 4 Chromium carbide- Nickel Chromium 50 kg
- Composition Chromium carbide = 75 %, Nickel = 20 % , Chromium = 5 %
- Particle size = - 106 + 10 micron
- All powders should have excellent floatability & should be suitable for plasma spray coating.
Quotation should accompany detailed chemical & sieve analysis of the powders.
Thanking you
Yours truly,
Islamabad, PAKISTAN
Ed. note: This RFQ is outdated, but technical replies are welcome, and readers are encouraged to post their own RFQs. But no public commercial suggestions please ( huh? why?).
Plasma powder spray coating or plasma sputtering?
Q. Hello,
I would like to plate some metallic parts with ZrN. The deposit thickness I want it's 2-4 micrometer. Do you think I can use plasma spray coating? Or I have to use plasma sputtering process because the deposit thickness I want is very light?
Thanks to answer me.
Have a good day.
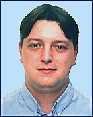
Christophe Petit
- Chicago, Illinois
2001
A. Chris:
There's no way you can plasma spray such a thin layer without leaving an enormous amount of voids or bare substrate (probably up to 50%). The thickness you are looking for is within the range of size of the plasma powder particles! I don't know enough about the sputtering.
Monterrey, NL, Mexico
2001
A. ZrN at the thickness you are looking for is typically deposited by cathodic arc, though you can sputter the coating on as well. Arc deposition is just easier, as the cleaning of the substrates is much less important (high ionization of the zirconium). A number of companies can do the work for you, if your batch is large enough to cover a full run.
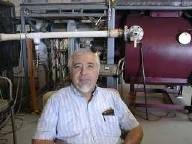
Jim Treglio - scwineryreview.com
PVD Consultant & Wine Lover
San Diego, California
2001
Q. I have a piece of metal in my laboratory for analysis which the sender claimed is coated with a carbide cermet and also polished.
Is there a difference between carbide and cermet? How can we detect if something like that is polished or further worked than the coating. If there is an analytical testing method such as ASTM or ASE to make the differentiation please let me know.
Thanks
NY Customs Laboratory - Massapequa, New York, USA
2005
A. Yves, "carbide" is usually short for "cemented carbide", which is a name for a mixture of a metal carbide particulate held together in a cobalt (or less commonly another metal) binder. The metal carbide is most often tungsten carbide, but chromium, titanium, and others can be found commercially. In this context, "carbide" is a "cermet", which merely means a mixture of ceramic and metal. It is certainly possible to have a cermet that isn't carbide- say, aluminum oxide mixed with aluminum would be a cermet, but not a carbide. (It's also pretty uncommon.)
Tungsten carbide cermets are available as bulk products: it's easy to find ball bearings, cutting tools, and wear pads made of the stuff. It is also a common coating applied by plasma or HVOF thermal spray techniques, and those are just about always polished afterwards. If I wanted to determine if a piece was solid tungsten carbide or coated steel, I'd check the density. Tungsten carbide is HEAVY.
ASTM specifications covering carbides are found in ASTM Volume 02.05.
Hope this helps!

Lee Gearhart
metallurgist - E. Aurora, New York
2005
Tungsten Carbide coating by Plasma Spray coating method
2005Q. Dear sir,
We are in manufacturing of Progressive Cavity Pump in India. For our export consignment, specification of Helical rotor is as Under:
Base Material : ASI 4150 Tungsten Carbide coating 0.010"
Is it technically possible?
We are being offer 0.001" Thick Tungsten Carbide coating by Plasma Spray coating method in India. The application of Pump is Storm water with Sand and Grit. Will 0.001" thick coating be sufficient for this application?
Assuming that hardness of base material ASI 4150 can be achieved at Rc45.
- Kanpu, India
![]() |
A. At the risk of being corrected because I am not an expert but I understand plasma spray works better for ceramics, which needs the very high temperature to melt the particles. For tungsten carbide spraying, HVOF is the process of choice and modern guns can easily deposit in excess of 0.020" (0.5 mm). Both processes work in "line of sight", which means that complex geometries and/or internal cavities will be hard to impossible to reach. Other options are CVD or PVD. Guillermo MarrufoMonterrey, NL, Mexico 2005 A. 0.010" is a bit thick, but can be done. Your part is not an easy one to plasma spray because of its constantly changing distance from the gun and the shape in general. 0.001" is quite close to not worth the effort as it will wear thru in some spots fairly quickly and then it will wear/peel from the rest very fast. - Navarre, Florida 2005 |
A. Dear Sir,
For Tungsten carbide Coating , 100 Microns is Ok for all applications after finishing. If it a severe application of wear n abrasion then we need to have coating of 300 microns.
Regards,
- Delhi, India
2006
A. 0.010" WC-Co or WC-Co-Cr is a walk in the park on 4150, especially when applied via HVOF. The HCAT website has published wear data on these coatings at this thickness. 0.001" thermal spray thicknesses often present practical challenges with adhesion. Most tech bulletins for thermal sprays mandate a 0.003" minimum.
That said, application angle is vital to coating consistency with HVOF. anything less than 45 deg from the surface may present problems. An uncomplicated geometry might be more forgiving with a plasma applied coating, and will allow angles approaching 30 deg. when I hear this application, I think along Mr. Marrufo and Mr. Watts's path of non line of sight coatings. But chrome at 0.010" might yield corrosion issues on 4150 from micro-cracking, and certainly will wear faster. PVD rocks for this sort of stuff, (maybe a layered TiN/Ti?)great with cavitation, but it isn't always cheap. Definitely a batch process.
The cheap way I would go is an e-plate Sulfamate Ni base, with a Hard Cr top coat, but watch your embrittlement. Used on Landing Gear all the time. Corrosion/wear resistant, cheap, Non-LOS, repeatable.
airline - Atlanta, Georgia, USA
July 25, 2008
Need Tungsten Carbide Coating by Plasma Spray Coating Method
RFQ: Dear Friends,
Can anyone inform me, where in India Tungsten Carbide coating by Plasma Spray coating method is done.
Thanks
compressor accessories - Kolkata, India
September 2, 2009
Ed. note: This RFQ is outdated, but technical replies are welcome, and readers are encouraged to post their own RFQs. But no public commercial suggestions please ( huh? why?).
Q, A, or Comment on THIS thread -or- Start a NEW Thread