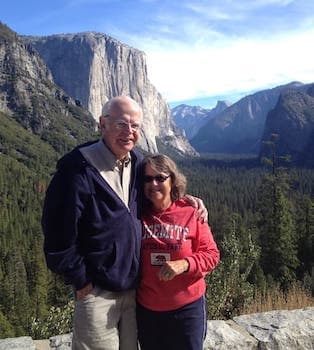
Curated with aloha by
Ted Mooney, P.E. RET
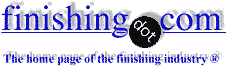
The authoritative public forum
for Metal Finishing 1989-2025
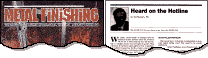
-----
Difference between Electrogalvanized and Hot Dip Galvanized Steel

< Prev. page (You're on the last page of the thread)
Q. Hello,
Can someone please explain to me the difference between hot dip galvanizing and zinc electro plating. I have bean searching for the answer too long. The two systems have the same characteristics.
- UAE, DUBAI, MERDIF
May 29, 2017
A. Hi Elias. Hot dip galvanizing is the application of a zinc coating by dipping a steel article into molten zinc. Zinc electroplating is the application of a zinc coating to a metal by dipping the article into an acidic or alkaline water based bath and applying DC current to dissolve zinc off of zinc anodes and reduce it onto the article.
Some characteristics are similar because the surface is zinc in either case; but some characteristics are quite different because of the application method. This 3-page threads explains in detail most of those differences; the differences cannot be condensed into a single sentence.
I think if you present your full situation people can recommend which finish is most suitable for that situation. But if you want to be able to make such determinations for yourself, it's not realistic at a level of study less than at least carefully reading these 3 pages and asking further detailed questions. Good luck.
Regards,
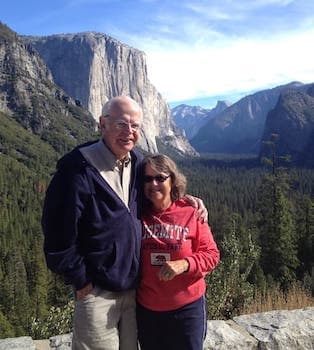
Ted Mooney, P.E. RET
Striving to live Aloha
finishing.com - Pine Beach, New Jersey
June 12, 2017
Q. I have a drinking water system. I want to know what can I use, Hot Dip Galvanized Carbon Steel Pipes or Electrolized Galvanized Carbon Steel Pipes?
These pipes are exposed to sunlight.
EL SEWEDY - Cairo, Egypt
July 4, 2017
A. The basic difference is electroplating is generally done for 4 microns [.00016"].This means the coating on the steel of zinc. Whereas Hot dip Galvanising generally based on various standards has a requirement for 86 microns of zinc. For corrosive environment HDG is a norm. Hot dip and electroplating are different processes altogether.
Vishal AgarwalINDANA STEEL PVT.LTD - kolkata,West Bengal, India
June 25, 2017
Q. If Steel Wire is zinc coated : 14g / mm2 would you say this is electro galvanised or hot dip galvanised?
Thanks in advance for your reply.
Regards, Simon
G,VELLA AND SONS LTD. - MARSA, MALTA
August 16, 2017
A. Hi cousin Simon. I wouldn't say either unless I knew. If you claim it is hot dipped and it is not and it goes into a computer server room, you could be sued out of business. If it goes into life support equipment, you could be charged with manslaughter if zinc whiskers short it out at a bad time. Don't guess! I'd just say 'zinc coated'.
Why exactly does it matter? Please post your situation, rather than an abstract question. Thanks!
Regards,
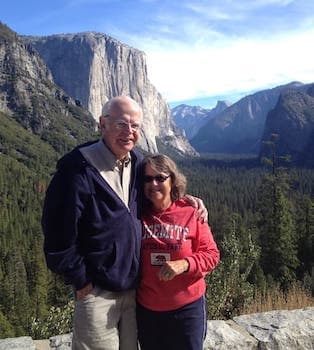
Ted Mooney, P.E. RET
Striving to live Aloha
finishing.com - Pine Beach, New Jersey
August 2017
Q. What do you recommend for a dock?
Stacey drake- elberton Georgia
September 14, 2017
A. Hi Stacey. If you're telling me that the only choices for this dock are zinc plating or hot dip galvanizing, I certainly wouldn't pick zinc plating.
