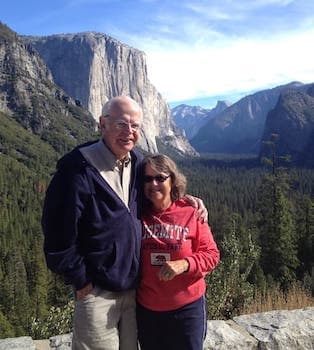
Curated with aloha by
Ted Mooney, P.E. RET
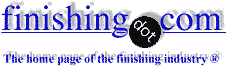
The authoritative public forum
for Metal Finishing 1989-2025
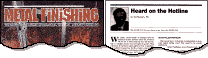
-----
Gold plating over Nickel on PCBs for wire bonding
1996
Q. Hello,
My name is Don White and my question is concerning gold plating of printed circuit boards. We wish to have a board plated with nickel then gold. I have specs/notes for gold fingers, but have never done a 'gold body' board. I believe the gold can be electroless and much thinner than the hard gold required for fingers. What thickness and hardness would the gold be for this application be and how would it be specified? Please excuse my lack of knowledge in placing the question to you. I hope this is enough information for an answer.
Thanks in advance,
Donald Whiteby Reid & Goldie
-- hard to find & expensive; if you see a copy cheap, act fast!
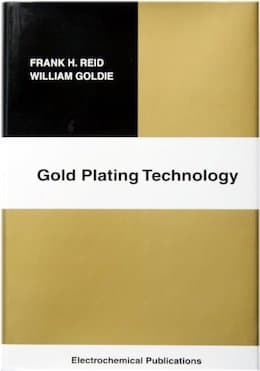
on eBay or
AbeBooks
or Amazon
(affil links)
A. The term used a couple of years ago when I worked in a board shop was "deep gold". The meaning should be obvious: normally you only plate the tips (at the edge of the board, achieved by careful trimming).
With deep gold the whole board is immersed into the plating solution and plated just as you would plate the copper, tin, or tin-lead. The big difference is that the photoresist has to be much more resistant because of harsher chemistry.
I don't remember the specified thicknesses, but I think they were the same as on tips, e.g., 50-100 nickel with minimum 20 gold?
Hope this helps.
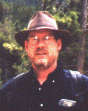
Bill Vins
microwave & cable assemblies - Mesa (what a place-a), Arizona
1996
A. Don, it really depends a lot on the reason for the gold finish on the board. If it is just as a solderability preservative, then a relatively thin pure gold finish will normally work. Most in the industry prefer other finishes since gold will tend to reduce the reliability of solder joints...immersion tin, Benzotriazine, or solder plate/fuse are logical alternatives if solderability preservation is the objective.
If on the other hand the application calls for wire bonding, then relatively thick pure gold is required...normally at least 20 µin and more like 40 µin. Most of the time, due to the high cost of gold, masking is used for such an application to put the gold only in those regions that require wire bonding.
Definitely do not use hard gold if wire bonding or solderability are required ... you will have serious problems. Use only pure gold (i.e., 99.9% pure) for these applications.
Hope this helps.
Ted Adlam (from not quite so sunny but very humid Singapore)
Ted Adlam- Singapore
1996
Don,
Be careful about selecting electroless gold on you PCB's. Unless your plater & chemist are VERY familiar with the process and have A LOT of experience prepping the board, the E'less Au will end up growing laterally along the surface of the board instead of up from the deposit and your entire board will end up covered with gold. Although all E'less Gold suppliers will guarantee their Gold will build up 150+ microinches quickly, none of them will guarantee that the lateral growth will not occur. And it is thermodynamically the more favorable reaction by several orders of magnitude unless you know how to shut it down. Maybe an E'less Au techie out there will chime in with the answer to this pbm.
Good Luck
Dave Kinghorn, in neither hot nor humid VERY sunny Sunnyvale, CA
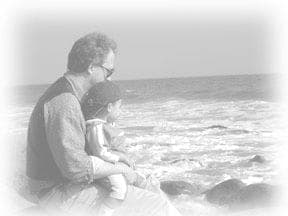
Dave Kinghorn
Chemical Engineer
SUNNYvale, California
1996
Wirebonding to a copper plate
Q. I am trying to connect wirebond to the copper plate; however, since wirebond won't attach to the copper plate, I plan to attach gold ribbon or gold tab to the copper plate. Then wirebonding will be performed on top of the gold ribbon or gold tab. The application is for an X-band amplifier design and I am trying to ground the source of the device to the copper plate.
My question: Is this the best way to do this? Thank you.
