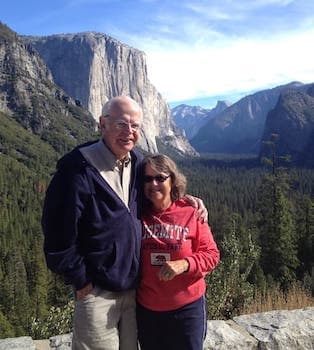
Curated with aloha by
Ted Mooney, P.E. RET
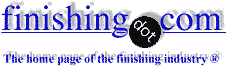
The authoritative public forum
for Metal Finishing 1989-2025
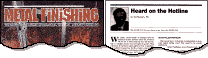
-----
Aluminum electropolishing: theories and practice
1998
Q. Theories of electropolishing aluminium are claimed to be well established with regards to the formation of a solid film on the Al-surface. This solid film formation (oxide) is claimed to be the reason for limitation of the current density (vs. time) when electropolishing Aluminium.
I find this quite hard to believe, with respect to an experimental program I have performed during the last year.
Among others I refer to The Surface Finishing and Treatment of Aluminum and its Alloys [adv: suggestions on AbeBooks, Amazon & eBay affil links] by S. Wernick, R. Pinner, P.G. Sheasby, 5.th edition, vol.1, ex.p. 64-68.
I personally believe in earlier theories based on diffusion layers.
Could anyone give me some feedback and/or information regarding research papers/articles/books/reports, etc., which scientifically motivates the solid film theory and limitation of the current density (vs.time) ?
Do you have any experience with solid film theory and/or diffusion layer theory?
Regards,
Jan Morten Soraker- Norway
A. I'm studying that right now in my research at the University. Although I've read Wernick and Pinner also, it seems their theories are very outdated. Their chapter on this subject offers about six explanations and doesn't seem to me to conclude with anything.
The Introduction to the High Temperature Oxidation of Metals ⇦[this on Amazon affil links] by N Birks and GH Meier seems to do a much better job of explaining the reactions and thermodynamics describing formation of oxides although they do not specifically address aluminum anodizing. Another source of information is a good text on Physical Metallurgy focusing on the lattice mismatch across the metal oxide interface. We are currently working with x-ray diffraction to determine the crystal structure of oxides. Aluminum oxide appears to be amorphous.
Dave Fairbourn- Sandy Utah
1998
A. Recently we published a paper dealing with Pattern Formation During Electropolishing of Al.
'Pattern Formation During Electropolishing', Physical Review B, V. 56, pp. 12608-12---.
You could find this paper on the Web at
http://www.nd.edu/~vyuzhako/papers/prb97/prb97.html
Sincerely,
Vadim Yuzhakov- University of Notre Dame - Indiana
1998
----
Ed. note Mar. 2014: Unfortunately that paper is no longer available on-line from Notre Dame, although it can be purchased from Physical Review B
Multiple threads merged: please forgive chronology errors and repetition 🙂
Aluminum Electro-polishing Magazine Article
Q. Hello All, recently in one of the industry related journals/magazines an article was published on the Electropolishing of aluminum. Has anyone read or know which publication that was in? Thank you.
Michael V [last name deleted for privacy by Editor]- Portland, Oregon USA
2001
A. Hi Michael. Maybe you're prescient because "Electropolishing of Aluminum" by K.B. Hensel appears in the August 2001 issue of Metal Finishing magazine, but I don't see any significant articles about electropolishing of aluminum in 2000 or early 2001.
Regards,
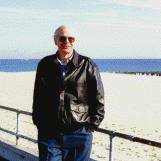
Ted Mooney, P.E.
Striving to live Aloha
finishing.com - Pine Beach, New Jersey
Electropolishing Aluminum Diecast Parts
Q. Is there an electropolishing process that is effective on aluminum diecast parts made from a 413 aluminum alloy? I'm looking for alternative to hand buffing which tends to be labor intensive and costly in a production environment.