If you're asking of all the materials in the world, which are best for your particular dock, we'd have to know something of the situation, as they are often made of teak, cedar, pressure treated wood, galvanized steel, plastic, stainless steel and possibly other materials. Good luck.
Regards,
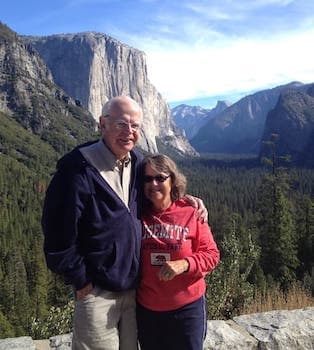
Ted Mooney, P.E. RET
Striving to live Aloha
finishing.com - Pine Beach, New Jersey
September 2017
Does zinc plating require pretreatment before powder coating?
Q. Hi,
This is a very interesting forum to follow. I am just wondering does electrogalvanized steel (Zinc coated steel) needs special surface treatment like cleaning before it enters powder coating line?
Thanks in advance.
Jeremy
- Cleveland, Ohio, United States
October 11, 2017
A. Hi Jeremy. All metal requires pretreatment before powder coating. However, zinc plating conducted on finished parts at a plating shop virtually always has a chromate conversion coating applied, and this chromate conversion coating is supposed to serve as proper pretreatment for powder coating.
Regards,
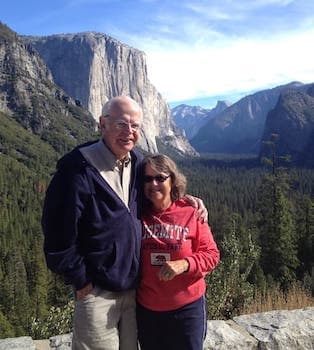
Ted Mooney, P.E. RET
Striving to live Aloha
finishing.com - Pine Beach, New Jersey
October 2017
![]() |
Hi Mr. Ted Mooney, - Cleveland, Ohio, United States October 12, 2017 A. I would think that this item requires further explanation. trainer - Newcastle, NSW, Australia October 15, 2017 |
December 13, 2017
Q. Hi All experts.
What is the difference between GI Plate with EG Plate?
Is EG plate a type of GI plate or via versa?
Or completely different things?
As my reading continues, more confusion I get.
Please advise.
Thanks and have a good day!
- Jakarta Indonesia
A. Hi Braham. "EG" is an acronym for ElectroGalvanized, i.e., a zinc coating that has been applied by electroplating rather than by hot dipping. "GI" is an acronym for Galvanized Iron, and actually means galvanized steel.
If you were able to give me an exact detailed specification of what YOU mean when you say "GI", then we could compare it to EG and answer your question. But some people sometimes call hot-dip galvanized material "GI", and other people sometimes call electrogalvanized/zinc electroplated material "GI" ...
It's not your fault or my fault, but since we unfortunately can't know whether people actually mean electroplated or hot dipped when they say "GI", we can't answer your question. People will always try to obfuscate to sell you something :-(
Regards,
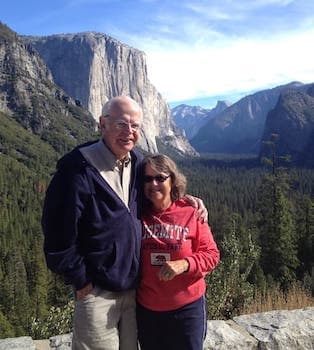
Ted Mooney, P.E. RET
Striving to live Aloha
finishing.com - Pine Beach, New Jersey
December 2017
Q. Hello,
Is anyone able to recommend hardware requirements for an outdoor hockey rink? The options are hot dip galvanized or electroplated. From earlier comments, it seems hot dip galvanized is thicker and will last longer.
Thanks everyone,
Amy
- Canmore, Alberta, Canada
May 15, 2018
A. Hi Amy. Hardware for outdoor exposure should probably be galvanized. I doubt that zinc electroplated hardware will last long in outdoor exposure.
Regards,
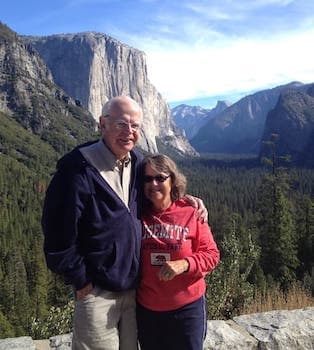
Ted Mooney, P.E. RET
Striving to live Aloha
finishing.com - Pine Beach, New Jersey
June 2018
Q. Hi, We produce steel doors that are powder coated. We are about to have a fire test done on our doors. Would HDG be more fire resistant than the Zintec doors? Thanks for your time.
