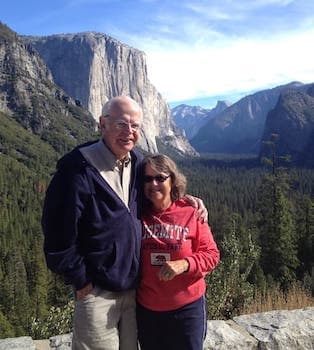
Curated with aloha by
Ted Mooney, P.E. RET
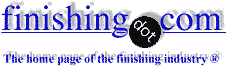
The authoritative public forum
for Metal Finishing 1989-2025
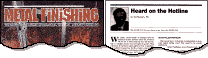
-----
Power Supply for Hobbyist Zinc Plating
Q. I'm very pleased to have found this website, and hope I can find some assistance. I am setting up a small hobbyist zinc plating operation. I have all of the required materials, but my question relates to power supplies. The materials I have suggest approximately 1-1/2 volts applied to the cathode and anode, at a rate of .025 amps per square inch of material to be plated. The parts I plan to plate range from an inch to 400 inches or from .025 amps to 10 amps.
D-cell batteries will only work briefly for the smallest of items. Unfortunately there seems to be no source for an affordable adjustable power supply. I considered using an inexpensive auto/marine battery charger ⇦ this on eBay or Amazon [affil links] as a source, some are available in 10/2 amp settings for 6 and 12 volts. I had hoped to use resistance to control the power to the required settings. I dug out my old college physics textbooks and spent much of this morning number-crunching, and it seems possible to use resistance in series with the plating load to reduce voltage and resistance in parallel with the plating load to reduce amperage flowing to the plating load. I've calculated the required resistors and none seem to exceed 420 ohms at 10.5 watts. I found variable coil resistors that can handle this load.
Am I on the right track or are my assumptions flawed? Am I missing out on some simpler/more affordable approach? Any help that can be offered is greatly appreciated.
Damon K [last name deleted for privacy by Editor]- North Wales, Pennsylvania
1999
A. It would take dozens of D batteries in parallel to deliver 10 amps @ 1.5 volts. The parts cost for a line-powered 1.5VDC @ 10A power supply shouldn't be too much, perhaps an experienced electronics person could build one for you if you can't yourself. Try a surplus electronics store to keep the cost down. If 6 volts is really too much, then this might be the way to go.

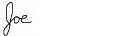
Joe Davisson
St. Louis, Missouri
1999
A. Battery chargers generally supply unregulated, unfiltered power, with lots of ripple. This is good for charging batteries but not so good for certain kinds of plating. It's not hard to build a power supply. Radio Shack has a great little book with detailed plans for constructing voltage regulated power supplies. That might be the way to go, if you can't find a used one. By the way, controlling voltage and current with resistance can be done, but in the 5 - 10 amp range the resistance elements will have to dissipate a lot of power and can get mighty HOT.
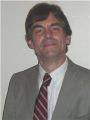
Dave Wichern
Consultant - The Bronx, New York
1999
A. Why don't you use the battery for the source of current in plating, and recharge a second battery with the battery charger ⇦ this on eBay or Amazon [affil links] offline?


Tom Pullizzi
Falls Township, Pennsylvania
1999
A. You could try using a PC switch mode power supply. These power supplies are usually thrown away with old computers, I'd be surprised if you had to pay money form one. The +5V output is regulated and usually have > 15A current rating. Make sure you use *all* the red and black wires at these current levels and keep below %80 rated output. These supplies are built at absolute minimum cost so don't expect them to be a rugged and reliable power source.
Happy plating
Adam
- Melbourne, Australia
2000
? What kind of plating you want to do? Decorative, Corrosion protection etc. What kind of solution you are using? How much money to invest?
Harshad v [last name deleted for privacy by Editor]- Alhambra California USA.
2002
Power supply for zinc and anodizing
Q. I am new to plating and I'm restoring an old tractor. I would like to re-plate the bolts and some of the brackets. I ordered a zinc plating kit from an online retailer. They sell the power supply also but for the surface area I would like to plate, the power supply of adequate size is to expensive. I need at least a 10 amp supply. I have seen some on eBay & amazon but I'm not familiar with all the technical specs to know if they will work for plating. One unit is a BK Precision 1746 linear 0-16v/0-10amp. the other is a Korad KA3010D linear 30v/10amp. Are these a suitable power supply for plating and anodizing?
Joe KellyHobbyist, Restorer - Fort Walton Beach, Florida, USA
December 27, 2018
A. Hi Joe. We don't comment on particular brands or sources (why?), but 16 V is far more than enough for zinc plating ... but iffy for anodizing some alloys. But there is a lot more to plating & anodizing than a power supply, so I would suggest trying some samples with whatever smaller equipment you have or can easily afford. I think you'll find bolts more difficult than you expect, so why not try to plate one with dry cells or an old 6-volt old tractor battery or battery for a child's ride-on toy before gearing up for production? Good luck.
