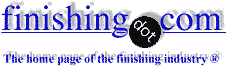
-----
Surface Treatment for 440C SST
Q. I am designing a flexible coupling for the motion system of a semiconductor wafer prober. The selected material, for its high yield strength and stability, is 440C stainless. The environment these parts will see is quite mild, typically controlled at room temperature and low humidity and no exposure to water, oils, or chemicals, but I would like to ensure a quality surface finish.
These parts see very rapid alternating loads so fatigue is a top priority and thus, surface quality is top priority. Can anyone recommend a finishing process that will prevent corrosion without stressing or embrittling the surface?
I have investigated passivation and have been referred to QQ-P-35C (canceled) [link is to free spec at Defense Logistics Agency, dla.mil] type 4 and have been assured (by my vendor) that it will have no negative effects on the surface of my parts. The parts will be lathe turned in the free machining state (440f), then heat treated to C condition before being passivated.
If anyone could help, I would be most grateful.
semiconductor equipment - San Jose, California
2003
A. QQ-P-35c (an obsolete specification) Type IV should work fine. If you want a safer way to give you better corrosion resistance, consider using one of the citric acid formulations with the proper pretreatment (needed for nitric also). We assume that the 440C is hardened to 60 Rockwell.
adv.
Let us know if we can help.
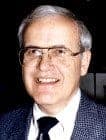

Lee Kremer
Stellar Solutions, Inc.

McHenry, Illinois
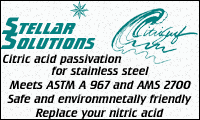
2003
A. Derek, 440F is the free machining grade of 440C: i.e., it is 440C with controlled amounts of manganese sulfide (think 'dirt') added to give better machinability. The machining chip will break when it hits one of these dirt particles, so the chips will be short and small, rather than long and stringy. If it is truly 440F that you machine, a heat treat will not give you 440C. You will still have the dirt, and that is a poor thing to have in your material if you want high fatigue resistance.
Along those same lines, I'd recommend that you rethink your choice of 440C. Remember that it's a bearing grade, so it has lots of carbides in the microstructure. These give great wear resistance, but suck in fatigue, both in lowering your overall stress to initiate a crack and in increasing the scatter of fatigue life that you'll get. If you HAVE to use 440C, consider using a grade with the carbides refined, like Latrobe's 440 N-DUR, or a P/M grade- I'm not sure offhand who makes those.
As an alternate, consider something like CarTech's Custom 465 PH grade of stainless steel. It is not a bearing grade, so it doesn't have the carbides that rob your fatigue strength, yet it will get into the low 50's HRC. Latrobe has other things in their arsenal, and Allvac has their 13-8 Super-Tough: there are a lot of good choices out there.
I agree with Lee Kremer, and will say we use Type VIII for 440C with good results. If you are making the part of stainless steel, you should passivate it. Period.
Good luck!

Lee Gearhart
metallurgist - E. Aurora, New York
2003
A. We have some experience on 440c, let me tell you that anti corrosion properties of material are maximum yield by doing the heat treatment properly i.e., either air cooled/inert vacuum cooling with nitrogen/ or by cooling in air up to certain temp and then cooling in water or oil). I don't have details right now but if you require can be found out. After heat treatment components can be polished with amalgam of chromium oxide, fine grade emery
⇦ on
eBay or
Amazon [affil links]
and oleic acid. But before polishing I would like to know your component drawing and may be advise you more appropriately.
Regards,
- New Delhi, India
2003
A. Passivation per QQ-P-35 will not enhance 440C surface finish. Try electropolish which removes .0003-.0005" per surface. However, to avoid hydrogen embrittlement you have to bake it out within 4 hours of electropolish for a minimum of 23 hours at 375 °F.
However, I had a bad experience with 440C where I had a highly stressed part fail. After micrograph exam I found out that the carbide was not evenly distributed which definitely contributed to the part failure.
Vascomax-350C is even stronger but is not a stainless steel, it is a maraging steel. Yield is 325 ksi, tensile ultimate is 335 ksi. Very hard to machine, grinding is better.
If your application does not require yield above 210 ksi try MP35N, a nickel alloy. Heat treat before machining. After that it is 260 ksi ultimate and great corrosion resistance, fatigue and wear. We use heavily in aerospace.
Good Luck
- Houston, Texas
2003
A. Electropolishing will not cause hydrogen embrittlement. Some electropolishers even claim the process removes pre-existing hydrogen. This must be true to some extent, given the active evolution of oxygen at the surface and the typical EP temperature of ~160 F.
With 440C, proper heat treatment using inert atmospheres is essential for a good microstructure and a corrosion resistant, shiny surface. Do not acid pickle; remove any scale by polishing as suggested by Mr. Singh. Passivate with either Type II or VI solutions or one of Stellar Solutions [a finishing.com supporting advertiser] citric acid formulations.
If you actually have 440F, all 440C precautions apply. Additionally, follow Carpenter Technologies' A-A-A passivation procedure [hot Alkaline, Acid (Type II passivate), hot Alkaline] and for good measure, dichromate soak per QQ-P-35C, paragraph 3.5. The first alkaline step prevents the 'frosting' commonly experienced with free machining alloys; the follow-up alkaline and dichromate steps delay the inevitable rusting.
- Goleta, California

Rest in peace, Ken. Thank you for your hard work which the finishing world, and we at finishing.com, continue to benefit from.
2003
Chemical Polishing 440c Stainless Steel
Q. Hello Everyone! My name is Helen. I am a chemical engineer at a Technology firm where we make electropolish, passivation and etching for Medical Industry.
We are having a problem Chemical Polishing a 440c Stainless Steel part to a mirror finish. How can we bring the luster out better? Any suggestions on the total polishing process will be greatly appreciated. Thanks!
- Israel
November 12, 2013
adv.
Helen,
Switching to Universal Electrolyte will solve the problems of better polishing. Moreover it will provide the optimal passivation layer for 400-series stainless steel. Contact me for more information.
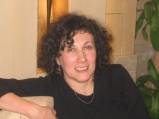
Anna Berkovich
Russamer Lab

Pittsburgh, Pennsylvania
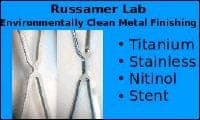
November 25, 2013
A. If the surface roughness is over 18RMS, you may want to do some mechanical finishing before you electropolish.
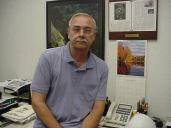
AF Kenton
retired business owner - Hatboro, Pennsylvania
December 5, 2013

this text gets replaced with bannerText
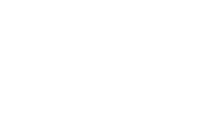
Q, A, or Comment on THIS thread -or- Start a NEW Thread