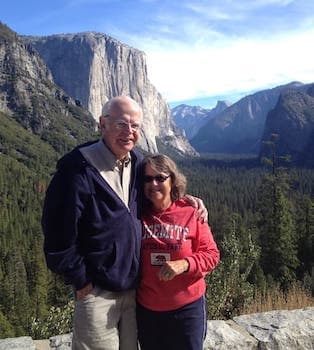
Curated with aloha by
Ted Mooney, P.E. RET
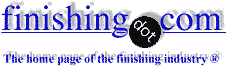
The authoritative public forum
for Metal Finishing 1989-2025
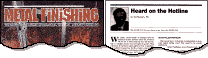
-----
How to compare ASTM B117 Salt Spray and ASTM B368 CASS Test?
Q. Hello everyone!
I have a question regarding:
1) Is SST or CASS defined for PVD coating life? PVD is done over nickel plating and SS [stainless steel] base material parts. Is SST test right for that?
2) As per many experts & standards CASS test for nickel, chrome and decorative parts. But from last 1 year we are doing SST for that -- is it right or wrong? Currently our supplier mainly fails to survive at 96 hours. Can we go for CASS test? Then how many hours is survived in CASS test?
3) We are doing electrophoretic lacquering over PVD & Ni plating so my question is: any SST test available specially for lacquering?
Surface coating - pune
January 20, 2024
A. Hi Vishal. The buyer decides the testing requirements. It isn't completely clear to me where you fit into the supply chain, but it sounds like you are the buyer, which makes you the decider.
Your first task is to decide whether the service condition is mild, moderate, severe, or very severe before you can pick salt spray or CASS hours to simulate such exposure needs. The second issue is that salt spray and CASS documents tell you how to run the test, but not what constitutes passing vs. failing, so you need to decide that or quote another spec that does so.
I doubt that the PVD coating significantly improves the corrosion resistance of the nickel plating, but I suppose you could consider it similar to a chrome plating layer, and use nickel-chrome plating standards which are, according to "Quality Metal Finishing Guide" published by the Metal Finishers Supply Association (NASF.org):
mild ⇨ 0 CASS hours
moderate ⇨ 4 CASS hours
severe ⇨ 16 CASS hours
very severe ⇨ 22 CASS hours
As for neutral salt spray hours, buyers typically require 48 to 96 hours for high quality components
Electrophoretic lacquer is paint, albeit a quite thin layer. Why are you electrophoretic lacquering? Is it because the nickel is only thick enough to offer nice appearance but no significant corrosion resistance? You really need to decide exactly what you are trying to do, and toward that end, retaining a finishing consultant or establishing a genuine partnership with a competent finishing shop may be advisable.
Luck & Regards,
Ted Mooney, P.E. RET
Striving to live Aloha
finishing.com - Pine Beach, New Jersey
⇩ Related postings, oldest first ⇩
Q. We are plating ABS with 20 microns of copper, 10 microns semi-bright nickel, 10 microns of bright nickel, 2 microns of micro porous nickel and finally 0,15 microns of conventional chromium coating. The Dubpernell Test shows more than 10000 pores/cm2 .
After 30 hours of CASS TEST, hemispherical pits develop in the nickel deposit beneath the chromium topcoat, but the copper is not seen. Should we consider that a failure? Should we consider the parts having failed the CASS TEST when pits appear in chromium layer or when the pits have crossed the nickel layer and copper appears?
We thank you for help.
NICRODUR S.A. - BsAs, Argentina
2002
QUICKSTART:
Accelerated corrosion testing is ideally used a QA measure to get early indication when something is going out of whack in the processing, such that the components are less likely to survive the previously expected period in the real world.
Unfortunately, such tests are also often used as predictors of real life, despite the fact that the corrosion mechanisms are so fundamentally different that the approach leads to erroneous results. For example, hot dip galvanizing is by far the most robust finish in most environments, lasting 50-100+ years without maintenance due to the glassy zinc carbonate skin which forms on it over the course of years ... but it performs poorly in accelerated testing.