Regards,
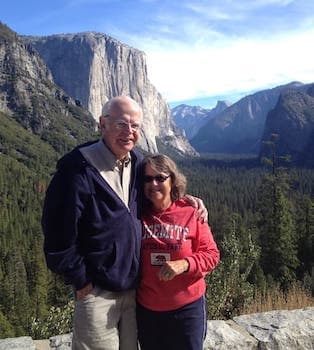
Ted Mooney, P.E. RET
Striving to live Aloha
finishing.com - Pine Beach, New Jersey
December 2018
Q. Ted, Yes I still have a lot to learn. I have never experimented with plating. I have read a ton over the last couple of days to the point by brain hurts. I have been wanting to put a system together for some time now.
I'm looking to keep it simple in the sense that I just want to flip a switch, adjust my values with the knobs on the PSU, and plate. I really don't want to mess with batteries, chargers, light bulbs and such. Maybe I'm over thinking the whole thing and making it more confusing than it is.
I'm looking at trying to zinc plate up to about 60 sq. inches and anodize up to about 30 sq. inches. Could you recommend spec's and features in a PSU that I should be looking for?
From what I have read there are basically two types: a linear and switching. Does it really matter in plating which one to use?
Joe Kelly [returning]- Fort Walton Beach, Florida, USA
December 28, 2018
December 2018
A. Hi Joe. My understanding is that switching power supplies involve using electronics to change the frequency of the incoming current from 60 Hertz to a much higher frequency so that the transformer can be much smaller; and that they became popular as a result of the micro computer revolution in the mid to late '70s because hobbyists and consumers didn't want to lug around a fifty pound transformer with their Apple 1 and such. Industrial plating, with its very high amperage power supplies (often many thousand Amps), was slow to adopt switching power supplies but they are no longer uncommon.
10 Amps is a very small plating power supply by industrial plating standards, but adequate for 30 to 60 sq. inch parts ... and for zinc plating and anodizing I don't think there's any particular advantage to a 10 Amp linear power supply over a switching one.
But the idea of keeping it simple and just flipping a switch and plating probably has a number of well seasoned electroplaters with their decades of experience chuckling ... which is why I'm suggesting you try to successfully plate one part before committing to refurbishing the plating on your whole tractor. Knowledge & experience, not a particular power supply, really is the heart of the matter.
Regards,
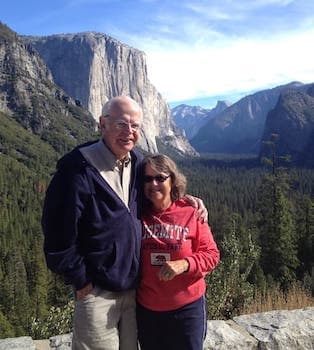
Ted Mooney, P.E. RET
Striving to live Aloha
finishing.com - Pine Beach, New Jersey
December 28, 2018
Hi Joe
As one of Ted's old platers ........
A couple of things you need to know.
Prep for plating is vastly more important than for painting. Do you have the the essential chemicals for this and how to confirm that the cleaning was successful?
And do you have the chemicals to remove unsuccessful plating? You are not going to get it right first time.
Assuming you get a good deposit, you need to know that nuts and bolts are particularly difficult. Inside threads are difficult to get coverage and male threads build up on the peaks and starve the valleys. So threads that fitted perfectly before plating don't any more.
I like to see people trying new ideas; But I also like old tractors! There surely must be a local plating company that would give you the finish you want at a fraction of the cost of setting up yourself.
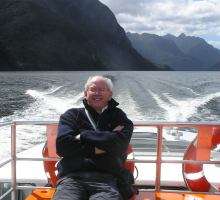
Geoff Smith
Hampshire, England
Q. Geoff Smith, Thank you for replying. There is not a plating company near me. I would have to ship all the pieces to a facility. A lot of the fasteners and bracket are either obsolete or very expensive to replace if lost. I have not contacted anyone (I might do that tomorrow) but from what I have read is that facilities will take it in one lump of parts. I have them sorted and tagged so I know where they go. If I get a pile of nuts, bolts, spring, clips and so on back in one pile, I will spend 2019 sorting them back out. I like learning new things and have the time to apply to this project. I know the zinc finish that I will get probably won't be as good as a professional plating facility but I'm ok with it. This tractor will not see any more farm life as long as I have it. It will be my own collector's item. I have been reading different forums and watching videos on the products I have bought and feel I will have great DIY hobby results.
Joe Kelly [returning]- Fort Walton Beach, Florida USA
January 3, 2019
A. Hi again, Joe. You can read and watch videos about how to rebound a basketball a hundred times, but you'll still totally stink the first time you hit the court. Please practice on scrap parts because, speaking of expensive, if you've redone the parts one-too-many-times and over-pickled them you won't be able to save them. If any of the parts are high strength steel, don't forget the baking before and after plating. Best of luck.
