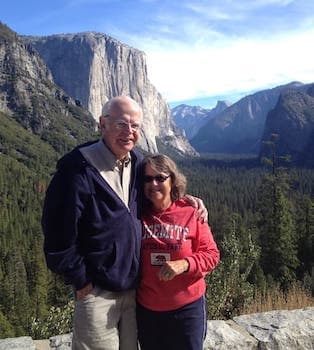
Curated with aloha by
Ted Mooney, P.E. RET
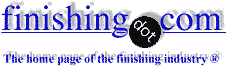
The authoritative public forum
for Metal Finishing 1989-2025
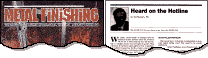
-----
RMS vs Ra
Q. Hello Mark. Your comment is clear. I want to ask you a question. Could you please help me?
In these days, I'm seeing Ra or Rz values in all technical drawings.
I'm working in a foundry and casting machine products. Sometimes I have to measure rough cast surfaces. But my profilometer is measuring until Ra 12.5
Do I need to buy a new profilometer to measure surfaces roughness than Ra 12.5? Or do you think microfinish comparators will be enough for this?
Technical Designer - Izmir, Turkey
February 28, 2022
Hello Sefik --
I'm not sure what your customer needs.
Since you are trying to measure a cast surface, I assume it is NOT a bearing surface.
Cast surfaces usually have only requirements to look good and be free of defects that would weaken the casting (cracks, sand holes, etc)
For appearance purposes, comparison samples would be sufficient.
. . . along with text that listed other forbidden defects.
If the customer actually put a microfinish symbol on the cast surface, it sounds like a design error.
If the customer calls out a default finish spec for a part, it should apply to machined surfaces, only.
It sounds like your profilometer is not able to measure a surface roughness greater than Ra 12.5.
First verify what the customer really needs.
If you need to measure a VERY rough surface, you will need a different profilometer.
Good Luck!
- now in Eureka Springs, Arkansas, USA
⇩ Related postings, oldest first ⇩
Q. What does the RMS means? How can we convert 3.2 - 6.3 RMS to Ra value? Please reply immediately.
Thanks,
- India
2001
Hitesh,
Term RMS refers to the mathematical Root Mean Square which is an average of peaks and valleys of a materials surface profile. Ra stands for roughness average.
Ra is a average of only peaks; therefore, to get an Ra, multiple your 3.2 to 6.3 by 2 to get 6.4 to 12.4 Ra.
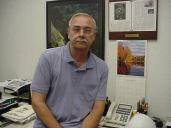
AF Kenton
retired business owner - Hatboro, Pennsylvania
2001
Ed. note: This thread has continuing errors so it was very hard to follow. We went back and added this anachronistic running commentary based on clarifications by subsequent readers:
RMS and Ra measure two different things, so there is no actual conversion factor. But for sine wave roughness the factor would be 1.11, and for many real world metal working processes the factor approximates 1.25. Later readers also noted that RMS is usually expressed in microinches whereas Ra is usually expressed in microns; but this is not universally true either, which adds to the confusion :-)
I thought I should point out an error in your RMS to Ra conversion. The ratio is not 2:1, but 1.11:1 This is a significant difference. An RMS of 60 µin would be an Ra of 54 µin, not 30 Ra. You may want to check/verify your source for the ratio as your response prompted me to double-check my own numbers. I am afraid you will find that I am correct.
Please let me know if I misunderstood your comments.
Still a nice website for information on finishing. Keep up the good work.
ceramics - Golden, Colorado
2003
I agree. RMS is generally accepted to be about 11% higher than Ra. Also note that outside of the US values are generally expressed in microns : 1 micron is equal to 40 micro-inch.
Regards,
electropolishing - London, England
2004
Ra value means roughness average in microns whereas RMS means root mean square value in micro inches so if you know the conversion from mm to inches you have the answer with you..for e.g. 0.4 Ra value conversion is 16 rms.