John Koonceaerospace - Naples, Florida, USA
2001
A. Some companies, such as ourselves, do electropolish aluminum. Because it is a diecast, samples are advised.
Donna Nowak- Cleveland, Ohio USA
2001
Q. Hi,
I ask about the best methods for electropolishing of Aluminum diecast alloy. And the best alloy for diecast and electropolishing in the same time . I try with solution contain sulfuric, chromic and phosphoric acid but it is very good with pure Aluminum alloy -- but with Aluminum diecast it not good, and the part becomes dark after electropolishing because the content of alloy from SI and MN metals may be too much.
Thanks,
Aly Gomaa- Giza, Cairo, Egypt
2003
Alternating current for aluminum electropolishing?
Q. Hello,
We are working for an aluminum manufacturer and we need a process for ALUMINUM electropolishing. I've heard that it needs AC and a few seconds of immersion... Could anybody help us?
Many thanks.
Roux Bernard- MARSEILLE, PACA, FRANCE
2003
Q. Please give me the detailed procedure for electropolishing of aluminum. I have tried out with phosphoric and chromic acid , which was used as electrolyte. I was able to remove scratches but I was not able to get the mirror bright finish. Please advice the correct procedure in detail.
Thank you,
Anand Kumar R- Bangalore, Karnataka, India
2003
A. The only aluminium electropolishing solutions I know use dc currents. They generally operate at about 10A/dm2 (anodic) in hot baths. Processing times will depend on the solution, but generally 5-10 minutes will be OK. The aluminium will need desmutting after electropolishing and this is done in a hot chromic acid/phosphoric acid bath for up to 5 minutes.
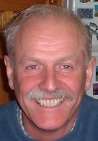
Trevor Crichton
R&D practical scientist
Chesham, Bucks, UK
2003
A. There is an article in the March 2003 issue of Plating & Surface Finishing Magazine talking about Electropolishing of various metals. It should give you some ideas.
S. Y. Yuen- Hong Kong, China
2003
Q. Please help me on a problem related to aluminium electropolishing. I have been trying for some time to electropolish high purity Al using the Battelle procedure ( mixture CrO3 + H3PO4+ H2SO4 at 0.14 mA/cm2 and 75-80 °C and I keep obtaining non-reproducible, mostly unsatisfactory results. The samples obtained are very bright, but there are numerous macroscopic pits. I obtain similar results with a mixture 1:3 HClO4 + ethanol (20 sec at room temp), with the pits even more dense. Please give me some advice - how can I get a shiny smooth surface.
Mariana CiureanuPolytechnic Univesity of Montreal - Montreal, Quebec, Canada
2003
Q. I'm working on a 6082 Al-alloy, and I've to electropolish it; I'm using A2 as electrolyte but I don't reach to obtain a good result looking to the pattern at the SEM using EBSD detector; can someone tell me which can be good parameters for the electropolishing?
Thanks a lot.
Mauro Spinsanti- Ancona, Italy
2004
Q. I am a student interested in basic polishing 6061 Al. Does anyone know of a basic process for this? Also the safe chemistry would be helpful. I am new to this so the more information the better. Thanks so much in advance.
Ted Eisenbachhomeowner - Mountain Top, Pennsylvania, USA
2004
Our Electropolish is Incompatible with Anodizing
2005Q. Hello All, Does anyone have any experience with a proprietary aluminum polish creating a "heavy" anodic film which is incompatible with Type II sulfuric Anodize?
I have been working with it for 3 years according to the data sheet recommendations and cannot get the supplier to understand the film that is contributing to a soft, impossible to seal anodize coating, amongst other problems.
The bath is advertised and sold as a "replacement" for bright dip, and has yet to yield acceptable results, and being new to the industry, I cannot convince them there is a problem, yet can document it and prove the problems by not going into the chemical before anodize, eliminating the same problems (the parts must be brightened before anodize and we don't want to put in bright dip).
Is there any desmut that will remove a Phos/hydroxyacetic/ethylene glycol based anodic film?
Note: chromic acid doesn't, neither does nitric acid! Both react with the film causing poor, discolored anodize.
Any ideas, since the vendor Is NOT helping!
Thanks Much.
Michael Voth- Sandy, Oregon, USA
Electropolish small aluminum brackets at home
Q. I need to know how to electro-polish some small aluminum brackets at home. They have been welded and have several places that can not be polished by mechanical means. Any light you could shed would be appreciated, i.e., proper voltage chemicals and percentages and time in solution.