Certain variations in the test procedures for certain substrates and coatings may somewhat improve their predictive value.
ASTM B117 Neutral Salt Spray (Fog) Test is the most commonly applied protocol across the board, but
ASTM B368 Copper-Accelerated acetic acid Salt Spray (Fog) Test (CASS test) is another widely used accelerated corrosion test, especially for nickel-chrome plated components.
A. Some automotive fuel components have this type of plating and CASS testing. We use both an appearance criteria (5% red rust at 24 hours) and a functional requirement (a burst test at 72 hours).
The interpretation of CASS and any other corrosion test data is always subjective and open for debate. This sort of thing is usually agreed upon between a customer and supplier based on technical experience and judgement. I have not seen an industrial requirement that uses a microscopic analysis of pores or corrosion sites. It could be done, but would you want a manufacturing process that requires constant microscopic analysis of test parts? This type of analysis may be better suited to research or an initial validation.
I suggest you strike up this conversation with a nickel-chrome plating chemical supplier.

Tim Neveau
Rochester Hills, Michigan
Multiple threads merged: please forgive chronology errors and repetition 🙂
Q. 1. How to compareASTM B117 Salt Spray and ASTM B368 CASS? If component resists 200 hours B117 test, how many hours should it resist for B368 test?
2. What is organic coating? Inorganic coating? Chrome plating is organic or inorganic?
Thanks,
- Nashua, New Hampshire
2003
A. 1. The only way to accurately and reliably develop a correlation is to build one yourself. That is, put some parts in neutral salt spray and some in CASS and see what you get. Keep in mind that both tests have significant variability, so it'd actually take numerous tests, control panels or parts in both tests, multiple cabinets, etc.
ACRONYMS:
NSS = Neutral Salt Spray, i.e., ASTM B117
SWATT = Sea Water Acidified Accelerated Test, described in Annex 3 of ASTM G85 Standard Practice for Modified Salt Spray (Fog) Testing
People often ask these types of questions, especially for SWAAT and NSS. There is no simple formula or factor to convert one test to another. They all induce different corrosion mechanisms on different substrates.
BTW, my investigation found that CASS was developed for Ni-Cr plated parts in Detroit. I talked to a guy who worked on the test, and he told me that they eventually determined that 8-12 hours in CASS meant 1 year in Detroit's environment (in the 50s or 60s). If you're not doing Ni-Cr plated parts, technically you're not even using the right test. Then again, I've seen lots of people use CASS (or NSS or SWAAT for that matter) with no idea as to how the test was developed or what its original purpose was. I'm sure many can relate.
- Pittsburgh, Pennsylvania
on AbeBooks
or eBay or
Amazon
(affil links)
A. Hi Liu,
1. To amplify Christian's excellent presentation, recognize that if two different tests for the same quality (corrosion resistance in this case) actually tracked each other the way we'd like, such that 200 hours of ASTM B117 (neutral salt spray) was equal to xx hours of ASTM B368 (CASS), there would be no point to having different tests and we wouldn't :-)
Rather, all accelerated corrosion tests are inaccurate indicators of real life, but the hope is that some may be less misleading than others for certain substrates, coatings, situations, and conditions. For example, CASS seems to have been developed in the belief that it is a better indicator of nickel-chrome life than NSS (neutral salt spray)
2. Organic coatings are coatings that are based on organic chemicals (basically chemicals that contain carbon). Most lacquers, paints, and powder coatings would be organic coatings. Inorganic coatings are coatings that don't contain (significant amounts of) organic chemicals. Metallic coatings like galvanizing and nickel & chrome plating and PVD are inorganic. There are probably some blurry areas, as there almost always are in life. Good luck.
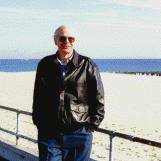
Ted Mooney, P.E.
