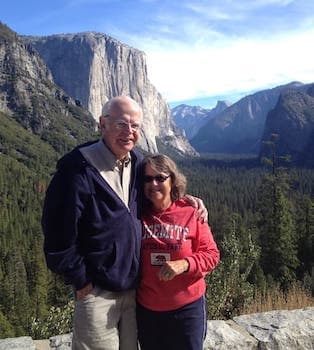
Curated with aloha by
Ted Mooney, P.E. RET
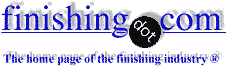
The authoritative public forum
for Metal Finishing 1989-2025
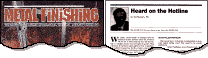
-----
Passivation of 440C Stainless Steel

this text gets replaced with bannerText
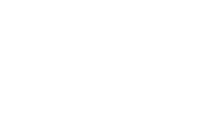
Q. Hello -
I'm looking for information on how effective a citric acid vs. a nitric acid passivating treatment is for machined 440C stainless steel components. We have been using 20%-nitric acid with the 2.5% sodium dichromate additive per AMSQQP35 [canceled] (Type-II solution). Some recent SEM examinations have revealed intergranular corrosion and preferential corrosion attack at carbide particles. The parts are typically hardened to a HRC56-60 range prior to passivation. The parts are not required to pass salt fog or similar tests prior to use; however, in-process IG or pitting corrosion can lead to SCC or fatigue cracking in service.
Best regards,
Terence Savas, Project Engineer- Irvine, California
2002
A. Terence:
As you know, 440C is very difficult to passivate properly, but it can be done quite effectively with proprietary citric acid formulations. We have data showing that it is better than nitric acid when treated according to normal alkaline/acid/alkaline procedures with the proper formulations. You have the right hardness to do the job well, but you need to clean the surface with 13+ pH solution before treating with the right citric acid formulations to get the best passivation.
adv.
We have a number of customers passivating 440C quite effectively, but there are some in the industry who say that 440C CANNOT be passivated, so do not expect the end product to be as good as an austenitic stainless in corrosion resistance. Contact us if we can help.
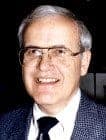

Lee Kremer
Stellar Solutions, Inc.

McHenry, Illinois
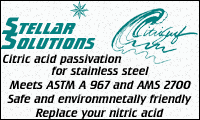
2002
2002
adv.
Russamer Lab spent some time investigating the problem of passivating steel 400 series, due to numerous requests from the customers. Our researches invented two methods of environmentally friendly passivation. The first method uses standard electropolishing equipment, low current. Passivated metal obtains black color. Surface is much better protected that any existing methods of steel 420 - 440 passivation. Salt spray test and other similar test are on the way. I will keep you posted. The second method reveals the best possible results. The surface stands any well-known tests on corrosion we have conducted so far. This passivating method is more expensive than the first method since special equipment and high voltage is required, but the results are superior.
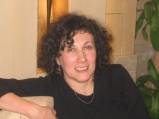
Anna Berkovich
Russamer Lab

