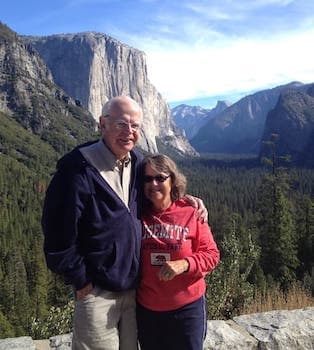
Curated with aloha by
Ted Mooney, P.E. RET
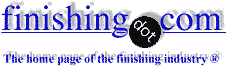
The authoritative public forum
for Metal Finishing 1989-2025
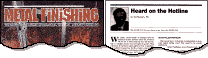
-----
Aluminum Brite Dip Chemical Composition / Effective Polishing Techniques
Quickstart: Aluminum 'bright dipping / chemical polishing' is a process done before anodizing on reflectors (street lamps, dentists' lights), but requires a nearly boiling mix of nitric & phosphoric acids.
It is probably the hardest to handle chemical in metal finishing, emitting clouds of choking brown NOx, requiring special garage style exhaust, custom double fume scrubbers, and usually automation because human exposure is a problem. It's also so corrosive that double-walled type 316L stainless steel tanks are usually used to hold it.
The term 'bright dipping', however, is slang -- so other processes are sometimes called 'bright dipping' which are far less aggressive and noxious, but not helpful for reflector manufacturing.
for Shops, Specifiers & Engineers
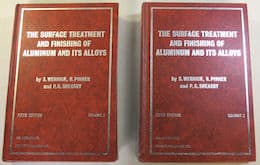
avail from eBay, AbeBooks, or Amazon
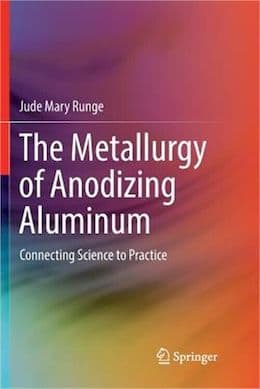
avail from eBay, AbeBooks, or Amazon
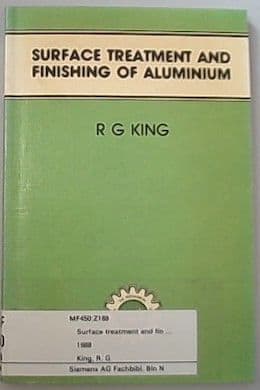
avail from eBay, AbeBooks, or Amazon
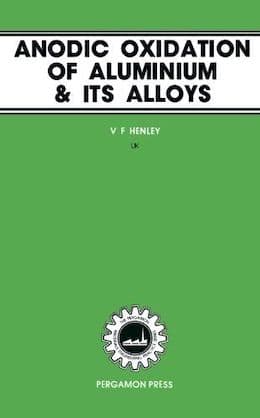
avail from eBay, AbeBooks, or Amazon
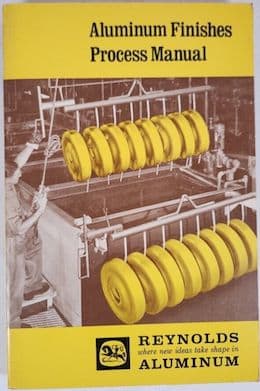
avail from eBay, AbeBooks or Amazon
(as an Amazon Associate & eBay Partner, we earn from qualifying purchases)
Q. Sir
I have an Aluminum Anodizing Plant and am doing job work.
Right now we're using phosphoric acid and sulfuric acid for bright dip.
But recently I read all these articles and question & answers and made new tank with 94% phosphoric acid and 6% nitric acid ...
Got a good result but problems arise about nitric acid smoke -- very dangerous for eyes & nose, and can't work or stay around there. Suggest if there is any solution please.
Please suggest solution for nitric acid smoke situation and what temperature should I use this bright dip with phosphoric acid and nitric acid.
- Rajkot Gujarat India
December 20, 2021
A. Hi cousin Bharat. These solutions run at near boiling, say 200-210 °F, although some people claim it can be done at 185 °F.