Charuhas- India
2004
----
Anachronistic running commentary: This is apparently incorrect because Charuhas has omitted the 1.11 conversion factor, and the RMS should therefore be 17.8
2006
Here is how I convert 0.1 µm Ra to RMS
1. step one: convert 0.1 µm to microinches
0.1 µm-.004 µin
2. step two: use the formula RMS=Ra/1.11
RMS=.004/1.11 which equals to: .0018 µin
3. step three: Write the result in standard engineering form:
.0018 µinRMS is usually written as: RMS 18
So here is completed plan on how to convert Ra to RMS (and back)
Good luck
- Orange, California
----
Anachronistic running commentary: This is incorrect in step 1 because 0.1 µm is not .004 µin; and in step 2a because the conversion factor is upside down; and in step 2b because of arithmetic error anyway. Correcting these errors: 0.1 µm = 4.0 µin; multiplying by 1.11 gives 4.4 µinRMS.
There is no formula to convert Ra values to RMS values or vice versa because the numbers are depending on the type of profile. The conversion factor 1.11 is valid only for sinusoidal profiles. The ratio for saw tooth profiles is closer to 1.17 and the ratio for random profiles can be as high as 1.2!
Fred Couweleers- Trondheim, Norway
2007
January 25, 2008
A brief response to the Peter from Orange California posting:
It appears there was a unit/conversion error at Step 1.
0.1 µm = 0.1 micrometer = 0.1 micron = 100 micro-millimeter
(µ-mm)
Author appears to have divided 0.1 by 25.4 (to get 0.004), but that's the conversion from mm to in. Conversion from meters to inches would be to multiply by 39.37.
Step 2 also appears to have a division error: .004/1.11 = 0.0036 (not 0.0018)
It would seem simpler to convert 0.1 µm Ra to 0.11 µm RMS, then to 4.37 µin RMS.
- Los Angeles, California
----
Anachronistic running commentary: This answer and method appears to be correct, but in commenting upon the division error in step 2, Jon does not note that it should have been multiplication rather than division :-)
May 28, 2008
Actually, this entire thread seems to be riddled with errors.
Ra is in microns
RMS is in microinches
This is the best that I can figure:
RMS=(Ra/.254)*1.11
However, 1.11 is just a theoretical relationship, and there really is no mathematical relationship, so the actual value varies by process. For most processes, 1.25 is the "best guess".
www.qualitydigest.com/june01/html/surface.html
- Austin, Texas
----
Anachronistic running commentary: Thanks Sean, but let's underscore the word "entire" -- because your '.254' should be '.0254' :-)
Q. After reading all this, I am now completely confused. We have a part that calls for a 63 Ra finish on an English drawing and want to check it in RMS. Anyone know what the equivalent RMS value is?
ed gard- south bend, Indiana
July 25, 2008
C'mon now, Ed. You can't read a dozen postings in a row, each pointing out the errors in the previous, while having larger errors themselves, without getting confused? :-)
We've gone back and added a running commentary addressing the errors in the postings, so it should be clearer now. Your Ra is apparently in microinches, not microns. So the RMS you measure should probably be between about 1.11 and 1.25 times the Ra value that you quote.
Some subjects require studying in tutorial format. For example, you can't reasonably ask "How do you design a jetliner" or "How can I safely perform an appendectomy" in an internet posting; you need to take courses and read books. It's beginning to look like surface profile measurement may be a little too complicated for us to learn through buckshot pattern Q&A in an internet forum :-(
Regards,
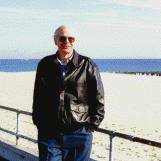
Ted Mooney, P.E.
Striving to live Aloha
finishing.com - Pine Beach, New Jersey
July 26, 2008
Q. Hi gentlemen,
could you help me to calculate 300-400 RMS to be Ra?
Sorry but I don't full understand what you guys talking from beginning, I'm not so familiar with inch.
