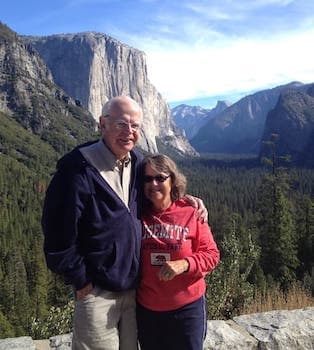
Curated with aloha by
Ted Mooney, P.E. RET
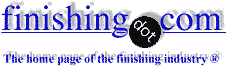
The authoritative public forum
for Metal Finishing 1989-2025
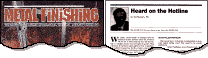
-----
Autophoretic coating adhesion issues
Q. Our Subcontract painter is finding adhesion problem using autophoretic paint on our brackets which are made from mild steel HR 3 pickled and oiled, the oil is minimal. Does anyone know whether any material grades are more suitable than others to this process?
Mark Vaughan- Stratford Upon Avon, U.K.
A. Hi Mark. I may be misunderstanding a bit, but "oil is minimal" isn't good enough. They need to be cleaned to waterbreak-free condition. Good luck.
Regards,
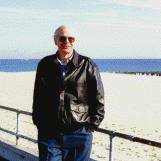
Ted Mooney, P.E.
Striving to live Aloha
finishing.com - Pine Beach, New Jersey
Q. We currently have an Autophoretic Coating process in our plant. The first 2 tanks are caustic (to remove oil, etc.); then the parts are rinsed, and dipped into the paint tank. The paint tank is experiencing high iron levels and therefore we are dumping 1000 liters per day into another tank and replenishing the paint tank. This is a very costly process, I would like to know if anyone else has experienced this problem? Henkel is suggesting a Gen 111 IEX Unit to remove cations -- however, I have heard this can cause further problems with the process.
I would appreciate anyone's thoughts on this.
Kind Regards,
autophoretic coating - Adelaide , South Australia, Australia
2003
A. An iron build-up in the paint bath is normal because this is how the autophoretic process works. Slow dissolution of iron changes the pH and ionic strength of the solution at the surface of the part, and these changes cause the paint emulsion to break and coat the part. Put another way, if no iron was being dissolved, the parts would not be coated. The only ways to control the iron build-up are by dumping part of the paint solution, or by an ion exchange process that selectively removes the iron. This IX process saves a lot of the expensive paint resin compared to the dumping method. As far as I know, the IX systems are only available from your supplier.
Lyle Kirmanconsultant - Cleveland Heights, Ohio
2003
Concise as well as informative, Lyle. Thanks!
Regards,
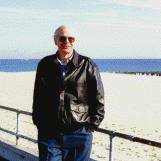
Ted Mooney, P.E.
Striving to live Aloha
finishing.com - Pine Beach, New Jersey
A. Dear Sir,
Regarding your request for removing iron from your ACC BATH, if you are using ACC 866 then I can recommend you the manual IX System which is a very simple way to remove the iron from your bath. You just use the iron filter like a work piece in your ACC866 then put it on the laundry; more information about manual IX filter at Henkel U.K.
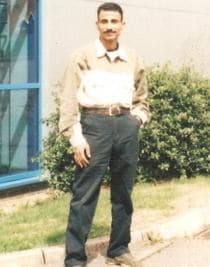
2006
A. One other tip - since the reaction rate between the coating solution and the steel substrate is controlled by both chemical and mechanical means (ferric fluoride and agitation) you might benefit from running the iron level lower and the agitation a bit higher. The reaction rate is higher with more iron in solution and the film formed with high iron and low agitation tends to be a bit softer, so you leave more iron behind with those conditions.
The IEX system was still pretty new back when I was at Parker Amchem, but It did work well, so the above comments are also accurate as well. In the long run, IEX is the way to go.
- Batavia, Illinois
May 12, 2011
Autophoretic 800 on a welded assembly
Q. We are a driveline manufacturing company looking to Autophoretic 800 coat a complete driveline assembly. The assembly contains two universal joints connected by a tube. The tube will be welded to yokes of the universal joints. Historically we had adhesion issues around the weld and heat affected zone with the Autophoretic 800 coating. Can anyone offer some assistance in how we could improve the adhesion issues? The weld is a MIG welding process.
John RameyDriveline Engineer - Pottsttown, Pennsylvania, USA
2007
A. In order to obtain adequate adhesion on welds, the oxide must be removed from the surface. This means either pickling in acid or mechanically descaling (sand blasting, wire wheel, shot peening, etc.).
Toby PadfieldAutomotive module supplier - Michigan
2007
Q. I'm technical support for a seating systems supplier Mexico. I worked with them on starting an Autophoretic line in 2006 and now they've contacted me to give support because Henkel recommended to install 3 new stages including pickling & and rinses after cleaners to improve the paint adhesion on some areas that are difficult for the adhesion of paint.
Alvarez JulioTechnical assessor - Cuidad juarez Mexico
June 2, 2017
Ed. note: This RFQ is outdated, but technical replies are welcome, and readers are encouraged to post their own RFQs. But no public commercial suggestions please ( huh? why?).
Q, A, or Comment on THIS thread -or- Start a NEW Thread