Regards,
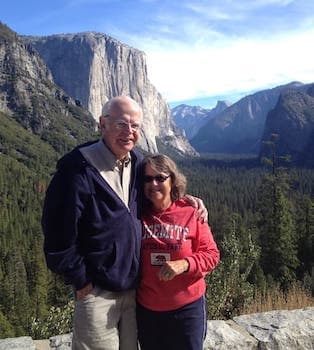
Ted Mooney, P.E. RET
Striving to live Aloha
finishing.com - Pine Beach, New Jersey
January 2019
Q. I have been reading about hydrogen embrittlement. I'm not sure of the grade fasteners used. The tractor that I'm trying to restore is a Kubota B6100. Mine was manufactured in 1979. All the bolts have a number stamped in the top 4,7 and 9. I know these numbers are used to indicate what torque is called for that fastener but would imagine the higher the number on the bolt head the higher the strength of steel. Most all the fasteners range between 6 mm-10 mm with a few 12 mm hold the axle gear case together. I'm having a hard time finding an appropriate bake schedule to follow. Especially since I don't even know what grade I'm dealing with. Any thoughts would be very appreciated. Thanks.
Joe Kelly [returning]- Fort Walton Beach Florida USA
January 7, 2019
A. Hi again. Please google for "bolt strength head markings" or a term like that. For someone to try to safely guess the strength and hardness of a fastener from a verbal description of a marking won't work.
Some fasteners are so hard that the specs forbid plating, but the basic idea of hydrogen embrittlement relief is bake before plating, then use only anodic cleaning and the mildest possible (or no) acids (substituting blasting for the oxide removal), then highly efficient plating (generates the least possible hydrogen), then baking again *ASAP*. Baking temperature 375 °F ± 25 °F for 3 hours minimum, probably up to 8 hours, and never use your kitchen oven for anything but food.
Keep in mind as you roam the internet for advice that "instructional" and "how to" sites are funded by advertising dollars, and their purpose is to earn advertising money from clicks. Many of the articles are written by people with zero experience in the subject; their expertise is limited to locating good 'key words' to draw traffic, then posting something they found that has those keywords :-)
So, just because they tell you how to do something and what supplies to buy is no indication that the author has actually ever done it or even been anywhere near the issue s/he is writing about :-( Although this site is also funded by advertising, we are fortunate to be blessed with many knowledgable readers, and we concentrate on one very narrow industry that the administrator has worked in for 50 years,
Regards,
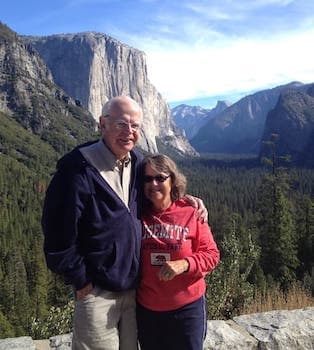
Ted Mooney, P.E. RET
Striving to live Aloha
finishing.com - Pine Beach, New Jersey
January 2019
Q. Hi, I have been experimenting with zinc plating small iron pieces. My question is, if I want to try zinc plating larger pieces I will obviously need to make a bigger bath, is there a limit to the size of bath I can use for a given power supply, would this work in a larger bath or will I need to step up the volts/amps or amount/size of cathodes being used. I would like to attempt zinc plating a swingarm off a kid's quad motor cycle, maybe do the whole frame eventually. Also would it be better to copper plate the iron/steel items and then put zinc on or just go straight zinc. Thanks for your time, cheers
Rodney Leigh De Jong- cranbourne south victoria
November 5, 2020
A. Hi Rodney. You had posted your inquiry on a thread about student science projects, but I thought it better to move it to this page.
Last question first: You should not do copper plating under zinc plating; that will increase the corrosion rate of both the zinc plating and the underlying steel.
Please see our "Introduction to Faraday's Law" which explains the science behind the amperage and voltage needed for plating. You will need a capacity of about 10-20 amperes per square foot of surface area you are plating. The required voltage is about proportional to the distance from anode to cathode, but that anode-to-cathode distance tends to grow as your parts get bigger just based on practical issues of not wanting the parts to short circuit on the anodes. Parts in a beaker are generally close enough that 2-3 Volts will do but large parts will tend to be far enough away that about 6 volts might be required.
Luck & Regards,
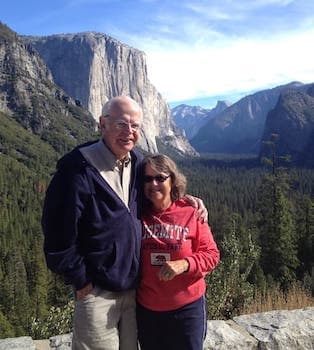
Ted Mooney, P.E. RET
Striving to live Aloha
finishing.com - Pine Beach, New Jersey
November 2020
Q, A, or Comment on THIS thread -or- Start a NEW Thread