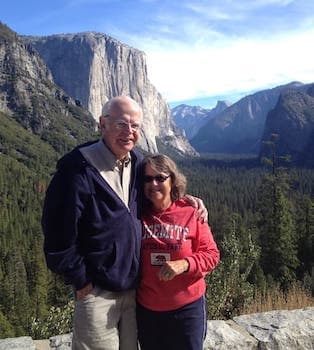
Curated with aloha by
Ted Mooney, P.E. RET
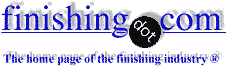
The authoritative public forum
for Metal Finishing 1989-2025
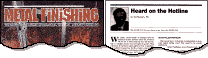
-----
Conductivity of Zinc and Zinc-Nickel Plating

Q. In zinc nickel now we are achieving resistance 35 milli-ohms on aluminium 60. Now we are using Hexavalent chrome with chromate fixer. Please suggest how can we reduce this to 2-3 milli-ohms resistance.
Base material = aluminium 60 series
Undercoat = electroless nickel 10-12 microns
Zinc-nickel plating = 10-15 microns
- Bangalore
November 13, 2022
A. Hi Bharath. You and Satheesh, both from Bangalore and both within the last year, have been the only people to ever inquire about this subject -- which prompts me to ask for clarification about this obviously unusual specification. The "units" seem wrong -- lacking an area, and not mentioning the contact pressure (you can review MIL-DTL-81706 [⇦ this spec on DLA] which describes an analogous situation for chromated aluminum and describes & illustrates the test equipment).
Satheesh said he followed the advice our readers offered to use the thinnest chromate he could, and still exceeded this value by a factor of 5X. I guess I'm not understanding why you are putting non-conductive chromated zinc-nickel on top of conductive electroless nickel is you are seeking conductivity. Are you sure that the area where good conductivity is required is not permitted to be masked from the subsequent zinc-nickel and non-conductive chromate?
Luck & Regards,
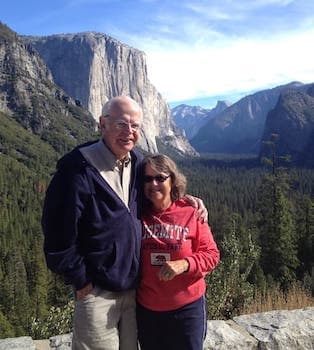
Ted Mooney, P.E. RET
Striving to live Aloha
finishing.com - Pine Beach, New Jersey
Addendum Nov. 17, 2022: Please look at John Parlevliet's posting on topic 45763 . Claims are made that the conductivity of the system can depend on the plating bath more than the chromate. Possibly, switching from an acid to alkaline plating bath or vice-versa could affect this resistance ... possibly -- I don't know.
⇩ Related postings, oldest first ⇩
Tip: Readers want to learn from Your Situation 🙂
(little can be learned from abstract questions, so many readers skip them)
Q. Is Zinc Plating conductive? If not, what plating is?
Thank you,
Sharon NicodemusRittal - Springfield, Ohio, USA
2002
A. The zinc itself is conductive, however, conventional chromate conversion coatings add surface resistance that lower the anticipated conductivity of pure zinc. Furthermore, organic topcoats and other sealers intended to boost the corrosion resistance of chromated zinc typically degrade the surface conductance even further.
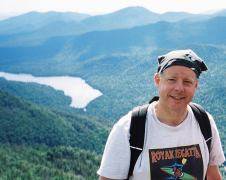
Milt Stevenson, Jr.
Syracuse, New York
A. Zinc in itself is very conductive, the chromates applied after plating for corrosion resistance do offer some electrical resistance. The "clear" or colorless chromate is the most conductive. ASTM B633 Type III
Bill Grayson- Santa Cruz, California, USA
A. Hi Sharon. Please describe your situation and you will surely get suggestions which will help resolve it. Nickel plating and electroless nickel plating are quite conductive and are frequently used for such things as contacts on the ubiquitous chargers, audio and video connections, etc. But nearly all metals tarnish or oxidize, creating some resistance on their surface; that is why, for low voltage / low amperage digital circuits you see gold plating because gold does not tarnish.
Luck & Regards,
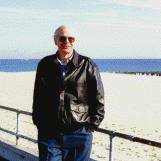
Ted Mooney, P.E.
Striving to live Aloha
finishing.com - Pine Beach, New Jersey
Q. How to achieve conductivity - Resistance value within 2.5 milli-ohms on Zinc Nickel plated connectors connected to braid or cable with 2 inch length?
Zinc nickel plating is done with an undercoat of Electroless Nickel. Base material is Aluminum 60 series.
- Bangalore Karnataka India
June 20, 2021
A. Hi Satheesh. Zinc-nickel and electroless nickel are quite conductive, but the chromates used on them are not. You should try the thinnest, clearest chromate available, with no topcoat. Unfortunately, this will probably adversely affect the corrosion resistance; but with electroless nickel underneath, maybe it will be okay.
Luck & Regards,
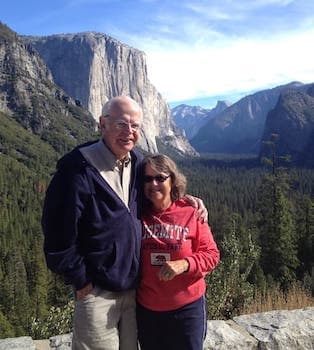
Ted Mooney, P.E. RET
Striving to live Aloha
finishing.com - Pine Beach, New Jersey
Q. Hi, thanks for your ideas. Yes we have already made top coat layer thinnest by reducing concentration and process time by which we have achieved electrical resistance less than 10 milli ohms, but still we need to achieve less than 2.5 milli ohms consistently for our connectors used in aerospace applications.
Any specific parameters to be adjusted in Zinc Nickel Plating bath?
What is oven baking process temp & time to be maintained after chrome passivation?
- Bangalore Karnataka India
A. Hi again. I've heard of measuring the resistivity of type III chromate conversion coatings on aluminum per MIL-DTL-81706 [⇦ this spec on DLA] , but sorry I'm not familiar with any similar requirements for zinc-nickel plating and chromate conversion coatings. But your units don't seem right to me as they lack an area and a pressure (MIL-DTL-81706 requires not greater than 5000 microhms per square inch at a contact pressure of 200 psi). Is any particular machinery described for your test? The referenced documents notes that the surface roughness of the item being tested and of the electrode pads can have a great effect on the reading. You might want to consult that document to clarify your requirement. Please describe your situation and what 2.5 miliohms means, i.e., the requirement in context and the test method to determine compliance.
Luck & Regards,
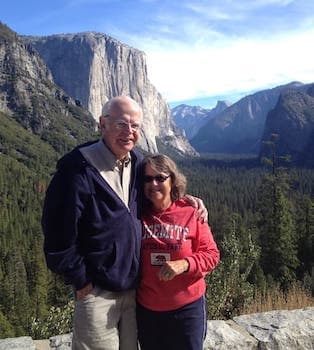
Ted Mooney, P.E. RET
Striving to live Aloha
finishing.com - Pine Beach, New Jersey
Q, A, or Comment on THIS thread -or- Start a NEW Thread