Striving to live Aloha
finishing.com - Pine Beach, New Jersey
Q. We manufacture parts for mostly military end use. Our parts generally are aluminum with Cad Plating over electroless nickel plating. Has anyone ever compared CASS Testing with the standard neutral salt fog spray testing? We are developing an alternative to Cadmium plating, and if there is a comparison that someone has done, it would be great to find the results of the comparison, i.e., one hour (or 7 hours) of CASS = XXX hours of ASTM B117.
Tom SaxeManufacture aerospace products - Chatsworth, California, USA
2006
A. Hi Tom. If someone can suggest which of the two tests is better for your situation, or can propose another test, that would be great. But we appended your inquiry to an earlier thread which touches on the difficulties of correlation. Unfortunately, I think the answer is that you will not know the real world life of your cadmium substitute, nor how it compares to cadmium in the real world, except by real world testing. And only after that can you build a correlation to accelerated testing. While developing correlation can be useful, trying to develop a predictive correlation that doesn't require real world testing probably won't work. Many have tried.
Regards,
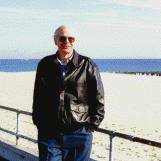
Ted Mooney, P.E.
Striving to live Aloha
finishing.com - Pine Beach, New Jersey
Multiple threads merged: please forgive chronology errors and repetition 🙂
Q. Sir,
We, the pioneer in auto electrical manufacturer in India, do various types of high corrosion resistant plating/coating systems based on customer requirements (in case 720 hours NSS is the requirement, we need to wait 30 days for the result).
Is there any other accelerated tests available to correlate NSS test to avoid the longer time? Can we correlate NSS & CASS tests? For What application & evaluation CASS test can be recommended?
Thanks in advance.
- Chennai, Tamilnadu, India
2006
A. First a side note about CASS. A few years ago, I tracked down a gentlemen who was involved in the original development of CASS. According to him, CASS was used for chrome plated bumpers. 8-12 hours in CASS correlated to 1 year performance in Detroit in the 50s/60s. (He didn't say how they defined failure in the test or the field.)
Those in the business know that CASS is used for a bunch of things, yet you'd be hard pressed to find anyone who could tell you *why* the test is used in a specific instance. (You could probably say that about a lot of these tests.)
That said, you generally cannot correlate accelerated tests to tests such as NSS for numerous reasons. The corrosion mechanism may not (and usually is not) the same, and CASS (and even NSS) is not representative of what goes on in the field. Salt cabinets (assuming they're run properly, which is generally not true) also have a great deal of variation that makes any correlation, in my opinion, greatly suspect.
That said, I have seen some published R&D that correlates electrochemical tests (DC/EIS) to NSS for painted parts. Note, however, that you must develop the test yourself. You cannot simply pull a "method" off the shelf and say that an expected corrosion rate of x mm/yr in an electrochemical test corresponds to y hours in NSS. You must take the time to develop this correlation yourself because it depends on the paint, substrate, chamber, and test equipment.
Circle-Prosco, Inc. - Pittsburgh, Pennsylvania, US
Q. I'd like to speed up our 1000 hours for coil coatings requirement of ASTM B117. I'm planning to use CASS test. Is it comparable? If so, what will 1000 hours of B117 equivalent to CASS test.
Raphael AtienzaTwin aces industries - Philippines
2007
A. CASS is not comparable to NSS, at least not in any generic way. It will give you a different corrosion mechanism.
If you want to use CASS as a proxy for NSS, you will have to very carefully develop your own correlation which will depend on the substrate, paint, even the cabinet(s) themselves. You'll also have to run periodic tests to verify that your correlation is still correct. This assumes, of course, that you're running the test purely as a quality assurance test to make sure your process is running the same sample to sample. If you're trying to mimic some field failure, you're talking completely different corrosion mechanisms....
