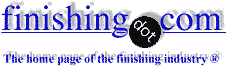
-----
Wedgebonding problems with nickel - gold plating
Q. We are electroplating lead frames for electronics. We mostly plate Au (0.4µ, approx. 15 mils) direct onto NiFe frames and never faced any problem with wirebonding.
One of the other finishes is ordinary Nickel plate (sulphamate) + Gold (pure) which we have been plating in the past and are starting up again now.
For a new customer this finish gives wedgebonding problems. The gold-electrolyte is a neutral, additive free type. We're absolutely sure there is no copper-, nickel-, iron- or cobalt contamination or an organic contamination present in the electrolyte.
We use PR-current on both the Nickel and the Gold. Variation in the layer thickness from 15 mils to 60 mils gives no improvements. We investigated the influence of fine-grained Nickel and gold versus course grained but did not succeed. Products of a colleague are good. Sometimes the results of our product are also good, next time they're bad. Does anyone have any suggestion in how to improve?
I'm especially interested in general guidelines about what plating parameters will theoretically improve wedgebonding further or literature references.
Thanking in advance for any comments!
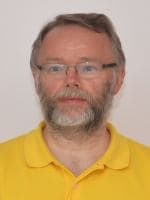
Harry van der Zanden
consultant - Tilburg, Netherlands
1996
A. Dear Mr. van der Zanden
"Sometimes the results of our product are also good, next time they're bad" indicates that even with the success you enjoy now, a review of your process instructions is in order. You might have the right combination, but without good process control, you don't always nail it.
You mention you just started this job again, are the results operator dependent?
Do you have written instructions on PR, current density, bath concentrations, pH? Are the instructions understood and followed? Is the PR at the correct settings, Has anyone calculated the current density on a rack lately? Is the equipment is good condition?
p.s. what is 'wedgebonding'?
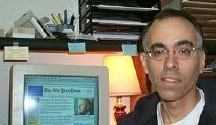

Tom Pullizzi
Falls Township, Pennsylvania
A. You say you are using PR (periodic reverse?). Why?
If you are trying for leveling, you may be passivating nickel, and unless your gold is a high cyanide alkaline type, the gold is probably not redissolving, therefore not leveling.
I would suggest keeping the following information, at minimum, if running reel-to-reel:
(a) line speed, current in each electrolytic bath, forward and reverse cycle times, surface area of each part run,
(b) chemical composition in each bath, at minimum pH and temperature
If running rack change (a) to time and current per rack, also forward and reverse cycle times.
There is software available that will help you to determine and track cycles and settings as well as chemical analyses.
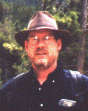
Bill Vins
microwave & cable assemblies - Mesa (what a place-a), Arizona
1996
A. Harry,
Are you plating Reel-to-reel or plating strips on racks? In any case, 15 microinches Au onto A42 should be sufficient. If it can be demonstrated that it is not a process control issue on your end, you may want to check out your customer's QC procedures. Are the frames failing on the line or in incoming QC? In many cases I have found unreasonable QC tests failing parts that are perfectly functional, because the QC test is actually designed for different types of parts, but applied in a blanket fashion. Maybe you can scan a photo of a failure and this website can let us see the pbm you face?
Regards,
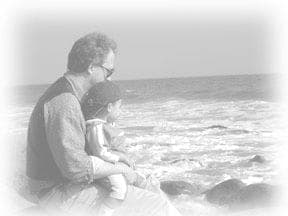
Dave Kinghorn
Chemical Engineer
SUNNYvale, California
1996
1996
Hello colleagues,
Thank you all for your comments on letter 580; let's continue this discussion.
I have to say that this makes the WWW very useful to me. I don't expect anyone solving my special problem fully, but the discussion makes it already possible to find possible ways to solve.
As long as it is possible, I would like to answer everyone personally.
Starting with Tom Pullizzi:
Let's further explain you the situation:
We started with a trial run of 20 mtr. This one was rejected.
Then we continued with a new sample run, after full analyses of our gold-electrolyte and taking good notice of things possibly wrong, and excluding these things as much as possible.
