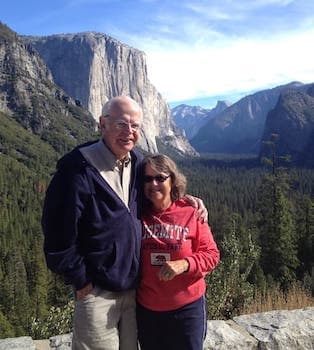
Curated with aloha by
Ted Mooney, P.E. RET
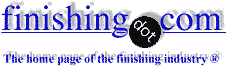
The authoritative public forum
for Metal Finishing 1989-2025
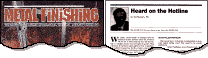

Jump to this related thread:
• Topic 2906 "Plating external threads: dimensional effects"
• Topic 22409 "Zinc Plating Thickness and Tolerance on Fasteners"
• Topic 51293 "Zinc plating blind holes / threaded holes"
• Topic 57493 "Zinc Plating Internal Threads: dimensional changes & coverage issues"
• or continue with -----
Thread dimensions after plating
Q. I am having a problem with electroplating zinc on steel. I am using the barrel plating process. The parts are all 3 and 1/2 inches or longer and are usually double ended studs with the hex at various lengths along the shank. I need at least 5-10 microns coverage. The problem is when I get the minimum required at the center of the hex, the both ends are overplated to the point that I can not even get the appropriate ring gage on the parts. If I plate to the gage, the shank has no plating at all. I have tried variations in the process including changes in load size, tumble time, bath concentrations, and current adjustments. Nothing seems to work at giving me an acceptable part. Is this the infamous "dogbone effect?" All advice is greatly appreciated. Thank you for your help.
William Travis BoylesAltoona, Pennsylvania
2000
A. Assuming you are using an acid zinc process (about 90 percent of zinc barrel plating is acid zinc), you can probably reduce the dogbone effect by going to a plating shop that offers alkaline zinc or cyanide zinc plating.
The thickness variations you are seeing are a direct reflection of the primary current distribution, which is what you will get in an efficient (acid zinc) process. You need a process which is less efficient at high current densities, so that some of the electricity going to the ends of the studs releases hydrogen and oxygen instead of depositing metal.
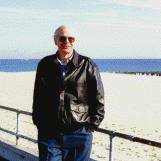
Ted Mooney, P.E.
Striving to live Aloha
finishing.com - Pine Beach, New Jersey
A. Mr. Mooney is correct in recommendation of the process change but you have to remember that the shank is a non-machined portion and baths which generate more hydrogen and plate evenly may leave the shank portion unplated as well on account of the plating depositing faster in the cut or rolled threads.
In my experience only Chloride Zinc baths are able to deposit on Stud shanks . The only remedy to this will be to ask for a greater dimensional tolerance before and after plating or use yellow or olive chromate to compensate for the reduced plating thickness. Regards,
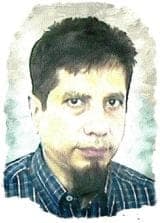
Khozem Vahaanwala
Saify Ind

Bengaluru, Karnataka, India
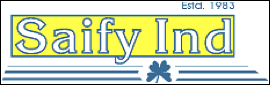
My kind friend Khozem treated my response too charitably :-)
I missed the facts that studs will be hardened steel, not mild steel, and it is indeed difficult to alkaline zinc plate hardened material, so switching from acid to alkaline seems more likely to compound your problems than to simplify them as he warns. More importantly, his hands-on experience easily trumps my book knowledge!
Regards,
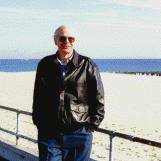
Ted Mooney, P.E.
Striving to live Aloha
finishing.com - Pine Beach, New Jersey
![]() |
Q. I am having same problem on double-ended studs except they are brass and bright nickel plated .0002-.0005. Parts are 2 inches long with 1-inch hex between the 2 10-32 threaded ends. One threaded end is 1/4-inch and the other 3/4-inch. Before plating, appropriate sample size passed QC ring gauge inspection. After plating, about 40% of studs at the short end either strip out when the nut is applied or strip the nut itself out. Some of them won't go through the "Go" gauge at all and some will only go part way. The long end that is threaded has not presented a problem. Can anyone explain this? Thank you in advance. Jere WrightDallas, Texas 2007 A. Hi Jere. Brass substrates are different than hardened steel, and nickel plating is different than zinc, so there might be a better discussion thread for your question, but some quick thoughts: Regards, ![]() Ted Mooney, P.E. Striving to live Aloha finishing.com - Pine Beach, New Jersey |
Multiple threads merged: please forgive chronology errors and repetition 🙂
Q. I have problems in assembling a nut onto a bolt. Basically, the bolt answers to the thread gauge before plating, but when we do the nickel plating on it, material builds up, thereby preventing the nut to go on. Is there any method of maintaining the thread on the bolt to any specific dimension before plating, so that the nut assembles onto the bolt without any difficulty.
Thanks,
Raghu RamanChennai, India
2001
A. You need to have undercut in threads. This means threads are deeper before plating. The nominal diameter is reduced to compensate for the plating thickness depending on the plating thickness. Some also drill larger hole and tap accordingly in matching part if you are buying standard bolts. Have you tried minimum zinc plating on the bolt? Some standard companies sell plated bolts which will fit correctly as they have undercut on bolts.
Payal MagCharlotte, North Carolina
Q. What is the typical thickness for Zinc Plating F70B4A? We are a precision metal manufacturer and have a requirement for a pitch diameter of a threaded component to be made "snug to No-Go for acceptance after plating"; however, my no-go gage will not go on even snugly. I've measured the actual pitch diameter and would like to not have a rework process. The thread is 13/16-24.
