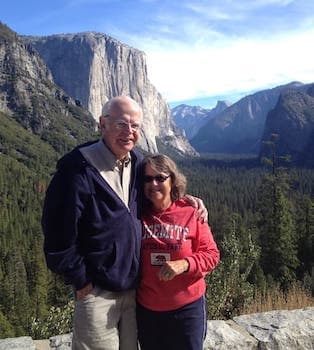
Curated with aloha by
Ted Mooney, P.E. RET
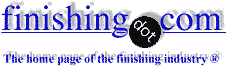
The authoritative public forum
for Metal Finishing 1989-2025
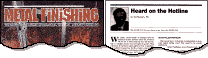
-----
Difference between Electrogalvanized and Hot Dip Galvanized Steel

Q. I understand from your postings that hot-dip galvanizing provides 10x better protection for outdoor exposure than electro-galvanizing. Can you provide a link to any technical literature that succinctly states this fact. We want to show a customer why hot-dip galvanizing is better to use on a project when compared to electro-galvanizing (3" x 3", 11 gauge steel legs and brackets exposed to the outdoors 24/7, often in maritime environments, for 10-30 years).
Thanks!
- Reno, Nevada USA
August 3, 2015
A. Hi Tyler. I don't think I or anyone here said quite that ...
I have claimed that, for zinc coatings, service life is roughly proportional to the zinc thickness: "zinc is zinc" -- although galvanizers claim the zinc-iron alloying extends the life, and platers claim the purity of the zinc plating deposit extends the life. When coating is done post-fab, heavy hot-dip galvanizing might be 10X as thick as thin zinc electroplating. But if the galvanizing is done pre-fab, while processing sheet, some sort of wiping action is common and hot-dip may not be be much heavier than zinc electroplating. My guess until you say otherwise is that 11 gauge legs are fabricated from pre-coated sheet.
If you can say that your coatings will be substantially thicker than the alternatives, the service life should be substantially longer than the alternatives. If your zinc coatings are the same thickness, the service life will be about the same. If the parts are painted or powder coated after the zinc coating, it can be pretty hard to make predictions :-)
Regards,
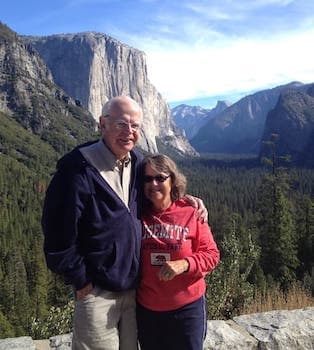
Ted Mooney, P.E. RET
Striving to live Aloha
finishing.com - Pine Beach, New Jersey
August 2015
Dear All.
I found this site while I was looking for differences between hot dip galvanized wire and electrogalvanized.
I am going to buy chicken mesh (hexagonal mesh). In the spec of the mesh I have 40 to 45 grams per square meter. We also have information it is hot dip galvanized.
Recently I got question if we could use mesh made from electrogalvanized wire. So my question would be if there is no difference assuming the thickness of zinc layer would be the same? Is there any cost difference by using one or another application method? Mesh would be exposed mainly outside so corrosion resistance is most important in my case.
Thank you very much in advance and have a great day!
Wojciech
- Bydgoszcz, Kujawsko-Pomorskie, Poland
August 19, 2015
A. Hi Wojciech. After many pages of postings on this subject we are into endless repetition, but ...
For practical purposes, "zinc is zinc" so the corrosion resistance of equal thicknesses will be about equal. Electrogalvanizing will usually prove more practical and cheaper for thin coatings, and hot dipping will prove more practical and economical for thick coatings. Wire gets a bit more complicated regarding practical thicknesses and costs because it is often drawn down to a thinner gauge after coating. You might have to shop around regarding relative cost for in-between applications. Good luck.
Regards,
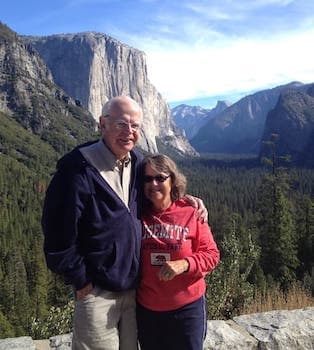
Ted Mooney, P.E. RET
Striving to live Aloha
finishing.com - Pine Beach, New Jersey
August 2015
![]() |
October 3, 2015 Hi Ted - Algiers, Algeria
But this site has maybe a hundred "regular readers" who answer most of the questions, and who made & continue to make this site a grear place to get answers. Although I'm only the operator of a small website not a movie star, to them and about them I happily repeat Bette Midler's words, with full sincerity & true humility: "Thank you ... Thank you ... Thank God for you, the wind beneath my wings". Regards, ![]() Ted Mooney, P.E. RET Striving to live Aloha finishing.com - Pine Beach, New Jersey |
Q. Dear experts, What is better for Interior false ceiling of Under Ground Metro Rail Stations.. Electro galvanized Steel sheets OR Hot dipped galvanized Steel Sheet?
