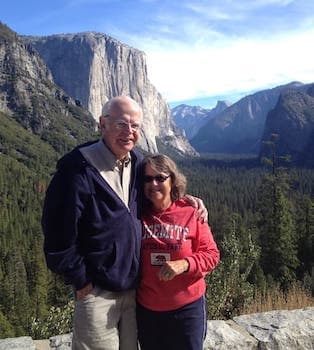
Curated with aloha by
Ted Mooney, P.E. RET
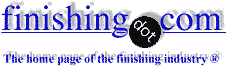
The authoritative public forum
for Metal Finishing 1989-2025
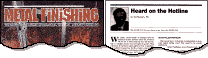
-----
Best material choice for small plating tanks?
I wish to construct a series of small plastic tanks (23 tanks to be exact) for an acid copper and acid tin sulphate plating line. Size will be 8" x 14" and 12" deep of solution (6 gal). There will be an outer lip on top for added support. Max. temp is 40°C (104°F). Because this is new to me I afraid of buying the wrong materials and wasting my time and money only to find I should of done it different. The choices of material are PVC or polypropylene, with PVC being preferable due to ease of hot air welding. What sheet thickness should I chose ? 1/8", 3/16" or 1/4" ? I can weld in a horizontal "belly band" if the sides look like they are bulging out. Tanks will rest on a flat bottom.
Adam Seychellin-house plating - Melbourne, VIC, Australia
2003
First of two simultaneous responses -- 2003
Hi Adam !
Well, you mentioned PP and PVC but didn't mention Pe !
May I suggest you go to a rotationally moulded Pe tank. Surely in Melbourne you must have someone doing this ... in the general Vancouver area, we have at least two. You may have to compromise slightly on the tanks as they probably won't have that exact size, alternatively you could get them to make a special size just for you which might be viable for the quantity you want.
Pe ... normally it's a medium density Polyethylene that they use, can be moulded to have wall thicknesses of up to 1/2" ... for your size, 3/16" should suffice for normal usage but I'd opt for l1/4". Temperature wise they'll tell you its OK to 150 °F
If you get some slight distortion due to the heat, weld on a 1/2" thick x 1" wide reinforcer at 1/3 of the tank height, ie. at 4" from the bottom. But like PP, Pe welding is best done using dry air ... and scrape clean the to-be- welded area first of all.
You might find further data in the archives ... have a gander at 8925, 3254, 6696, 12182, 7132 and 8169 ... these should give you some ideas, I hope.
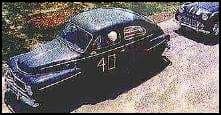
Freeman Newton [deceased]
(It is our sad duty to advise that Freeman passed away
April 21, 2012. R.I.P. old friend).
Second of two simultaneous responses -- 2003
Buy molded (seamless) plastic tanks for greater reliability. Standard sizes (in the US) include 8x18x12" (7 gal) and 12x15x12" (9 gal), plus lip. Material can be natural polypropylene (3/16" thick), medium density polyethylene (1/4€) or cross-linked polyethylene (5/32"). A girth support rib is not needed. You may be able to get a sizable discount for this quantity.
Ken Vlach [deceased]- Goleta, California

Rest in peace, Ken. Thank you for your hard work which the finishing world, and we at finishing.com, continue to benefit from.
2003
Hi again Adam,
Re Ken's reply, yes, you wouldn't need a reinforcer if you used PP or, I think, cross-linked Pe.
However, you'd probably pay twice as much for PP and 50% more for cross-linked, which you cannot weld to at all! Also PP has a very critical moulding temperature and most mfgs don't like it !
On checking 'true' figures rather than manufacturer's figures (which maybe right but that depends on what test they used) ... the ASTM D648 test shows a max. temperature for medium density Polyethylene @ 131 °F @ 66 psi but 150 for cross linked. ... but I recall once seeing a data sheet showing 170 °F for m.d.Pe !
In short, may I suggest you stay with the normal Pe that rotational moulders use ... you may never ever have to weld on a reinforcer ... but then, who knows, maybe 'to-morrow' you'll want to use a higher temperature.
I hope that this further data is of some help to you.
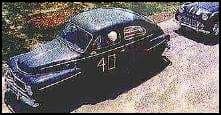
Freeman Newton [deceased]
(It is our sad duty to advise that Freeman passed away
April 21, 2012. R.I.P. old friend).
Thanks Freeman and Ken. I should of mentioned that many of the 23 tanks need to be made from a large tank partitioned off into many smaller tanks. This is the reason for going fabricated tanks and because PE doesn't doesn't seem to be as popular for manual welding as PP or PVC I didn't mention it. For example, one tank will have six partitions equally spaced at 3" width and have a 16" length bottom x 12" high. The partitions will add strength to the sides so I'm hopping 3/16" PVC will suffice. Do I have to be careful with plastics becoming buckled over a period of time which are under stress ? I mean 6 gal tank made from 1/8" PVC plastic might look like it is surviving to begin with, but I'm not sure how it will hold out after a year. I've seen 14"x14" tank lids made from 1/8" PVC that had sagged slightly in the middle over time and that's only under its own weight.
Adam SeychellPCB - Melbourne, Australia
2003
If the cost is not too high for you, an ideal material for small custom tanks like this is polished white PVC. It is the most attractive material a tank can be made of, you don't have the flammability problems of polypropylene, and as you mentioned it welds well. It is limited in use because of its 140 deg F max temperature, but if your max temp is 104, it sounds perfect.
Although it is possible to construct tanks of 1/8" material and even thinner, much as is done in the fabrication of exhaust hoods, I don't know any manufacturers who are comfortable using a sheet thickness less than 1/4" on custom tanks. These are small tanks and I would have them built with a rim band but no belly bands.
If the partitions are for rinses, they are not a problem and thinner material could be used for the partitions. But if they separate process solutions from each other, be forewarned that you may find it difficult or impossible to get the welding gun into narrow gaps between partitions, so you may be relying on one-sided welds. There are many highly experienced and well equipped plastic tank fabricators available (several advertise here), and it may be better to buy the tanks than to try to make them yourself. Life is easier when you have the forming equipment and fusion butt welding equipment, and you've seen the problem a thousand times before.
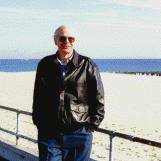
Ted Mooney, P.E.
Striving to live Aloha
finishing.com - Pine Beach, New Jersey
2003
Adam,
What Ted said about the difficulty of welding in narrow spaces is right on! Also, he mentioned min. 1/4" PVC ... and as a long term fabricator (PVC being my favourite plastic) I wouldn't use less ... and for the partitions so terribly narrow, I'd have opted for 3/8" !
No ... Pe is no more difficult to weld than PP ... both are so-called Polyolefins, both burn very slightly but whereas PP is more rigid and stronger, Pe is superb in impact. Don't try it ... go and buy your tanks ... and remember that these moulded Pe tanks have nice radiused bottoms and corners which you won't easily do at all if you make your own from PVC !
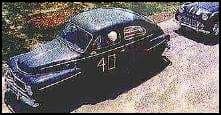
Freeman Newton [deceased]
(It is our sad duty to advise that Freeman passed away
April 21, 2012. R.I.P. old friend).
2003
Q, A, or Comment on THIS thread -or- Start a NEW Thread