E.g., we measured Cu, Ni & Fe-contamination level in the gold electrolyte the second time, we checked and calibrated rectifiers & temperature controls and we just continued as we thought everything seems to be O.K.
With the same line parameters we made the second sample run.
This sample run was approved.
So we started with a somewhat longer sample run; this one was bad again, while to our opinion, as far as we could analyze and see, we reproduced the second sample-run.
After this we started several samples (fine-grained nickel with grain-refiner; fine-grained gold, but also here the results were sometimes bad, sometimes good and reproducing the good samples seemed to be impossible.)
The results are not operator dependent, as all samples were made by the same operator, together with myself to be absolutely sure that no occasional mistakes were made.
Anyway, your suggestion helped my in reminding me of the fact that I have to extend for the next sample run our checklist with data to be checked before we start up any sample run again.
"Wedgebonding means that they only make wedges; normally a wirebond is made on a chip surface, starting with a ball (This ball is caused by a hydrogen melt through of the gold thread) and then the wirebond nailhead goes to a next place where the bond is made and the nail head is cutting through the wire after the bond is mad. This is called the "wedge"
Some products have a wedge to wedge connection via a special wirebonding device. This is the case for this special product. See also Microelectronics Packaging Handbook [on Amazon affil links], Edited by Rao Tummala & Eugene J.Rymaszewski, published by van Nostrand Reinhold book, ISBN 0-442-20578-3, pp. 391 and further on)
To: Bill Vins
To my present knowledge, but I am in for any new comment on this, for wirebonding, normally very soft, ultrapure gold deposits are necessary, with as small a greenhouses as feasible.
This brings us to the use of PR-current with very short cycle times (milliseconds) as deposits with these current type are best suited.
For Nickel, this situation as a little bit comparable; I'm not absolutely sure if we need it here, perhaps it can be a consideration to make a sample without PR, but PR here also should make the deposit softer and finer grained.
The finer grains should make a grain boundary preferred Cu-diffusion from the copper base material more difficult. Also porosity of PR-deposits is less and this brings us to PR-current, but not with the purpose you mentioned.
You're absolutely right that this is also a good reason to use PR, but I think here the cycle times are longer?
Be sure Bill that here in the Netherlands it's not so sunny! Thank you so far.
To Dave Kinghorn
Yes, the funny thing is that we never faced any problem with the gold plating on A42.
This problem only started, the moment we started plating Nickel-stripe, followed by gold spot on copper base material.
The wedgebonding takes place at 150 °C, I can give you additional information that always a 500 °C heat test in air during 60 seconds on gold plated A42 looks better as the same test on the nickel and gold plated copper base, even when this gold has a double thickness,
Therefore I think perhaps nickel diffusion takes place. I know that wirebonding is a critical process.
No, the frames are failing in the line test. And the same sample which was good before is good again if retesting at the same moment takes place.
Concerning you question about scanning a picture to show the problem, sorry I'm not so far advanced that I already know how to handle that. Perhaps in the future, but I can give some more details:
After wirebonding with a 25µ gold thread, they do a pull test.
They specify that the average value should be more than 200 mN.
The failing products are giving typical values of 100 mN or so.
I am wondering whether or not it is possible to obtain a kind of "Web brainstorming" or Web storyboarding" about this problem and reasons for bad wirebonding.
I hope we can complete a list like this:
-Too high metallic contamination level in the gold electrolyte
Causes: Dissolved copper from the base
Drag-over of nickel solution
-Organic contamination on the gold surface.
-Diffusion of nickel through the gold layer
The process sequence is degreasing, acid dip, nickel plate, nickel activation, gold strike, gold strip plating, gold backstrip, rinsing, blow-off
Anyone who wants to add something more to this discussion I welcome.
