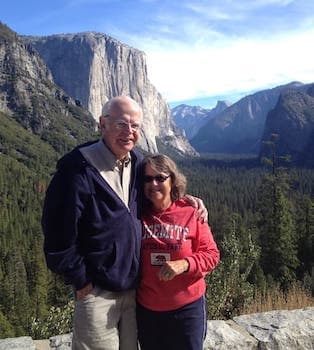
Curated with aloha by
Ted Mooney, P.E. RET
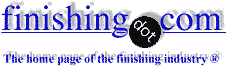
The authoritative public forum
for Metal Finishing 1989-2025
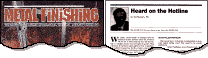
-----
Is salt spray testing appropriate for powder coatings?
Q. Is salt spray testing an effective, industry standard, means for process control for a powder coating system? How often should salt spray tests be performed to verify the process: continuous, periodic?
Tom Clark- Cleveland, Ohio
1999
A. Yes, salt spray testing is certainly effective and an industry standard, but I don't think I'd exactly call it a process control for two reasons: first, it gives only general indications & likelihoods rather than definitive answers; second, it's too slow for most process control feedback.
Regarding the first reservation, think of health screenings where doctors do a risk assessment for certain diseases. If your parents had heart disease, and you're overweight, and a smoker, and a type-A personality, etc., you're at high risk. If none of the risk factors apply, you're probably at low risk. But there is no guarantee either way that you'll get heart disease or you won't.
Similarly, salt spray hours don't correlate quantitatively with actual field performance; but if your salt spray resistance starts going downhill it is highly unlikely that the finish will do well in the field, and if your salt spray performance remains good it is unlikely that there is anything dramatically wrong with the finish in terms of corrosion resistance.
Besides being only a general indicator, salt spray testing as a process control is hindered by not offering very useful real-time feedback: it can take 240 hours to run the test, or 500 or 1000, or more. You can powder coat an awful lot of rejects in 1000 hours!
Periodic testing would seem to be adequate.
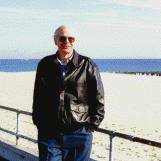
Ted Mooney, P.E.
Striving to live Aloha
finishing.com - Pine Beach, New Jersey
1999
1999
A. I have to agree with Ted. Our experience with salt spray is that it is not very predictive as a measurement tool for most companies because the salt atmosphere corrosion mechanism is not what most things are exposed to day in- day out. For example, while salt spray may be valid for a mfr. of outdoor beach furniture, it is very much not valid for mfrs. of office furniture. Office furniture, for the most part spends its life in an air conditioned and humidity controlled environment.
The other thing to realize is that a coating "system" includes the pretreatment and coating(s) used. There are plenty of excellent pretreatments that perform miserably in salt spray thanks to a weak coating or weak coating application. Likewise, there are terrible pretreatments that do great in salt spray thanks to a dynamite coating.
We have found that since the salt atmosphere corrosion mechanism is an aggressive one that salt spray is an effective "comparative" coating system evaluator. This means that it is a good way to compare changes in an existing coating system by varying the parameters, changing pretreatments, sealers, process sequence, coatings, coating thickness, etc. This works well when compared to the current system. It is important to remember,as well, that other things such as adhesion and impact resistance should be tested for each variation.
Where to begin is with a good strong program toward analysis of field corrosion and paint failures. This will give you actual data (aka real world data) that will tell you how long your parts are lasting out in their real environments. Only then can you truly relate to your customer's concerns. You cannot do that through salt spray, because this is only one point on a curve(more later). What comes to mind is a good customer relations program that rewards them for bringing failures to your attention, with replacement parts or whatever. Do this under the auspices of a true continuous improvement program aimed at letting your customers help you make the product that the buy better. This will build customer loyalty. It is cheaper to keep the ones you've got than to find new ones.
But I digress... After you have this real world data, you may be able to say with salt spray that you have discovered a system which is much improved over the old system and implement it, then follow field failures again to assess the actual improvement. You will do this multiple times over the lifetime of a product, change paints, change coating systems, change cleaning systems, pretreatment suppliers, etc. These are the additional points on the curve that you are looking for the curve that relates salt spray to real world performance.
Only companies that have studied this for many years and have a very good idea of what environment their parts are stored in have a correlation between the two. If your parts are used in multiple environments, (i.e. inside, outside, seaside, etc.) this becomes multiple curves, one for each environment.