Pittsburgh, Pennsylvania
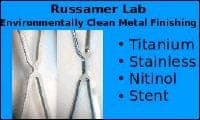
A. Okay, this reply will hopefully provide some useful information for people performing passivation of 440C and perhaps other grades like 420.
While validating a nitric passivation process I found that 440C stainless repeatability passed the boil test but sometimes failed the copper sulphate
⇦ this on
eBay or
Amazon [affil links] test (both tests ASTM F1089) in a completely random manner. Some seemingly identical batches would come up with no evidence of copper plating whatsoever and others would be totally plated. After much frustration in trying to identify the variable in passivation that was causing the problem, I finally found that the answer was the method of handling the test coupons during the test.
A single coupon would generally pass but a number tested together would often fail. If one coupon bashed into another it would damage the passive oxide layer over the very small collision area, which one would expect to become plated. Instead the copper sulphate plating would first occur on the damaged area but the reaction would continue and quickly plate the entire part. I confirmed this theory by placing two drops of copper sulphate solution on a carefully handled part for the required 6 minutes. The surfaces under both drops passed the test but when I made a very light scratch on the metal the entire area under the drop became plated while the other drop remained clear. If the two drops merged the combined surface became plated.
The moral of the story is handle the test coupons carefully, although it would be good to have a passivation process that is robust enough that a scratched part could still pass the test (excluding the scratched area).
Just as a matter of interest, does anyone know if electropolishing or any other process could pass such a test with 440C or is this just not possible with this grade of material? I have tried a citric process and had a similar result to nitric.
- Christchurch, New Zealand
2007
A. (440C Stainless Steel)
FINISH: PASSIVATE i.a.w. ASTM A967, NITRIC 4, OR 10% BY WEIGHT OF citric acid AT 145 °F-155 °F FOR 30 MINUTES WITH A PRE AND POST NEUTRALIZATION WITH 5% BY WEIGHT OF SODIUM HYDROXIDE AT 160 °F TO 180 °F FOR 30 MINUTES. WITHIN 3 HOURS FOLLOWING PASSIVATION, BAKE THE PART AT 300 °F +/-20 °F FOR 8 HOURS MIN TO REMOVE EXCESS HYDROGEN PER AMS2759. DO NOT CONDUCT PASSIVATION TESTING TO AVOID CORROSION.
Engineer - Toms River NJ
February 24, 2022
When to passivate 440C component -- before or after grinding?
Q. This concerns passivation of 440C stainless steel that has been hardened to Rc 55-60. Here is my question: Should I passivate before grinding or after grinding? Moreover, another sub question: How to brighten it, that is, remove the tawny color that it takes on from hardening?
Here is why I am asking: My company manufactures precision dimensional gauging equipment. Recently we have changed some of our measuring surface plates to 440C. In the case of a ground part, does the ground surface need passivation in order to resist corrosion adequately? The instruments are used typically in laboratories or in some cases on shop floors, or in the vicinity of shop floors. I am concerned with sending out parts for passivation after the final grind, because of the risk of damage to the fine ground surface during transit. Also, how does the passivation affect surface finish quality, if at all?
Paul HossfieldManufacturer - Providence, Rhode Island, USA
2004
A. As far as whether to passivate prior to or after grinding, it should be done after. If you grind a passivated surface, the passivation is lost on that surface. This is because passivation only goes into the material a very, very, very small distance. If you feel that you need to passivate, package the parts very carefully when shipping them and find a processor that is worth their salt.
I have heard that nitric acid passivation would remove the discoloration from HT, however, that has not been my experience, albeit from a long time ago. What I typically do is to either electropolish, tumble, or grit blast the surfaces to mechanically remove the discoloration. I am quite sure that you need to do this prior to grinding the final dims on your gage blocks.
I would think that gages used in labs and in shops (I work in both labs and shops) from 440C should be fine without passivation, particularly on the ground surfaces. Moreover, as a purchaser of this sort of thing, the discoloration wouldn't bother me a bit. As a frame of reference, razor blades are typically made from 440C. A ground 440C surface can be fairly corrosion resistant if you get a good finish. Another thing, heat treated 440C is more corrosion resistant than non-heat treated.
Marty Padget- Santa Clarita, California, USA
2004
2004
adv.
We can suggest passivating solution which we have designed and tested on Schick razors made from 440 stainless steel. Also there is another method - low-voltage electropolishing in saline-based environmentally-safe solution. Sharp parts are not damaged, and passivation layer is created on the surface.
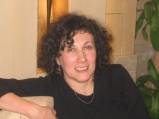
Anna Berkovich
Russamer Lab

Pittsburgh, Pennsylvania
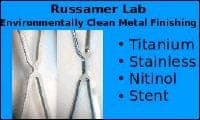
A. Hardened 440C can be passivated very well with the right citric formulations. Precleaning is important for good passivation.
adv.
We have found with our formulations run hot you can remove the normal discoloration of heat treated parts and get excellent passivation in one step. Let us know if we can help.
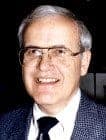

Lee Kremer
Stellar Solutions, Inc.