Thanking you all already,
Harry
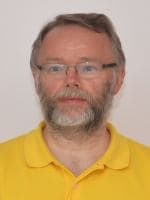
Harry van der Zanden
consultant - Tilburg, Netherlands
A. Harry,
Don't tell me you are trying to do this on a MECO stripe plater! AHHHHHH! (Just Kidding) Regarding your comment about Ni diffusion... Fine grained Nickel structures are preferred by fast diffusers such as Cu since they offer a greater cross-sectional pathway for grain-boundary diffusion. Going to larger grains will actual shut down this mechanism. I use to use 40-60 microinches of large grain Nickel(DC plated) from Sulfamate to shut down Cu diffusion @ 150'C. Of course it seems that the Ni is more tensile under these conditions, but there are precious few grain boundaries available for Cu diffusion. The tensile stresses may cause "orange peel" but you can DOE your bath to find a zero stress condition. Takes about a day on a R-T-R plater. But I suspect your pbm is more fundamental. You mention that it began when you started striping the Cu with Ni plate. So did you wedgebond the same part prior to the Ni stripe? If so then it could be a wirebonder parameter pbm. With that Ni layer, you must turn up the wire bond power. After all, wirebonds yield high pull strengths only if the wire is driven through the plating into the base material, which may no longer be the case if you have added a Ni stripe. Also, are you doing the goldspot on the same machine as the Ni stripe? Or do you remove the reel and pass it on to the Au machine? You mention Au spots, but then callout a gold stripe-backstrip operation. Do you backstrip to form spots, or just to deflash the Cu? Sometimes these backstrippers leave a bit of residue. Proprietary rinse surfactants can be used followed by a VERY hot air dryer. Also, are you using Puma to activate?
Regards, Dave, SUNNYvale CA
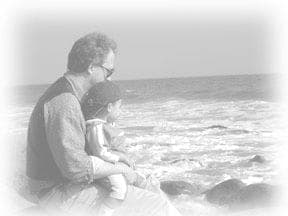
Dave Kinghorn
Chemical Engineer
SUNNYvale, California
1996
1996
? This is a very interesting discussion. After reading all the letters, I am still trying to understand the failure. Using the diagram below, can anyone tell me...
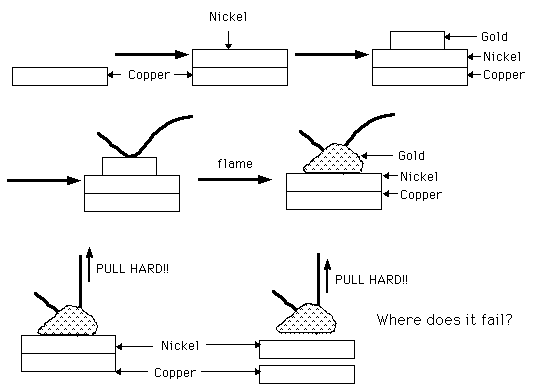
- Isn't the purpose of the gold plate only to keep the nickel clean and active until bonding?
- Are you not putting a nickel layer on to prevent diffusion of copper into the gold?
- If this is so, then you want to bond gold to nickel layer only? and expect the nickel/copper bond to be perfect (atomic adhesion of Cu to Ni should be as good as Cu to Cu or Ni to Ni atomic adhesion).
- Where does the pull test fail?
- Would a microsection of the bond show distinct layers of Gold, nickel and copper as shown?
- If the nickel is not acting as a diffusion barrier, what is its purpose?
On another subject, I would never try to plate nickel without an alkaline cleaning step, then acid dip, then nickel plate. I don't like the idea that you are degreasing, then going right into acid. Are you getting a water break free surface?
thanks, tom


Tom Pullizzi
Falls Township, Pennsylvania
1996
Q. Here I am again to continue the discussion.
Ted,
thank you for your suggestion to chat live, I never exercised it before but I think it would be nice. As far as I know the time-difference is such that it is 6 hours earlier at your site. I think the best thing is that we chat live, the moment we're two weeks further on and having more details. The next coming weeks it will be very difficult for me to predict when I'm home. Anyway, I look forward to this occasion.
Hello Dave Kinghorn,
Sorry, I read something like "as long as it sound not like a commercial … but without kidding, it's a MECO reel to reel line, so no concerns about the condition of the equipment, it belongs to the worlds top-class.
Concerning yr remarks, I think you're right, I'm not so concerned about this zero-stress condition. I don't think it's a prerequisite is it? Some stress is of no concern as the Nickel is not bended and I don't think this tensile stress causes spontaneous cracking of the nickel.