Regards!
Madanmohan Goswami
Shivdatt Construction Pvt. Ltd. - Mumbai, Maharashtra, India
February 19, 2016
A. Hi Madanmohan. The atmospheric corrosion resistance of zinc coated steel is pretty much proportional to the thickness of the zinc. In the case of post-plated fabrications, the thickness of zinc on hot-dipped articles almost always greatly exceeds the thickness of zinc on electroplated (electrogalvanized) articles, and therefore they are significantly more corrosion resistant.
But in the case of pre-plated sheet, my understanding is that the hot dip galvanize lines usually have "wipers" to reduce the thickness of the zinc coating and hold it to a particular thickness/weight. So in this case, I think you have to go by what the coating thickness/weight specification is, rather than ideological factors. In other words, the specification should tell you the zinc thickness, and the thicker coating will be the more corrosion resistant.
Regards,
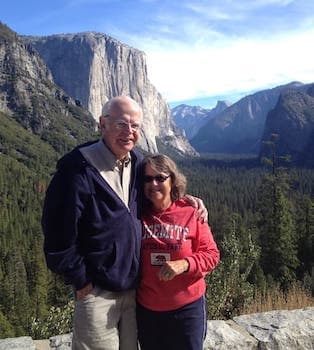
Ted Mooney, P.E. RET
Striving to live Aloha
finishing.com - Pine Beach, New Jersey
March 2016
Q. Hi,
Which process (between electro-galvanizing and hot dip galvanizing) is better if I want to coat my fastener (Material: Mild steel) which is going to be dipped most of the time in electrolyte bath?
Anxiously waiting for reply.
IIT Bombay - Mumbai, Maharashtra
March 17, 2016
A. Hi Pratik. Neither!
These zinc coatings are useful towards preventing corrosion under atmospheric conditions; and thick zinc coatings like hot dip galvanizing can be useful for saltwater exposure. But depending on the "electrolyte", it may well attack a zinc coating much faster than it attacks steel. For example, zinc dissolves almost instantly in hydrochloric acid. A quick rule of thumb is probably that zinc is not chemically resistant.
Regards,
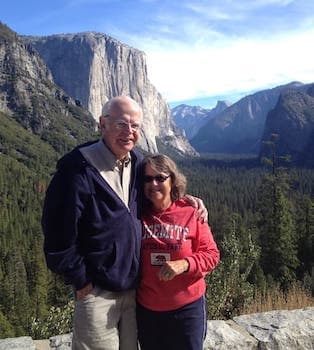
Ted Mooney, P.E. RET
Striving to live Aloha
finishing.com - Pine Beach, New Jersey
March 2016
June 21, 2016
Q. Hello,
We make leaf springs for automobiles (used outdoor under chassis) and use steel liner in between the leaves. These liners are supposed to be Galvanised.
What would be the correct operations for these liners ?
Plating or Hot Galvanising?
Thanks
- Pune, India
A. Hydrogen Embrittlement is probably a smaller concern with galvanizing, but if they are supposed to be galvanized, that means hot dip galvanized to me regardless of advantages or disadvantages.
When someone offers to sell me 'gold', I don't want to have to use the the longer form 'real genuine gold, atomic number 79 on the periodic table, not fake gold-colored cheaper imitation stuff'. And when 'galvanizing' is specified, it should mean galvanizing, i.e., hot dipping, without the need to say 'real genuine hot dipped in molten zinc galvanizing, not fake electrogalvanized cheaper zinc electroplated stuff' :-)
Regards,
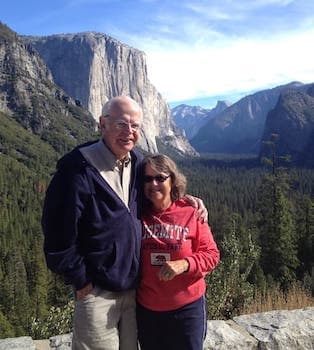
Ted Mooney, P.E. RET
Striving to live Aloha
finishing.com - Pine Beach, New Jersey
How are fasteners galvanized
Q. Could you please throw some light on how the Fasteners (threaded nuts and bolts) used in Transmission towers and telecom towers are Galvanized (they are not electroplated as acid resistance required is higher, as they are exposed to rains, and cyclic weather).
