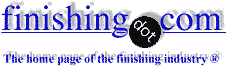
-----
Passivation
1998
Have read with interest your series of letters (FAQ - passivation of stainless steel). We seem of late to be having more than our share of challenges with this particular process. We are a job shop, and get all types of alloys, but particularly 303, 416Se, and 420 seem to be problematic. We have a strong alkaline soak cleaner, and then will run a rabbit or two parts through the designated solution (either inhibited with dichromate, or nitric solution only per ASTM ASTM A380 ). Recently in some fairly polished 303 parts, we ran two rabbits...ok results...then the first rack of parts came out etched...30 minute time in the dichromate inhibited bath was what was done. Anyway, there are lots of problems out there it would seem.
An industry rep I talked to said that on the west coast there is a lot of cheaper s/s alloy showing up from China, and that it has been a problem for other finishers as well. Question...how does one really interpret ASTM A380 ? For example, 30-60 minutes is a pretty wide window...70-140F is a pretty wide window...20% -40% HNO3 is the same, as well as 2-6% dichromate. It seems that any one of these factors can have a significant effect on the part...especially difficult or substandard alloys. If you soak clean, then go in the solution for five minutes, and test the parts with copper sulphate ⇦ on eBay or Amazon [affil links] solution...no free iron evidenced, isn't that sufficient? or, to "meet the spec" do you have to use at least the minimum concentration, time, temp. etc. for the category you need to use for the designated alloy?
Also, where do Citrate solutions, phosphoric electroclean or electropolish, or even some of the chemical polish solutions for s/s fit in? They are not officially passivation treatments according to the spec., yet many o.e.m.s or captive shops use them because they achieve a passive surface. Are there other possible contaminants (other than free iron) that can pose a problem in the passivate solution? What about synthetic or para-synthetic cutting fluids/coolants? We only have a problem with the one customer's parts.
Any help would be appreciated! You can post this on the hotline...perhaps someone else out there has come across something that will keep us all from frying more parts in what is becoming a real bothersome process to deal with.
Sincerely,
Mike Solvie1998
I have had plenty of problems over the years with 303 stainless. I believe that the sulfur in the alloy creates a sort of galvanic cell. The best results I ever had were when the part is completely oil-free, and DRY, before it is put in the bath. Use a non-metallic fixture to hold the part.
Look at ASTM A967-96 to find the citric acid passivation.
Good luck...keep those parts oil free before they go in the bath!
Dave McKayDear Mike:
Sounds like your experience is "normal". This has been posted before, but I think the best thing to do with 303 is a hot soak in NaOH before passivation to get rid of the MnS inclusions, etc. Then Passivate according to ASTM A967 for best results. This allows you to use either nitric or the state of the art citric formulae for the best results.
The citric systems allow a lot safer use of some of the poorer 400 grades without danger of an exotherm. There are excellent formulations available on the market that give improved results over the old nitric formulae, without the hazards and costs.
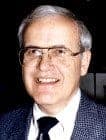

Lee Kremer
Stellar Solutions, Inc.

McHenry, Illinois
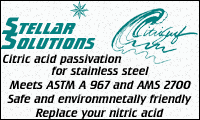
1998

this text gets replaced with bannerText
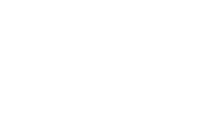
Q, A, or Comment on THIS thread -or- Start a NEW Thread