So one of the coming experiments will be plating without PR-current on the nickel
The problem began when we started Copper base material with nickel stripe and gold spot.
Before we plated gold spot directly on NiFe-base, so no Nickel-intermediate was necessary.
We do the nickel & gold plating in one operation-cycle.
As far as I know this wirebonding is a cold-welding process where heat and ultrasonic energy are applied to "melt" the two surfaces together.
I can imagine that applying gold directly on copper will only work if a so called reducing atmosphere (Hydrogen/nitrogen) is used during the wirebonding and this is not the case as far as I'm informed.
To my information the nickel should prevent Cu-diffusion, as this copper is oxidized and prevents a good welding between the gold-gold surfaces.
Anyway, the difficulty is that our customer is already using a current source who delivers Nickel stripe & gold spot on their copper base material. This source also had similar problems in the beginning, but overcame these problems already.
What I want to do by opening this discussion is to find as much information as possible to make a good DOE possible.
Yes, we do backstrip, as we use a gold strike to assure gold adhesion on the nickel surface and to prevent Cu-contamination of the gold electrolyte by the immersion reaction between Au from the electrolyte and the Cu from the base material.
We already planned to make samples without this backstripping, as you're right in the fact that they can leave residues on the surface.
No, no PUMA-activate is used. We use a cathodic activation consisting of KCN & KOH.
DOE is common to me, but what do you mean by pbm?
Thank you so far.
Hai Tom,
Question 1:
You're nearly right with your drawings.
1, 2, 3 & 4 are O.K.; forget about nr. 5 and the flame.
In step 4, the Au-thread is mounted to the surface; by using a special head design, the gold thread is placed on the plated surface.
Heat is applied to heat the plated gold surface up (using a heater block over which the product strip is guided) and the head is fed with ultrasonic energy.
What I meant with the flame is the following: After this wedgebond has been made, the nailhead cuts the thread off on the surface of the product.
For some bonding devices a possibility is that the nailhead then goes up again; this causes the now loose gold thread to expose itself partly hanging in the air under the capillary hole of the nailhead and so a relatively long length of gold thread is now staying outside this nailhead.
Than a hydrogen flame is applied to let this end melt and makes it forming a ball.
This ball can be used to start the whole cycle again.
When using wedge/wedgebonding, no balls are formed, only wedges are made and the bonder head clamps the thread, each time it is transported to another place.
Nr. 6 is in principle O.K. again. The wire, which is supposed to adhere to the surface is picked up by a special fixture and so force is applied until it lifts from the surface or until the wire breaks.
In our problem, the wedge comes loose from the gold surface. So no plating adhesion problems but no good weld is formed for some reason.
Question 2:
Yes, this is the purpose of the nickel
Question 3:
As far as my information goes, the purpose is an optimal adhesion between the gold on the surface and the gold of the bond thread. The should make a perfect weld together.
Question 4:
See nr. 1.
Question 5:
Not made yet; I feel it should be a good idea to do this, I keep you informed about the results.
Question 6:
Already answered.
Yr. last comment: There should be some misunderstandings. The sequence (in short; not mentioning all the rinses) is copper base; a two step degreasing (electrolytically), acid dip, then nickel plate followed by nickel activation & gold strike, than plating goldspot and the last steps are backstripping of this gold strike, final rinsing and drying by blow-off
Again thanks to all; The puzzle is still not solved but I have some more pieces.
Still drizzling here in Holland,
Kind greetings to everybody,
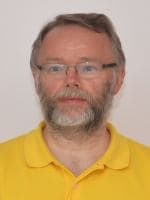
Harry van der Zanden
consultant - Tilburg, Netherlands
Hi Mr. van der Zanden,
Thanks for your reply to my drawing.
I misunderstood when you said "degreasing", I thought you meant solvent cleaning.
But, I wonder now what makes you think that there is something wrong with g? I think at this point, I would want to see that micro section of a weld to make sure you are not compromising the diffusion barrier.
And, I think you are right to investigate the "backstrip" (is that a reverse etch of some sort?). I don't see why you need to roughen the surface to get good adhesion of gold to nickel. It may mean there is passivation of the nickel before gold plate.


