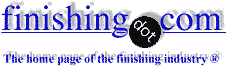
-----
Plating both outside AND inside of a tube
Quickstart:
Plating thickness is essentially proportional to the applied current and time (per Faraday's Law). But electricity wants to take the path of least resistance, so edges, corners, and protrusions get thicker plating, while recesses and inside diameters get lesser or none.
Some plating solutions (usually the more chelated or complexed ones) exhibit better "covering power" or "throwing power" than others. Addition agents (brighteners) can also help with covering and throwing power by being attracted to the high current density areas and somewhat covering/blocking/insulating them to steer the current away so it flows towards other areas. But to get coverage in IDs longer than their diameter may require "auxiliary anodes" within the ID and/or other specialty techniques
[editor appended this entry to this thread which already addresses it in lieu of spawning a duplicative thread]
Q. ID plating technics and suggestions and fixers
employee - Chennai
November 24, 2024
The corrosion resistance of finishes is often checked via standardized accelerated corrosion testing conducted in accordance with specifications such as ASTM B117 and ISO 9227.
Q. how to enhance my salts Paray in crimping hose alkaline zinc plating
Plant head - Chennai
February 8, 2025
A. Thicker plating or switching to an alloy zinc process are the general solution to increasing salt spray hours.
Luck & Regards,
Ted Mooney, P.E. RET
Striving to live Aloha
finishing.com - Pine Beach, New Jersey
⇩ Related postings, oldest first ⇩
Zinc Plating Thickness on I.D.
Q. We are zinc plating hubs for blower wheel (.0002-.0004). The hubs are .72 and .98 in diameter with various hole sizes .313/.314, .3755/.3765, .5005/.5015.
We drill and ream the holes to the nominal (using a hydromat) and check ok before plating. But after plating some of the hub's ID are undersize, ex .3127 instead of .313. These hubs most always are undersized by the ends of the holes. I understand that the is more of a chance for the zinc to build up here because of the electric concentration but by a factor to two or three times?
My question is - can it build up by a factor of two/three times?
Please advise and explain.
Thank you,
for Shops, Specifiers & Engineers
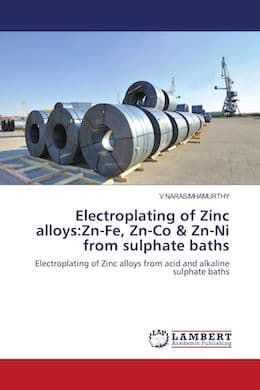
from eBay, AbeBooks, or Amazon
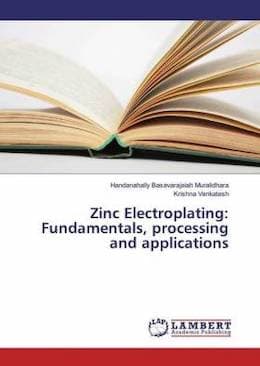
from eBay, AbeBooks, or Amazon
"Alkaline non-cyanide zinc plating with reuse of recovered chemicals" by Jacqueline M. Peden (1994)
from (U.S. EPA)
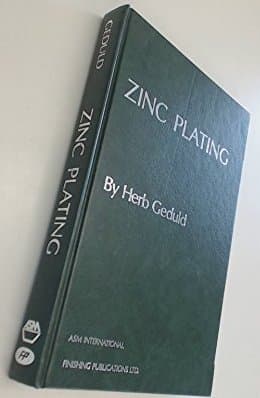
from eBay, AbeBooks, or Amazon
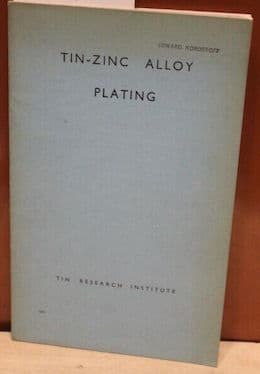
from eBay, or AbeBooks
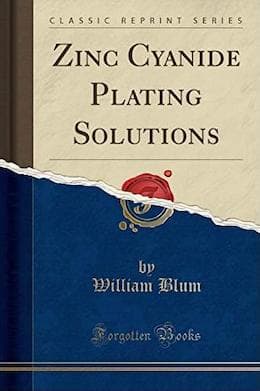
from eBay, AbeBooks, or Amazon
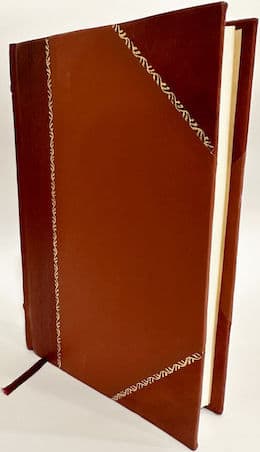
from eBay, AbeBooks, or Amazon
(as an Amazon Associate & eBay Partner, we earn from qualifying purchases)
- North Ridgeville, Ohio
2002
A. Yes, thickness variations of two or three times, or even more, is not a lot. However, you should determine if your plater is using an acid or an alkaline process as the alkaline processes offer significantly more uniform thickness, and it may be possible to reduce the thickness variation without redesigning the part. You should also tell us if the parts are racked or barrel plated.
