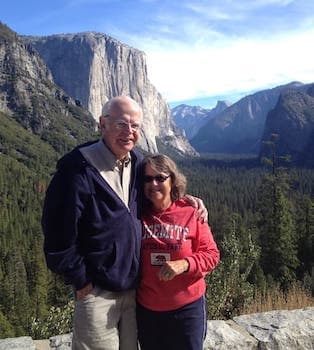
Curated with aloha by
Ted Mooney, P.E. RET
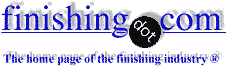
The authoritative public forum
for Metal Finishing 1989-2025
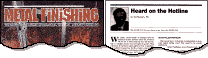
-----
Zinc-nickel Plating, misc. Q & A's

Q. We are currently producing parts with MIG MAG, and these parts then undergo a Zinc-Nickel application (bath) and then KTL (cataphoresis) painting.
After the Zinc Nickel application we get these black spots. Almost always in the same areas on the welding cords (some less intensive, some more intensive). And we do not understand where this is coming from.
- Carregado, Portugal, Europe
August 4, 2023
MIG = metal inert gas
MAG = metal active gas
ISO 4063
A. Hi Vasco,
Proper plating can only occur on pure clean metal, and I suspect that welding slag and oxidation is not fully and reliably removed.
Before sending the components through the line, thoroughly scrub those welding lines on a half-dozen or so with a scrub brush
⇦ this on
eBay or
Amazon [affil links] well wetted with pumice
⇦ this on
eBay or
Amazon [affil links] and Spic and Span
⇦ this on
eBay or
Amazon [affil links]
or similar detergent. Ask the person who is doing this to really overdo it, and if they are satisfied that the weld line is truly clean. Then rack the parts for the regular cleaning and plating cycle.
When you are satisfied that this solves the problem or does not solve the problem, please get back to us.
Luck & Regards,
Ted Mooney, P.E. RET
Striving to live Aloha
finishing.com - Pine Beach, New Jersey
Q. Hello Ted
Thank you for your reply.
We made 2 attempts regarding scrubbing:
1) Scrub the weldcords before the welding and then go through the zinc process. Result was ok.
2) Scrub the part after the zinc process and then go through the zinc process again. Result was ok.
We also made a different attempt:
We passed an unscrubbed part (with the black spots) through the zinc process 2 times in a row.
This first time it came out with the black spots.
The second time it came out with much less black spots.
But our focus is to get rid of these black spots without the need to rework parts or having to pass them 2 or more times through the same processes.
What we changed in our process in the past:
1. We introduced Gas Stargon C15 with 15% CO2 (DIN EN ISO 14175 M20 (Ar-CO2) onto the welding area (while welding) in the beginning (20L), during and at the end of the welding process to prevent contaminations - results improved.
2. We passed from a conic shaped nozzle to a cylindrical shaped nozzle to concentrate the flow of the gas onto the welding area - results improved.
We do not think this contamination is coming from the material we are welding, nor the welding wire, since the black sports are almost always in the same areas.
What else can we do? What else can we test?
Thank you for all the help in this matter
- Carregado, Portugal, Europe
August 9, 2023
A. Hi again, Vasco.
You may have misunderstood the intention of my posting. I am not suggesting that parts be manually precleaned as a permanent solution, I was suggesting that you try this as a way of determining whether the problem results from your existing cleaning process being inadequate -- and you apparently proved that it is inadequate.
Sorry, I have no welding expertise and cannot predict the effect of those welding changes. All I can say based on the results of your experiments is that your current cleaning process is not adequate for the current condition of the components.
So it is time to talk about your mechanical and then your chemical cleaning/pretreatment steps before zinc plating and how to improve them.
I have no idea how large those parts are, but is vibratory finishing done? If not, is it a possibility?
Luck & Regards,
Ted Mooney, P.E. RET
Striving to live Aloha
finishing.com - Pine Beach, New Jersey
⇩ Related postings, oldest first ⇩
Q. Hi
I need the process for Zinc-nickel plating of metal parts (9SMn28K, SAE 1215)
I have the standard - DIN EN ISO 4042-P3R
Many Thanks
Shalom Barr- Ashkelon,Israel
2002
Q. I have a challenge. I hope someone can help me up.
1. Is Zinc-nickel plating solderable?
2. Can Zinc-nickel be applied on aluminum?
We used to silver plate our aluminum microwave electronic equipment parts. This part is soldered on another also silver plated part for best contact between two parts. Keeping that contact is critical for our product. Right now, our product will be exposed to the harsh environment. In this situation the silver plating is going to change the color to black (corrosion). It looks terrible. We need some kind finish which is much more stable than silver plating, but solderable on substrates of aluminum.
