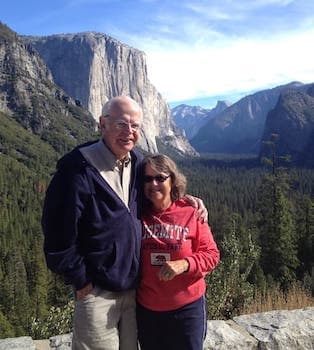
Curated with aloha by
Ted Mooney, P.E. RET
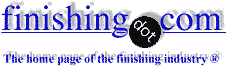
The authoritative public forum
for Metal Finishing 1989-2025
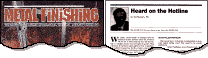
-----
Etching During Stainless Steel Passivation
2002
One of the processes that we carry out is the Passivation of Stainless Steel. We mostly work in accordance with AMS AMSQQP416.
We have full laboratory facilities and all our solutions are regularly analyzed and maintained within close limits. We have carried out this process for many years.
On four occasions, the stainless steel components have been badly etched during processing. When I say etched - I mean destroyed.
On one occasion we were processing two baskets of identical components at the same time (in the same load); one full basket became etched, the other one didn't!
When processing six loads of identical components, one load got etched, the rest didn't!
We have checked for stray currents, contamination, etc., but have never found anything wrong. (Damaged items have either been 300 or 400 series material.)
We have weighed a component that has been etched, re-processed it, and then re-weighed it to see if further attack occurred. It didn't.
We can never subsequently reproduce the attack on similar components or materials. Has anyone experienced the same problem?
John Potter- Sheffield, Yorkshire, England
First of two simultaneous responses
The best guess may be that the parts which became etched were machined and/or cleaned slightly differently, such that a miniscule amount of oil remained in the pores of the parts and produced an organic acid. See our FAQ on this subject at www.finishing.com/faqs/sstpass.html for some interesting reading. If you can switch to citric acid passivation you can probably put an end to the problem.
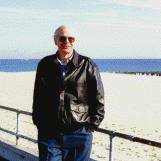
Ted Mooney, P.E.
Striving to live Aloha
finishing.com - Pine Beach, New Jersey
2002
Second of two simultaneous responses
Was the 300 series 303? Was the 400 series a free machining variety? (Se +/or S) Did either have EDM machining? Were you using a nitric/dichromate solution? I think you will get a lot of feedback on this and more particulars will help. Yes I have seen this, and it can be most confounding. I think you will hear from Lee Kremer of Stellar Solutions [a finishing.com supporting advertiser] on this issue, he has good advise.
Jon Quirt- Fridley, Minnesota
2002
I would examine the method of processing in baskets: 1) Are the baskets of suitable material, e.g., 304/316 SS, titanium or polypropylene? 2) Are the baskets used in other processes whereby they may pick up contamination? 3) Is sufficient agitation used to ensure that the parts are fully exposed to the bulk solution in each process step? 4) Is there sufficient rinsing to ensure that there is no carryover of solution within the parts or within the construction of the basket?
The process procedure may be identical on paper, but human nature being what it is, the baskets may be getting varying amounts of agitation and rinsing.
Ken Vlach [deceased]- Goleta, California

Rest in peace, Ken. Thank you for your hard work which the finishing world, and we at finishing.com, continue to benefit from.
2002
AMSQQP416 is a standard for electrodeposited cadmium plating. Do you mean AMSQQP35 [canceled] ? I agree with Ted and Jon, and ask the same questions as Ken. However, this is a very common problem in the industry with nitric acid passivation. I hear this all the time and have seen it in our Lab with nitric acid and even with straight citric acid occasionally. But, it will never happen in a properly formulated bath. I have heard a number of theories on this from various sources. You should read the materials that Ted referred you to and check out whether you MUST use nitric acid. As you stated, it can happen with one basket out of 6 on the exact same lot of parts from the same bar of steel. I have heard of it happening with fresh tanks of nitric and old ones. Usually the sodium dichromate with prevent this, if you can use it. This usually happens with the "poorer" grades of stainless steel, but I have heard of it with austenitic steel also.
It is most certainly an electro-chemical attack on the surface that once started takes off quickly to ruin the parts, but have not seen a good answer on why it happens with just one basket and none of the others subsequently. As you stated, you can reprocess the same parts and it does not happen the second time through. I think that it is usually started by a static electrical charge that transmits through the metal basket, but I have not had time to prove this out. I have seen the "opposite" of this, where 440C parts after heat treating are badly discolored and put in the passivation bath. Nothing visually happens until quite suddenly the surface of the entire batch of parts almost instantly turns a beautiful shiny color when the basket is touched with a metal object (forceps).
You can usually get a better passivation job without this danger of etching the parts if you use citric acid proprietary formulations, if you can use them. Let us know if we can help. You should be able to totally eliminate this problem.
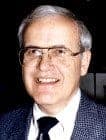

Lee Kremer
Stellar Solutions, Inc.

McHenry, Illinois
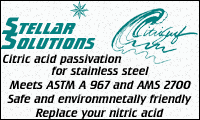
2002
Hi Lee,
Can you give us some more details on turning heat treated 440C shiny? I had thought shiny 440C required preserving the machined surface by encapsulation in SS foil prior to heat treatment (as mentioned by James Watts).
Ken Vlach [deceased]- Goleta, California

Rest in peace, Ken. Thank you for your hard work which the finishing world, and we at finishing.com, continue to benefit from.
2003
My experience is with several customers who have supplied quantities of samples of 440C hardened to around 60 Rockwell. The samples came in to us brownish or golden colored, but with a very good, smooth surface- shiny brownish. What happened to turn them a bright shiney is that during the passivation process (in CitriSurf at around 160F) I would reach in with forceps and pull out a part to check how it looked. When I did this and touched the part with the forceps- all of a sudden all of the parts in the basket suddenly lost all of the brown discoloration and became a bright, shiny metallic color.
Because of the suddenness and the fact that it happened when I touched the parts, my only conclusion was static electricity. I have no proof of this, but it has happened a number of times in the same manner. If I had time I would set out to prove this by supplying a static discharge intentionally. Maybe someone else out there has experienced the same thing, or has time to check on this.
I am leaving for Europe tomorrow and am on the run for the next couple months.
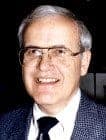

Lee Kremer
Stellar Solutions, Inc.

McHenry, Illinois
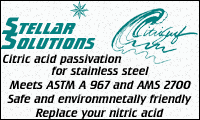
2003
May 13, 2010
I am having a similar issue. I've just had some parts machined out of 440C, and had them fully hardened. Upon receiving them, I was surprised to see the discoloration of what I would describe as a black-green film. It reminds me of a really bad and ugly anodize. This discoloration is not bright looking, bull dull. I believe it to look like an atmospheric type sediment that baked on.
As I'm not familiar with hardening Stainless Steels, I'm not sure if this is typical. The heat treater/machine shop says it is.
If it is, is there an easy way to remove it without degrading the hardness or fragility. I'm mainly worried about leaching, as I'm not sure what this black "stuff" is exactly, nor if it will come off or leach off into our process material. These 440C parts are cutting blades, so I'm assuming as we begin to run, the abrasion from the slurry alone should shine them up. Is this a correct assumption?
- Visalia, California

this text gets replaced with bannerText
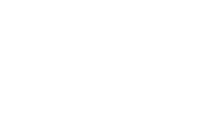
Q, A, or Comment on THIS thread -or- Start a NEW Thread