Tom Pullizzi
Falls Township, Pennsylvania
A. I agree with Tom, there must be a passivation of nickel along the line. That is the most common reason for adhesion problems between nickel and gold.
How long the Nickel is bare before gold plating? When plating gold on nickel for decorative purposes we first plate the nickel with chrome then we strip the chrome in cyanide solution anodically and activate it in another cyanide solution - cathodically. Sara


Sara Michaeli
Tel-Aviv-Yafo, Israel
1996
A. Harry, could you perform an experiment where you turn off the pumps on the backstrip station and let the material pass through to final rinse, then test one piece for ionics in the ultrasonic DI/Ion chromatography tester, and let your customer attempt to wirebond another piece? Since you indicated wedgebond pulloff without breach of Ni or Cu layer, the pbm (problem) lies in the upper surface of the Au. Therefore no Ni Passivation pbms exist. By the way, could you reveal the gold wire diameter and the wedgebond pull strength in gms you are expecting? Also, are you using a water shedder in your final rinse? Sometimes they require a VERY hot air dryer. But I still suspect the wirebonder parameters are not the correct ones for your part. A "proper" wirebond would be driven well into the nickel, even into the Copper; yet your bonds are pulling off from the surface of the gold only. They are not being driven deep enough. If you want to wirebond to Gold only, you must provide a very thick layer, approx. 150 microinches and you must drive wedge deep...it then has more gold to hang on to. If you use thin gold, you MUST drive the wire into the base material with increased wirebond power. This technique yields superior pull strengths to gold-gold bonds. But the above test will indicate the presence of detrimental contamination on the part. By the way, for our non reel-to-reel techies, MECO is good equipment, and its virtually impossible to detrimentally passivate the Ni on a MECO machine in-process. That's why I asked earlier if you were plating the Gold on another machine at a later time.
Regards,
Dave, in SUNNYvale, CA
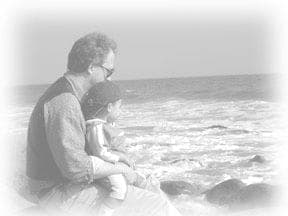
Dave Kinghorn
Chemical Engineer
SUNNYvale, California
1996
1996
Q. Dear Tom Pullizzi & Sara,
I think we still have some misunderstandings in between us.
No adhesion problem of the nickel is occurring; after plating we do the following tests:
A: 1' - 500 °C in air: Not any sign of a blister.
B: Before and after this heat test: A sharp several times bending with pliers: No sign of a loose plating or peeling or flaking of the nickel from the base material, nor of the gold from the nickel.
C. Before and after this heat test applying scotch tape to the surface and retracting it from the surface with high force. No evidence of any peeling.
The problem is not the adhesion of the gold, but the fact that during wirebonding no good weld between the gold wire and the plated gold surface is formed.
The stripping action is done after the gold plating, so no attack of nickel takes place, as the nickel is protected by the gold layer. The only function of this stripper is to remove excessive gold from the all-over surface, caused by the fact that we place a gold strike all-over on the surface before putting the gold stripe selective on the surface.
I hope this made everything a little bit more clear, I understand that it is difficult to explain, I'm sorry for that.
Anyway many thanks for you co-operate thinking and kind greetings,
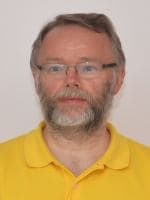
Harry van der Zanden
consultant - Tilburg, Netherlands
1996
As I promised to tell something more in wk 47, here some additional information:
We made laboratory samples and found out that at least 2 influences that embarrassed me make the situation worse:
1. A Cu-contamination in the mg/l. level in the Nickel-electrolyte
2. Back stripping action deteriorates the wirebonding quality.
The preheat cycle for the gold surface is 150 °C,
The capillair is heated to 100 °C.
The frequency is 25 kHz.
Within a few weeks we will start again with line-samples and I'll keep everybody informed.