McHenry, Illinois
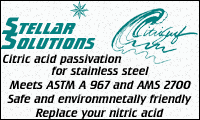
2004
Multiple threads merged: please forgive chronology errors and repetition 🙂
Tip: Readers want to learn from Your Situation 🙂
(little can be learned from abstract questions, so many readers skip them)
Q. What are the effects that would occur in a material made from 440C when passivated?
Are there any treatments to provide similar hardening and properties to that material rather than passivating?
Is AMS 5630 and AMS 5618 the only materials containing 440C?
What are the most common applications for which materials made with 440C are passivated?
Why some companies don't passivate?
- Hartford, Connecticut, USA
2004
A. Hi, Nexal.
Passivation removes loose iron (caused by machining), and to some extent it chromium enriches the surface. It doesn't harden the material. Electropolishing offers the same sort of reduction in surface iron. 440C is a specific grade of martensitic stainless steel. The general reason for passivation is to discourage rust. If steel tools were not used in the fabrication of the parts, it is possible that passivation isn't necessary.
Please tell us your own situation -- hypotheticals inject an endless list of ifs-and-&-buts into the proposition which can discourage readers from replying :-) Thanks.
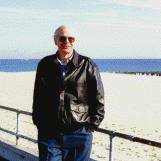
Ted Mooney, P.E.
Striving to live Aloha
finishing.com - Pine Beach, New Jersey
2004
A. 440C is a very common grade of steel that is used where high hardness is required, up to 65 Rc. It is used in almost every industry. The high carbon content gives it excellent properties for some applications, but not excellent corrosion resistance.
440C can be a difficult grade to passivate unless you use the correct procedures. Some companies say that you cannot passivate it, but this is not true.
First, it must be hardened to above 58Rc to get good passivation. You also need to pretreat with alkaline to get good passivation. Many companies use electrical assistance. In order to get good corrosion resistance you must passivate 440C, but if it is in a completely non-corrosive atmosphere you can get by without it.
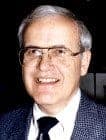

Lee Kremer
Stellar Solutions, Inc.

McHenry, Illinois
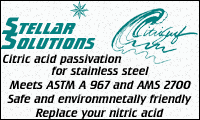
2004
Q. We have some parts with AISI 440c materials at about 55HRC hardness. When descaling in HF+HNO3, all of them etched. With commercial ferroclean some of them cleaned but others not. In solution 1 of ASTM A967 some of them passivated but another severely etched.
Now I don't know why and what to do?
Please help me. Parts are of precision dimension. Another question is about heat treatment after passivation.
sharghmetal - Tehran, Iran
2006
2006
A. Hi Saman,
Problems with 440C are largely due to the heat treatment. For precision parts, I suggest the following:
Heat treat in vacuum, inert gas or neutral atmosphere to avoid or minimize scale formation.
Preheat as necessary for large or complex or heavily cold-worked parts.
Austenize at 1065 °C (upper end of range) for maximum dissolution of carbides (increases Cr in metal to ~13%).
Inert gas quench to ~room temperature.
Subcool to -75 °C to transform retained austenite (improves dimensional stability).
Double stress relief: Heat to 250-275 °C for 1 hour, cool to room temperature. Repeat. Should give HRC 55.
Note 1: Do not stress relief (tempering) at or above 300 °C; it reduces corrosion resistance.
Pickling can hydrogen embrittle this alloy. If the scale formation cannot be avoided, either mechanically clean or use a 3-step chemical cleaning:
Initial pickle bulk of scale in hot, inhibited acid. Rinse.
Scale condition for 1 hour in hot alkaline, potassium permanganate
⇦ this on
eBay or
Amazon [affil links] . Pressure wash.
Final pickle in inhibited acid or 10:1 nitric:hydrofluoric acid, e.g., 25% nitric-2.5% hydrofluoric. Rinse.
Note 2: Check whether ARDROX® (Chemetall), TURCO® (Henkel)or Cee-Bee® (McGean-Rohco) descalers are available. Suitable for precision parts, e.g., jet engine components.
Note 3: Don't use a molten salt descaling bath, as the temperature promotes carbide formation (depletes Cr from the metal).
Passivation.
Letter 24346 mentions good results for 440C using QQ-P-35C (canceled) [link is to free spec at Defense Logistics Agency, dla.mil]C Type VIII solution: 30 minutes in 50 vol% nitric acid at 50 °C.
Heat treatment after passivation ordinarily is not necessary. If hydrogen pickup from pickling is suspected, a 175 °C bake-out should not affect hardness.
- Goleta, California