But no, you did NOT "read all these articles and question & answers" or you wouldn't have done it because we never fail to suggest that this process only be done inside a garage type hood with automation -- never manually out in the open with conventional exhaust systems :-)
You can try the proprietary fume suppressants to see how much they help, but even with them I doubt that it is safely workable on a manual line. In 40 years of frequent visits to plating & anodizing shops I only saw three shops which did aluminum brite dipping, and all three were automated and did their small manual bright dipping experimentation within a lab hood.
If your solution is being held in other than a fluoropolymer lined 316L stainless tank or a double-walled 316L stainless steel tank, leakage onto the floor may be just around the corner, and your problems only beginning. Electropolishing might be an alternative :-(
Luck & Regards,
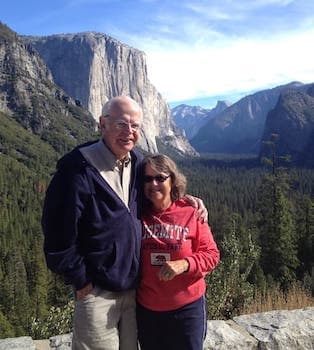
Ted Mooney, P.E. RET
Striving to live Aloha
finishing.com - Pine Beach, New Jersey
I guess the first thing to say is if you have been working anodizing shop for any extended length of time, then you should be glad that your nose is still able to be offended by the fumes.
Bright dip temps can vary depending upon what type of jobs you are processing. polished parts might need to be around 210 °F but up to 220 will work fine as well especially if you are bright dipping reflectors. Non polished parts can be processed the very lowest 185 °F as Ted wrote but that could almost be pushing it which could result in an etching type process as opposed to brightening.
Lastly again Ted is correct. Ventilation is critical. All work loads will generate differing amounts of fumes or orange smoke. Wearing a ventilator is not a good remedy. Ventilation along with fume scrubbing is critical. you may be getting yourself in deeper than you want to go. Proprietary chemical brightening chemicals may be the way to go with having fumes that are much less noxious.
supervisor - Cicero, Illinois
Saporito Finishing Co.

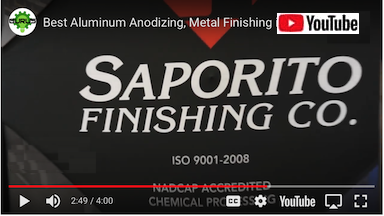
⇩ Related postings, oldest first ⇩
Q. In regards to Type II Anodizing, I have read about a process called Brite Dipping in which the part(s) are brought to a high shine utilizing a solution of this so called Brite Dip. I have done much looking on this subject and have been unable to determine what the chemical composition of this Brite Dip solution is. Is it possibly/advisable to mix my own Brite Dip solution? Secondly, at what temperature does this Brite Dip solution operate at?
I am also looking for an effective mechanical way to polish several parts at once on a processing line environment. Currently I am buffing my parts manually utilizing a variety of polishes. What would you suggest a person use in order to increase production without losing any of the quality. Would a simple bead blast followed by a Brite Dip be sufficient?
Thanks so much for your time. Cheers!
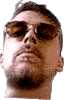
Daniel DeGueldre
anodizing shop entrepreneur - Ste. Anne, Manitoba, Canada
2004
Q. I am quite surprised that nobody has offered any input to this post over the past 1-1/2 weeks. Perhaps this Bright Dip solution is an old family recipe and not meant for prying eyes. Perhaps there are several recipes utilized in order to mix an aluminum Bright Dip solution. None-the-less, I have found myself stumped.
I think I have narrowed down the most important chemicals required in order to mix a Bright Dip. So far I have, Phosphoric Acid (H3O4P) and Nitric Acid (HNO3). I have done a lot of reading of the past weeks in regards to this question, yet I'm still stumped. I think I have the two major chemicals correct, however, the actual solution formula still proves impossible to nail down.
If you know what your Bright Dip solution is composed of or if you are mixing your own Bright Dip solution in your shop, please post your recipe here. I am also curious as to what temperature your Bright Dip operates at. Thanks so much in advance.