Thanks,
Xiaoling- Montreal, Quebec, Canada
2003
A. I have heard of Zinc/Nickel being tack welded, but not soldered. Also, you can apply the alloy to Aluminum if needed. Please remember that the purpose of Zinc/Nickel originally was to serve as an alternative to Cadmium plating on steel. Both are sacrificial, but the Cadmium is both toxic and a carcinogen. On Aluminum use good preparation including a good Double Zincate.
You may wish to investigate Tin/Zinc plating. It can be applied to aluminum, is solderable, and can be plated from either a neutral or alkaline solution. You can check your vendors for names of products.
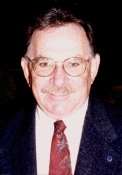

Ed Budman [dec]
- Pennsylvania
With deep sadness we advise that our good friend Ed passed away Nov. 24, 2018
2003
Zinc-Nickel plating of nails for pressure treated wood?
Q. Part of our business is the zinc plating of 2.1/3.1 dia. nails for our customer who exports some to the US. We are told that because wood preservatives are no longer allowed to contain Arsenic there is a move towards a zinc/nickel requirement. For us this would be a major investment in new plant and any feedback as to this possible change would be greatly appreciated.
Many thanks,
Russell WaitePresswork /Stampings and zinc plating - Ulverston, Cumbria, England
2003
A. Hi, Russell. Indeed the older grades of pressure treated wood have been banned and the newer grades are heavy in copper, which causes very rapid corrosion of zinc plated nails.
As a personal anecdote the deck/dock boards where I live always get too rough and splintery after several years and rather than redoing the entire deck I am in the habit of replacing the worst dozen or so boards each year. The nails I had long been using did not survive even a single year in the new pressure treated boards.
I don't know for a fact that zinc-nickel plated nails will be any better because this is not atmospheric corrosion but galvanic corrosion. The most common satisfactory nails, other than stainless steel, are surely hot dip galvanized. Good luck.
Regards,
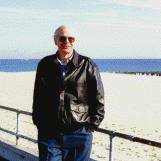
Ted Mooney, P.E.
Striving to live Aloha
finishing.com - Pine Beach, New Jersey
Zinc Nickel Plating in Military applications
Q. What Types of Chemicals is Zinc Nickel resistant to? i.e., JP4, JP5, Coolants, etc.
Thanks
Pat Haleharsh environment connectors - Naugatuck, Connecticut, USA
2003
A. Pat, zinc nickel electroplated steel is currently being used for fuel tanks on automobiles. The zinc nickel coated steel typically has an epoxy coating applied prior to the parts being formed. It is the combination of the pretreatment, epoxy coating and zinc nickel substrate which provide the resistance to the fuel and the corrosive environment, not just the zinc nickel.
Roy NussTrevose, Pennsylvania, USA
A. Hi,
While Roy answered Pat's question very well, and I learned a lot from it, it should not be interpreted that zinc-nickel plating is never used "stand alone". To the contrary, almost anything that is zinc plated can probably benefit from the additional corrosion resistance of zinc nickel plating instead.
Regards,
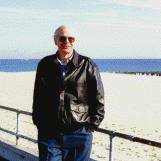
Ted Mooney, P.E.
Striving to live Aloha
finishing.com - Pine Beach, New Jersey
ZINC-NICKEL PLATING CHEMICALS REQUIRED
RFQ: WE NEED CHEMICALS FOR DOING ZINC-NICKEL PLATING. IN INDIA. WHO IS THE SUPPLIER? IS THERE ANY POSSIBILITY TO GET THE CHEMICALS IN INDIA?
R.Ramarao Yalamanchiplating shop - Hyderabad, Andhra Pradesh, India
2004
Ed. note: This RFQ is outdated, but technical replies are welcome, and readers are encouraged to post their own RFQs. But no public commercial suggestions please ( huh? why?).
Zinc-nickel plating on aluminum
Q. Hi. I'm currently seeking to realize a zinc-nickel plating on aluminum parts.
For that, I have to make a double zincate.