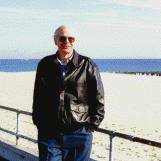
Ted Mooney, P.E.
Striving to live Aloha
finishing.com - Pine Beach, New Jersey
A. Kevin,
Because you are plating an I.D. you actually reduce the I.D. by 2x the plating thickness. We plate eye unions and we will spec the pre-plate I.D. oversize by 2x the upper specification of the plating thickness so as to be in specification after plate. However since yours is a close fit, (with I assume a shaft) you may want to plug the I.D. to prevent plating build up from changing the I.D. For your future reference, if you plate a thread your thread pitch will increase 4x the plating thickness. I hope this helps.
- Versailles, Kentucky, USA
A. Mr Ziegman:
I have been plating hubs similar to the ones you speak of for quite some time. I can relate to your problem because I have had parts over plate in this area. You are correct in your posting of concentrated electricity, or High Current density. Typically Chloride Zinc baths (acid zinc), because of their very high efficiency, can fluctuate in distribution well beyond the 2x you are referring to. First thing I would do is to inquire about your suppliers chemistry. If its alkaline and you can pinpoint some kind of frequency, I might have some other suggestions.
- Muncie, Indiana, USA
Thank you all for your responses. We are looking into the plating bath make-up as you have suggested. We are also looking into reaming the holes bigger with the anticipation of the hole closing up. If you have any other suggestions I welcome them and thank you in advance.
- N. Ridgeville, Ohio
Readers may be interested in these topics which offer insight into thread allowances for plated parts:
• Topic 2906 "Plating external threads: dimensional effects"
• Topic 22409 "Zinc Plating Thickness and Tolerance on Fasteners"
• Topic 12211 "Zinc Plating Internal Threads: dimensional changes & coverage issues"
I.D. rust in plated hydraulic tubes
Q. My company bends and assembles steel hydraulic tubes that get zinc plated. During the zinc process acid is used which removes the oil rust protection from the inside of the tubes. This causes the inside to rust. We then have to sandblast the id of the tubes to remove the rust as our acid cleaning would remove the zinc from the outside of the tubes. Is there a better way to clean the tubes after plating? These tubes are 1/4" to " diameter and 1 to 8 feet in length.
Gary RickertMorton, Illinois, USA
2002
A. It is not uncommon when nickel plating tubing work to finish the cycle with a dip in a phosphatizing process so the inside of the pipe gets rustproofed whereas the phosphating does nothing to the plated surface. I am not sure exactly how this would work in the case of zinc plating if the zinc surfaces need a subsequent chromate conversion coating, but hopefully it's food for thought.
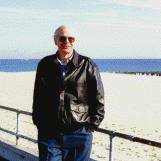
Ted Mooney, P.E.
Striving to live Aloha
finishing.com - Pine Beach, New Jersey
A. Gary,
I have one crazy idea and that's to employ what a professional pipe bender uses for tight radius bends in metals, particularly copper.
