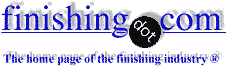
-----
To use plastic plating tanks or not
RFQ: I wish to purchase a 20 Liter divided electroplating tank with an Anion membrane.
Johan Loots- Palm Springs, California
October 16, 2023
privately respond to this RFQ
Ed. note: As always, gentle readers: technical replies in public and commercial replies in private please (huh? why?)
⇩ Related postings, oldest first ⇩
Q. We have used plastic lined steel tanks to plate nickel (semi bright and bright) since day one. These tanks, even when properly painted, still begin to rust and look ugly within one or two years time. Several of the tanks need to be replaced and I would like to replace them with tanks constructed of all plastic. This would be ok except that several here are concerned about the possibility of a fire in the shop and melting these tanks. Are their concerns valid? Are there other drawbacks in using plastic tanks? Thank you for all your help. Keith
Keith AndersonBrainerd, Minnesota
1999
A. Except in the case of extremely large tanks or special cases, steel should be considered ancient history. Polypropylene and fiberglass are both excellent tank materials--although polypro is flammable and I would be very cautious about using it if the tanks have electric heaters.
As for the tanks melting, is the plant sprinklered (yes, all plating shops should be sprinklered, see letters 42969 and 46934) and are the electric heaters equipped with modern double or triple safety cut-offs? If so, the possibility of tanks actually melting seems pretty remote.
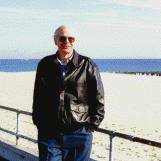
Ted Mooney, P.E.
Striving to live Aloha
finishing.com - Pine Beach, New Jersey
A. Every type of tank construction has its pro's and cons. The following are some comments/thoughts based on personal experiences with the various tank types.
On large tanks, I agree with Ted that a suitably lined steel tank is the best choice. With lined, steel tanks, cleaning and painting the outside of the tank is a fact of life as is spark testing of the lining to check for pin-holes and small tears.
An undetected pin-hole can lead to serious corrosion going on between the lining and the steel tank, and one day you could see your solution on the floor, or worse.
On smaller tanks, polypro works well. If using electric heaters, always use liquid level controllers. When purchasing a polypro tank , make sure there are adequate and properly placed reinforcing bands. If not, you'll experience bulging of the tank and breaks in the seams at corners. Another thing to watch is that the corner seams have been properly welded; if not, leaks can occur rather quickly.
With fibreglass it's a good idea to get a sample of the fibreglass that's going to be used, and let it sit for about a week in a beaker [beakers on
eBay
or
Amazon [affil links] of your nickel plating solution. Keep the sample solution at the operating temperature of your nickel solution. Then plate a Hull Cell
⇦ huh?
panel to see if there are any adverse effects. If there are, see if the nickel can be cleaned up with a carbon treatment. If it can't be, I would ask for a different grade of fibreglass to evaluate. Some resins used in the manufacture of fibreglass can have a very nasty effect on nickel plating solutions.
If you don't have a lab, your supplier of proprietary additives would probably be willing to check out the materials for you, or be able to recommend a grade which they know is ok.
With any new tank lining, you should ask your additive supplier for a recommended procedure for leaching the tank, prior to pumping the plating solution into the tank.
Cheers

Ken Lemke
Burlington, Ontario, Canada
Q. Thank you Ted and Ken for your responses. The only question I am left with is what is large? Our tanks would be approximately 1500 gallons, do you think this would be too large for polypro?
Thank you again for this wonderful service. Keith
- Brainerd, Minnesota
A. I can only speak for myself, but the only time I would choose steel today would be for very large or exceptional tanks, and I think 1500 gallons is rather ordinary. I designed a line for a steel mill a couple of years ago where the tanks were 9500 gallons (18' W x 5-1/2' L x 13' deep) and the loadbar weighed 25 tons. I "chickened out" and specified lined steel -- but that's the only exception I can think of offhand in the last few years. Being a steel mill, they would probably have insisted on steel tanks anyway.