Rest in peace, Ken. Thank you for your hard work which the finishing world, and we at finishing.com, continue to benefit from.
Q. Hi, I'm having parts made of 440C passivated following
ASTM A967 -01 Citric 4, after being blasted with glass shot. They rust all the time after 10 minutes of cleaning in deionize water and Liquinox in an ultrasound bath.
What is wrong with the procedure? Could electropolishing do a better job than glass shot?
Or is it the passivation that needs to be revised?
Thanks
Product designer - Montreal, Canada
2007
Q. In addition to the question, our pieces need to be laser engraved, that is why we are not using nitric passivation.
Marc Thebo [returning]- Montreal, Canada
2007
A. Your sentence construction makes me wonder if the citric acid is after or before the glass bead.
What is the possibility that the glass bead and the cabinet are contaminated with iron/rust?
Proprietary citric acid works better than home brew. Electropolish works very well on 400 series, but it is another chemical process to maintain and keep up. Time for a cost benefit analysis.
- Navarre, Florida
2007
A. James is correct. There is no reason for the 440C to rust if it is hardened correctly and passivated correctly according to ASTM A967-01 Citric 4. This is done all the time with proprietary citric formulations with excellent results. When done correctly it will not remove the laser marks but will produce excellent corrosion resistance. What hardness are you running?
adv.
Contact us if you need help.
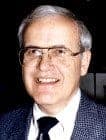

Lee Kremer
Stellar Solutions, Inc.

McHenry, Illinois
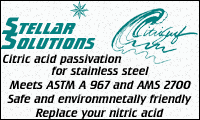
2007
Q. So as I am reading, is it safe to assume that once the 440C is heat treated [approx. 45 RcC] that regular Citrisurf passivation will work and no rusting will occur on 440C?
I have had rusting on 440C after blanking and on an "annealed" end of a heat treated part. [Both rust conditions occurred on Non- heat treated material.]
Thank you for your help,
Medical Devices - Middlefield, Ohio
2007
Passivation / Re-passivation of 440C
Q. I have a 440C part, 58-62 RC that has slight rust beginning to form. I need to remove this rust before the part can be assembled and used. These parts were passivated per AMS2700 method 1 type 2. How do you suggest I remove this surface rust? Will passivation be necessary after the rust is removed, if so, is there a higher risk of etching/flash attack? The ID of the part is finished to an Ra or 4 or better, I'm assuming that the first passivation would have been done after the ID was finished, but I'm not certain, could passivation affect the surface finish? Lastly, the clearance between this part and its mating component is .000200"-.000300", will passivating again have any impact on the dimension of the bore? I read in another thread on this site that cleaning the part for an extended period would reduce the risk of flash attack, can anyone recommend a process to prepare these parts for passivation?
Dean CampbellEngineer - Redmond, Washington USA
October 17, 2013
A. The high carbon stainless steel 440 will sooner or later rust again, unless you Electropolish it.
adv.
Electropolishing in Universal electrolyte will create the thickest possible anticorrosion layer.
No additional passivation is required.
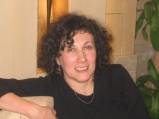
Anna Berkovich
Russamer Lab

Pittsburgh, Pennsylvania
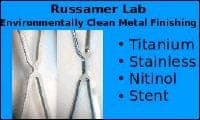
October 21, 2013
October 30, 2013
A. Dean,
First of all, understand that 440C is on the lower end of the scale for corrosion resistance among other stainless steels. With passivation it will be better off than without, but it will never stand up to a bad environment the way grades like 304 or 316 will.
The rust can be removed via any normal commercially available rust remover. I would indeed passivate again afterwards, since the rust is a sign that the environment overcame the passive layer that was there before. You ask if there is a higher risk of etching or flash attack, a higher risk compared to what? Once the rust is removed it's just a 440C part, same as it always was.
Nitric based passivation can change the surface finish (etching) if one is not careful, citric acid based passivation almost never does. Same answer concerning keeping the size tolerance, nitric has the potential to cause trouble, with citric it's more difficult to create a problem.
I'm not sure people really understand what flash attack means, I'm not totally sure I do either, but in general you're not going to have flash rusting if you keep your stuff dry. That's even true of carbon steel, but as far as stainless goes the only time I ever witnessed flash attack in my lab is once when I was running some variety of 400 series stainless and as I was moving parts down through the line I notice the part in the water rinse between the acid and the dryer was rusting. After that I started moving parts through the rinses and into the dryer more quickly.
adv.
Let us know if we can help.
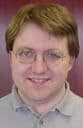
Ray Kremer
Stellar Solutions, Inc.

McHenry, Illinois
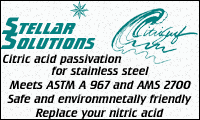
Q, A, or Comment on THIS thread -or- Start a NEW Thread