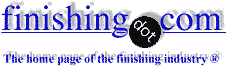
-----
Cooling system for a nitric/hydrofluoric acid bath
What metals, if any, can withstand immersion in a 12.5% HF, 7.5% nitric acid bath used for chemical milling of titanium? The plastic tubing coil does not allow enough heat transfer to keep the bath cool. Are there other options such as high thermal conductivity plastic tubing? Trying to avoid installing a stainless steel shell around the plastic tank to form a water jacket.
Cheers,
aerospace forger - Cheshire, Connecticut
2003
Practically speaking, there is none. That is a nasty solution. There are ways to go. One is to use thinner plastic tubing. Less thickness = better heat transfer.
Drawback is it is not as robust to physical abuse. The next way is to use more coils.
Drawback is cost and tank space lost. Third is to use a chiller or using one at a lower temperature. Think about polypropylene glycol rather than regular ethylene glycol.
There is no waste treatment required for a spill.
It is used as a preservative in some food. Last, you may be able to increase the flow rate and get a minor improvement in cooling, but not much unless your flow is really slow now.
- Navarre, Florida
2003
2003
Hi Ian,
My first thought was WHY doesn't he use a larger cooling coil ?
... available in PVDF (my preference) and a Teflon type.
Then I thought, ah, let's look at this from an entirely different viewpoint. Why not perhaps continue using your coil BUT then hit the hottish fumes with an eliminator BEFORE your scrubber.... the modus operandi being that you'd have to use a pump (CPVC) to generate around 10 psi ... and spray continuously the 'hot' liquid into the eliminator.
Materials of construction? PVC ... max. operating temperature 140 °C ... solid cone spray jets of PVDF ... capacity ... approx. l gal per 1000 cfm.
What actually HAPPENS is that the returned liquid is much cooler. At one trade show in the USA I had an eliminator (blade type) set-up being constantly sprayed but could NOT get any cold water ... so had to use hot water ... but lo and behold, the emerging water was C O O L ! In other words the heat transfer worked extremely well.
This design was also successfully used for chrome .... see the archives # 20279. Food for thought, anyhow.
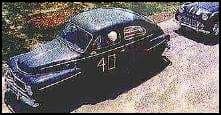
Freeman Newton [deceased]
(It is our sad duty to advise that Freeman passed away
April 21, 2012. R.I.P. old friend).
Dear Ian,
Another option for you would be to utilize a shell and tube or plate and frame heat exchanger to increase the thermal transfer. This would prevent the need to take up valuable tank space. These types of heat exchangers come in all shapes and sizes with coatings to suit the application's needs. Best of Luck.
Kansas City, Missouri
2003
Ian,
Before someone shoots me down in flames, that figure in the 3rd para of 140 degr. C applies to PVDF, certainly NOT to PVC which maxes out at 140 degr. F !
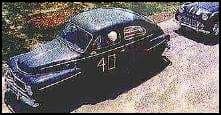
Freeman Newton [deceased]
(It is our sad duty to advise that Freeman passed away
April 21, 2012. R.I.P. old friend).
2003
Gentlemen,
Thanks for the responses. The existing all-plastic tank setup does not perform (cooling-wise) as well as the old stainless shell/PVC liner/water jacket model. We still have one of those in use as a passivation tank, but the shell is shot. We're planning on switching the tanks and installing a new stainless shell. The old shell has supports welded inside to support the plastic liner walls and to create the water jacket cavity that has one inlet and one outlet, both at the top. I intend to improve on the heat transfer by placing the inlet at the bottom, the outlet at the top, and using the I-beam supports to spiral the flow around the liner. Can't wait to find out how well it performs...
aerospace forger - Cheshire, Connecticut
2003
2003
Ian,
Excuse me for 'sticking my oar in' but you say you'll be using a PVC liner inside a s.s. tank. I assume you are talking about a rigid uPVC liner.
Back in Ye Olden Days we did this ... not always successfully because of the tank size (sometimes quite large!) and initially because one has to make an allowance for the different expansion rates.
So if you tank is X feet long and the max.temperature is Y degrees F, then the PVC tank should be LESS in width and length ... ie. Y x
3.5 x 10 to the minus 5 x 'X' ... . ... and to play ultra safe, DON'T fill up the PVC tank with cold water! Use 'Y' temperature.
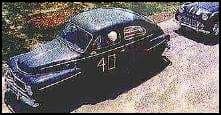
Freeman Newton [deceased]
(It is our sad duty to advise that Freeman passed away
April 21, 2012. R.I.P. old friend).
Ian,
There are plastic heat exchangers in PVDF, PE-RT and PP that can be offered in the space saving custom configurations. This may be too late in your case but for the future..
In a nutshell, there are "plastic heat exchangers" available today, that utilize thin wall design and minimize the negative impact of the isolating effect of plastic materials on the overall heat transfer coefficient. However, another important factor effecting the overall heat transfer coefficient is related to the thermal/hydraulic design of such exchanger; for example, a cooling medium with too low velocity will be less effective in overall heat transfer rate than the exchanger properly sized and designed for optimal performance.
For cooling applications PE-RT is rated for 180 F and offers 30% better heat transfer coefficients in comparison to PVDF.
I would be very interested in hearing what heat exchangers you used in the past (surface area and within what approximate volume in your tank) and why they were not effective. Best of luck,
Tustin, California
2003
Hi Kris,
You mention both PE-RT and PP: ... oh dear, for this application I'd sure stay away from any PE ESPECIALLY if it's thin and ABSOLUTELY if there is, as with the PVDF heat exchangers I've used, any welding to be done.
PE and PP don't love nitrics. However, PE-RT being such a common material, it's probably FAR less expensive than PVDF which, incidentally, excels in strong acids. So I'd suggest that it could be used FOR A SHORT TIME ... unless it is welded or fused at all.
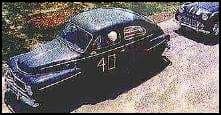
Freeman Newton [deceased]
(It is our sad duty to advise that Freeman passed away
April 21, 2012. R.I.P. old friend).
2003
Freeman,
My suggestion about PP and PE was general in nature. We don't know the specifics (temperatures) involved in Ian's application, so obviously there may be tradeoffs necessary. I am double checking the suitability of PE or PP for 7.5%, but you are correct that for higher concentrations PE and PP should not be used.
You sound like you had some negative experiences with plastic exchangers. I would be very interested to hear from you.
Best Regards,
Tustin, California
2003
Q, A, or Comment on THIS thread -or- Start a NEW Thread