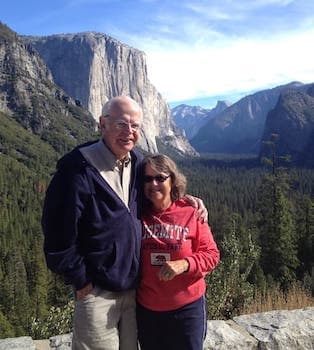
Curated with aloha by
Ted Mooney, P.E. RET
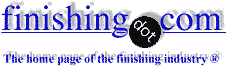
The authoritative public forum
for Metal Finishing 1989-2025
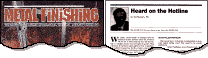
-----
Pickling and bright dipping of copper
Q. I often read your threads on metal finishing and you have helped me a great deal throughout the years. I have been in the field a while and now have my own company.
I'm currently Tin plating copper bus and using a heated caustic based soak clean and 15 percent sulfuric pickle. However, I'm having trouble with adhesion or activation especially around the edges of the part where it has been laser cut and it's been overheated. There is a copper oxide all around the cut edge.
I know there are various ways of effectively removing scale and oxides from the copper but I don't want to kill my tin acid bath with drag in.
What do you recommend I do?
What do you think would work the best without being problematic for my bath down the road. I could maybe add some nitric into the pickle. I could also maybe add some ammonium bifluoride, or the E prep 222 you had mentioned.
Any advice would be appreciated.
- Virginia
September 23, 2023
A. Hi Aaron. You must plate onto metal, you can't reliably plate onto oxides. In turn, this means that you must remove those oxides, and apparently the sulfuric acid isn't cutting it.
We don't suggest brands or sources in this forum ( huh? why?). EPI is a supporting advertiser of this site; please consider mention of their products as an advertisement rather than a recommendation of a particular brand. But I have seen sulfuric acid plus stabilized hydrogen peroxide successfully used as a copper prep several times, and it strikes me as simpler & safer than the alternatives. I'm not aware of bifluoride being useful or needed unless the alloy contains silicon.
But process changes should be tested in the lab before being implemented on the production line. So maybe pull a few parts after cleaning, pickle them in beakers in the plating lab, and then return them to the line for tin plating. As long as you have good rinsing between the acid dip and the tin plating I would not expect the addition of an oxidizing agent to the acid dip to adversely affect the subsequent process.
Luck & Regards,
Ted Mooney, P.E. RET
Striving to live Aloha
finishing.com - Pine Beach, New Jersey
⇩ Related postings, oldest first ⇩
Q. We are making copper washers. Is there a defined method to pickle copper washers so that it shines and does not become blackish.
Vikram Kiradgaskets & components - Pune, Maharashtra, India
2001
![]() |
A. I would recommend using a peroxide-based bright dip followed by a triazole containing corrosion inhibitor. This will provide some tarnish resistance, but won't last forever. To keep the parts bright for long periods of time, a clear chromate finish or a lacquer sealer may be what is needed. Dan Brewerchemical process supplier - Gurnee, Illinois A. What you are looking for is a bright dip, not a pickle. The bright dip has many formulations, but will typically contain some nitric acid and some chromium 6. I would suggest finding several formulations from several sources and try each of them in the lab. The exact copper alloy and temper will make a difference as to which one will work best. James Watts- Navarre, Florida |
A. We also manufacture copper washers. Pickling won't solve your problem. Copper due to the material nature gets oxidised quickly when exposed to atmosphere. The best way to have a highly concentrated sulfuric & nitric acid bath, then it has to be rinsed with water (preferably soft water). Then it is dipped in a solution (Copper finish solution).
Thanks.
Karwar Industries- Mumbai, India
2004
Q. I am a student trying to make a copper-water heat-pipe. The copper tube has etched in rectangular grooves running in the axial direction. The aspect ratio of each groove is 0.5 mm x 0.5 mm. In the course of my testing, it came to my attention that the copper surface trapped a lot of gas which evolve out into the evacuated heat-pipe. After reading a bit, I learned that heat-pipe manufacturers typically pickle the copper in a nitric/phosphoric acid (50%-50%) solution. I guessed that this solution had the effect of cleaning and passivating the surface and that the passivation likely decreased the porosity of the oxide layer and the associated trapped gases.