They use a material called 'ROSIN' ... it is poured into the pipe and sets rock hard. It is removed, after the pipe has been heat formed, going by memory, by just using hot water, ie. it's a water miscible material.
I'm not sure of the affect the plating acids might have but at least it's worth a try as it is as cheap as wurst, can be easily applied & removed. In other words it could act as a plug at each end.
May I suggest you approach a local specialist in pipe bending. And if this works, let us know, OK?
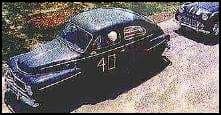
Freeman Newton [dec.]
R.I.P. old friend (It is our sad duty to
advise that Freeman passed away 4/21/12)
A. Some other fabricators of tubing that you describe have found that alkaline zinc gives them better results than parts plated in Acid Chloride Zinc. The main reason given, is that the Acid Zinc baths form an active surface on the inside of the tubes, which flash rust rapidly. The Alkaline Baths keep a passive surface which has less tendency to flash rust.
Make sure, that the tubing is free of rust prior to going into the plating tank. Many times the tubing arrives at the plater with considerable internal corrosion. Preplate pickling does wonders for such tubing. Post Plate corrosion on the insides usually necessitates stripping of the zinc, pickling to remove the oxide and replating. A costly and inefficient method.
Some firms specify proprietary silicated compounds after the plated part is chromated, to give longer storage times after plating. A good chemical manufacturer can assist you with that selection or option.
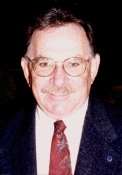

Ed Budman [deceased]
- Pennsylvania
With deep sadness we advise that our good friend Ed passed away Nov. 24, 2018
A. Hello Gary,
After chromate passivation, a good rinse followed by a water soluble lacquer dip may give temporary protection from flash rusting inside the tubular surface.Once dried, rust preventive oil may be applied.
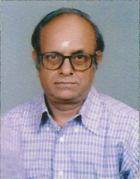
Subramanian Ramajayam
consultant - Bangalore, India
A. There are 2 issues at play here.
1. The main issue is stop putting the finish, acid and sand blasting on the inside. This is a big no-no in our world of fluid power. You are removing the tubing dia. The ID is just as important as the OD of the tubing. And if I call out for a .032 wall thickness it is not for the dia. it is for the working pressure. And so on; I can go on with the hydraulic issues but it will go on and on.
2. The answer is when you form the tubing and install the flare, nuts, etc. If present just install end caps so the inside is not effected. Or should I say contaminated. If no ends on the tubing then install plugs. Bottom line do not get any contamination inside of the tubing.
If you need help call a local hydraulic shop and get some advice. Remember you must not contaminate the inside of the tubing. It is important nothing is inside or whatever equipment your tubing is going onto will be effected. And always clean the tubing with the asap hydraulics hose/tubing cleaning system. This will remove any contamination left inside from forming. This is a bullet projectile that cleans the tubing inside.
- Downingtown, Pennsylvania
September 7, 2009
Q. We have tubing, usually about 3/8" ID to 1" ID that our customer spec calls to be CAD plated or Zinc plated. CAD is better but is becoming harder to find vendors and I am told that it will probably disappear over the next few years, I think due to environmental concerns.
Is there any way to get the inside of the tubing zinc plated or is there another process that I could convince my customer is equivalent to for corrosion protection? Presently, we have to coat the inside with LPS as a crutch.
Is it true that the zinc plating process will actually strip the ID of corrosion protection.
Thanks
Aerospace Manufacturer - Duluth, Minnesota
2006
A. Yes, simply running the parts through the necessary pretreatment steps will probably strip any previous cad or zinc plating from them. Electroplating is driven by current, and I'm sure that you can picture that virtually no current will flow from the anodes all the way to a spot on the inside of a tube because it will take the path of least resistance instead.
It is certainly possible to plate the insides but it may be prohibitively difficult depending on the particular parts and their value. Plating the inside requires "stringing" an auxiliary anode through the center of each tube and probably also involves some kind of pumped solution transfer because stagnant solution within the tube may not contain enough zinc or maintain the right balance.