Jack BannisterNorwood Group - Heaton Mersey
June 6, 2018
A. Hi Jack. Although I don't actually know, I would be surprised if the relatively thin coatings of zinc on steel doors have much effect on their fire resistance. "Zintec" may be a bit ambiguous though; it's the name of an aluminum door manufacturer in the USA, as well as the name of a coating on steel doors -- and quick googling shows that some manufacturers claim it to be zinc electroplating, others claim it is a zinc-aluminum mix.
Within the UK though, it probably means: "the trade name for British Steel plc cold rolled sheet and coil that has been electrolytically coated with a thin layer of zinc. It is produced at steel thicknesses of 0.4 to 2.0mm and contains a thickness of zinc from 1.0 to 1.75 microns. Zintec can be recognised by its matt grey appearance significantly different to the bright spangled surface produced by hot dip processes of galvanizing and Galvatite." -- according to https://uk.answers.yahoo.com/question/index?qid=20100721083134AAD8SSB
Regards,
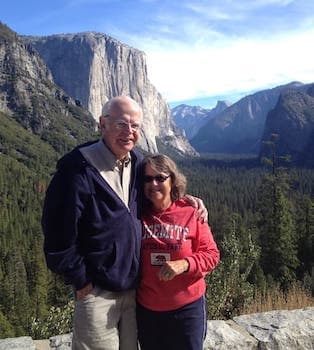
Ted Mooney, P.E. RET
Striving to live Aloha
finishing.com - Pine Beach, New Jersey
June 2018
Q. I live in a Chicago high rise and we're about to construct a 2000 sq.ft. roof deck using pedestals, 2 x 2' trays, and 2 x 2' porcelain tiles sitting on top of them. When I asked whether the trays were hot dipped or plated, he said he'd have to check with the China plant. He came back and said hot dipped. Both sides are mottled, with the frosted glass appearance, but on one side, just the corner areas are smooth where there is a piece welded on top of each corner.
This deck has to last decades exposed to Chicago's weather and we're concerned it won't last if not hot dipped. Think it's really hot dipped except for the corners?
Keller Teal- Chicago, Illinois USA
July 18, 2018
A. Hi. The main sheet is definitely hot dipped galvanized; it's hard to say what the corners are, and the pictures aren't definitive enough to really understand what's going on with the rolled edge and whether this was pre-galvanized such that there are raw edges.
Hot dipping is an excellent indication that they will outlast zinc electroplated trays; but without knowing the exact specs or exactly how they're used, it might be a stretch to expect 'decades'. Rainwater is not very corrosive, but I would try to avoid exposure to de-icing salt or fertilizers. Good luck.
Regards,
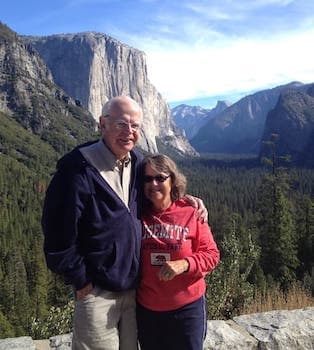
Ted Mooney, P.E. RET
Striving to live Aloha
finishing.com - Pine Beach, New Jersey
July 2018
![]() |
A. Sir: Galvanizing Consultant - Hot Springs July 20, 2018 Q. I suspect that the dipper was instructed to make sure that those tile support plates could be welded/soldered to the corners afterwards, so he may have done something to smooth them out? Perhaps it's difficult to weld/solder to HDG?
- Chicago, Illinois, USA July 19, 2018 |
A. The fact that the welding doesn't seem to have burned off the galvanizing on the main sheet at the point of the welds, suggest that the whole was galvanized after welding, but that the varying thickness of the steel plate versus the thicker corners has shown a different appearance.
The main plate galv is very nice finish with good spangle that is more often found in pre-galv sheet (continuous galvanizing as opposed to batch galvanizing), but such a finish is possible in batch galv.
In the later pictures the edges of the thicker corner pieces look unusual, almost ungalvanized, but hard to tell.
It's quite possible to weld galvanized stee after galvanizing, but arc welding (stick, mig, tig etc) will burn away the zinc in the HAZ (Heat affected zone). And that will be very obvious. It's very possible to solder galvanized steel, but I suspect soldering would not be strong enough. You could test for soldering with a knife. If you can cut the weld material suspect soldering it's very soft. If the weld is steel and the surrounding zinc not burned, then the weld was done before galvanizing.