Circle-Prosco, Inc. - Pittsburgh, Pennsylvania, US
2007
Q. May I ask a question about Salt spray test and CASS? We have a standard salt spray test equipment, but we want to do CASS test on this equipment. Is this possible? If it is, what should we do?
Thanks for helping.
- Izmir, Turkey
July 25, 2012
A. Hi Kerem. The supplier of your salt spray cabinet can advise you on this, but if not, it would be best to get access to ASTM B368 because it specifies the equipment and procedure required. It's only 4-5 pages, and then you won't be guessing whether your procedure complies :-)
Regards,
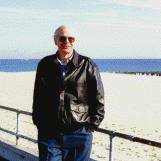
Ted Mooney, P.E.
Striving to live Aloha
finishing.com - Pine Beach, New Jersey
In CASS test we get rusting only on knurling
Q. We have checked the part for 48 hours CASS TEST but we have observed the rust only on the knurling area.
So my question is whether there is any specific requirement of CASS test for threaded, knurled area?
- Gurgaon, Haryana, India
February 24, 2014
? Hello Pankaj, which exact standards does your CASS test comply with?
Davey ShawShenzhen, Guangdong, China
A. ASTM B368
Pankaj Mahajan [returning]- Gurgaon, Haryana, India
A. Pankaj,
I doubt the standard gets that specific, it is probably more a matter to discuss with your customer. If they only require that the non-knurled areas pass CASS, then you should be fine.
Are these parts stainless steel, or a non-ferrous alloy perhaps? If the knurling process is causing iron contamination, passivating the parts should help.
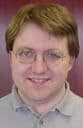
Ray Kremer
Stellar Solutions, Inc.

McHenry, Illinois
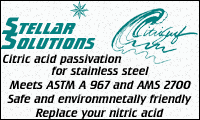
Q. From many threads I can see that there is no relation between NSS and CASS. But I see in some webpages, which claims that CASS is 9 to 15 times faster to NSS? Can we take this as a thumb rule?
PRAVEEN DP- CHENNAI, TN, India
July 25, 2014
by Seymour K Coburn
on AbeBooks
or eBay or
Amazon
(affil links)
A. Hi Praveen. You appear to be acknowledging that there is no correlation, but then asking whether the correlation would be 9-15:1 if there was a correlation? :-)
I think it's true that CASS is more aggressive than NSS and will always be faster. Other than that, any correlation there may be would only be for a given plating on a given substrate ... because how much more aggressive the CASS solution is would depend on what you are trying to corrode with it.
The origin of your 9-15:1 ratio may be that copper-nickel-chrome coatings are sometimes spec'd to pass a few hours in CASS, but several times more hours in acidic salt spray or neutral salt spray. Good luck, but please accept the general thrust of this whole thread that any correlations between CASS, NSS, and real life are at best no better than the backup data for your parts that you have accumulated to demonstrate them :-)
Luck and Regards,
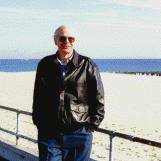
Ted Mooney, P.E.
Striving to live Aloha
finishing.com - Pine Beach, New Jersey
Q. I am curious, does anyone know how many hours of CASS testing would be comparable/estimated to years a vehicle corrosion "in the field" would be. I understand that would be a estimate (especially considering there would be a difference between what part of the country the vehicle would be "in the field").....I am just looking to see if anyone has an opinion on this question.. I am specifically questioning/asking 48 hours or 80 hours of CASS replicate the amount of corrosion would equate to years of a vehicle would see in lets say Michigan...
Any opinions or thoughts would be appreciated..
- Grand Rapids, Michigan USA
September 18, 2014
A. Hi Derrick. Back in 2002 Christian Restifo expressed his belief that "CASS was developed for Ni-Cr plated parts in Detroit . . . they eventually determined that 8-12 hours in CASS meant 1 year in Detroit's environment (in the 50s or 60s)."