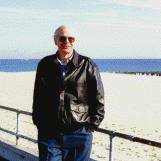
Ted Mooney, P.E.
Striving to live Aloha
finishing.com - Pine Beach, New Jersey
A. It certainly is not world class for aero parts but you can zinc plate in and out by hot dip galvanizing. Most commercial pipes and fittings are processed this way and have all their surface protected.
Guillermo MarrufoMonterrey, NL, Mexico
A. Hi there,
Electrolytic zinc plating will be really hard to accomplish inside the tube.
You can use hot dip zinc plating, or other process where you do not apply current, maybe Electroless Nickel.
Saludos.
- San Luis Potosí, México
A. Another method to plate zinc or cad for that matter, is using a brush plating process. We have experience in running electrodes down the ID's of pipes or tubes in order to get deposits of a variety of metals onto the surface.
There are several factors that must be determined at the onset of work; these include length of the tube and deposit thickness, but the process has been successful on previous applications
- Valencia, California
A. Yes, it is possible to plate inside tubes today. You will need in principle 2 main conditions: a, the suitable electrolyte; b, the matching internal anodes. As electrolyte I recommend alkaline zinc electrolyte and an internal auxiliary anode. With both of this you may come close to your target.
Rudolf Kempf- Haan, Germany
2006
Plating nickel and chrome inside a tube
Q. Is it possible to plate inside the tube in nickel and after nickel in chromium baths? The hollow is only 1 or 2 cm long
Bojan Koren- Bovec, Slovenia
September 24, 2014
A. Hi Bojan. The devil is in the details. In conventional plating with no special internal anodes and without solution pumped through the tube, a tube of 2 cm diameter or more may nickel plate 1-2 cm deep, which could total over 2 cm if you count from both ends. But a 1/2 cm dia "straw" will not plate on the inside.
How critical is the chrome? Because I think you have a good shot at getting full coverage of nickel, but only enough chrome coverage to just make it around the bend, not inside the tube. For non-critical components, I think a lot of people would be satisfied with that. Good luck.
Regards,
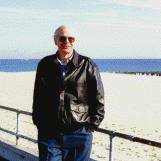
Ted Mooney, P.E.
Striving to live Aloha
finishing.com - Pine Beach, New Jersey
A. If you are after corrosion protection and a good wear surface, consider electroless nickel.
If you want it to look more like chrome, look into electroless cobalt. It is a bit more expensive but will make your life a lot easier.
- Navarre, Florida
Yes I know that electroless nickel has much better covering power, but we don't have it in our company and I have no experience with electroless nickel.
- Bovec, Slovenia [returning]
October 3, 2014
Q. I have a couple of questions about plating the inside of a tube...
1) should the flow be continuous within the inner diameter and is there a way to calculate the needed rate and
2) what is the best way to prevent the build up of plating on the bottom of the tube on the outer diameter (aside from masking it)?
- Belliare, Michigan, USA
October 6, 2014
?. Hi Dawn. The thread has wandered a bit, so we don't know if you are talking about zinc plating, nickel-chrome plating, or electroless nickel. What is the length and inside diameter of the tube? Is it made of steel? Thanks!
Regards,
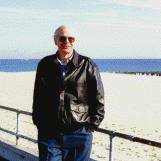
Ted Mooney, P.E.
Striving to live Aloha
finishing.com - Pine Beach, New Jersey
Q. Morning Ted,
I just hired in as new engineer. I have a chem eng degree so I have a decent understanding of chemical process and the mechanics of plating in general. I have a background in flash plating nickel (barrel-type) & yellow chromate but I've never done anything like this. We're dealing with DOM tubes, 32" long with varying inner diameters from 0.75" - 3".
I was just looking for some overall info on plating the inside of tubes just so I can understand what is happening (we are using auxiliary anodes down the lengths of the tubes). This is copper plate by the way. Things I'm trying to learn are 'Is flow supposed to happen through the ID', 'Is there a way to calc what optimum flow is,' 'what are different racking options', etc. This is an old (but very effective) process but there isn't anyone on-site that can truly explain "why" we do what we do. I'm just looking for some perspective.