On my first try, I first cleaned a piece of copper measuring 50 mm x 25 mm x 1 mm by dipping it into NaOH followed by HCl. Afterwards, I submerged this copper into a 15cc mixture of nitric acid (50% acid - 50% DI water) and phosphoric acid (50% acid - 50% DI water). The dipping was done in room temperature, and the beaker was hand-twirled to produce a swirling motion. After 3 minutes, the resulting copper was removed from the beaker and sequentially dipped into 3 beakers of DI water for rinsing purpose. The whole rinsing process lasted around 10 seconds. The piece was then immediately dried with a paper towel. The piece was pink in color and looked a little rough similar to having been sandblasted.
On my second try, I placed another copper piece with same measurement and NaOH/HCl precleaning into a 400 cc mixture of nitric/phosphoric acid. Again, the dipping occurred in room temperature, but without the swirling. After 2 minutes, the copper was removed and subjected to an extended rinsing cycle of 1 minute. Afterwards, the piece was left to air dry. Upon inspection, I found the piece to have streaks of blue-ish/red-ish marks. There were also a few pink spots, but most of the surface had the typical copper color (reddish/yellow). The surface also looked a little rough, but was also noticeably more shiny than in my first try.
The following are now my questions:
1. What is the function of the nitric acid and why the mixture with phosphoric acid?
2. What is the passivation layer supposed to be?
3. How much solution am I supposed to use for the dimensions mentioned above?
4. Is the pickling process self-limiting or is there a requisite time duration?
5. Is agitation or heating required during the pickling process?
6. For my objective, do I wish to have surfaces similar to that produced under the first trial or the second?
7. What are the bluish/reddish streaks?
8. Why did the surface in the first trial turn up pink while the second trail turn up reddish-yellow?
Any help or pointers would be greatly appreciated.
Samuel Leestudent - Kowloon, Hong Kong
2004
sometimes on
AbeBooks or Amazon
(affil links)
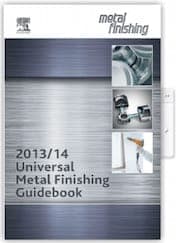
free pdf is currently available from academia.edu
A. Hello, Samuel. Students like yourself want to deeply understand their projects, and that's admirable. But even still ...
When you decide to make a heat pipe, you start with a piece of copper metal, you don't re-invent copper mining and smelting technology.
Similarly, metal finishing and the supply of metal finishing chemicals has been a well-developed industry for over a century, so I suggest that you treat the issue of bright dipping like you treated the copper metal: Find companies offering packaged processes for bright dipping copper and buy the process from them; they will include technical data sheets with operating conditions that have been demonstrated to work over the decades, plus troubleshooting hints.
Nitric acid based solutions are usually reserved for cleaning up very heavy scale rather than simple chemical brightening these days. I would investigate a proprietary sulfuric acid - peroxide dip designed for bright dipping, and then follow with a dilute sulfuric acid dip if necessary, and then treat with a proprietary benzotriazole-based copper preservative ⇦ this on eBay or Amazon [affil links] . Further info can be found in the Metal Finishing Guidebook ... but a proprietary process will probably be faster, easier, and better than a home-brew of acids, oxidizers, stabilizers and other addition agents. Good luck.
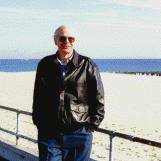
Ted Mooney, P.E.
Striving to live Aloha
finishing.com - Pine Beach, New Jersey
Pickling brass with citric acid
Q. Hi, I am doing my final year project on pickling process in a company. They use Nitric acid for removal of carbon contents (pickling) that is scale removal process in brass material. We would like to implement and suggest citric acid for pickling process. But I have doubts whether citric acid will do scale removal process for brass. Please do give some ideas and help me.
Aravinth Kanagaraj4th year Student, Sastra University - Trichy, India
February 8, 2018
A. Hi Aravinth. I am not familiar with the use of citric acid for pickling or bright dipping brass; my understanding is that simple mineral acids will not brighten brass because oxidizers are required. But we have attached your inquiry to a thread where we've suggested that a proprietary mix of sulfuric acid and inhibited hydrogen peroxide might be able to be used for bright dipping of copper and brass. In this case the hydrogen peroxide provides the oxidizing power, which obviates the need for nitric acid.