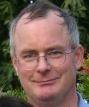
Geoff Crowley
Crithwood Ltd.
Westfield, Scotland, UK
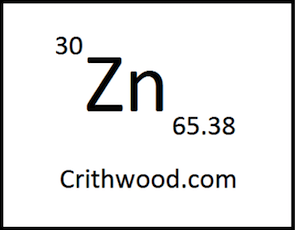
August 15, 2018
Q. Hello,
Why do the carmakers stampers prefer Electrogalvanized over hot dip galvanized steel?
- Joinville, SC, Brazil
August 15, 2018
A. Hi Carlos!
(Please re-read our request that you tell us who you are, what you do, and why you want to know because abstract questions are often misunderstood, and they usually generate a need to address "ifs, ands & buts" that didn't even apply to whatever your own unique situation may be; as a result they are time-consuming and unrewarding and the readers will only very rarely respond)
Can we assume that you are talking about the sheetmetal areas on automobiles which will subsequently be painted, like rocker panels and fenders? Electrogalvanized/galvannealed sheetmetal is less expensive than hot dip galvanized sheetmetal, the paint will adhere easier and better, and since the coating is thinner and smoother it is more compatible with the decorative nature of an automobile. Good luck.
Regards,
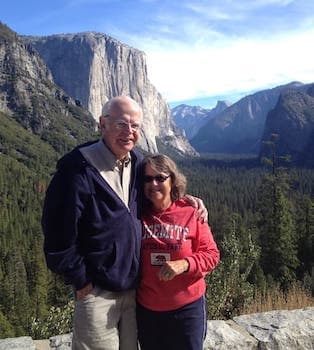
Ted Mooney, P.E. RET
Striving to live Aloha
finishing.com - Pine Beach, New Jersey
August 2018
Electroplating vs. galvanized for permanent tent
Q. Hi.
I am in the process of purchasing an A-Framed tent for worship purposes. The quote for Electroplated frames is significantly cheaper than the hot-dipped galvanized steel. Can I go with the electroplated in this case? The tent will be permanently set up!
Evangelism - South Africa, Cap Town
September 8, 2018
A. Hi Deone. It's very difficult to determine the quality of anything from the seller's sales pap, but I doubt that electroplating will deter rust for very long in that situation. Hot dip galvanizing is probably better.
Regards,
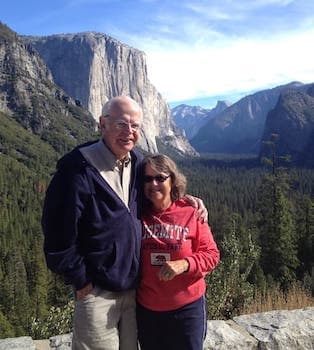
Ted Mooney, P.E. RET
Striving to live Aloha
finishing.com - Pine Beach, New Jersey
September 2018
September 10, 2018
A. Sir:
Because of the salt air in Capetown, I do not think electroplated will last more than one year.
Hot dip galvanized may fill in the screen spaces.
Regards,
Galvanizing Consultant - Hot Springs, South Dakota, USA
Q. We are using EGI steel sheets to fabricate fire resistant steel doors with infill as honeycomb or Odiboard 2.6. Are we on the right direction? Our primary requirement is a one hour rating. The overall door width is 40 mm. Thank you
Tony RanasingheTrat Coatings Pvt Ltd. - Ragama ,Sri Lanka
December 13, 2018
A. Hi Tony. As far as I know, galvanizing and zinc plating are not about fire protection they are about corrosion resistance. So I'm not quite sure what the question is -- you are using an infill with a one-hour fire rating, and that's fine, but whether you use hot-dip or electrogalvanizing doesn't sound like it would affect the fire rating.
Is this an interior or exterior door? Is the zinc coating the final finish or is paint/powder used over it? Will it be used in Sri Lanka or exported?
Regards,
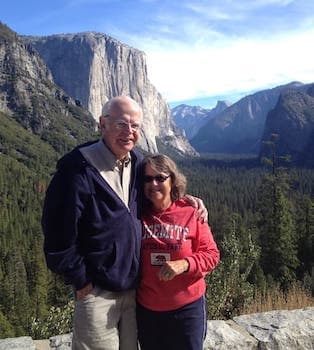
Ted Mooney, P.E. RET
Striving to live Aloha
finishing.com - Pine Beach, New Jersey
December 2018
Q. Thank you for the reply. Yes we use EGI steel sheets for corrosion control and resistance since SRi Lanka is an Island. We use powder coatings as a finish product. Thank you.
