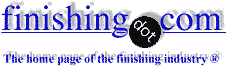
-----
Problems in powder coating
< Prev. page (You're on the last page)
September 2, 2015
Q. Good day
My name is Etienne.
We have been experiencing blotches when powder coating various products, it seems that it is only when using a texture powder. And from various suppliers, we have had sales reps to come with new guns and we still have the problem.
We have found that it is more on prepared surfaces like grinding or brushed material from steel supplier.
(click thumbnails to open hi-rez photos)
You can only see the blemishes when you look at the product from an angle.
adrian Botha- roodepoort,gauteng, South Africa
September 3, 2015
A. Well,
There are several potential causes of this problem.
(1) Maybe you have a defective batch of powder. This unlikely but not unheard of.
(2) Maybe you are using a vibratory feed hopper rather than an aeration system? Special effects powders be they ripple or metallic or texture have to be aerated adequately.
(3) Maybe your air supply is inadequately filtered of liquid? do you have a well maintained and refigerant cooled air supply?
These are the three most obvious answers to your problems.
I hope this helps.
Regards,
Bill Doherty
Trainer - Salamander Bay, Australia
September 8, 2015
Q. Hi William
Thanks for your response
(1) When the problem first occurred we got our suppler out (their technical department )and painted panels with them. They also had the test equipment to test the static of the units (all okay) they took a sample of powder back to the lab for practical testing (all okay). As you said, don't believe it is the powder (but was checked).
(2) Yes we do use vibratory feed hoppers they are ITC Gema (optiflex B). We have always used vibratory feed hoppers as we do 15 to 20 colour changes a day. We have had one metallic blue texture powder that we battled with to get the colour and silvery texture the same (this was not the blotches); this was due to the silver flakes and the base material separating (silver being heavier and settling to the bottom of the box). With our suppliers help we have overcome that problem by agitating the powder manually every now and then and by reducing the KV
(3) We have Kaeser compressors with the appropriate air dryers in place as we have highly moisture sensitive equipment in our factory that is all fed off the same air line (laser cutting machines).
We have also done the mirror test on our air lines at the points of painting and it was all dry and okay.
When we did tests with our supplier we took a mild steel plate and only polished a strip down the middle (so you had virgin material on each side and a polished piece in the middle). The blotches were only where the surface was polished/ground (we had the sandpaper supplier out as well, no problem there).
The blotches have also occurred on brush finished stainless steel (rough surface); we have never had blotches happen on untouched surfaces (cut and bent parts). The blotches only happen every now and then and only on surfaces that are rough; this is very confusing for us as we and our supplier have not come across this in the past.
Hope the new information helps and your input is highly appreciated.
Thanks,
- roodepoort,gauteng, South Africa
September 9, 2015
A. Hi,
I find the last two paragraphs of your response puzzling.
Am I right in concluding that only the polished (or sanded) section on one occasion has the flaw but on another occasion the flaw is on unpolished (not sanded) surface?
I really think you should try a full on aeration hopper scenario for the special effect powder you are using.
Metallics can be bonded or not in formulation. Textures, ripples etc, I do not believe can be.
Give an aeration hopper a try if only for special effects and please advise your result.
Hope this helps.
Regards,
Bill
Trainer - Newcastle, NSW Australia
Hi.
Yes you are correct in saying that it only happens on sanded or brushed parts of product and never on parts that have not been sanded or brushed (plain mild steel)
I will have to get hold of our gun suppler and get a demo gun to try (worth a try ).
Thanks again for the feedback, it really is appreciated
Adrian
SPE - South Africa
September 9, 2015
September 12, 2015
A. I like Bill's suggestion of aeration stirring rather than vibratory.
We've found that vibration causes many problems in special effects, metallics, and textures. Air fluidizing solves most of them.
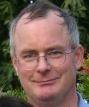
Geoff Crowley
Crithwood Ltd.
Westfield, Scotland, UK
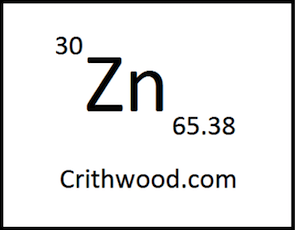
A. You only need a fluidising hopper.
Your gun and the rest of your gear could remain.