Sang LeeUCLA - Los Angeles, California
1999
? What is the material that you are trying to bond with? Have you tried to burnish the copper surface? Can you attach a molytab with some kind of conductive epoxy then try to bond to the molytab?
Mitchell Jackson1999
Minimum Gold Plating Thickness to prevent Nickel Oxide forming below?
Q. What must the minimum thickness of gold plating be over a Nickel layer(nominal thickness 200 you inches)to prevent Nickel oxide from forming beneath the gold?
Greg YadacusU.S. Army - Huntsville, Alabama
2003
A. Greg, This is a difficult question to answer. Much depends upon the surface roughness of the nickel as well as the substrate. It also depends upon the porosity of the gold. My experience comes from gold wire bonding to gold plating. In that case we found that 30 microinches was needed to eliminate any nickel oxide forming on the surface of the gold. We also observed that pulse plated gold was less porous than DC plated gold.
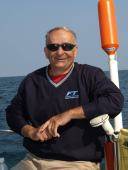
Pat Mentone
St Paul, Minnesota
2003
Multiple threads merged: please forgive chronology errors and repetition 🙂
Q. We require gold plating on PCBs that are suitable for wire bonding, at the present moment, we specify gold per MIL-G-45204 [link is to free spec spec at Defense Logistics Agency, dla.mil] Type III, Grade A, Class 1, 50 to 100 microinch over Nickel Plate per FED-QQN-290 (replaced by AMSQQN290) , 50-100 microinch thick. Some plating houses tell me that it is not possible for 1:1 ratio of such plating, but others have done it before. Is there any truth in this? Is it due to equipment or process inadequacies? If it is not possible, what are the reasons?
Sam Tan- Singapore
2003
![]() |
A. It's due to equipment & process. Most plating baths comprised of just a heated tub with an anode & cathode dropped in can be expected to plate out a thickness distribution of ± 50% of mean within ±3 standard deviations(~99.7% yield). Most Nickel callouts are 100-400 microinches. The plater targets a mean value of 250 microinches. ± 50% means all thickness tests anywhere on the part will be between 125 - 375, well inside the 100-400 spec even on drifty days. Now let's look at your 50 - 100 callout: Plater targets 75, ± 50% means the thickness will be between 38 - 112, way out of spec. To do better, the parts must be run on substantially upgraded equipment which yields a better process, but at a substantially higher per board cost. ![]() Dave Kinghorn Chemical Engineer SUNNYvale, California 2003 A. Of course you can plate Au over Ni in a 1:1 ratio, but the real question is why? Do you really need that Au thickness for wire bonding? Also, the usual reason for the Ni is to act as a barrier coat to prevent a Cu/Au solid solution. ![]() James Totter, CEF - Tallahassee, Florida 2003 |
A. Pure gold (0.9999 which is what you need for wire bonding) can be plated at any thickness including 0.000 005 up thru 0.5 inch over ANY thickness of any kind of nickel (but the nickel must be fully "activated" for the gold to bond). Any statement to the contrary is not technically correct.
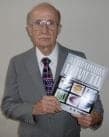
Robert H Probert
Robert H Probert Technical Services

Garner, North Carolina
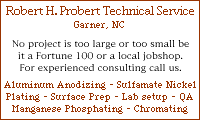
2003
A. Hello Fellow Tank Jockeys:
This is a classic example of the difference between accuracy and precision. They are not the same thing. While it is factually accurate to state that "ANY thickness" of Gold can be plated over "any" thickness of Nickel, it is also accurate to state that you will plate out a "distribution" of thicknesses all over your part, and the grand average of all these thicknesses is your target mean...the aforementioned "ANY thickness" value.
A trained plater can target this mean value, say 75 microinches, quite "accurately." However when the very same trained plater measures this very same electroplate in, say, 100 different locations and plots a histogram of this data, a "distribution" of thicknesses will be observed. The "wideness" of this distribution is known as the "precision," and is characterized by a mathematical term known as the "standard deviation," or "variance."
Looking again at our 50-100 microinch callout example, the 75 microinch target mean, the grand average of all measurements, the "ANY thickness" value, can be hit exactly with little effort. Now look at the individual measurements. About 90-95 percent of them will be between 50 and 100 with most being between 60 - 90. 5-10 percent will be either high or low. The part fails, yet the "ANY thickness" value was hit perfectly. Why? Precision.
