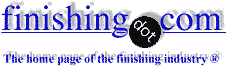
-----
Surface Finish Cross Reference Charts
Q. When machining or grinding parts, surface finish is a controlling dimension. When working with German prints, Rz is used to describe surface specifications. DIN standards. Can anyone recommend a cross reference sheet showing Rz vs. Ra vs. RMS ? Ra & RMS are easy to find.
Thanks in advance.
machinery co. - Warrenville, Illinois
2003
A. Seems like a popular question. We get similar questions about once a month. First Rz and RMS are the same thing; however, they are measured differently. Rz is a result of ISO 9000 standards and specifically is measured over 5 peaks and valleys at 10 points on the part. RMS does not specify these factors.
Ra to RMS is a variable ratio that depends on the manufacturing process and can vary from 1.11 to 2.10.
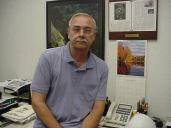
AF Kenton
retired business owner - Hatboro, Pennsylvania
2003
A. We recently purchased a surface finish tester and I was informed that RMS & Rq are the same rather than RMS & Rz?
Tony Pottsmfg - Warren, Michigan
2007
A. Tony P.,
While my knowledge of mechanical finishing does not rival Mr. Kenton's, I believe that he has made an error, and that you are correct that it is Rq rather than Rz which is essentially the "same thing" as RMS.
One of the quickest but clearest descriptions of the differences between Ra, RMS, Rmax, and Rz is at www.ptonline.com/articles/200403fa3.html
Then you may want to jump to letter 9524, which explains the mathematical relationship between
RMS and Ra pretty exhaustively. They can't be converted because they don't measure quite the same thing, but they do track each other such that pretty good approximate conversions are sometimes possible, as Mr. Kenton has said. Good luck.
Regards,
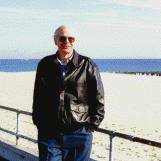
Ted Mooney, P.E.
Striving to live Aloha
finishing.com - Pine Beach, New Jersey
Q. How to convert 1.86 Ra into Rz value?
Milind D ShopeshwarkarManager - India
August 7, 2008
Q. What exactly is Rmax and RMS value? Is Ra and Rz are same in meaning i.e., former represents ISO std. and latter one for DIN std.? How these values are calculated theoretically which is implied to the checking instrument?
Sachin RohatgiAutomobiles - Sahibabad, Uttar Pradesh, India
2003
A. Here is a handy cross reference for you to use. It shows the difference between the standards.
www.clearlakefiltration.com/pdf/surface_finish_chart.pdf#search='surface%20finish%20RMS%20chart'
- Greenville, South Carolina
2006
A.
Sachin,
Rmax is a bit different and you should not attempt to approximate it in terms of the other measurements because it is meant for a different purpose. It is essentially the deepest of five adjacent peaks and valleys, and tends to be used in electroplating and buffing, not as a measure of overall roughness, but as an indication of whether there are visible scratches on the surface.
Miland,
Rz is the most complicated of all because it has had three different definitions over the years :-(
The approximate conversion between Ra and Rz is well explained at http://www.mmsonline.com/articles/1102gage.html and you will probably find it a bit disheartening that the "conversion factor" will depend upon in which direction you are converting.
If you are controlling via Ra but your customer will be measuring in Rz, you would multiply your Ra by more than 7.6 and as much as 20 to guess at the Rz value he will read.
The point of all this is that it's fine to "convert" one parameter to another to give yourself an overall feel for what another roughness scale is like, but they measure different things so there is no such thing as a real conversion. If your customer is going to measure a different parameter than you, you risk failing his inspection unless you apply a very big safety factor in making your "conversions".
Regards,
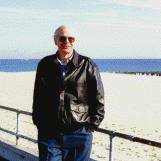
Ted Mooney, P.E.
Striving to live Aloha
finishing.com - Pine Beach, New Jersey
Q. Is there any correlation between Ra & Rmax while measuring surface roughness?
Chandrashekhar Pprocess engg. - dewas (M.P.) India
June 20, 2009
A. Hi, Chandrashekhar. We have appended your inquiry to a thread which hopefully answers it. There is some small degree of correlation, similar to the fact that tall people will tend to weigh more than short people. But there is no exact relationship. If I tell you that one of my sisters-in-law is 5' 8" tall and the other is 5' 2", you might assume that the taller is the heavier, and the odds would be in your favor, but you might be wrong :-)
Regards,
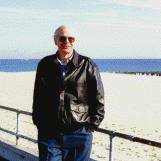
Ted Mooney, P.E.