Regards
Amol
- Pune, Maharashtra, India
July 20, 2016
A. Hi Amol. I am no expert and have no galvanizing experience at all, but I understand that they are dipped, then 'spun' in a centrifugal machine to minimize drips blocking the threads of the screws. I also understand that to minimize thread interference, the nut 'blanks' are usually galvanized first, then drilled and tapped; although this means the thread is bare steel, the galvanizing of the screw thread, plus everything else being galvanized, protects them.
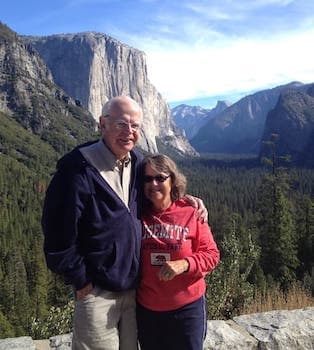
Ted Mooney, P.E. RET
Striving to live Aloha
finishing.com - Pine Beach, New Jersey
July 2016
A. Dear Mr. Amol,
You can Galvanize threaded nuts and bolts with the help of Centrifugal machine.
Gunatit Builders

Manjalpur, Vadodara, Gujarat
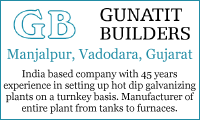
July 26, 2016
A. Ted is exactly correct in his description of hot-dip galvanized fasteners. An alternative is mechanical galvanizing, which gives equivalent zinc thickness (roughly two mils).
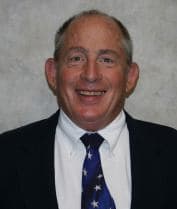
Tom Rochester
CTO - Jackson, Michigan, USA
Plating Systems & Technologies, Inc.

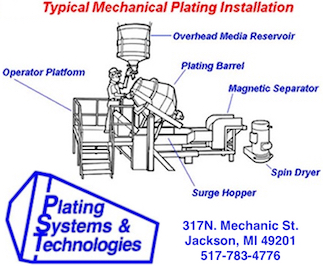
July 21, 2016
Excellent point Tom. Hot dip galvanizing and zinc electroplating are not the only ways to apply a zinc coating, and sometimes neither is the best way!
When very thin coatings are required on very small fasteners, zinc electroplating is the usual choice. When very thick coatings are required on very large fasteners, hot dipping is the usual choice. In the broad middle range, mechanical galvanizing or other approaches may be better than either.
Regards,
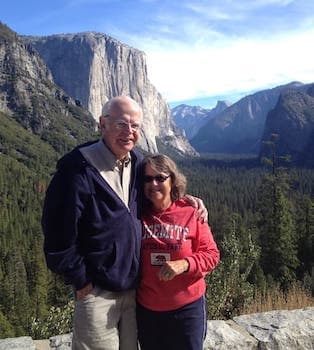
Ted Mooney, P.E. RET
Striving to live Aloha
finishing.com - Pine Beach, New Jersey
July 2016
Q. Sir,
How can we know once painted 2-coats whether the metal sheet is Hot dipped or Electroplated for a lay man.
Please help.
Thanks.
- Mumbai, Maharastra, India
July 27, 2016
? Hi Kumar. You probably can't. Why does it matter to you?
Regards,
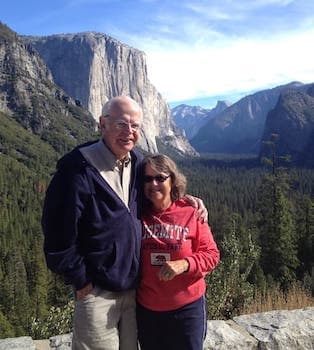
Ted Mooney, P.E. RET
Striving to live Aloha
finishing.com - Pine Beach, New Jersey
July 2016
Q. Sir, Thanks for your prompt reply. I asked you that because I want to check one container as the vendor told that it is hot dip galvanised but not pre galvanised.
Can we also do powder coating baked in Oven on the hot dipped galvanized container. Which lasts longer, powder coating baked or sprayed epoxy primer and 2 coats of Paint?