Cheers!
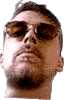
Daniel DeGueldre
anodizing shop entrepreneur - Ste. Anne, Manitoba, Canada
2004
A. Hi Daniel. Wernick, Pinner & Sheasby [on
AbeBooks,
Amazon &
eBay affil links] has a 94-page chapter on chemical and electrochemical brightening of aluminum that will explain everything you could imagine -- no secrets. Generic bright dip is composed of nitric acid & phosphoric acid and operates at 190-210+ °F. A typical formula is 80% by volume phosphoric acid & 3.5% nitric acid.
People probably don't say much about brite dipping chemistry for a number of reasons.
First, very few anodizers do brite dipping, which limits the amount of response we can expect.
Second, there are a number of proprietary suppliers, and people may not be sure if a composition they know of is generic knowledge or is actually a proprietary trade secret they can get in trouble for publishing.
Third -- and most important to me personally -- those who are familiar with it realize this is a really, really, really, nasty solution that requires specially designed garage-door type fume containment (not conventional lip exhaust or push-pull exhaust), plus rather special unconventional fume scrubbers to deal with the wild NOx fuming and the high solubility of nitric acid which conventional fume scrubbers can't fully handle, and very well engineered secondary containment because it is extremely aggressive even to expensive construction materials. This stuff running out on the floor after eating through a 316L stainless tank would be a major concern!
So speaking for myself, while I'll cheerfully give anyone a few minutes of my time, when we get into aluminum bright dipping, it's just so chock full of "Why in the name of hell didn't you warn me about THAT?!" issues that it's a topic that cannot be quickly dispatched. I, and maybe others, tend to not want to be pulled into a discussion when I see such a very long very rocky road in front of me. Are you willing to invest in full automation? ... a totally enclosed ventilation system? ... special custom-design double fume scrubbers? ... the consequently required higher pressure exhaust fans to push the fumes through double scrubbers? ... double-walled 316L stainless steel process and rinse tanks? -- If not, please understand that I want to discourage you from working with this chemistry, not encourage you :-)
This is perhaps a good area to start with a proprietary solution from a vendor who will give you some hands-on help. I believe Albright & Wilson may be one; search for their Phosbrite bright dip.
Good luck.
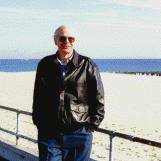
Ted Mooney, P.E.
Striving to live Aloha
finishing.com - Pine Beach, New Jersey
A. Well...For those who care to contribute or simply for those who wish to experiment, I have learned of the following formula for a Bright Dip bath :
94% Phosphoric Acid & 6% Nitric Acid operated at a temperature of 180-185 °F.
If this seems crazy, please correct me. I'm simply relaying information which has come across my desk.
It should be noted that this solution requires extreme caution when handling. Use in a properly ventilated area and dispose of the waste accordingly!
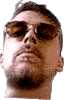
Daniel DeGueldre
anodizing shop entrepreneur - Ste. Anne, Manitoba, Canada
A. Typical home-made solution is as follows:
Phosphoric Acid 73-83% (vol)
Nitric Acid 2-5% (vol)
DI Water 14-23% (vol)
Heated to a temp of 200-210 °F.
Like Ted said: extremely nasty stuff, and use with caution. This bath works well on wrought alloys, not castings (or alloys with high silicon content). Nitric acid content must be kept stable, or you'll have undesirable results. Also heed his advice on finding a supplier of pre-made brite dips. They are much easier to work with, but if you're intent on making your own, the above recipe works well. Use double walled 316L tanks to contain your solution (I would even coat the inside with a fluoropolymer coating).
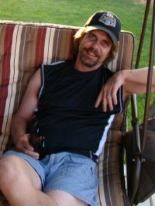
Marc Green
anodizer - Boise, Idaho
A. Bright dip for aluminum:
phosphoric acid(d=1,75) 65%
nitric acid(d=1,5) 25%
acetic acid
⇦ this on
eBay
or
Amazon [affil links] 10%
30-60 sec, 80-110 °C temp.