Striving to live Aloha
finishing.com - Pine Beach, New Jersey
June 22, 2009
Q. The material we purchase comes in with an inspection sheet measuring Ry. We only have the ability to measure Ra and cannot afford to purchase a machine to measure Ry. Is Ry the same as Rmax, or Rz, the max. peak to valley height? Is there an equation to approx. convert from Ry to Ra? Thanks.
Ron Homolaktubing finisher - Marion, South Carolina
August 3, 2009
A. Hi, Ron. As you can see, we appended your inquiry to a thread which partially answers it. Yes, it is my understanding that Ry is the same thing as Rmax.
But that you cannot convert Ry to Ra and vice versa. Let's look at it from a plater's perspective: Nickel plating will level out a rough polished surface and generate a nice, smooth, mirror surface, but is incapable of filling in a severe scratch -- in fact, it will only highlight it. So a plater would like to reject any parts with a deep scratch rather than wasting money processing parts that will be defective. The Ry value tells him how deep the worst scratches are.
Ra, the average roughness, may be important for a coefficient of friction application, for lubrication situations, for general appearance without finishing, and other reasons, but it doesn't tell the plater what he needs to know, and he cannot calculate from the average roughness what the deepest scratch is.
Regards,
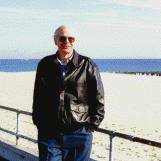
Ted Mooney, P.E.
Striving to live Aloha
finishing.com - Pine Beach, New Jersey
August 4, 2009
A. An example comparator:
Ra 116 (inches) = Ra 2.95 (metric) = Rmax 374 (inches) = Ry 9.5 (metric)
per Mitutoyo precision reference specimen.
- Beloit, Wisconsin
November 11, 2009
Q. Have a slider under a rocker arm in an engine. One side has a sphere machined into the top and a flat surface on the bottom. Is is made currently by a German company and we are shopping for a U.S. supplier and all have a problem with the Rz6.3 finish in the sphere and the flat bottom. We sent new parts for them to analyze to convert to Ra but they came back with Ra to Ry which a reply stated its used by platers. I don't think we want a glass smooth surface rather a little rough to hold an oil film. I'm surprised that profilometers won't make the conversion.
Brad Beeengineer - Livonia, Michigan
May 3, 2011
A. Hi, Brad.
Of all of the confusing and almost countless surface finish roughness specifications, Rz is the worst because there are 3 different Rz scales and meanings. As noted in Alex Tabenkin's excellent article "To Each His Own Parameter" in the June 01 issue of Quality Digest (www.qualitydigest.com/june01/html/surface.html): "If your print calls out an Rz value with no further explanation, warning bells should go off. A time bomb may be ticking."
As a starting point you need to find out what standard it is that these parts are to be measured by. It's probably an ISO/ASME standard, but that's just guessing.
Regards,
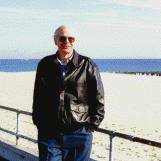
Ted Mooney, P.E.
Striving to live Aloha
finishing.com - Pine Beach, New Jersey
May 4, 2011
Q. Hello. I work for a industrial engine MFGR and they just supplied me with a Mitutoyo SJ-400. I need to measure surface roughness on cylinder block deck and cylinder head deck.
What is the best measurement to use Ra, Ry, Rz, Rq?
I am just a mechanic and not a machinist so please bear with me I am new to this.
- Bristol, Virginia
September 17, 2013
A. Hi Glen. There may possibly be an "accepted" or "conventional" scale to use for this application, and another mechanic or machinist from that industry may tell us both ... but I doubt it. There is some reason you are measuring this roughness, so you need to find out who wants to know the roughness and why (or at least what scale they need it in). Good luck.
Regards,
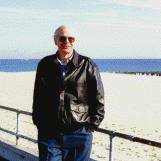
Ted Mooney, P.E.
