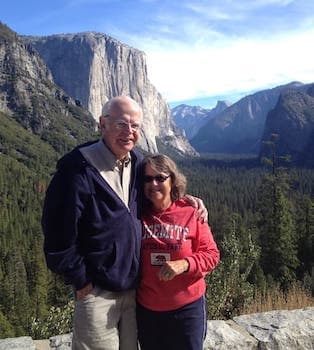
Curated with aloha by
Ted Mooney, P.E. RET
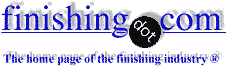
The authoritative public forum
for Metal Finishing 1989-2025
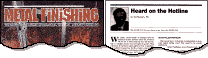
-----
Anti-galling coatings. Can plating solve our galling problem?

Q. I am with the University of Texas, Center for Electromechanics, and I was hoping that you could help me with some information. We have a problem with two shrink fitted parts (a hub onto a shaft) galling on us when we take them apart. We thought that a plating of some sort would help with this problem. The plating will need to be able to withstand 50 ksi compression, and the parts are made of AISI 4340 steel, HRC 46. We are also needing to have a friction coefficient of about 0.15 between the parts, and the plating must be able to withstand temperatures up to 700 °F. Is this possible, and do you have any general information on compression strengths and/or threshold galling stresses, operating temperatures, and friction coefficients of platings, or any other suggestions? Thank you very much.
Michael Lewis- University of Texas at Austin-Center for Electromechanics - Austin, Texas
1998
A. I do not have numbers, but adding electroless nickel to ONE of the two parts will virtually eliminate the galling you are experiencing. It has excellent lubricity, can stand the temp you mentioned, and is a very uniform coating that if put on by someone really good, you probably would not have to grind or hone after plate if the parts are properly sized to start (allowing for the plate).
James Watts- Navarre, Florida
A. Michael,
In the vacuum industry plating silver on threads, etc. is commonly used to prevent seizing and galling between metal parts. This might work for your application.
Donald M. MattoxSociety of Vacuum Coaters
Albuquerque, New Mexico
"Handbook of Physical Vapor Deposition (PVD) Processing" (2010) [on AbeBooks or eBay or Amazon affil links]
and "The Foundations of Vacuum Coating Technology" (2018) on AbeBooks or eBay or Amazon affil links]
by Robert K. Guffie
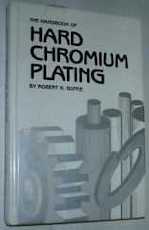
on AbeBooks
(rarely)
or eBay
(rarely)
or Amazon
(affil links)
A. In plating I think the resistance to compressive forces is generally referred to as hardness. Most plating is rated on Rockwell C (HRC) or Vickers hardness (HV)scales. However, you also have to look at adhesion when talking about resistance to compressive forces.
The coefficient of friction on a plated surface will depend largely on prior surface preparation. Generally, if you have a rough surface prior to plating -- you will have a rough surface after plating.
Silver plating gives you a surface that provides lubricative and anti-galling properties. It can withstand temperatures up to 1200 °F. However, it may not be adherent enough to withstand the compressive forces you write about.
Nodular thin dense chrome plating is also a good anti-galling/anti-spalling coating that can withstand temperatures above 700 °F. It is harder (~ 1000-1200 HV or >300 ksi) than silver plating and may suit your application. It is strongly adherent to basis metals such as 4340 and is extremely resistant to wear and abrasion.
You may also check out nickel plating.
In parting: A good test is better that a thousand opinions.
Greg Haatajahelicopters - Fort Worth, Texas
Q. I would like to know the Rockwell hardness or the Vickers hardness of electroplated nickel.
by William Safranek
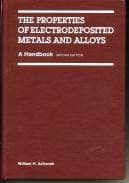
on eBay or
AbeBooks
or Amazon
(affil links)
JADCOM - Fremont, California
2000
A. Sorry, Chris, but there is no single value -- not even a narrow range. But Safranek says in "Properties of Electroplated Metals and Alloys": 110-250 kg/mm2 for dull nickel, and 463-622 kg/mm2 for bright nickel, while declining to offer Rockwell or Vickers numbers because "hardness measurements seem to be greatly dependent on the applied load and type of indentor".
His book has 70 pages of data on the properties of nickel electroplated under different conditions, and another 50 pages on the properties of electrodeposited nickel alloys and composites. If you need detailed data, it's a great resource.
Luck and regards,
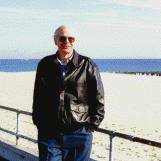
Ted Mooney, P.E.