A fluidising hopper is a cheap and easy construct.
I am really interested in your result, please publish.
Regards,
Bill
Trainer - Newcastle, NSW Australia
September 14, 2015
September 23, 2015
Hi all
Thanks a lot for all your input.
Since my last post I have had a demo from Gema of their fluidise unit with the hopper.
Been running it for a weak in my batch line.
I have compared the work from the batch (hopper unit) to the work from our other two conveyer line (vibrating units).
I cannot see a difference in the finish of the end product in structure, hammertone, texture, and metallic colours (special effects powders).
I still can't see what will cause the blotchiness. Thank goodness it has only happened twice this year.
Thanks
Adrian
SPE - South Africa
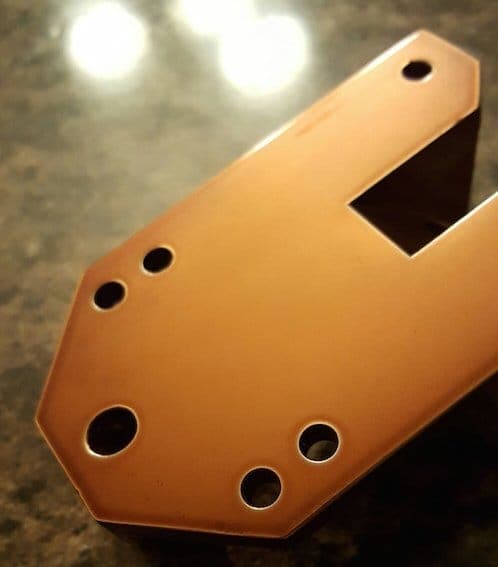
Clearcoat pulls away from edges, and pools at bottom of parts
My issue is my transparents seem to pull away from the edges of my parts and pool at the bottom of the part. This is new metal and it's clean, so no grease or polish on it, etc. I'm so frustrated I just can't figure out why they are doing this; my edges are not sharp and my oven is at the temperature the manufacturer specifies. If you guys have any ideas as to why this is happening I'd be very grateful
Steve Clark- Westbank, British Columbia, Canada
December 19, 2015
A. Good day Steve.
Interesting situation. I am by no means a pro at paint, but I am involved in paint adhesion testing wet/dry with primers and epoxy top coat for aerospace. You mention this is new metal. What is it and what are the previous metal compositions?
"This is new metal and it's clean, so no grease or polish on it, etc." Can you verify?
Do you have a process to clean prior to paint, and does the part exhibit a water break free surface before paint?. It looks like the paint is not "biting/adhering" at the edges which are not sharp, and at the perimeters of the holes, and as you say it is pooling at the bottom. Are you dipping or spraying? Obviously you are confident with the viscosity. Have you done a paint adhesion test on these parts?
Food for thought.
Regards,
Aerotek Mfg. Ltd. - Whitby, Ontario, Canada
December 22, 2015
Q. Hey Eric
By new metal I mean that it hasn't been used for its intended purpose yet. So in this case no bearing grease, etc. As for the type of metal it's aluminum; it was cleaned just with water then out gassed in case there was any cutting solution on it from the CNC machine that made it. I lightly rubbed it with 000 steel wool
⇦ on
eBay
or
Amazon [affil links]
and washed again. I have powder coated many things and only in the past few months have I tried the transparent top coats. This one being a copper, there is no base coat under this and the manufacturer said I didn't need one.
I did try putting a metallic base powder under it and had the same issue, again doing so under the manufacturer specifications.
Just so stinking frustrating since removing powder coat from corners can be a nightmare. So any help is good help at this point. And thanks for taking an interest in my problem, Eric.
- Westbank, British Columbia, Canada
December 22, 2015
December 23, 2015
A. Good day Steve.
I do not understand that it was just cleaned with water and out gassed. I am having a problem with the STEEL WOOL on aluminium and washing again.
Washing with what?