Part of my responsibility is going to be to evaluate and optimize our current processes but I just need to understand what is happening before I can make any improvements.
Thanks,
Dawn
- Bellaire, Michigan USA [returning]
October 7, 2014
A. Hi Dawn. I haven't personally been involved in ID plating of long tubes like this, and hopefully someone else will tell us both about it. But we both know that as you plate the metal out of the small volume of plating solution inside a tube, its concentration will decrease to unworkable, and that's why you need flow. So you could calculate how much copper you are trying to plate and how much flow you would need for the copper concentration to not drop more than say 5 pr 10 percent, and assure that the flow rate is adequate to keep the concentration within the target range.
You might also calculate and/or measure whether there will be a temperature rise within the tube that may be problematic. I think the short answer is that there is probably not a flow rate that is too high for successful operation, but there is surely a flow rate that is too low, and you will be able to at least approximately calculate that. Good luck.
Regards,
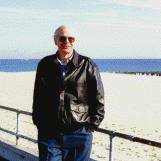
Ted Mooney, P.E.
Striving to live Aloha
finishing.com - Pine Beach, New Jersey
Q. Dear Professionals,
I am trying to zinc electroplate (gold colour) an item which is ID 7" x Length 12". Material is mild carbon steel and around 4 mm thick. We are located in Thailand.
I've found many small facilities which are unable to get the zinc plating to go full length of the OD^ID and one which can do it by adjusting the current on his machinery. As far as I know he has not run any jigs through the centre of the pc.
A few others have said they can do it but will need to make jigs and I suppose put an anode down inside the pc.
My problem is that we are extremely late with delivery and the one supplier who can do this work is painfully slow due to prior commitments. Anyone have a fix they can suggest?
- Banpong, Ratchaburi, Thailand
November 13, 2014
A. Hi Kirk. I assume there is a typo in your posting, and you mean "full length of the ID". An internal anode is a good idea considering the touch-and-go dimensions and the type of part, whereby if done right it seems to just barely work most of the time. I think it will be simpler, faster and cheaper than struggling to try to get by without it. But yes this will require special jigging that someone has to pay for.
If the quantity of parts is small, the special jigging can be accomplished in a short lead time but labor intensively with fairly standardized racks, plus copper wires, platinum clad titanium auxiliary anode material, and platers tape or masking materials. If it's a production job, custom designed racks, made of properly plastisol covered copper and stainless are no problem except for cost and lead time.
Regards,
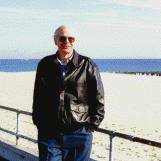
Ted Mooney, P.E.
Striving to live Aloha
finishing.com - Pine Beach, New Jersey
Dear Ted,
Thank you for your reply and yes, that was a typo, should be ID of course. I'll work with a couple facilities to get some jigs set up. The quantity is roughly 1,200 pcs and we're well late.
Thanks again.
Kirk Riddell [returning]- Banpong, Ratchaburi, Thailand
A. Hi.
Yes, an auxiliary anode inside the ID would do the trick. I'm not sure, but for an ID of 7", I would think an alkaline zinc bath should be able to plate inside the tube.
The beauty of alkaline zinc is its ability to plate inside low current density areas.
- Penang Malaysia
A. Thanks, Cheah, I don't disagree if the plating is not critical and "coverage" rather than specified thickness will suffice.
Luck & Regards,
Ted Mooney, P.E.
Striving to live Aloha
finishing.com - Pine Beach, New Jersey
Q. I want to do plating inside tube 101.6 dia * 1.6 thick bent tube, bend angle is 43 degrees, and after bending total length is hardly 300 mm, please guide me and give your suggestion.
RAMESH PANCHALexhaust silencer manufacturer - Mumbai, Maharashtra, India
December 10, 2014
A. Hi Ramesh. You didn't include the units in your dimensions, nor the type of plating, but since you are a silencer manufacturer, you probably mean that the tubing is 101.6 mm in diameter (4") and 1.6 mm thick (1/16"). I doubt that you will get consistent full coverage in a 300 mm bent length (11.8") without auxiliary anodes, but are you sure it is required? Zinc plating is sacrificial, and "good" rather than perfect interior plating might be satisfactory for this application. Are you sure zinc plating will hold up to the temperatures of your application?