Striving to live Aloha
finishing.com - Pine Beach, New Jersey
Multiple threads merged: please forgive chronology errors and repetition 🙂
Q. I AM LOOKING FOR A COATING TO USE ON A VARIETY OF THREADED STAINLESS STEEL PARTS TO PREVENT GALLING. THE PARTS ARE DISASSEMBLED/REASSEMBLED IN THE FIELD ON A REGULAR BASIS FOR REBUILDING AND CLEANING. CAN YOU SUGGEST A COATING OR PLATING THAT WE CAN HAVE APPLIED TO PREVENT THIS FROM HAPPENING?
MIKE RUFENACHT- MINNEAPOLIS, Minnesota
1999
A. Graphite-based PVD coatings might fit the bill.
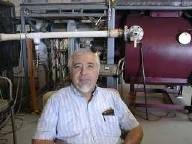
Jim Treglio - scwineryreview.com
PVD Consultant & Wine Lover
San Diego, California
by Fabienne Delaunois et al
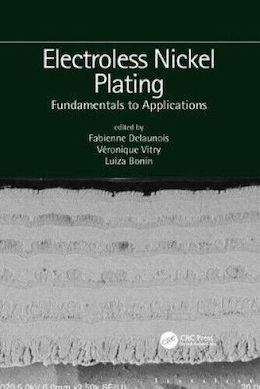
on eBay or
AbeBooks
or Amazon
(affil links)
A. One of your best options is Electroless Nickel. It prevents galling, you could also use EN with Teflon so that assembly/disassembly will be easier to perform.
Enrique Segovia- Monterrey, N.L.
A. Silver is the standard non-galling coating for the vacuum technology business. Silver coated bolts are standard items.
Donald M. MattoxSociety of Vacuum Coaters
Albuquerque, New Mexico
"Handbook of Physical Vapor Deposition (PVD) Processing" (2010) [on AbeBooks or eBay or Amazon affil links]
and "The Foundations of Vacuum Coating Technology" (2018) on AbeBooks or eBay or Amazon affil links]
A. I used to use a proprietary chromium plating where I worked previously. The coating is extremely hard, (about 70HRC / 1100HV), satin in appearance, and works wonders. In our experience it adhered and lasted much better than either Nickel or Silver. We used it for Nuclear applications mainly, where exfoliation of Nickel had been a problem.
Wayne Ward- England
A. There is an austenitic stainless steel called 'Gall Tough' and a competitive product called 'Nitronic 60'
Steve Cassidy- Hudson, Massachusetts
A. If silver plating is not used, there are lots of different dry film lubricants, which are affordable solutions, particularly the ones that come in a spray can and do not have to be baked. They are not as good as baked, but would work fine for a touch up.
James Watts- Navarre, Florida
A. Mike - Another anti-gall coating is manganese phosphate. It also holds an RP [rust preventative] oil very well for corrosion protection. The production process is similar to zinc phosphate. Ask your chemical vendor for info.
Dan Brewerchemical process supplier - Gurnee, Illinois
1999
A. We provide and train customers for anti-galling copper plating.
Major licensors uses this process for anti-galling reasons.
- Singapore
February 10, 2010
Ed. note: Gentle readers, this is a service for technical information and camaraderie. For a whole host of time-proven reasons ( huh? why?), we can't post suggestions of brands or sources (although we can post clearly labeled paid advertisements of course).
We edited out proprietary suggestions from several postings above, and had to decline to post some suggestions that offered only proprietary names without any generic info. Please try your best to answer technically and generically. Thanks!
Multiple threads merged: please forgive chronology errors and repetition 🙂
Finishing of threads, 17/4PH or 13% Cr parts
Q. Will I introduce a potential corrosion problem if I use silver to coat the threads of parts made of these materials? We have a problem with fragile threads when assembling or disassembling parts made of these materials, and I would welcome any advice regarding this problem.
Jan HabrekkeBTU AS - Trondheim, Norway
2005
A. Hi Jan. It is a commonplace to silver plate threads of stainless fasteners to minimize galling issues, although it is not the only potential solution to the problem. To know whether you might have a corrosion problem would require knowing the severity of exposure conditions plus the other materials of construction in electrical contact with the silver plated stainless fasteners though. Good luck.
Regards,
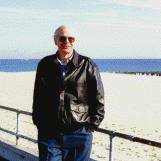
Ted Mooney, P.E.
Striving to live Aloha
finishing.com - Pine Beach, New Jersey
TDC = Thin Dense Chrome
A. Try TDC coating. We apply a coating that is used for anti gall applications on 17 4 and provides a good corrosion resistance.
Jed Chamberlain- England
A. One good anti-galling option is semi-permanent, self lubricating metallic PVD coatings. These work especially well on threaded stainless steels.
The most effective for stainless steel is silver-palladium -- if applied correctly.
Bill Haden
- Houston, Texas USA
January 25, 2025
Q, A, or Comment on THIS thread -or- Start a NEW Thread