Since this is a "new" metal, (is this the first time processing aluminum?) perhaps this is a situation where the cleaning chemistry (powder coat) is not compatible with the aluminum. Your alternate metallic base also proved negative.
When I have issues with paint (we process aluminum as spray), I process the items with a pre-anodize cleaning process.
It involves a wash/wipe with MEK (that is ONLY what is allowed following specs), MILD alkaline soak (high caustic/high pH will cause you grief), to remove any trace of "exotics", and a deoxider to deal with any oxides, if there are any, based on the alloy.
Maybe I missed the train.
Regards,
Aerotek Mfg. Ltd. - Whitby, Ontario, Canada
December 23, 2015
A. Your coating is too low in viscosity, or is applied too thick.
Try two layers, each half as thick. Let the first layer air dry before applying the second.
If you do not see the problem prior to bake, the coating may be thinning as it begins to heat in the bake oven. You can try air drying to let it thicken up a bit before baking.
Your part looks like the armature for an ignition coil. Most mfrs of those use precoated sheet and don't bother to coat the edges at all.
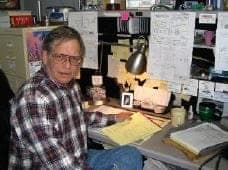
Jeffrey Holmes, CEF
Spartanburg, South Carolina
Q. Hi, my question is in powder coating. Aesthetics is the major problem or what? How to reduce that problem?
Nelson j. simonups pvt ltd - Bangalore, India
March 28, 2018
A. Hi Nelson. I think we're going to need more words than that before we can help you much :-(
Regards,
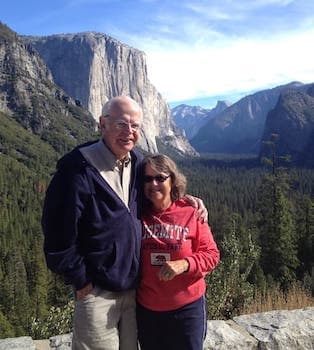
Ted Mooney, P.E. RET
Striving to live Aloha
finishing.com - Pine Beach, New Jersey
March 2018
Rough edges on metallics
Q. We are having issues with rough edges and some bubbling when spraying metallic powder onto aluminum castings. Part process is: 3 stage washer - dryoff oven - robotic powder epoxy prime - oven cure (parbake) - robotic topcoat powder (bonded uerethane metallic) - oven cure.
While the majority of the part comes out great, a thin fin coming off the part will either have a rough abrasive edge, or a slightly bubbled edge. We have experimented with several powder flows, and electrostatic settings. We are able to eliminate the bubbles by lowering the Topcoat film build. But then the rough edges turn up. Occasionally, we will turn out a rack or so of good parts, then slowly back to rough edges. Lowering the electrostatic KV and Ua levels seems to make things worse, while high KV seems to help. At a loss.
Any input would be appreciated!
Robotic Powder Paint Tech - Fond du Lac, Wisconsin USA
May 23, 2018
Ed. note: This RFQ is outdated, but technical replies are welcome, and readers are encouraged to post their own RFQs. But no public commercial suggestions please ( huh? why?).
May 25, 2018
A. Hi Chris, you are obviously looking to a high quality protective finish and, by the sounds of it, working well towards that.
That said, it would be very helpful to view photographs of the problems.
A picture is worth a thousand words?
I trust that your powder delivery system for metallic is aerated rather than vibratory?
Please provide photographs to allow any constructive further advice.
Regards,
Bill
trainer - newcastle nsw australia
Black "rub marks" on powder coating
Q. Hi guys, we have a problem that, after the supplier sent in the parts, when we are about to use it we found that there is serious rubbing marks (black) on the powder. I would like to know what is the root cause of this rubbing mark? FYI, we are facing this issue when we rub the parts with a clean soft cloth. Is this because of the quality of the powder or what?
Moon RadzukiActiforce Mechatronics Sdn. Bhd. - SUNGAI PETANI, KEDAH Malaysia
August 14, 2018
Please add the photos that will maybe explain the problem.
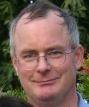
Geoff Crowley
Crithwood Ltd.