Then again you may be contemplating nickel plating?
On the third hand, I thought most silencers these days were made of stainless steel :-)
Regards,
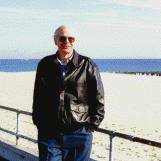
Ted Mooney, P.E.
Striving to live Aloha
finishing.com - Pine Beach, New Jersey
A. The Manhattan Project needed to chrome plate the inside of pipes for gaseous diffusion plant. They found an old guy and his son working in their garage; they used the pipe as the tank, put chemicals and electrodes in side pipe, capped it, rotated it and viola. I just recall recall reading about in the book Manhattan Project
David Christensenretired - Minneapolis, Minnesota USA
January 20, 2017
Q. Sir.
We want to plate zinc-nickel plating in 14 mm dia. tube. Plating must be in the ID of the tube. How should I do it?
Please suggest
With regards
D.Ravi
Plating shop - Chennai Tamil Nadu, India
November 29, 2017
A. Hi Ravi. You haven't told us what the tube is made of, or how long it is, but the general principle presented on this page and on thread 4153 is that you need to run an anode through the center of the tube, and probably flow solution through it as well. Good luck.
Regards,
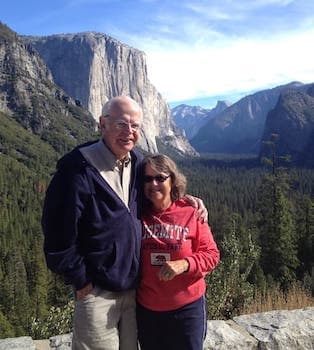
Ted Mooney, P.E. RET
Striving to live Aloha
finishing.com - Pine Beach, New Jersey
Corrosion proofing the ID of plated tubing
Q. Dear Sir,
What would be the best method to prevent corrosion appearing from the inside of small diameter steel tubes (diameter around 10 mm) I wonder about the conventional chrome plating but there is a issue regarding zinc plating on the inside of the steel tube. Other metal plantings like electroless Nickel or Hot dip galvanizing would be more expensive and not practical according to my situation. So please advice what would be the most economical and practical method
Thanks
Research and Development Officer - Sri Lanka
July 13, 2018
A. Hi Thanura. I don't understand what you mean by "there is a issue regarding zinc plating on the inside".
An approach I have seen is to do the chrome plating of the outside first, then go into a phosphatizing solution which leaves the chrome plating okay, but reacts with the bare steel inside diameter to create an iron phosphate coating. If you can afford to plug and unplug the tubes, you might have additional processing options.
I think the readers and myself have only a very vague idea of your situation so far.
Regards,
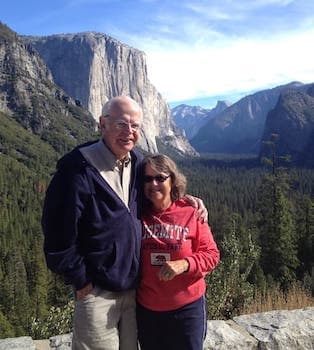
Ted Mooney, P.E. RET
Striving to live Aloha
finishing.com - Pine Beach, New Jersey
Q. I want to do plate a double ferrule fitting which is made up of carbon steel with the standard dimensions. And which plating do you recommend for this object.
I am not able to do an uniform plating in the internal surface of the part. So, please can you guide me and get me a solution.
Nikhil Sawant.- Maharashtra, India.
September 21, 2020
A. Hi Nikhil. Certainly electroless nickel plating would be easier than any electroplating process, and is well suited towards this. However, please tell us why you want to plate them so we know what platings sound useful and non-useful. What flows through them, hydraulic oils?