Most "typical" plating baths being comprised of a warmed bucket with anodes over the sides have a precision of ±50% of mean within ± 3 standard deviations. Now do the same experiment with the 100-400 callout. Plater targets 250 and hits it exactly. Plater takes 100 measurements and 100 are within the 100-400 callout. Same tank, the precision is the same, yet the part now passes. Why? The callout is now wide enough to fully envelope the plating processes' precision. And that's the difference between precision and accuracy, and also illustrates how just calling out a thickness is a dangerous way to specify and electroplate.
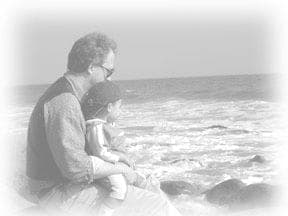
Dave Kinghorn
Chemical Engineer
SUNNYvale, California
2003
Minimum gold plating thickness for Al wire bonding
Q. We have an internal debate going on regarding how much Gold to deposit on PCB pads for Al wire bonding. I have heard everything from .01 µm to 8 µm for this application is there an industry standard or recommended thickness. Will the thickness have a meaningful effect on Pull tests?
Steve Cappellaelectronics mfgr - Bedford, Massachusetts
2004
Why doesn't hard gold plating work with large aluminium wire bonds?
August 2, 2011Q. Dear all,
I already read some very interesting letters on this forum about wire bondable surfaces, but none of them explained very accurately what my boss is asking for :)
We use in our (automotive) product (used in the engine compartment) a PCB that we need to connect to lead frames. The lead frames base material is phosphor bronze.
There are currently conflicts within our company to know what the best plating is for our application. We have two alternatives:
1) nickel undercoat (about 2 µm) + soft gold strike (about 0,1 µm) + soft gold finish (about 0,2 µm)
2) nickel undercoat (about µm) + soft gold strike (about 0,1 µm) + hard gold finish (about 0,25 µm)
I understand that hard gold IS NOT a good solution for bonding large aluminium wires and I understand that it is now the industry standard, but process engineers and purchasing do see some cost advantages. On the other side, It seems that wire bonding Al wires on hard gold is under tight conditions possible... But I didn't find any advice about what are these conditions. And in any case, I didn't find any scientific evidence, argumentation, case studies or theory why bonding on hard gold should not /cannot work with high reliability.
So, I have to bring some objective and technical arguments why we may lose many millions by using hard gold instead of soft gold! Can you please help me to understand what happens during wire bonding process on hard and soft gold?
R&D Engineer - Stuttgart, Germany
A. Bruno,
The reason PURE, Soft gold is better for wire bonding is because hard gold obviously has hardening agents known as alloys or brighteners. If the alloy contains nickel, cobalt, silver there will be additional intermetallic formations at the interface after bonding that will shorten the shelf life of the part, and many times fail. When I worked for a major precious metal supplier pure, soft gold was always recommended for wire bonding.
Good Luck.
- Mesa, Arizona
September 14, 2011
September 23, 2011
Hi Mark,
Thank you very much for your answer. It's now clear to me. Meanwhile I bought the book "Wire Bonding in Microelectronics". If I understand well, the hardening agents work like impurities in the gold coating, leading to the "Horsting effect", namely intermetallics that precipitates in voids after some temperature change. Is that right?
Is there anywhere some case of studies, showing bad experience of hard gold?
Regards,
- Stuttgart, Germany
Gold wire bonding failure on gold plating over nickel electrolytic plating
Q. Hi I am working as an engineer in plating process. I want some guidelines for improving the gold wirebonding on gold plating surface. We have plated some samples of 50 micro inch electrolytic gold plating on 180 micro inch nickel over copper base material,
i.e.: copper ==> nickel ==> gold strike ==> gold plating,
the result of gold wire bonding on gold surface failed using 1.5 mil gold wire,
Additional info:
contamination of gold bath - iron (60 ppm), copper <1 ppm, purity of gold is 99.9%
Anybody can advise how to improve the gold and nickel adhesion? What are the possibilities causing wire bonding failure?
- Singapore
July 24, 2015
A. Hi Sangeetha,
Whilst wire bond failure may not necessary due to plating deposit but also wire bonding parameter setting, it seems your soft gold bath iron content is too high. Normally should be less than 25 ppm. Gold deposit purity should be at or above 99.95% by wt. Alternatively,you may reduce gold thickness by plate a thin layer of Pd over Ni follow by Au.
Regards,
David
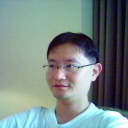
David Shiu
- Singapore
July 28, 2015
----
Ed. note: Readers may also be interested in letter 580, "Wedgebonding problems with nickel-gold plating".
Q, A, or Comment on THIS thread -or- Start a NEW Thread