- Cerovski vrh Croatia
![]() ![]() |
A. DEAR SIR I HAVE A RADIATOR SHOP AND USED BRIGHT DIP FOR 48 YEARS, AND YOU DON'T NEED ANY HEAT. USE COLD. I USED A PLASTIC BOTTLE LAY ON IT TAKE KNIFE CUT 10 INCH HOLE IN IT PUT THE BRIGHT DIP IN ABOUT 2 INCH AND PUT THE PART INSIDE, LOOK AT IN 20 MIN. IF CLEAN, WASH IT WITH WATER , IF IT'S REAL BAD YOU LEAVE IT IN LONGER, OK? BRIGHT DIP IS AN ACID don't LEAVE THE PART HALF WAY OUT OF THE BRIGHT DIP, IT WILL CUT THE PART. OK, HOPE THIS HELP YOU. DOUG BROWN- MAXWELL, TEXAS December 11, 2008 A. I used chromic acid to brite dip aluminum parts for years at our chrome plating shop. It works immediately and is used at about 120 °F. Jack Hamor- Hesperia California November 23, 2010
To an infantryman, a tank is an armored fighting vehicle, while to an oil delivery man, it's a vessel for holding fuel. Similarly, aluminum 'brite dip' or 'bright dip' is slang that's applied to more than one process or situation. The bright dip that a radiator shop or truck-wash uses might be room temperature and fluoride based ...The bright dip that a plating shop uses might be a Chromic acid based desmutter for removing dark smuts from aluminum ... ... but the other posters here were referring to solutions which dissolve the aluminum to make it optically smooth and chemically polish it. Perhaps the phrase "chemical polishing" would be better than "bright dipping". The chemical polishing or bright dipping that we are talking about here is what is used before anodizing to make reflectors for outdoor lighting, doctors' and dentists' lights, etc., and usually involves very noxious, nearly boiling, solutions of nitric & phosphoric acid. Regards, ![]() Ted Mooney, P.E. Striving to live Aloha finishing.com - Pine Beach, New Jersey |
A. I know of 2 basic formulas for bright dipping aluminum.
The typical R5 process consists of 80% phosphoric acid, water, and HNO3. specific gravity should be around 1.65
You need 1000 ppm of copper (as copper sulphate) and diammonium phosphate or urea (2%) as a fume suppressant.
The nitric acid concentration is the 3 to 4%, water should be about 10%, the balance is the phosphoric acid. Make sure you use 80% phosphoric acid.
The second formula, similar to the phosbrite 174, is a mixture of phosphoric acid and sulfuric acid. the specific gravity should be about 1.70. Also use copper and the fume suppressant. Same concentrations as before : Nitric 2 to 4 %, about 10% water, 15 to 20% sulfuric, the balance is 80% phosphoric acid.
Operating temperature should be over 212 °F, as the b/d generates water. With the heat you control the specific gravity of the solution (also by adding water when necessary).
The immersion time should be from 1 to 3 minutes (depending on the alloy).
To formulate a B/D bath is pretty simple - I provided you with the "secret" ingredients. The real deal is to know how to operate it in a production line.
The operating parameters are very tight, if you don't keep accurate controls, you are bound for disaster.
- No. Hollywood, California
December 14, 2008
Daniel. This is a good topic. Bright dip anodize is what they used on aluminum car parts. I restore them and send my parts out to get bright dip anodized. I would like to do my own and this here has given me a lot of information. Thank you all for commenting.
Chrome world - azusa california usa
February 25, 2016
Room Temperature Acid Brightener for Aluminum
Q. Hi all, let me introduce myself, My name is Alfredo, I just opened a small workshop for aluminum products (anodizing and powder coating).
Right now I have a project to brighten aluminum. My question is:
1. Are there any Acid Based chemical for aluminum brightener that works on room temperature (do not need any heating procedures)? I don't have such facility in my workshop.
2. If there are any, can I make my own solution? I want to make the solution myself since there's no chemical supplier that provides such chemicals here.
I've read some articles using Phosphoric Acid and Nitric Acid, but none of them work (maybe it's because I have the wrong percentage of it)
I'd be really grateful for any suggestion from experts here.