Westfield, Scotland, UK
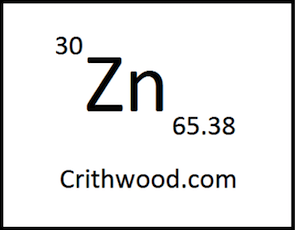
August 22, 2018
----
Ed. note: Photos can be e-mailed to
'Spiderwebs' in powder coating
Q. Hi. I have a problem like spiderweb on my finish ... why? It's happening only with white.
Lorenzo bonini- Firenze, italia
November 21, 2018
Q. I have cured powder that is not adhere to the metal, peals at the edge and comes off in strips. This material has been through the wash system and it is checked twice daily. Only one set of parts seem to have this problem but I am concerned other parts my fail an adhesion test.
GEOFFREY M HOCHIndustrial equipment - Ponchatoula, Louisiana USA
February 6, 2019
February 19, 2019
A. Poor adhesion can be attributed to so many factors, and you haven't really given much info here.
You mentioned a "wash system". What is that? just water (doubtful), but at a distance we can't tell to be able to suggest much. What chemistry does your "wash" include? It is a cleaning only? conversion coating? Other?
Cure cycles? Temp? Time? Heat transfer method? (Infra Red or how air)?
Metal? What are you coating? Aluminium, steel, stainless steel? Bronze, galvanized steel? Copper? Titanium?
And what shape is the metal? Thin sheet? fabricated from plates? Lengths? castings? And are these different to those that you have no problems with? How?
Do you do any tests for adhesion? How? scratch? cross hatch? pull-off?
Do you test for cure? How?
More info and you might get a much more useful answer. Pictures too and you bring us right with you to see the problem!
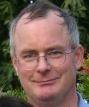
Geoff Crowley
Crithwood Ltd.
Westfield, Scotland, UK
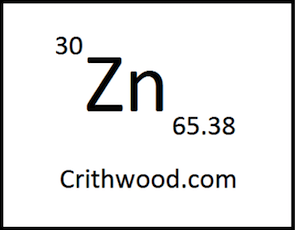
Q. Hi sir,
I am jagan
Good Morning.
We are facing colour fading problem in our part. Part size 650 MM x 600 MM. We are using texture powder. Past 7 years we did not face this kind of problem.
Following points are checked internally.
Gun Power flow, air flow, KV all are ok. After finishing, curing, we face colour fading problem. Some areas looks like glass finish and some looks like matte (dull) finish. Micron was checked ok, range was (55 to 75).
nsc - CHENNAI, TAMIL NADU, INDIA
May 25, 2019
June 20, 2019
A. This sounds like a powder issue not an application issue.
If with time the coated surface fades in colour and in gloss, when it was OK immediately after coating, then look at the powder. Same supplier? Same quality? Different batch?
It could also be an environment issue.? Is the material being subjected to the same environmental conditions? If for example you previously installed indoors, and are now installing outdoors in strong sun, then you will get different performance.
Something has changed if you get a different result. If the difference is only in service then the powder or the environment.
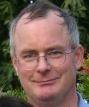
Geoff Crowley
Crithwood Ltd.
Westfield, Scotland, UK
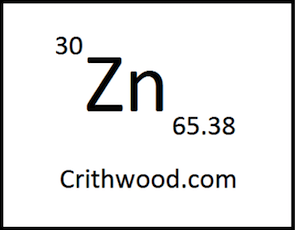
Q. Hello sir, we are powder coating aluminium diecast parts. After curing we see watermarks or cords (like powder flow after melting). We've done done all solutions, checked chemicals, changed powder. Please help us out.
swapnil jadhav- NALASOPARA WEST, India
July 24, 2019
September 2019
A. Hi Swapnil. Pictures sent to mooney@finishing.com for posting here would probably be worth a thousand words because readers may not draw the right mental image from "watermarks or cords".
Is this polyester powder? Please tell us about your shop's successes, not just your failures, so we have a good starting point: Is this a brand new installation and you have never successfully powder coated, or do you have substantial experience, and this problem just popped up? Do you normally powder coat diecast and only this one particular part is a problem, or you have only powder coated extruded aluminum before, or never done aluminum before?