Tony Ranasinghe [returning]- Ragama ,Sri Lanka
December 19, 2018
A. Hi again Tony. I would expect electrogalvanized sheet followed by phosphatizing and powder coating to be excellent in corrosion resistance.
Regards,
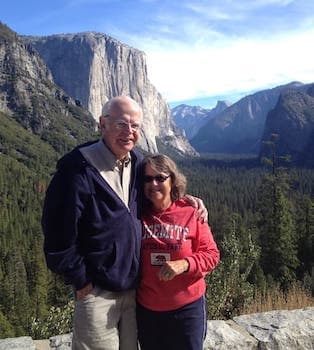
Ted Mooney, P.E. RET
Striving to live Aloha
finishing.com - Pine Beach, New Jersey
December 2018
Q. Hi, to follow up on a recent post where I asked about how to tell if a process of hot dip galvanizing being offered for roofing gutters was technically accurate (thread 29835), I should have contextualized (for the benefit of you and the readers) that the reason I wanted to know about the visual difference between the bright spangles associated with electro galvanizing versus the flat full grey associated with hot dip galvanizing is that hot dip galvanizing has a -- generally speaking -- greater longevity in outdoor situations and also that for me the full flat grey appearance is, for one thing, more aesthetically pleasing -- taking on the the visual qualities more closely along the lines of lead coated copper gutters and downspouts though without the almost prohibitive costs of lead coated copper, while simultaneously providing a corrosion resistant coating that exceeds that of electro-plating zinc.
My concern is that through accidental obfuscication or willful ignorance the terms and qualities advertised for the roof gutters and related components are being conflated or confused and I wanted to research the product enough on my own (and with your help and that of this forum) to share a method of inspecting a sample with the naked eye (for those of us without laboratory testing equipment to discern the difference and by extension to make an informed purchasing choice.
Roughouse GV LLC - New York NY usa
December 3, 2019
A. Hi Richard. Unfortunately, when you seek a certain aesthetic from finishes which are not designed to be decorative, it can be a tricky road. Two such finishes may meet all specifications and not look the same. And finishes on different types of parts may be applied differently, resulting in a different aesthetic.
Something that concerns me about gutters is that I suspect they are not hot dip galvanized after fabrication; rather, I believe that, conventionally, the coil of metal is continuously galvanized in reel-to-reel fashion, and "wiped" to minimize the zinc thickness. This wiping is going to leave the metal with a different look than the gravity drip of hot-dip galvanizing on articles dipped after fabrication; plus the greater thickness of zinc on hot dip galvanizing compared to electroplating may not persist after they have been wiped.
In short, when you want a particular look from galvanizing you may have to work with a particular applicator.
Regards,
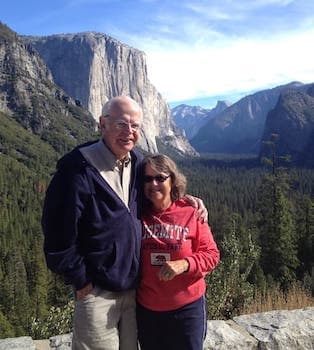
Ted Mooney, P.E. RET
Striving to live Aloha
finishing.com - Pine Beach, New Jersey
December 2019
Q. Hi Sir ... Which type of galvanising is required for bucket handle, Hot Dip or Electro-galvanising? Because one of our customers is complaining that the material we supplied to them (which is HDG) is getting dull after some days of manufacturing. Please suggest. At present we are sending him material without wax. Shall we try for waxing? Will this waxing increase the life of shine on wire?
Manoj M Thakur- Abu Dhabi, UAE
June 3, 2020
A. Manoj, Personally I prefer HDG. It is thicker and gives a more decorative finish, with lovely crystal structures. It is easier to use HDG than electroplating, as you don't need so much equipment. The down side is that HDG is much thicker than electroplate and that you can add brighteners to electroplated zinc and these reduce the dulling you mention. The dulling is caused by oxidation of the zinc, so to keep it bright, you need to prevent oxidation. This is easiest done by dipping the galvanised product in oil or very low melting point wax.
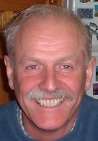
Trevor Crichton
R&D practical scientist
Chesham, Bucks, UK
June 8, 2020
Q, A, or Comment on THIS thread -or- Start a NEW Thread