Thanks before!!
Regards,
Alfredo
- Indonesia
September 13, 2018
A. Hi Alfredo. The nitric-phosphoric acid bright dip requires high temperature; moreover, it's a very dangerous mix.
What is the alloy? Are the products castings with silicon, which would require fluoride chemicals? Are you sure it's not more practical to mechanically polish the products?
Regards,
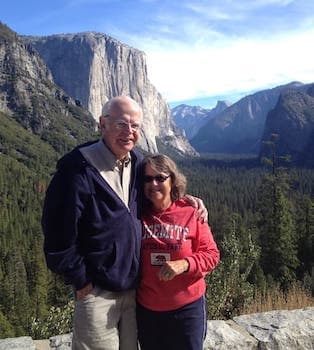
Ted Mooney, P.E. RET
Striving to live Aloha
finishing.com - Pine Beach, New Jersey
Q. Thank you Ted for your reply, really appreciate it.
The alloy is an aluminum-magnesium 5xxx series, I assume it is the 5005 aluminum series (the same aluminum for extrusion/door partition, etc). I don't know about the silicon castings of the aluminum, but I have a friend that used to work in an anodizing plant and he said that he used an acid based chemical to brighten the aluminum without any heating procedures, unfortunately the chemical is imported and he's not working there anymore.
Thanks,
Regards,
Alfredo
- Jakarta, DKI Jakarta, Indonesia
October 12, 2018
![]() |
Q. Hi, I just want to find out how to clean my gas stove buyers and now I am back in my biology class at school which I hated. Is there any simple way to clean/brighten the gas burners? Basie Van Wyk- Stellenbosch South Africa October 7, 2018 A. Hi Basie. Can we assume that your gas stove burners are made of aluminum? For a win-win, you might ask your biology teacher if she is familiar with any grease eating bacteria or other organisms that might help clean the burners. Regards, ![]() Ted Mooney, P.E. RET Striving to live Aloha finishing.com - Pine Beach, New Jersey October 2018 |
Q. I am looking for a Bright Dip for polished aluminum parts that does not contain nitric acid; it is for the anodizing process.
Hernandez, Alejandro- Tijuana, Baja California, Mexico
October 9, 2019
A. Hi Alejandro. From my own experience, I don't think you'll find a chemical bright dip free of nitric acid. However, you can electropolish the aluminum to similar brightness with electrolytes that are free of nitric acid.
Regards,
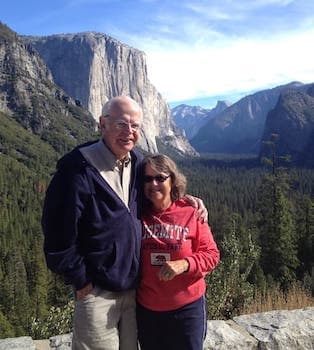
Ted Mooney, P.E. RET
Striving to live Aloha
finishing.com - Pine Beach, New Jersey
October 2019
adv.
I think Accu-Labs, Inc. [a finishing.com supporting advertiser] may have what you may be looking for:
213 ALUMINUM BRIGHT DIP
- newark, New Jersey, usa
February 22, 2020
A. Thanks Alexander! We don't print brand or source suggestions in this public forum ( huh? why?) ... so when products from our supporting advertisers are mentioned, we mark it as an advertisement :-)
The data sheet says it contains 2-4% nitric acid, but with a fume suppressant to deter NOx fumes.
Regards,
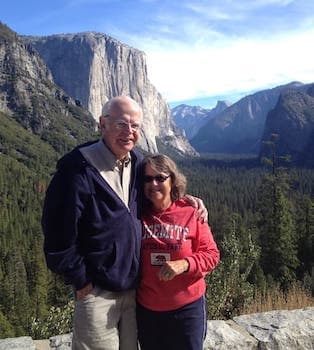
Ted Mooney, P.E. RET
Striving to live Aloha
finishing.com - Pine Beach, New Jersey
Q, A, or Comment on THIS thread -or- Start a NEW Thread