Ted is right about the predictive aspect of salt spray, as well. Not many coating systems operators like to wait for over a month to hear if the parts that they painted last month are coming back. Look at some other predictive methods like coating thickness, pencil hardness, impact resistance, tape adhesion, etc... for quick checks to see if something is grossly wrong. Use salt spray to help you improve the coating system and for periodic quality evaluations.
One last thing about specifications... Do create a spec. One that is comprehensive and takes into account what your customers expect from the product, not how your engineers think the product should perform. Don't make the salt spray goal be some unachievable number, just because it is an industry standard test. Do the real world correlation work as time allows. Look to continuously improve your product through whatever means are at your disposal including salt spray. Consider alternate cyclical failure analysis methods, UV exposure, outdoor weathering, cyclical humidity-salt-UV module testing, etc if they more closely match the environment that your customers use your parts in. As always, Good Luck.


Craig Burkart
- Naperville, Illinois
Powder Coating Thickness Standards
Q. I am looking for a standard thickness of powder coating. Would you please advise me where to get this?
Thanks,
Andy NguyenBP Solar - Frederick, Maryland
2002
A. The normal industry wide thickness standard for powder usage is mils or 1/1000s. Each property type and specific manufacturer has their own criteria for topcoat thickness/s. Thus, a manufacturers product specification sheet is part of the answer to your question. The reason is that any adjustment made to the "manufacturers specified" thickness will affect the topcoat performance in impact resistance, flexibility, hardness, edge coverage, chip resistance, weathering, salt spray testing and others. This is a common area for problems to make there appearance. Painters need to attempt to apply the powder evenly and according to the product specification sheet to insure you meet the manufacturers specification/s. So if it calls for 2 to 5 mils it should read 0.002-0.005. This will give you the maximum benefit from that particular powder specification.
![]() Bob Utech Benson, Minnesota |
![]() Ed. note: Bob is the author of: "High Performance powder Coating" on eBay or AbeBooks or Amazon [affil links] |
A. Hi Andy. Bob is an expert in powder coating and I am not ... and fools rush in where angels fear to tread. So I could probably give you a general feel that about 2 mils is pretty average for thermoset powder coatings (the typical epoxy and polyester "paints"), but thermoplastic coatings like nylon and vinyl are probably usually something in the order of 5X as thick.
Regards,
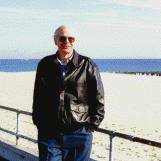
Ted Mooney, P.E.
Striving to live Aloha
finishing.com - Pine Beach, New Jersey
Salt Spray Hours vs life in years
Q. Dear Readers,
I have been asked the same question from various customers over the years. If anyone has information, please reply:
As per ASTM B117 (Salt Spray Test) results for 750 or 1000 hours means how many years of life of the coating in marine/corrosive environmental/atmosphere? How to calculate these figures? Is there any specifications available?
I also wondering to make answer for this question: Different environmental temperatures, weather conditions, Air contaminants, Different coating thicknesses, Different Coatings, Different Application techniques, etc. How to co-ordinate all together?
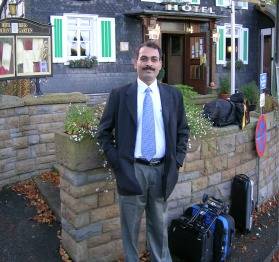
Kalyan Dhakane
Mumbai, India
2005
A. Hi, Kalyan. This site has also been asked the same question numerous times too, but the question is based on a basic misunderstanding of the purpose of salt spray testing. Salt spray testing is a QA measure; it is done to make sure that process control hasn't gone south with nobody noticing it, it doesn't predict real-world life. That is, if you have a well developed process, and it regularly withstands (say) 240 hours of salt spray, something has gone terribly wrong if it now fails in 24 or 96 hours.
Similarly, if you learn that zinc plating usuallys last 96 hours, or anodizing 192 hours, or powder coating 500 hours or electroless nickel 1000 hours, and yours doesn't, then something might be wrong with your process. But it is totally wrong to infer from those numbers that electroless nickel is more corrosion resistant than powder coating, which is more corrosion resistant than anodizing, which is more corrosion resistant than zinc plating -- because the salt spray rating is absolutely no indication that one coating will outlast the other in real environments!