In order to not dissolve my zincate in the zinc-nickel bath (which is very alkaline), I have been told to make a chemical nickel on my zincate.
But the cost of that kind of treatment is too expensive, so I would like to find an other way to realize my deposit.
I have also heard about a zinc plating realized with a cyanide zinc bath (less alkaline than zinc-nickel baths) before the achievement of the zinc-nickel plating.
Could you give me any advice to realize this treatment and, as far as possible, others ways to make my zinc-nickel plating.
Thanks for your help.
Student - France
2007
Q. I would like to know the standard which is used for evaluating the Zinc nickel parts with base metal as aluminium.
RAMESH CN- Bangalore, KARNATAKA, India
January 16, 2013
A. Hi Ramesh. There are no proper standards except those which were written into the purchase order :-)
So if you are in QA, that's what you'll need to find. but if you are writing a purchase order and spec'ing parts, standards are available from ISO, ANSI, military, etc., and a starting point might be ASTM B253 "Standard Guide for Preparation of Aluminum Alloys for Electroplating" and ASTM B841 "Standard Specification for Electrodeposited Coatings for Zinc Nickel Alloy Deposits".
Good luck!
Regards,
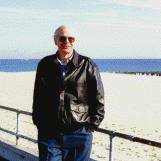
Ted Mooney, P.E.
Striving to live Aloha
finishing.com - Pine Beach, New Jersey
Color of Zinc-Nickel plated bushing
Q. WHAT IS THE APPEARANCE (COLOR) OF A ZINC-NICKEL PLATED BUSHING?
Gersain VejarSheet metal shop employee - Gardena, California, USA
2007
A. Alkaline Zn-Ni is a semi-bright coating. Take a look at aftermarket parts made for VW, Mercedes, or some other European automotive manufacturer, they commonly use this coating on fuel filters, etc.
Don't expect the "jewelry" bright look you get from zinc plating/clear chromate, particularly acid zinc. (I'm not familiar with the acid Zn-Ni process; it seems to me that the alkaline bath is more common and easier to run) But, as an old plating foreman I used to commiserate with, when his OC inspectors rejected parts for dull appearance, "the protection is there." Alkaline Zn-Ni is not the easiest process to run, nor is it much cosmetically, but it is a great finish when it comes to preventing rust.
That's the whole idea, at least it ought to be.
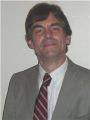
Dave Wichern
Consultant - The Bronx, New York
2007
Is this part suitable for Zinc-Nickel plating?
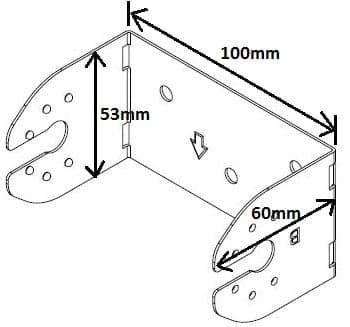
Q. Is the steel bracket suitable for Zinc-Nickel plating process?
The proposed process is Zinc-Nickel 0.0003" min thickness, 12-17% Ni Alloy, with Black Chromate and Organic Topcoat.
The steel stamping is made using a progressive die.
Dimensions of bracket are roughly 100 x 53 x 60 mm, material is 20 ga 1018 steel.
Quality Engineer - Burbank, California, USA
August 6, 2019
Q. Hi all I'm new here and new to electroplating. I'm in the process of setting up my first electroplating setup and have been given a load of new nuts and bolts to be plated but they are already zinc plated in a silver finish and need to be yellow.
I have purchased a hobby plating zinc nickel kit and my question it this, can I plate straight over the existing zinc plate or will it have to be stripped off completely and started again?
Any help greatly appreciated.
Thanks
C
- Swansea, Wales
September 20, 2021
A. Hi Cee. If you were a production plater, the answer would be yes you can proceed directly to plating over what you've got AND yes you have to strip them ... because sending the parts through an electroclean tank will strip the chromate anyway, and sending them on to the HCl acid dip will strip the zinc anyway.
I don't know exactly what you intend to do for pretreatment, but the chromate must be removed, and the existing zinc plating must be at least acid activated.