Remember that theoretical knowledge like this is to guide you in jar-testing of a revamped process ... you don't redesign a production process without testing :-)
Luck & Regards,
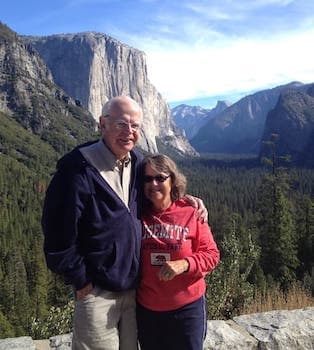
Ted Mooney, P.E. RET
Striving to live Aloha
finishing.com - Pine Beach, New Jersey
February 2018
Q. I heard that for stainless steels citric acid is better so is it better for brass? While using nitric acid the brass material tends to tarnish and shining is lost in 4 weeks. Which acid can I use for pickling of brass.
Aravinth KanagarajSastra University , Thanjavur - Trichy, India
February 8, 2018
(to help readers understand and follow the Q&A's)
citric acid , or alternately nitric acid, is not used to brighten stainless steel but to 'passivate' it. If stainless steel receives any exposure to plain steel during the manufacturing process (which it almost always does), it will rust; passivation is required to dissolve this contamination by carbon steel. You can search the site for dozens of threads about passivation, including citric acid vs. nitric acid passivation.
A. Hi again Aravinth. You can certainly do a bit of jar testing of citric acid if you wish, but my opinion is that it will play no useful role in pickling or tarnish prevention for brass.
citric acid is used for passivation of stainless steel, not brightening or tarnish prevention. The tarnish which forms on stainless steel is essentially transparent, which is why it can maintain its shine; the tarnish which forms on brass is brown-ish, which is why the shine is lost.
A dip in a sodium benzotriazole based or chromate based tarnish preventer will extend the period of brightness. If electrical conductivity is not required, a lacquer or clearcoat can be applied.
Good luck.
Regards,
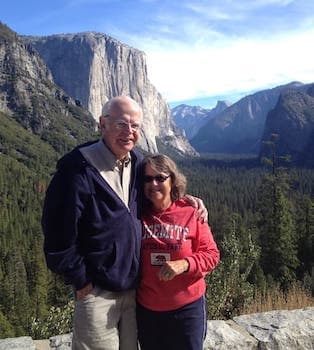
Ted Mooney, P.E. RET
Striving to live Aloha
finishing.com - Pine Beach, New Jersey
A. Brass tarnish isn't really terrifically difficult to remove, citric acid is one among many things that do so effectively. This generally leaves the surface shiny and new-looking. I'm not sure if that counts as a "bright dip" or if that term refers specifically to something else.
Note that this does nothing to prevent the tarnish from coming back, that's where you need a clear lacquer or something similar.
Though I don't think the terms pickling or scale are typically used in reference to brass tarnish, so I'm tempted to think you are talking about something else.
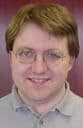
Ray Kremer
Stellar Solutions, Inc.

McHenry, Illinois
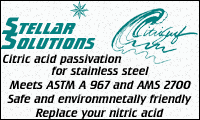
A. Thanks Ray. I suppose, but don't personally know, that if someone has a formerly bright brass object which has become tarnished, citric acid can remove that tarnish, restoring the bright finish. But to get a bright finish on brass in the first place requires, to my knowledge, an oxidizing solution. Pages 166-168 of the Electroplating Engineering Handbook ⇦ this on eBay, AbeBooks, or Amazon [affil links] explain the process of bright dipping copper and brass, concluding with mention of proprietary stabilized peroxide-sulfuric acid dips as a possible substitute for nitric and chromic acids.
Have you ever added peroxide to citric acid ? I wonder whether such mixes might work as bright dips as described in the EEH.
Regards,
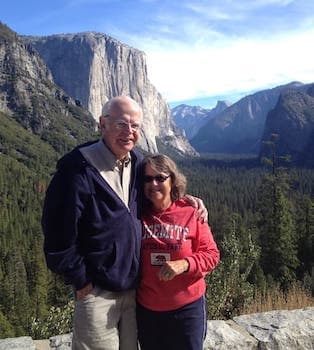
Ted Mooney, P.E. RET
Striving to live Aloha
finishing.com - Pine Beach, New Jersey
Q. Hi,
Is it good to pickle brass with sulfuric acid plus hydrogen peroxide? As nitric acid is used currently in a company to remove the oxide layers of brass, which I don't want to follow. If I use sulfuric acid + hydrogen peroxide will it affect brass? And in what concentration are these two acids used?