Thanks
- Mumbai, Maharastra, India
July 27, 2016
Hi again Kumar. You can strip the paint off and look for the presence of zinc on the sheared edges and around any punched or drilled holes. If there is none, the material probably was plated or galvanized before fabrication; if there is zinc there, it was plated or galvanized after fabrication. But I was trying to understand why it is functionally important to you that the metal sheets were hot dipped after fabrication rather than being electroplated, so "because the vendor claimed they are" is not quite the direction I was looking for you to go :-)
If proving or disproving a commercial claim is the intent, you must hire a professional testing lab, not rely on "a lay man" to generate a professional opinion.
You can do powder coating or epoxy primer and paint after proper pretreating, which is probably zinc phosphatizing. Epoxy primer and two coats of paint will probably "last longer" than a single layer of thermoset powder coating because there is probably less chance of a pinhole or porosity in a 3-layer coating system ... but the reason you see both approaches is because each is "better" in certain circumstances. Best of luck.
Regards,
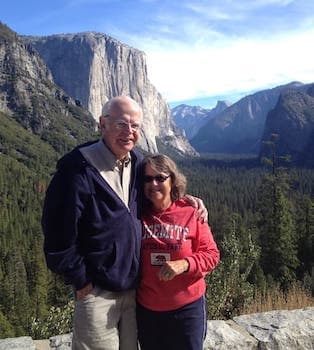
Ted Mooney, P.E. RET
Striving to live Aloha
finishing.com - Pine Beach, New Jersey
July 2016
Q. Hi,
We have a situation where we are mounting an irrigation siphon with same flange part to be assembled with bolt and nut. What would be the best option HDG or EG
Thanks for your advise,
- Kigali, Rwanda
April 13, 2016
A. Hi Fabrice. It's not clear whether you are talking about a coating for the flanges or the nut & bolt. If you're talking about the nut & bolt, it's not clear what the coating on the flanges is. In any case, HDG gives greater thicknesses and therefore probably offers superior corrosion resistance.
Regards,
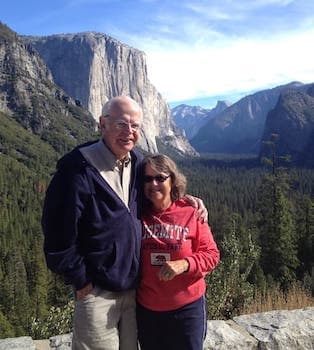
Ted Mooney, P.E. RET
Striving to live Aloha
finishing.com - Pine Beach, New Jersey
Tip: Readers want to learn from Your Situation 🙂
(little can be learned from abstract questions, so many readers skip them)
A. Sir,
Is there any other recent technology other than these two?
- Dhaka,Bangladesh
June 30, 2016
A. Hi Aushi. Certainly there is ... there are many different coating and corrosion-resisting technologies. Tom Rochester just mentioned mechanical galvanizing, and there's sherardizing, flame spraying, zinc-rich paints, etc. What is your situation?
Regards,
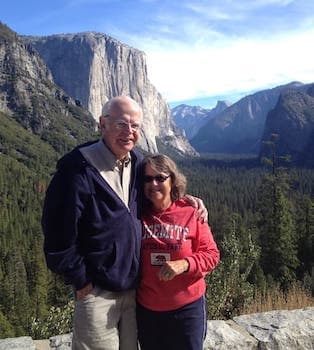
Ted Mooney, P.E. RET
Striving to live Aloha
finishing.com - Pine Beach, New Jersey
September 2016
Is hot dip galvanizing or zinc electroplating better for pipe?
Q. Please correct me if I'm wrong but another advantage of electroplating is that it doesn't flake off over time. This is especially important if used for piping as the flakes from HDG could potentially clog small orifices in equipment fed by an old pipe network. As I understand it EG wont flake off as it is a chemical bond and not just one metal melted onto another.
Leif Macrae- Forestville, California, usa
September 20, 2016
A. Hi Leif. It's hard to compare adhesion strengths between different technologies because they are all subject to being done poorly, with resulting low bond strengths. If done right, both galvanizing and zinc plating will "stick" far more than is necessary for suitable pipeline service, although you may be right that electroplating sticks better in the ideal case.
But it is much easier to hot dip galvanize the interior of a pipe than to electroplate it with zinc, so I am not familiar with any pipe that has an interior coating of zinc plating anyway. If there is such a product line, please advise. Thanks.
Ted Mooney, P.E. RET
Striving to live Aloha
finishing.com - Pine Beach, New Jersey
November 27, 2016
by Polyanskiy & Belyaev
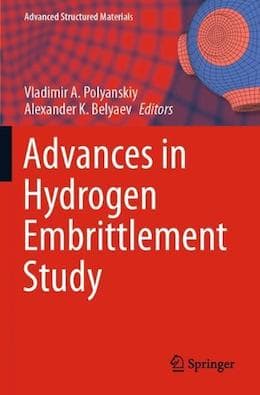
on AbeBooks
or eBay or
Amazon
(affil links)
Q. Dear Sir,
I read through the whole thread from 2003 till now.