Coating job - Karawang-Indonesia
October 20, 2008
1. Formula
RMS (Microinch)=(Ra/.0254)*1.11 (Micrometer)
2. 300 RMS=6.9 Micrometer
400 RMS=9.2 Micrometer
- Daegu, South Korea
November 16, 2008
Q. What would a 250 Ra equal in RMS? Please respond. Need help NOW!
Thanks very much.
Calibration Tech - Temple, TEXAS
May 21, 2009
Hi, Richard. We appended your inquiry to a thread that explains it all, including the fact that there is no exact conversion because they are measuring different things. Tall people will on average weigh more than short people, but you can't apply a conversion factor to determine a person's weight based on their height.
But for a sine wave profile, with RMS measured in microinch and Ra measured in micrometer, RMS = (Ra/.0254)*1.11, so an Ra of 250 micrometer would equal an RMS of 10,800 microinch. However ... this is so ludicrously rough that it is completely improbable. It seems far more likely that the 250 Ra you've given us is 250 microinches, not 250 micrometers -- equating to an RMS of 277.
Regards,
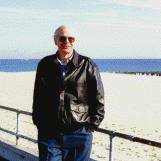
Ted Mooney, P.E.
Striving to live Aloha
finishing.com - Pine Beach, New Jersey
May 22, 2009
Q. I have to offer a part in aluminium oxide ceramics. The surface roughness indicated by the customer is "16 RMS". We indicate the surface roughness in Ra only. Can the RMS value be converted into Ra? If yes; what is 16 RMS in Ra? Appreciate any help.
Andrea Roposemployee - Mannheim, Germany
September 15, 2009
Q. How to control Ra Value by programming the Feed and Tool Nose Radius calculation? Basically I want to know what is the formulae?
I want to understand the entire concept of Ra and RMS. I would also like to know if there are separate symbols for both. Also in some drawings the numbers are 16, 32, 64 etc whereas in some drawings they say 0.5, 1.2, etc. Can anyone help me to identify the differences?
JACOB
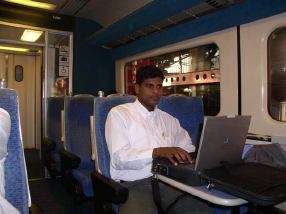
Jacob Ebanezer
forging & turning - Jamnagar , India
October 2, 2009
Q. Is there any specification to use either Ra or Rz to any particular form of surface?
Kindly clarify on which type of surfaces Ra should be used and similarly Rz
automotive - coimbatore, India
January 19, 2010
Q. Hi,
For what purpose Ra value should be calculated?
How to check the Ra value?
Kindly, guide me about this for tube surface finish in tube industry.
regards,
- Hyderabad, Andhrapradesh, India
December 14, 2011
Hi, Mahesh.
Ra is not to be calculated, it is to be measured with a profilometer .
I am sorry but I do not really understand the question. Are you asking why "Ra" measurement specifically is important (as opposed to Rmax, Rz, and RMS)? Or are you asking why should tubes be of a uniform, predictable smoothness rather than of random roughness? Whether the tubing be plated, painted, machined, used as a bearing, or as a clutch or brake surface, or whatever, there are 101 reasons for needing a consistent finish. Even operations as simple as writing on the tubing with a marker, or sticking an adhesive label on it will have different results on a very rough surface than on a very smooth one. Good luck.
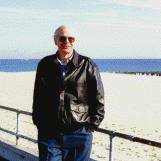
Ted Mooney, P.E.
Striving to live Aloha
finishing.com - Pine Beach, New Jersey
December 14, 2011
Ra roughness average is the main height as calculated over the entire measured length or area. It is quoted in micrometers or micro-inches. For 2 dimensional computation:
Ra = 1/n * SUM(ABS[Zi-Zmean] from I = 1 to n
The root means square(RMS)average is precisely that: the square root of the average height deviations from the mean line/surface squared.