Striving to live Aloha
finishing.com - Pine Beach, New Jersey
September 19, 2013
A. How do you intend to measure roughness? If you have a profilometer, that normally has settings to measure Ra, RMS and more. If the parts you are making are for a customer, there are usually surface finishing specifications.
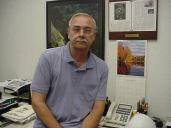
AF Kenton
retired business owner - Hatboro, Pennsylvania
September 20, 2013
Q. Hello All, I have come across a print that has a callout of a surface roughness less than 1.6 MICRONS after machining. My question is what would be the conversion to Ra/ µin. I'm using a Mitutoyo SJ-201. I wasn't sure if it as simple as switching to mm on the mm/inch function? Can anyone help?
E. Rich- Boxborough, Massachusetts U.S.A.
December 30, 2013
A. Hi E.,
Per Max T's posting of November 11, 2009, Mitutoyo says "Ra 116 (inches) = Ra 2.95 (metric) = Rmax 374 (inches) = Ry 9.5 (metric)".
Unfortunately, as far as I know it would be a leap of faith to assume "surface roughness" implies Ra reading.
Regards,
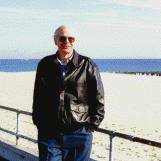
Ted Mooney, P.E.
Striving to live Aloha
finishing.com - Pine Beach, New Jersey
December 2013
Q. With all the "Global Manufacturing" going on, why is there not a "standard" means of measuring surface finish? Why does it have to be so confusing??
Greg DeBlaay- Caledonia Michigan USA
August 21, 2015
A. Hi Greg, I sympathize completely! Every time I want to try to answer a posted question on this subject I have to sift through it all again and try to remember it just long enough to answer. The following month none of it is in my memory banks and I have to start all over again :-(
But actually, the thing is, different types of roughness, not just different degrees of roughness, are significant for different applications. In my field of electroplating, for example, nickel plating can smooth out and shine up a roughly polished steel surface, covering up thousands of very tiny scratches but ... the plating will emphasize rather than conceal deeper scratches. So we'd like a roughness scale that deals with how deep is the deepest scratch, so we know whether the surface is platable. For friction applications the deepest scratch may not matter at all, and we might be entirely concerned with the average depth of the scratches; how much oil weeps paste an o-ring might be most predictable based on some other roughness parameter; visual shine and specularity might be relatively unaffected by surface irregularities of a certain pattern, etc. I think Einstein was working on a Grand Unified Theory of surface roughness :-)
Regards,
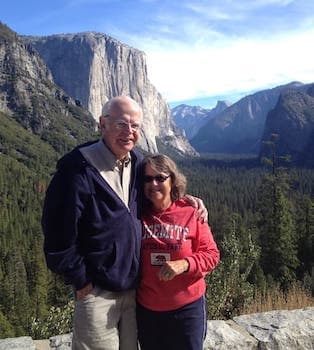
Ted Mooney, P.E. RET
Striving to live Aloha
finishing.com - Pine Beach, New Jersey
August 2015
A. Greg,
Several years back, one of the guys in one of the ASTM steel subcommittees I'm on got it in his head to put together some sort of surface finish standard. A few fruitless task group meetings later, he concluded that the issue was too complex, nobody there had any viable ideas to make it work, and he decided if somebody was going to pull it off it wasn't going to be him.
If somebody else feels up to the challenge, ASTM is always open to introducing a new standard. However it does seem like the sort of thing that would have happened already if it were at all practical.
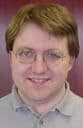
Ray Kremer
Stellar Solutions, Inc.

McHenry, Illinois
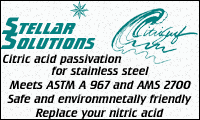
August 24, 2015
FYI It seems as if different industries require different parameters to correspond to their needs or functioning of the end product. I came up with a way to evaluate surface finishing removal equipment; however, that doesn't address the needs of a universal code for roughness or smoothness. You would think that groups like SME, ASME, etc would try to address the problem.
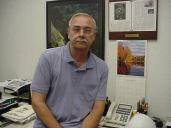
AF Kenton
retired business owner - Hatboro, Pennsylvania
August 24, 2015
Q, A, or Comment on THIS thread -or- Start a NEW Thread