P.S.: When it's time to buy the tanks, remember that "this wonderful service" is only possible because of our supporting advertisers.
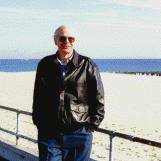
Ted Mooney, P.E.
Striving to live Aloha
finishing.com - Pine Beach, New Jersey
A. For a 1500 gal tank, most vendors will use steel angle iron as "belly bands" and use a PP angle over that to protect the steel from the chemicals. The PP angle is welded to the tank so that the apex or corner points out while the steel has one flat side touching the tank.
It is possible to build a tank out of PP completely, but this requires thicker plastic and a considerable amount of bracing on the outside, normally about 1" material.
I have seen a couple of beautiful tanks that were all PP and were larger than yours.
Fiberglass overlay with a fine cloth top fiber and a good gel coat is very nearly indestructible and good looking. A few bucks more, but a real class tank.
- Navarre, Florida
A. Hi Keith,
Your 1500 gal. tank is not overly large but in my abysmal ignorance I would have thought that a steel tank, sandblasted and having an acid resistant paint coat AND not resting in a wet sump + a nice large flange at the top so that the lining overlap would not allow drippage to get on the side walls would be perhaps ideal.
The suggestions by others to use Polypropylene make sense ... as long as you haven't got an oxidizing media in which case PVC, even the flexible PVC lining material would be better.
Like polyethylene, PP does burn, albeit quite slowly.It is not a strong material & has a low tensile & modulus, but is very good in acids & alkalies.
There is no reason not to make the tank entirely of PP but the thicknesses would be necessarily high, ditto for multiple reinforcers to prevent undue distortion.
Fibreglass might be OK ... there are a variety of 'resins' available which any competent FRP fabricator suggest you depending on temperature, acid or alkali resistance, flame spread, etc.
Fibreglass is a very good structural material. It has a heterogeneous structure not a homogeneous structure like thermoplastics and doesn't take too kindly to getting scratched, chemically speaking. Further, it's coeff. of expansion is way under that of PP. I reckon a 10 foot tank of PP will deflect easily by 1/2" for a measly 50 °F temperature differential.
The thermoplastics were essentially invented in Europe. The fibreglass industry, I like to think, was started in the USA. Both material types are DIFFERENT and have advantages & disadvantages.
If one could marry them together then you'd have the best of both worlds. The super inert & monolithic interior thermoplastic and the rugged fibreglass external structural
To-day we call this marriage DUAL LAMINATES although I used to call them armoured thermoplastics way back then as the world's first successful dual laminates were made in Canada. I remember going down to Columbus, Mississippi (Hooker Chem)in the sixties & making 15 foot diameter chlorate cell tanks on site, albeit from PVC:FRP. The secret to success is the bond and the bond strength! In those days, manufacturers had not succeeded in fusing glass cloth to PP sheets to allow one to attain a mechanical bond.
Hence, I'd suggest you might like to investigate that method price-wise versus straight PP!
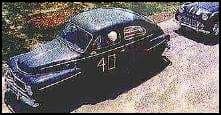
Freeman Newton [dec.]
R.I.P. old friend (It is our sad duty to
advise that Freeman passed away 4/21/12)
A. I've built poly tanks in the past, way over 1500 gal; if they're done right, its an excellent tank. I would suggest you consider polypro, but get references from the builder that are relevant to your application. 1/2" thick tanks are the general use in fabricated pro; I prefer 3/4" myself -- 1" is a bit overkill, but you won't break it.
Consider your application in ref. to tank design. Barrel tanks require a bit more heavy duty construction as they can't allow for damage if your line tosses a barrel; rack tanks need not worry as much as the weight is quite different. Space limitations! Important, polypro with steel bands will not always fit where a steel tank once was. Its very important to make sure you have enough space to replace a steel tank with polypro before you order it. A poly tank will occupy more overall space because of the steel/poly encapsulated girth bands. Also, if it's a plating/electrified tank, make sure your buss is 100% good -- an overheated connection can quickly destroy a poly tank. Electric heaters , protect yourself twice over, liquid level control and overtemp one shot thermocouple will make sure nothing can happen. Hope this helps, Ron.