Still waiting for additional information though
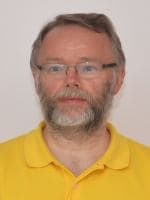
Harry van der Zanden
consultant - Tilburg, Netherlands
Q. Hi Harry,
I came across your letter (quite too old) about the lifted weld problem. May I know what is the root cause of that? It is because I recently encountered that problem but in my case, we're wire bonding aluminum wire to printed circuit boards (wedge to wedge bonding at room temperature, instead of gold bonding). Same trace structure-Gold over Ni over Cu. Typical values Ni= 1.2-3.8 microns Au= 0.19 - 3.6 microns. What possible storage condition may affect the bonding if considered a cause? We are building this device in small quantity; that's why similarly to your case before, it's hard to follow up on that problem.
Thanks for any help.
Regards,
- Laguna, Philippines
2002
? What was the root cause?
Dan Mendoza- Leominster, Massachusetts
June 28, 2010
----
Ed. note: Readers may also be interested in letter 24171, "Gold over Nickel on PCBs for wire bonding".
Q. Hi, can somebody help me why this happened? Ferrite core with Ag,Ni and Au plated. After copper wire bonding got hump. Thank you.
Ahmad a [surname deleted for privacy by Editor]R&D Analyst - Klang, Selangor, Malaysia
February 23, 2017
A. Hi ahmad,
Although we don't have a photo or further description, this sounds like a blister ... which usually indicates poor plating adhesion, which failed after time and temperature. If you tell us more about this "ferrite core", people may be able to give an indication of what to look for first.
Regards,
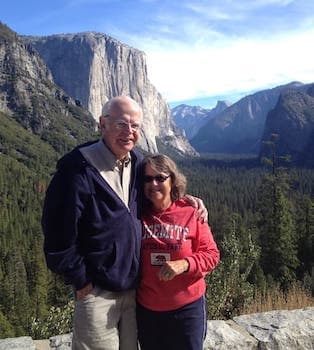
Ted Mooney, P.E. RET
Striving to live Aloha
finishing.com - Pine Beach, New Jersey
February 2017
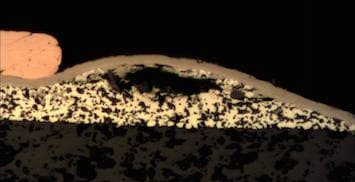
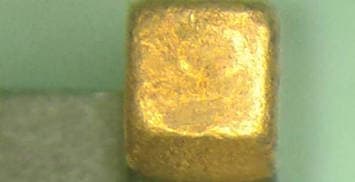
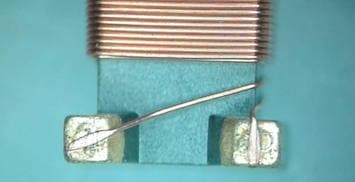
Q. Photos. Thank you.
Ahmad a [returning]R&D Analyst - Klang, Selangor, Malaysia
February 24, 2017
A. Hi again Ahmad. Your metallography shows the problem to be not so much blistering of the plating as your ferrite core disintegrating. It sounds like it absorbed water during the plating process, which got sealed in, and exploded upon heating.
Regards,
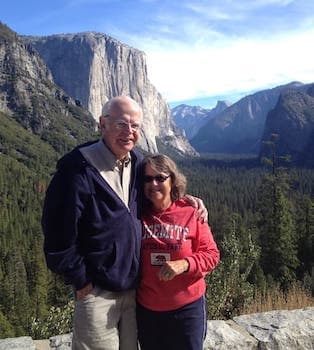
Ted Mooney, P.E. RET
Striving to live Aloha
finishing.com - Pine Beach, New Jersey
February 2017
Ferrite eroding during plating.
Q. I have some ferrite parts with a fused silver base metal layer. Nickel and then tin are electroplated onto the silver. There is evidence of erosion, after plating, at the point the base metal stops.
Could this be galvanic erosion? The ferrite contains iron oxide, nickel oxide, zinc oxide and copper oxide. Nickel plating is ~50-100 µin. and the tin is ~100-150 µin. Any thoughts on the erosion is appreciated.
James Dillow- Oregon, Illinois, USA
February 28, 2017
Q, A, or Comment on THIS thread -or- Start a NEW Thread