Thank you,
hobbyist - Fairland, Indiana
2007
A. Hi George. Please realize that aluminum electropolishing is an industrial process that you should think about carefully before attempting if the setting is not industrial. But you can find all the info in The Surface Finishing and Treatment of Aluminum and its Alloys [adv: suggestions on AbeBooks, Amazon & eBay affil links].
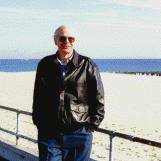
Ted Mooney, P.E.
Striving to live Aloha
finishing.com - Pine Beach, New Jersey
2007
Q. I am an Industrial Designer actively designing packaging for the Cosmetic Industry. I am interested in knowing if aluminum electro polishing is suitable for high speed screw machine components that are both functional and decorative. Specifically, can this finish be compatible with aggressive cosmetic fragrances. The first sample that I tested was immersed for twenty four hours and failure occurred as the finish orange peeled significantly.
Is there any ASTM data on this resulting performance? Are there differences in the process that would help to meet my mandate?
Thanks.
Product Designer - Saint Petersburg, Florida, USA
January 14, 2008
A. You need to anodize or at least lacquer after the electropolish. Top line lipstick tubes are anodized and dyed. Some cosmetic caps are just lacquered.
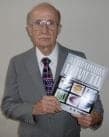
Robert H Probert
Robert H Probert Technical Services

Garner, North Carolina
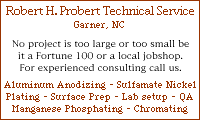
January 16, 2008
Q. I am electropolishing small foils of Al (~1mm thickness) using a solution of 70% vol. Phosphoric Acid, 30% vol PEG (Avg MW 400), and 3% weight poly-stearic. The solution temperature is 80 °C, agitated, and I am applying 20 volts. I originally used a phosphoric-sulfuric-nitric acid solution, but read that the addition of PEG and sterate controlled the polishing process better. I prepare every solution the same way, but the results are varied. At times I'll get great mirror finishes with no pitting, and other times I'll make a fresh bath and have tons of small pitting on the surface. I would also like to add that since this is such a small scale job the process goes on under a fume hood in a beaker [beakers on eBay or Amazon [affil links] on a hotplate being agitated with a stirring bar. I want to blame this on agitation, but can't prove it. Any help would be appreciated.
Ian McCueStudent - Maryland
February 21, 2009
Q. Hello;
What is the best solution and temperature and time and voltage for electropolish of 2024 aluminum.
Thanks for your help;
- isfehan, iran
September 4, 2009
A. Hi, folks. In addition to the technical article mentioned by S Y Yuen, and the responses offered here, you may wish to review the info on electropolishing of aluminum in the ASM Metals Handbook, Volume 5.
If you still need more help you might review the banner ad at the top of this page and consider contacting those people who have invested in researching the subject and are licensing their processes. Good luck.
Regards,
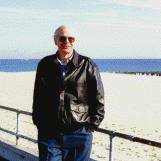
Ted Mooney, P.E.
Striving to live Aloha
finishing.com - Pine Beach, New Jersey
September 4, 2009
Q. Hi, could you help me?
What is the best solution, temperature and voltage for electropolishing of 6063 aluminum alloys before anodizing process to obtain high bright surface as a mirror after anodizing and sealing?
project - Ghazvin, Iran
December 29, 2012
Q. I need to electropolish 30 cm x 30 cm sheets of aluminum (1xxx series) to obtain a specular finish. We can easily do it on a lab scale with 2 cm x 2 cm coupons and achieve reflectivities of >90% and I wanted to achieve the same kind of reflectivities for the larger sheets. After doing some preliminary search, it seems to me that although there are a lot of equipment suppliers who provide equipment for large-part electropolishing of steel, there aren't too many for aluminum. I was wondering if there is any particular reason for that. Are the current requirements too huge or is safety (because of acid fumes or heating of electrolyte) a concern? Or is it just because there aren't too many people who need to electropolish large parts of aluminum?
RFQ: It would also be great if somebody could point me to an equipment manufacturer who supplies equipment for polishing aluminum at that scale (and ships internationally since I am based in India).