For example, hot dip galvanizing can last 75-100 years with no maintenance (no other finish comes close), but it performs rather poorly in salt spray tests because its real-world endurance depends on the slow formation, over months and years, of a glassy, stable skin of corrosion product compounds like zinc carbonates which don't form in the salt spray chamber. Similarly people may try to sell new processes by salt spray testing it against nickel-chrome plating, for example, and claiming that it is "more corrosion resistant" ... whereas the truth is that properly plated nickel-chrome truck bumpers still shine after resisting the worst that the world can throw at them for decades, and it's unlikely that the "new" coating with good salt spray hours can even begin to compare in the real world.
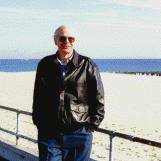
Ted Mooney, P.E.
Striving to live Aloha
finishing.com - Pine Beach, New Jersey
2005
Multiple threads merged: please forgive chronology errors and repetition 🙂
Salt spray life vs. powder coating thickness
Q. I want to know Salt spray life vs. Powder coating thickness
Pankaj AmbatkarDesigner - Pune, Maharastra, India
January 14, 2008
A. Hi, Pankaj
I don't think anyone can answer your question quite the way you've phrased it. But we shouldn't leave in place the implication that salt spray hours are proportional to coating thickness, as if corrosion sets in when the finish wears through, which is not the case. But letters 1618, 3010, and 45803 may give you the kind of information you are looking for. Good luck!
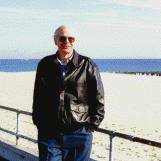
Ted Mooney, P.E.
Striving to live Aloha
finishing.com - Pine Beach, New Jersey
January 23, 2008
January 25, 2008
A. Pankaj,
A proper question would be "what salt spray results might I expect using (fill in the blank) pretreatment on (fill in the blank) substrate with a (fill in the blank) powder coating at the manufacturers recommended film thickness and cure schedule".
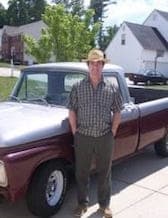
Sheldon Taylor
supply chain electronics
Wake Forest, North Carolina
Corrosion testing of powder coated components
Q. SIR,
WE ARE A LEADING COMPANY ENGAGED IN MANUFACTURING OFFICE STATIONARY ITEMS AND WE NEED STANDARDS FOR SALT SPRAY TEST FOR OUR POWDER COATED COMPONENTS WHICH ARE ALWAYS BEING USED IN INDOOR APPLICATIONS. WHICH CORROSION TEST IS APPLICABLE IN SALT SPRAY FOR THESE TYPE OF COMPONENTS? HOW MUCH THICKNESS IS REQUIRED FOR ABOVE SAID APPLICATION? AT PRESENT WE ARE DOING 60-70 MICRON COATING OF POWDER PAINT.
THANKS,
Employee - LUDHIANA,Punjab, INDIA
May 27, 2015
A. Rajesh,
Salt spray is a well-defined test method, the question you have to ask is how long of a salt spray test are you looking for?
No doubt it is a known quantity of how many hours of salt spray a 60-70 micron powder coat will survive on average, so you could base your requirements on that. This is an indoor office application, which tends to not be a corrosive environment, so you could base your requirements on that.
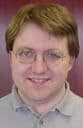
Ray Kremer
Stellar Solutions, Inc.

McHenry, Illinois
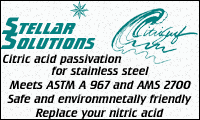
June 12, 2015
Q. Thanks for your reply. We are looking for 250 hours of neutral salt spray life on our components. How much thickness of powder coating do we require for this thickness. Is there any standard available for this. Kindly clear.
Thanks.
- Ludhiana,Punjab, India
June 13, 2015
A. Hi Rajesh. Salt spray hours are not proportional to powder coating thickness, as has been noted several times further up in the thread, because the powder coating is neither a sacrificial coating, nor does it get eroded away. Rather, the powder coating thickness should be as specified by the powder manufacturer, and is probably about 60-80 microns for polyester and epoxy powders for interior use.
In this application, proper pretreatment is probably what will chiefly determine your salt spray hours. Good luck.
Regards,
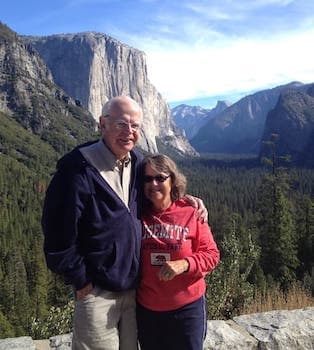
Ted Mooney, P.E. RET
Striving to live Aloha
finishing.com - Pine Beach, New Jersey
Q, A, or Comment on THIS thread -or- Start a NEW Thread