Ron Landretteplating equipment supplier - Bristol, Connecticut
A. This response comes quite some time after the question was asked but I'll offer up advise anyways.
For 1500 gallons 3/4" PP is ideal. The girthing is key to any large tank design. Steel encased PP girthing is common but prone to cracking in heated tanks if not constructed properly due to differences in expansion between steel and the PP. Make sure the entire tank is extrusion welded for much stronger welds and better weld coverage.
As for fire concerns, Fire Retardant PP is available, but of course, it's more expensive.
- Forest City, North Carolina
2001
A. Fire retardant PP is a material of construction that you really have to think about though! I designed a whole plating shop for NASA with it, and it was fine for many tanks, but not all. Specifically, we had to scrap the electroless nickel tank as we simply could not get it to work due to the never-ending leaching of the bromide fire retardant.
Regards,
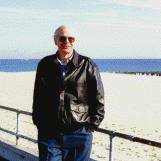
Ted Mooney, P.E.
Striving to live Aloha
finishing.com - Pine Beach, New Jersey
Q. Hello everyone,
I have been assigned in my work to set up a new electroplating line consisting of about 60 tanks of dimensions 35 cm width, 40 cm length and 40 m height. Usually all of our tanks comes from Europe and are made out of Polypropylene. Since it's quite expensive, I have been asked to try to find locally, suppliers that can make these tanks.However they are only able to make them in fibreglass. My question: Is fibreglass a suitable material for the plating tanks assuming they will contain strong acidic and basic electrolytes. Our set up must also be used for at least 5 years.
July 17, 2014
- Goodlands, Mauritius
A. Hi Ruben. Many different resins are used in "fibreglass", and it's the resin rather than the glass that must be chemically resistant. Please specify "vinyl ester resin", and don't forget the "surfacing veil", and then I doubt that you will have trouble with any of the tanks -- I know that I never did. Still, I would not use fibreglass on an electroless nickel plating tank or a chrome plating tank or any tank that was above 200 ° F (except a hot rinse). And I'd think twice, or go with the cheaper steel tanks, if the cleaners operated at 180 ° F or above. Best of luck.
Regards,
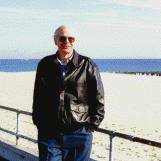
Ted Mooney, P.E.
Striving to live Aloha
finishing.com - Pine Beach, New Jersey
A. Hi Ruben Chinapiel.
Certainly P.P is the best solution.
Gunatit Builders

Manjalpur, Vadodara, Gujarat
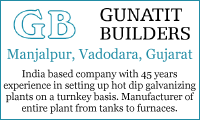
Hi Ilesh. Polypropylene can be a great material of construction, but only if you are super careful about electric heaters, potential bad contacts on electrified tanks, and other ignition sources. For several years I was "the plating shop specialist" for a firm that assisted insurance companies in fire claims & investigations ... and without exaggeration virtually every plating shop fire started from an electric heater in a polypropylene tank. If the solution level drops, the radiant heat can rather easily ignite the polypropylene.
Regards,
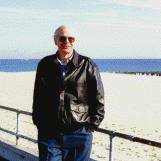
Ted Mooney, P.E.
Striving to live Aloha
finishing.com - Pine Beach, New Jersey
A. Hi
Not being an expert in glass fibre electroplating tanks but being quite familiar with glass fibre then I would be asking more about the gelcoat rather than the resin used to bond the fibres - that is assuming that EP tanks are gelcoated.