All help is appreciated.
Thanks.
- Mumbai, India
January 14, 2013
Small pieces electropolish at 25 V, but large pieces pull voltage down to 5 V or less
Q. We have a small set up for electropolishing, and don't generally have a problem because we only do it with small parts 4 x 6 inches x 1 mm thick. We use a 22 x 15 x 4 inch stainless steel tank as the cathode with plastic guards to prevent shorts. We went the with that SS tank to make sure cathode to anode ratio is always 3:1 minimum.
Our solution is 3-4 Gallons of 60% Phos with some surfactant at 120-130 °F for 5 minutes. We usually do 5A/25V or somewhere in that area to get the desired polished finish.
Recently we've been trying to do larger sheet 6xxx sheet metal aluminum, that's 13 x 10 inches x 1 mm thick, instead of the normal 4x4 but our voltage drops to almost nothing: from 25 V to .8-5 V. Sometimes if we pump the rectifier all the way up to 30 amps I can get 11-12 V. Of course there's no effect on the part, maybe some light indeterminable etching. Not sure what the problem is. When we go back to our smaller parts no problem.
Looking at Ohm's Law I guess the resistance would likely get too high with the size of the piece. My question is if that's the case, are there other methods/factors that influence resistance that we could try. We've tried cooling the solution, but below 100 °F it doesn't really polish even if the desired voltage is reached. And whereas when we start with 120 °F the Amps heat the solution, when we start at below 100, the amps never increase the solution temperature.
The piece lays flat, horizontal in the tank. And when we've held it vertical with just a small tip of the corner in the solution it polishes as our other products, so we think it's likely the size of the piece causing too much resistance being the problem. We've tried fewer gallons of solution which has shown to help somewhat, but is there anything else you can think of that we can try to reduce the resistance, if indeed that's the problem. We can't change the part size of course, so have to figure something else out.
Joel ToussaintMarch 15, 2015
A. Hi Joel. A large piece doesn't increase the resistance, it decreases it. Although we don't have enough data to know exactly what is happening, maybe your rectifier might be set at automatic current control, which causes the voltage to drop because you're holding the amperage constant while reducing the resistance.
My general impression is that your rectifier can't electropolish the larger parts -- either because it isn't big enough or because it's malfunctioning (single phasing?) and can't deliver the rated amperage. Good luck.
Regards,
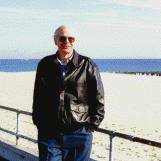
Ted Mooney, P.E.
Striving to live Aloha
finishing.com - Pine Beach, New Jersey
March 2015
A. Just a quick question. You mentioned the alloy on your larger pieces, but didn't mention it on the smaller pieces. Are your smaller ones perhaps 5xxx or 3xxx alloy? Those 2 alloys electropolish much better than the 6xxx alloy. That may also account for your varying voltage as well.
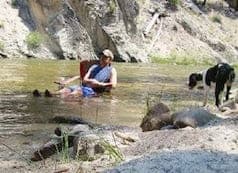
Marc Green
anodizer - Boise, Idaho
March 16, 2015
A. Joel
Electropolish is typically controlled by current density. Stainless steel current densities are often 200 - 300 amps per square foot, and higher. Your power supply may be adequate for your smaller parts but might be coming up short on the larger parts. That's why a corner dipped will polish nicely but not the entire part.
A 4x4 part will have 32 sq.in vs. 260 sq. in. for the 13x10. If your 4x4 runs at 5 amps, you would need almost 40 amps to polish the larger part. You might also need to look at your anode:cathode ratio.
- Colorado Springs, Colorado
March 16, 2015
Q. Dear all,
Do you have anybody that use electropolishing process before anodizing for especially 6 meters and more profiles?how is performance it?what is the advantages and disadvantages and can we get brighter as we compare normal polishing?
engineer - turkey,sakarya
June 22, 2016
Q. Good afternoon.
I have a company of electropolishing of aluminum. I am electropolishing some pieces of aluminum; the formula that I use is: I put them in a solution of 85% phosphoric acid to 45 °C with 10 volts for 10 to 20 minutes, then I sack them well and I put them in hot water, the pieces are quite bright, very good results.