RMS = SQRT[ 1/n* SUM(Zi-Zmean)^2 ] from i=1 to n
These are for 2 dimensions
- Austin, Texas USA
January 19, 2012
RMS= (RA/25.4)*1000
Bye,
SOLAI
- singapore
October 18, 2012
Hi Solai. Thanks, but sorry, that's not correct. But it is a proper conversion from micrometers to microinches. So let's rewrite it to
Ra [µin.] = (Ra[µm]/25.4)*1000
Regards,
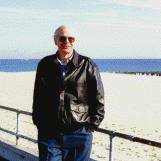
Ted Mooney, P.E.
Striving to live Aloha
finishing.com - Pine Beach, New Jersey
October 19, 2012
March 13, 2013
A. RMS and Ra are based on different methods of calculating the roughness. Both are done with a profilometer, but the profilometer calculates the roughness differently for Ra and RMS.
Ra is the arithmetic average of surface heights measured across a surface. Simply average the height across the microscopic peaks and valleys.
RMS is a Root Mean Squared calculation. That means you:
1) measure height across the microscopic peaks and valleys.
2) calculate the SQUARE of each measurement value
3) calculate the MEAN (or average) of those numbers (squared)
4) find the square ROOT of that number
The RMS is sensitive to the BIG peaks and valleys.
Ra is not.
Both numbers can be expressed in metric or inch.
RMS was more popular 40 years ago when I learned to measure surfaces. (most US industry still worked in inches.) Those old inch drawings specify RMS.
Ra is more commonly used today. (now most US industries work in metric) So they specify Ra in metric.
Both Ra and RMS can be expressed in metric or inch.
Inch/metric conversion guides are available on the web.
But there is no reliable way to convert between Ra and RMS.
It's only an estimate based on guessing what the shape of the microsurface looks like.
Read the user guide that came with your profilometer. Most of them can switch between RMS and Ra. Measure the part the way the drawing calls for.
- Watertown, Wisconsin, USA
"Measure the part the way the drawing calls for."
Bravo, Mark! You are absolutely correct.
Regards,
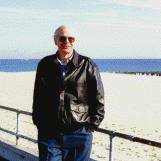
Ted Mooney, P.E.
Striving to live Aloha
finishing.com - Pine Beach, New Jersey
January 2016
A. Hi People, I'm Tony from Taylor Hobson do Brasil.
RMS is the same as Rq, according to the Taylor Hobson definition:
Mathematically, Rq is the Square Root of the Mean of all the "Z" Values after they have been Squared.
Taylor Hobson do Brasil - São Paulo, SP, Brazil
April 25, 2017
Q. Given that RMS is more sensitive to big peaks and valleys would it not be a better number to prescribe than Ra? If it is better, then why is industry moving to Ra? If I am supplying machine drawings, should I spec it out in Ra and not RMS?
I'm in the US and all manufacturing to be done in the US. All dimensions are in inches.
Design Engineer - Lafayette, Indiana
July 9, 2021
A. Hi Bryan. Surface metrology is not my field so I can't tell you which system you should use on your drawings or whether the industry is going the way you think it is or why. But I can comment from the point of view of electroplaters why there are many different measurement systems: electroplating does a good job of leveling out very shallow scratches but only emphasizes & magnifies deep ones. So we are more concerned with the deepest scratch than any sort of average. I assume that for other applications different measurement systems are better than others for judging the suitability of the finish.
Luck & Regards,
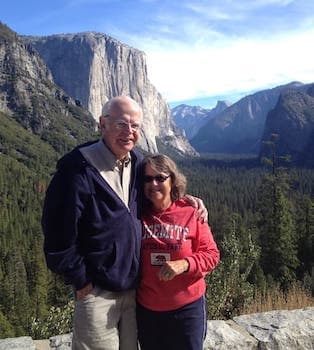
Ted Mooney, P.E. RET
Striving to live Aloha
finishing.com - Pine Beach, New Jersey
Q, A, or Comment on THIS thread -or- Start a NEW Thread