But Christian also remarks that there is significant variability throughout, such that you need multiple tests, multiple panels in each test, cabinets from different manufacturers, etc.
And I need to repeat, so that your Q&A can stand on its own without being misquoted, that this correlation applies at best only to nickel-chrome decorative plated parts. Other materials and coatings corrode in fundamentally different ways such that CASS test results have essentially no bearing on their anticipated life. Good luck.
Regards,
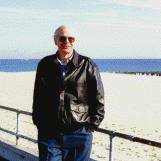
Ted Mooney, P.E.
Striving to live Aloha
finishing.com - Pine Beach, New Jersey
Thanks for your response Ted, appreciate your time!
- Grand Rapids, Michigan
Hi again Derrick. Way way back when I was chief engineer of the Equipment Division of Harshaw/Atotech and we built a large plating-on-plastic line for the company you work for. At the time, it was probably the biggest plating-on-plastics line in the country. It was a blast from the past hearing from you :-)
Regards,
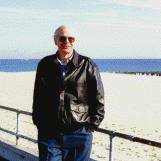
Ted Mooney, P.E.
Striving to live Aloha
finishing.com - Pine Beach, New Jersey
Q. Hi
I want to do salt spray test on the stainless steel by CASS method but I haven't any information about it. As well I know we don't use the method for stainless steel. But the NSS method test duration is too long, and I have little time.
Thank you all.
- isfahan iran
December 17, 2019
A. Hi Ahmad. You can learn the details of CASS testing in ASTM B368 or ISO 9227. Still, such tests are designed for QA: that is, if the parts previously survives X number of CASS hours, and they no longer do, something has changed that will probably reduce the life of the component in the real world. But establishing an initial correlation between this QA test and real world life can be a challenge; and to assume that X hours of CASS equals Y months of real world exposure is highly questionable, and depends on the type of component, the exposure conditions, the substrate, etc. For example, does accelerating the corrosion with copper really have any relationship to the actual exposure? Good luck.
Regards,
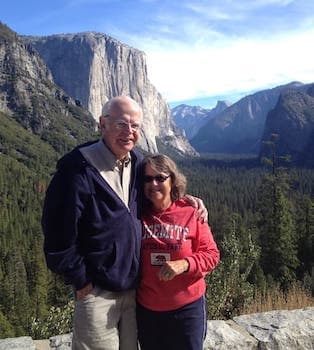
Ted Mooney, P.E. RET
Striving to live Aloha
finishing.com - Pine Beach, New Jersey
Thanks a lot dear Ted
Q. I read those standards but I can't find any information about stainless steel salt spray with CASS method.
Do you know for example X number of CASS hours is equal how long number of NSS method?????
Did you do any experiment on the stainless steel salt spray?
Regards
- isfahan iran
A. Hi again. CASS is more severe than NSS, but as has been said before on this page, I don't think any further correlation is possible.
Do you passivate your components, or do you electropolish them. What alloy(s) are they? Thanks.
Something to remember about stainless steel when doing accelerated corrosion testing is that, because it is not a coating, porosity of the coating and life of the coating are rather meaningless -- such that once it passes 4 hours we shouldn't be shocked if it passes 400 hours. Similarly a stainless which fails in 2 hours may not be all that different from a stainless that lasts hundreds of hours. Accelerated testing of coatings is quantitative but testing of stainless is really more of a qualitative test.
Regards,
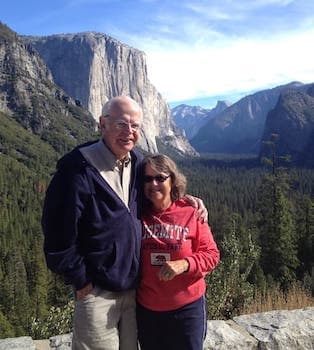
Ted Mooney, P.E. RET
Striving to live Aloha
finishing.com - Pine Beach, New Jersey
Q, A, or Comment on THIS thread -or- Start a NEW Thread