The problem I have is that when the pieces are dry and people touch them with their hands, white spots appear.
If someone could give me some advice I would appreciate it a lot.
- Valencia Venezuela
April 5, 2017
April 7, 2017
A. Hi Andres,
I think the white spots are due to an oxide film left after the electropolishing. The surface looks OK after polishing but when touched the residual oxide breaks up and scratches the surface and leaves white marks.
The electropolishing process produces an oxide film which continuously forms and dissolves: it is a key part of the process. Now, when you stop the treatment any remaining oxide must be removed. You can do in a number of ways:-
1) Lower the voltage: less oxide will be formed.
2) Increase the temperature of the electrolyte: the oxide will dissolve more quickly.
3) At the end of the processing, allow a short time in the electrolyte with the power off: any residual oxide can dissolve.
4) Introduce a separate deoxidising stage to remove the oxide layer. 5% sodium hydroxide should do.
When the oxide is being removed there will be no obvious chemical reaction. Once the oxide has dissolved, the aluminium begins to gas as hydrogen is formed. This is the point to look for. Of course, if you allow the gassing to continue the aluminium will start to etch and you will lose your polish! However, if properly done and controlled, the loss is negligible.
Harry
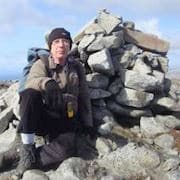
Harry Parkes
- Birmingham, UK
Friend Harry, thank you very much for your response. This week I will do the test according to your indications and I will be notifying you how the results came.
Thank you very much.
- valencia venezuela
September 19, 2017
Q. Hi all,
I run an aluminum anodizing bright dip line. In the last few months we've been struggling with parts that come out of the bright dip with "shiny ends." The parts come out very good looking, with the exception of the end of the part (always at the contact point between the aluminum part and the titanium contact point of the rack) being extremely shiny in comparison; giving it an uneven- though specular- appearance. I believe I may be inadvertently electropolishing my parts in this localized area. The tank is made of stainless steel with bright dip solution of phosphoric/nitric with the parts being submerged about 2 minutes. The problem appears to go away and leave incredibly good results when I insulate the crane hooks (that pick up the rack) with rubber (We leave the hooks on the rack during processing for safety reasons). The problem then comes back when the rubber gets saturated with water. The problem also goes away when I insulate the rack/part contact point with PVC or switch to aluminum rack clips. It's fascinating, but a real pain. My electricians cannot find any stray current in the system that would make this happen, but everything points to a small, unfinished, localized electropolishing reaction at the aluminum/titanium contact point. I was hoping someone could point me to additional reading material (I've read all of the material on this thread so far) or recommend a consultant in the Midwest US. I would greatly appreciate it. Any feedback would be appreciated. Thank you.
Aluminum Anodizer - Grand Rapids, Michigan, USA
June 11, 2018
Ed. note: This RFQ is outdated, but technical replies are welcome, and readers are encouraged to post their own RFQs. But no public commercial suggestions please ( huh? why?).
June 13, 2018
Q. I'm interested in Scott's question as well, not quite for the same reason though. We also seem to be getting some type of stray current though our hoist. An operator will occasionally receive what appears to be a static shock while the part is being held on the hoist hook while the operator is spraying the part off with a DI water hose/sprayer. Happens while the operator is steadying the part with one hand, and spraying the part off with the other. The operator is wearing gloves. It's intermittent, but happens enough to be annoying. I've had the maintenance department go over the hoist thoroughly, and like Scott's situation, can't find any stray currents coming from anywhere.
I'm considering coating our hoist hook with a thick ECTFE coating to possible eliminate the issue, but I am interested in the source if anyone else has had a similar issue. This is on an anodizing line, and the only time it seems to occur is the post anodizing rinse. I can't help but wonder if the part itself is somehow storing a charge after anodizing … is that possible?
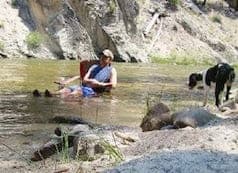
Marc Green
anodizer - Boise, Idaho
Q, A, or Comment on THIS thread -or- Start a NEW Thread