Telling us you've already checked every possible cause of problems is somewhat helpful, but obviously something isn't right. I'm no powder coating expert but discoloration plus excessive flow sounds like it might be excessive baking either through too high a temperature or two much time.
Regards,
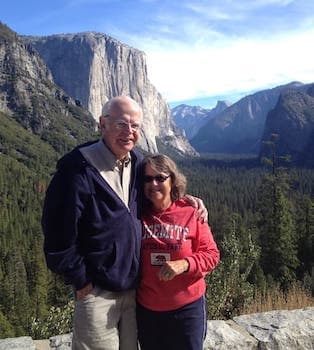
Ted Mooney, P.E. RET
Striving to live Aloha
finishing.com - Pine Beach, New Jersey
Q. Hi,
We are facing PEEL OFF COMPLAINT from Elevators doors.
This peel off from the beginning stage BUBBLES, and chips peel off observed doors.
Pre-treatment and powder coating every stage our quality person checked and confirmed after MOVING TO CUSTOMER,
also we are using chemicals and powders from reputed company manufactured, THEN WHY GETTING PEEL OFF?
- Chennai, Tamil nadu, India
September 30, 2019
A. Hi Dhinesh. Does your quality person do any adhesion testing? If so, what is the test?
Various substrates require different pretreatment strategies and it's possible that your pretreatment is correct for most of your work but not for those elevator doors. Adhesion to brass, aluminum, and galvanizing is quite problematic, for example, and adhesion to stainless can require pretreatment changes. If the material is cast, it can absorb problematic moisture. Please tells us what the substrate is, and what your pretreatment process is. Thanks!
Regards,
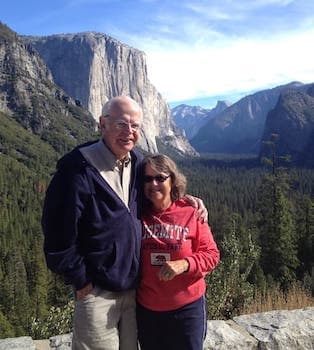
Ted Mooney, P.E. RET
Striving to live Aloha
finishing.com - Pine Beach, New Jersey
September 2019
October 2, 2019
Q. Hi,
We are using substrate - CRCA(TATA STEEL) 1.2 MM THICKNESS.
in substrate using rust preventive oil name QUAKER BRAND,
PRE TREATMENT TYPE HOT.
STAGES BELOW,
1.HOT DEGREASING
2.BORE WELL RAW WATER RINSE 1
3.BORE WELL RAW WATER RINSE 2
4.DERUSTING FOR OPTIONAL(ONLY FOR RUST COMPONENTS)
5.BORE WELL RAW WATER RINSE 1
6.PREACTIVATION
7.ZINC PHOSPHATING HOT TYPE
8.DM WATER RINSE
9.PASSIVAION
10.DRY OFF OVEN
PT CHEMICAL SUPPLIER NAME - CHEMITAL RAI(BASF GROUP)
POWDER MAKER NAME- JOTUN, AKZONOBEL,
- Chennai,tamil nadu, India
A. Hi again, Dhinesh. My experience with powder coating is rather limited and mostly book knowledge, but what an electroplater would probably do would be to take some sample parts and hand scrub them with pumice powder and a tampico brush, and maybe a small amount of detergent ... and then begin your pretreatment sequence again. Please try that if you can and see what you learn regarding whether failure to get the parts clean with your degreaser is the problem. Good luck.
Regards,
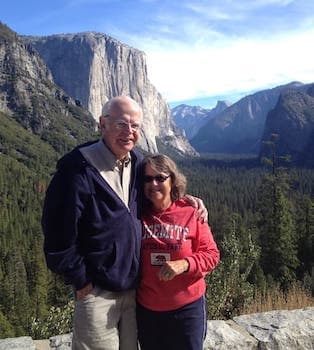
Ted Mooney, P.E. RET
Striving to live Aloha
finishing.com - Pine Beach, New Jersey
October 2019
Q, A, or Comment on THIS thread -or- Start a NEW Thread