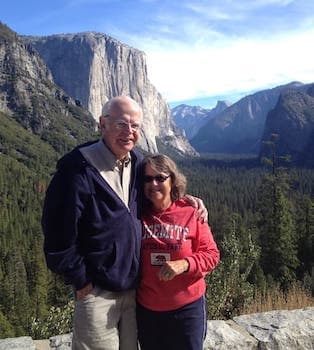
Curated with aloha by
Ted Mooney, P.E. RET
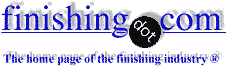
The authoritative public forum
for Metal Finishing 1989-2025
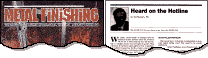
-----
Dubpernell test method for chromium plating
Q. The copper is deposited very much. We want to deposit copper for checking porosity, but a little higher amount of copper deposition on plated sample is making us unable to get good porosity surface for testing. Please suggest what we are lacking in method of copper deposition.
Thanks.
test engineer - haryana, India
July 9, 2021
by Weiner & Walmsley
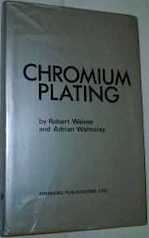
on AbeBooks
(rarely)
or eBay
(sometimes)
or Amazon
(sometimes)
(affil links)
A. Hi Prabhjot. Please make sure that you have studied ASTM B456 and are following the exact instructions, including not exceeding 0.6 volts and plating for not more than 10 minutes.
There is a good explanation of the theory & background in Weiner & Walmsley if you can find a copy. And
https://nmfrc.org/pdf/sf2004/sf04b07.pdf
is an excellent update on the technology.
Luck & Regards,
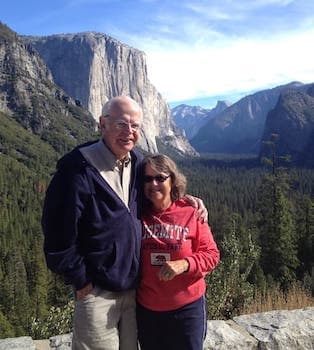
Ted Mooney, P.E. RET
Striving to live Aloha
finishing.com - Pine Beach, New Jersey
July 2021
⇩ Related postings, oldest first ⇩
Somebody explain me the method to obtain microdiscontinuous nickel on plated parts.
I know the specification of our customers but I need the lab method.
Thanks
POP - Puebla, Mexico
2006
2006
The Dubpernell test determines the number of discontinuities in chromium electroplating over a nickel base coat. It is described in ASTM B456, Appendix X4
[someone please verify that the latest version B456-03 still includes this method].
Briefly, Cu is electroplated at low voltage (0.6 V max) from acid Cu solution into the Cr porosity onto the Ni base plating. The part is photographed under a fixed magnification (e.g., 100x or 200x) before and after 16-24 hours of CASS corrosion. Both total and corroding pores are counted for a given area. The actively corroding pores are darker and larger than non-corroding pores.
After determining correlations and the necessary number of corroding pores for a given plating process, the corrosion step can be omitted, and only total pores are counted.
- Goleta, California

Rest in peace, Ken. Thank you for your hard work which the finishing world, and we at finishing.com, continue to benefit from.
Q, A, or Comment on THIS thread -or- Start a NEW Thread