Elizabeth McClellanMorganton, North Carolina
2004
![]() |
External threads. Reduce the minimum pitch diameter by not more than .001" inch on all threads for which the tolerance specified does not exceed .0035 inch. For threads with the pitch diameter tolerance greater than .0035 inch, the minimum pitch diameter may be reduced by an amount equal to 0.3 times the pitch diameter tolerance, but not more than .0015 inch. Zinc plating will not normally "throw" into internal threads unless the diameter is .750 or larger or special probes are utilized. The same calculation can be used for internal threads. Thomas J LuniewskiMineapolis, Minnesota I don't know the specifics on that spec. Typically zinc plating is about .0003 in. thick. That means you will have to allow .0006 in. on the diameter. Todd OsmolskiCharlotte, North Carolina 2004 |
Q. Is a different thread gauge used for plated & unplated?
BRIJESH SRIVASTAVAIndia
India
A. Hi Brijesh. Yes!
Regards,
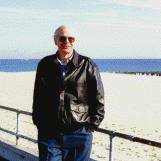
Ted Mooney, P.E.
Striving to live Aloha
finishing.com - Pine Beach, New Jersey
September 3, 2008
Thickness of Grade C of MIL-C-26074E
Q. The company I work for is still using this spec for plating carbon steel parts. We have encountered a question on the thickness of the plating for Grade C. It seems that the thickness should be regressing to a thinner coating for Grade C than for Grade A and B.
We have a small part that has #4-40UNC-2B threaded holes and when the plating is applied per Grade C is causes an excessive build up in the threads so that a thread gage (nor the screw) will no longer work in the threads. I was wondering if the call out for Grade C should actually be .00015, not .0015.
Wichita, Kansas
June 1, 2009
A. Hi Anna. I don't think that your interpretation is correct. Looking through earlier revisions it appears that Class C is 0.0015" thickness persists across all of them. Further evidence, besides the spec itself, is that an earlier revision had Class C deleted, and called for substituting Class B (0.0001") for it. Working to canceled specs is always a problem :-(
Luck & Regards,
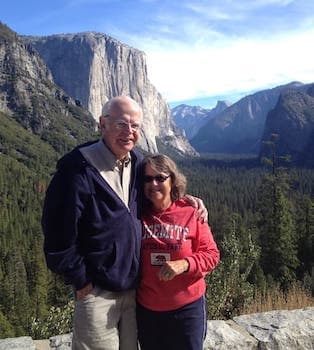
Ted Mooney, P.E. RET
Striving to live Aloha
finishing.com - Pine Beach, New Jersey
Multiple threads merged: please forgive chronology errors and repetition 🙂
Q. My name is Mike and I work for an aerospace company in the Quality assurance field. My question is "After cad plating hardware, do the plated threads still need to meet the drawing requirements or is it assumed that the threads met the requirements pre-plate"?
Michael SassLiverpool, New York
June 1, 2011
![]() |
A. Mike Colorado Springs, Colorado A. Hi Michael, Yeovil, Somerset, UK |
A. Hi Mike
This is an age old problem. The answer should be clearly shown on the drawing - but it rarely is. The only person who can clarify the position is the designer - his name should be on the dwg. Don't waste time speaking to the buyer. He will not have the authority or probably the knowledge to make the decision. Make the point that you cannot risk your company's reputation on a wrong guess and that the parts will not be plated until you have written confirmation (guess who will be blamed if you get it wrong). If you make enough fuss you may save yourself and others having the same problem on future orders.
It is possible to buy tap and die sets with "built in" plating allowance but by the time the parts hit the plating shop it is far too late.
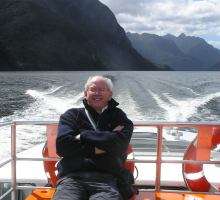
Geoff Smith
Hampshire, England
A. I have worked in aircraft fastener quality for 40+ years. The parts as finished must meet all drawing dimensions within the tolerance limits listed on the drawing. Usually the procurement specification will have that statement within it.
Donna WarnerNew Century, Kansas
Q. I have problem in inspections.
1) Which thread plug gauge & thread ring gauge I can use before & after plating (6h or 6H)?
2) Which thread plug gauge & thread ring gauge I can use before & after blackodizing (6h or 6H)?
Pune, India
February 23, 2013
A. - 6h ring gauge
AJAY SinghJanuary 18, 2014
India
Zinc plated external thread M36 x 1.5 6g
Q. We need to make finish product with zinc chrome and thread size check after chrome.
So which size of GO NOGO gauge we need to use during machining?
Or which dimensions we need to make thread?
India
March 16, 2020
(courtesy of https://www.engineersedge.com)
A. Hi Himanshu. Although the chromate conversion coating will have no effect on the dimensions, someone must specify the thickness of the zinc plating before your question can be answered because the plating can range from 5µm nominal for mild service to 25µm for very severe service.
Once the thickness is known, guidelines like MIL-S-7742 can be applied, wherein the short answer is that plating adds 4X the plating thickness to the pitch diameter. Good luck!
Regards,
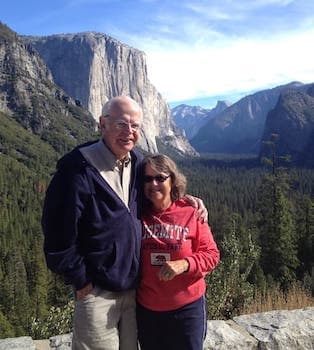
Ted Mooney, P.E. RET
Striving to live Aloha
finishing.com - Pine Beach, New Jersey
Q, A, or Comment on THIS thread -or- Start a NEW Thread