I notice that you stated there is no different effect on mechanical properties at least for mild steel.
But for high strength steel, such as HR500LA, is there any difference? And where can I find some paper on it?
Thank you.
Automotive - Nanjing, China
A. Hi Charles -- thanks for your patience! But proceeding from the abstract like this begins with a slight misquote of me; so then I have to note, for the benefit of other readers rather than you, that that isn't exactly what I said, etc., etc :-)
Instead, please tell us what you are doing and describe the details of your actual situation, and how it relates to hot-dipping vs. electrogalvanization (if it does).
The basic idea is that electroplating, pickling, cathodic electrocleaning, and some other metal finishing operations generate hydrogen. If the steel is soft mild steel, it's no problem; but in hard high strength steels this can cause hydrogen embrittlement, which means the steel can fracture under unexpectedly low loads. Hydrogen embrittlement is usually addressed by immediate baking, although some steels are so hard that they should not be pickled or plated at all. You seem to be describing a formable steel that doesn't sound real hard, but I think the steel vendor can give you a quick answer as to whether this grade of their steel can suffer hydrogen embrittlement. Then we can proceed with your questions from there. Good luck.
Regards,
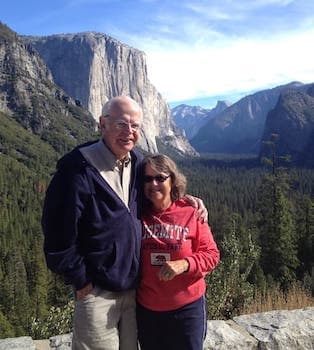
Ted Mooney, P.E. RET
Striving to live Aloha
finishing.com - Pine Beach, New Jersey
November 2016
Q. I am currently looking at different coating options for offshore drilling equipment cranes. Two topics that I have run into are galvanizing and plating. I understand there is electroplating and mechanical plating, but which (out of galvanizing versus plating), would be more suitable for the offshore environment?
We are doing multi-purpose cranes, and offline activity cranes.
Engineer - Houston, Texas
May 22, 2017
A. Hi Sami. If it's a question of zinc plating vs. hot dip galvanizing, the galvanizing will be much thicker and much more corrosion resistant, and therefore probably more appropriate for offshore use -- but things can be electroplated with many other metals which may be appropriate for different applications. As a trivial and obvious example, a hydraulic piston must be hard chrome plated; you can't galvanize it. Further, if components can be painted, or zinc plated and painted, or galvanized and painted, this will probably be better than bare galvanizing in most cases.
You can get answers to highly specific questions here, but I'm sure you understand that nobody becomes a finishing expert, able to independently and knowledgeably specify finishes, from a few paragraphs of Q&A's :-)
Finishing has been my career for 50 years and in many cases I would not attempt to specify a finish without some specialized help :-)
Regards,
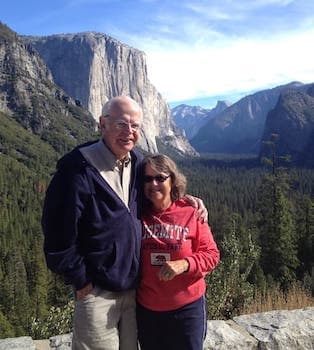
Ted Mooney, P.E. RET
Striving to live Aloha
finishing.com - Pine Beach, New Jersey
May 2017
A. Hot dip galvanizing would be less unsuitable than electroplating. There is a vast amount of literature available on what coatings are recommended for offshore use and merely coating them with zinc by any process is simply inadequate. Typical offshore use would have a base of hot dip galvanizing followed by two or more coats of paint.
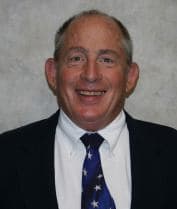
Tom Rochester
CTO - Jackson, Michigan, USA
Plating Systems & Technologies, Inc.

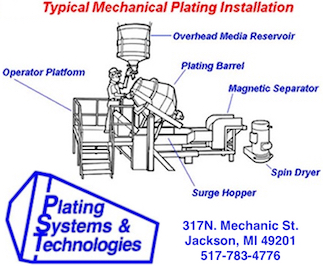
May 23, 2017
Q, A, or Comment on THIS thread -or- Start a NEW Thread