Luck & Regards,
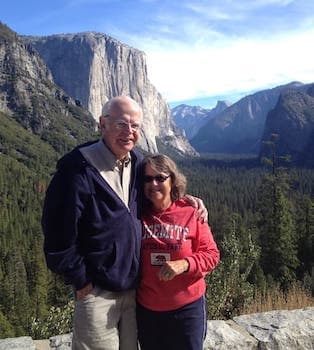
Ted Mooney, P.E. RET
Striving to live Aloha
finishing.com - Pine Beach, New Jersey
Q. Rusting inside M10 Thread, 45 mm (1-3/4") through hole, EN1AL Steel Hex, Zinc Plating?
We are manufacturing a steel hex nut with M10 threads inside, the total length of the component being 45 mm.
After zinc plating, more than 50% of the material remains un-plated in the middle of the tapped threads and after 2-3 days, rust appears.
External surface has no issue, it's only the inside thread having the problem.
Can anyone suggest a better method?
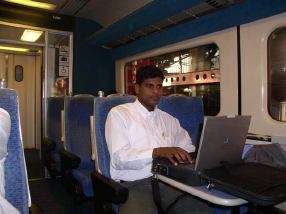
Jacob Ebanezer
forging & turning - Jamnagar , India
June 12, 2021
A. You have not said whether chloride, cyanide, or alkaline. In either case "throwing power" is maxed out, at the expense of efficiency, with higher Cl or CN or Caustic, and lower metal. If such an adjustment does not get the inside, then you must use an inside anode. An inside anode in this case may be a flexible steel wire with beads, the beads prevent shorting and the wire anodes the current on the inside.
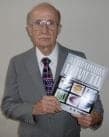
Robert H Probert
Robert H Probert Technical Services

Garner, North Carolina
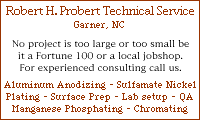
A. Hi Ebanezer. In addition to Robert's questions, we don't know if you are attempting to barrel plate this component, which will prove impossible.
The plating goes where the current goes, and pretty much in proportion to it; and the current certainly will not flow to the middle of the inside of this long narrow tube without the auxiliary anodes which Robert mentions.
The problem is not that this component is unplateable, it's that plating the inside of the thread will cost perhaps 20X or 50X what it would cost to barrel plate just the outside :-(
Luck & Regards,
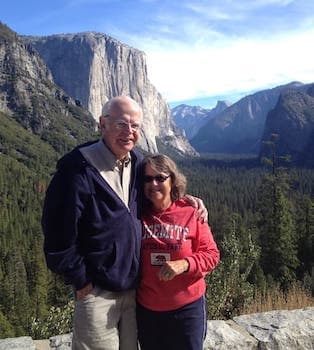
Ted Mooney, P.E. RET
Striving to live Aloha
finishing.com - Pine Beach, New Jersey
Q. Yes, we are doing barrel plating
Single-piece plating didn't work out well, as too much zinc plating was stopping go gauge to pass through easily.
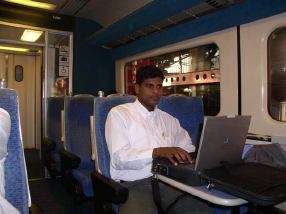
Jacob Ebanezer
forging & turning - Jamnagar , India
A. Hi again. Sorry to hear of your troubles with rack plating but I think you will never get electroplating coverage in the middle of a 45 mm (1-3/4") long M10, 8.38 mm (about 5/16") minor diameter female thread without auxiliary anodes -- but send a drawing to mooney@finishing.com for posting here if you think I'm misunderstanding.
Electroless nickel plating might work but is much more expensive than nickel plating.
Luck & Regards,
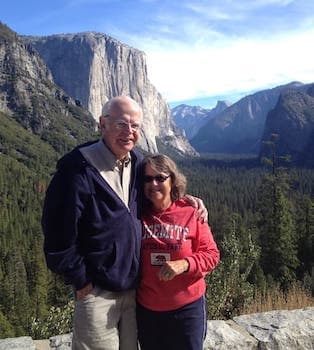
Ted Mooney, P.E. RET
Striving to live Aloha
finishing.com - Pine Beach, New Jersey
Q, A, or Comment on THIS thread -or- Start a NEW Thread