Seems that people have been using GRP for tanks for a long time so one assumes no problems other than those mentioned. I would however add that those in the boating fraternity do talk of slow ingress of water into the GRP matrix over extended periods of time so as far as I am aware GRP is not waterproof in the strictest sense although for most practical purposes it is.
- Dublin, Wexford, Ireland
October 14, 2016
Hi Jon. I've had a couple of fiberglass boats, so I know what you mean by gelcoat. I have never personally fabricated a fiberglass tank so I could be in error, but to my knowledge gelcoats are not used. Rather, rectangular tanks usually have three or more layers of glass roving impregnated with resin, then a resin-rich 'surfacing veil' on the inside of the tank which is sort of like a thin membrane that enhances the smoothness. Sorry, I don't know whether the veil is more usually applied right on the mold as the first step in construction, or is applied last to the inside of the finished tank asthe last step :-)
Regards,
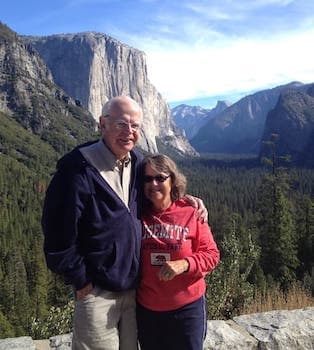
Ted Mooney, P.E. RET
Striving to live Aloha
finishing.com - Pine Beach, New Jersey
Q. We are looking at setting up a line for the de-oxing of copper and our customer specification is requesting a steel tank using a PVC or koroseal liner (or some other similar liner). The solution would be 32% HCl mixed with an equal amount of water operated at room temperature (59-95 °F). Would a carbon steel or stainless steel tank work well for this? If not, what would be a better option?
Benjamin Grant- Wheeling, Illinois, USA
October 16, 2017
A. Hi. A PVC/Koroseal liner in a steel tank would work. But if the tank is not huge, I prefer polypropylene or vinyl ester fiberglass. The issue is that over time the outside of a steel tank usually gets exposed to spills of corrosive chemicals, or fumes from them (HCl fumes significantly), or the liner gets a tear -- so a plastic tank is generally a lower maintenance, longer-lived solution.
Regards,
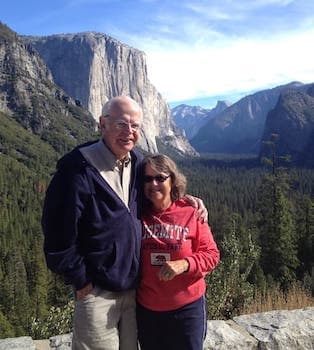
Ted Mooney, P.E. RET
Striving to live Aloha
finishing.com - Pine Beach, New Jersey
A. Hi Benjamin
Ted's advice is sound but HCl fumes significantly and you may need fume extraction.
However there are other more benign processes for cleaning copper. Without knowing how contaminated the copper is or your end use, advice can only be general. I would suggest that you take advice from any of the process suppliers linked to this site before you make a final decision.
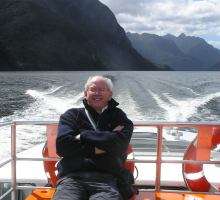
Geoff Smith
Hampshire, England
Unfortunately our customer is defining the specific chemicals we have to use to clean the copper that will be used in our electropolish line. We are looking at attaching a fume hood at the top of the tank to help with the fumes. I was very concerned about the inevitable spill and how a steel tank would handle that.
I too would think a polypropylene tank would work far better for our size and safety and will try and convince them to proceed with that instead of a steel tank with a liner. Thanks.
Dynomax Inc. - Wheeling, Illinois, USA
A. We're sure your problem will be solved with Polypropylene tank with in-built ducting system for Fume extraction and then cleaning it via scrubber.
Ilesh G VyasGunatit Builders

Manjalpur, Vadodara, Gujarat
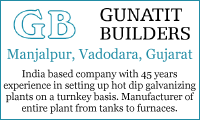
Q, A, or Comment on THIS thread -or- Start a NEW Thread