4th year Student, Sastra University - Trichy, India
A. Hi again Aravinth. Shops in the USA almost always buy their metal finishing processes as proprietaries rather than home-brewing them, so I have only seen the sulfuric acid plus stabilized hydrogen peroxide approach as a proprietary product. But I have seen it in successful use on copper a few times; and the vendor's data sheet says it can also be used on leaded brass (I don't know for sure whether it can be used on unleaded brass, and if not why not). I suggest that you contact a vendor about its availability in your area.
Regards,
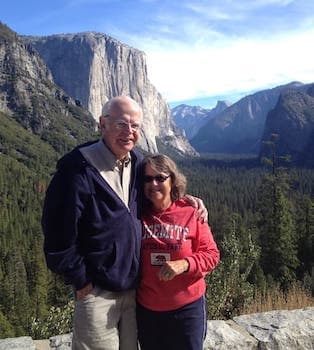
Ted Mooney, P.E. RET
Striving to live Aloha
finishing.com - Pine Beach, New Jersey
Q. Hi,
Thank you Ted Mooney sir. I followed the acid suggested by you sir that is dipping brass in water + sulfuric acid. Then dipping the component in hydrogen peroxide and then rinsing and dipping in sodium dichromate (gold coating) and then rinsing. The final result is good sir. But I want to know whether these acids will attack brass in future. If attacked what can I do sir?. And will it compensate the nitric acid cost, toxic everything. The company is using nitric acid now. I suggested and showed the result by dipping it in your suggested acid but I want to know any problems with this acids and some reasons.
Sastra University , Thanjavur - Trichy, India
Hi Aravinth. Glad to hear that sequential dips in sulfuric acid and in hydrogen peroxide worked, although that's not quite what I suggested. Good!
As for researching the long term impacts of your process changes, please return the favor by coming back to us with what you find out -- trying to teach is a great way to learn! This is a public forum, not a consultancy, and after 4 rounds of responses to your problem, apologies but we must move along because we have hundreds of other readers wanting their problems posted and replied to. Good luck.
Regards,
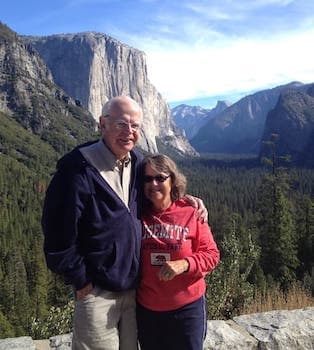
Ted Mooney, P.E. RET
Striving to live Aloha
finishing.com - Pine Beach, New Jersey
Q. Hi Sir, has anyone done any paperworks regarding the use of sulfuric acid and hydrogen peroxide for pickling of copper alloys.
Arun srini- Trichy, TamilNadu, India
March 13, 2018
A. Hi Arun. Sulfuric acid plus hydrogen peroxide is well commercialized as part of a proprietary descaler and bright dip sequence for copper ... for example, see the technical data sheet on E-prep 222 at the top of the page. There are not many free non-commercial metal finishing papers these days; most academic papers are behind elsevier.com, academia.edu, and similar paywalls, or part of conference proceedings you must pay for -- but you can try a search on scholar.google.com for "peroxide pickling copper". Good luck.
Regards,
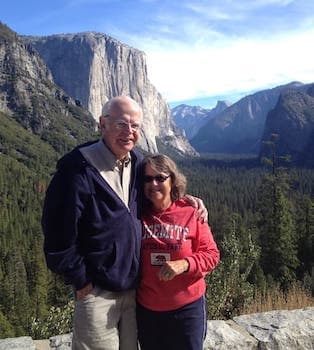
Ted Mooney, P.E. RET
Striving to live Aloha
finishing.com - Pine Beach, New Jersey
A. Hi Ted
Academia.edu only has a paywall for premium services.
You can search, read or download for free.
It is a vast database of academic papers with a considerable section on electroplating.
Many of these are academic research papers and it would be a mistake to believe that they all represent stable practical processes.
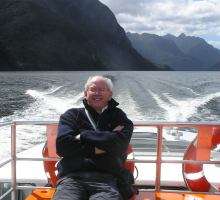
Geoff Smith
Hampshire, England
Q, A, or Comment on THIS thread -or- Start a NEW Thread