Luck & Regards,
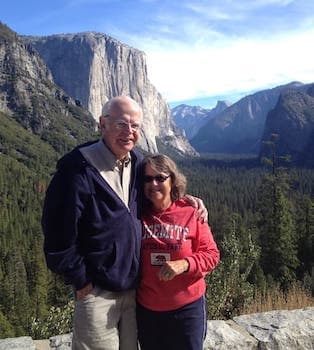
Ted Mooney, P.E. RET
Striving to live Aloha
finishing.com - Pine Beach, New Jersey
September 2021
Q. Hi Ted thanks for the reply I'm just doing the plating for restoration projects. I have purchased [name of hobby plating supplier deleted by editor] zinc nickel kit so I'm using the chemicals supplied within that kit it has an acid pickle for before the electrolyte. You're saying I need to be stripping the chromate -- how is this done please?
I have had some success but somehow I keep getting what look like burn marks on the bottoms of some of my pieces any ideas how this is happening and what I can do to prevent it?
Thanks again hope to hear from you again.
- Swansea, Wales
October 11, 2021
A. Hi again, Cee. The basic issue is that you can only successfully electroplate onto a waterbreak-free clean metal surface, and a chromate conversion coating is not metal.
The problem that arises for a hobby plater is that the simple way to remove a chromate conversion coating is to make it anodic in a strong caustic solution (similar to an electrocleaner) but this definitely generates hexavalent chromium -- the toxic, carcinogenic thing that made Erin Brockovich famous. A plating shop with a wastewater treatment system and employees with haz-mat training can easily deal with this -- a hobbyist not so well.
I guess what I would so is, while wearing a good dust mask, sand off as much of the thick chromate as practical, then immerse the part in an inhibited acid pickle, and assume that undercutting will occur, so as the zinc plating is removed, with it will go the chromate.
This site has approximately a quarter million questions posted, the majority having to do with plating defects, so please understand that it is rarely the case that anyone can get a quick answer to "this is what I see, what caused it?" :-)
Usually we'll need good well-focused, representative, photos of the defect (attached in e-mail to mooney@finishing.com for posting here) together with some detailed data about what you are doing (concentration, temperature, time, surface area, volts & amps, sketches or photos of the arrangement) to move the guessing game along productively. 'Burning', if that's what it actually is, is caused by excessive current density for the situation, and is usually most pronounced at corners & edges because those are the areas which often receive the most current. 'Electricity follows the path of least resistance' is usually a helpful truism. But if your kit doesn't include a cleaning step, or at least cleaning instructions, you need to start there. You need exceptional cleanliness of the surface for successful plating.
Luck & Regards,
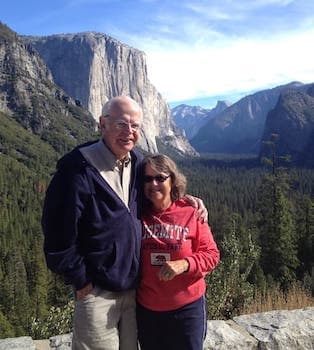
Ted Mooney, P.E. RET
Striving to live Aloha
finishing.com - Pine Beach, New Jersey
October 2021
Q. What is the best approach to remove zinc plating from fasteners and subsequently apply nickel plating?
The nickel coat is more durable than that of zinc, I presume?
Or the whole exercise is considered futile and I should retain the zinc coated fasteners?
I am currently restoring an old motorcycle and would like to nickel plate the zinc coated fasteners I purchased.
Many thanks in advance for your time.
Reuben
- New Jersey, USA
October 8, 2021
A. Hi Reuben. Although your question involves nickel plating, which is a very different thing than zinc-nickel plating, we added it to this thread because C B Evans just went through the same question as you about stripping the existing zinc plating, so that discussion should be applicable for you.
Although you're perfectly welcome to attempt zinc plating, zinc-nickel plating, or nickel plating there is one very big difference between them which refutes your "nickel coat is more durable than that of zinc, I presume?. That difference is that zinc and zinc-nickel are sacrificial coatings offering cathodic protection to steel, whereas nickel plating is at best a barrier-layer plating, but at worst it's anodic to steel and promotes the rapid rusting of steel. You are probably aware that steel boats and ships are often equipped with zinc anodes, the purpose of which is to sacrificially corrode to protect the iron/steel; ship anodes cannot be made of nickel because nickel is more noble that iron and the system would work exactly oppositely: the iron would corrode to protect the nickel.
Thus, imperfect zinc or zinc-nickel plating with a pinhole or porosity still offers substantial protection to the fasteners. Nickel plating must be perfect, completely free of pinholes & porosity, to function as a barrier coating; if a pinhole exists, the presence of the nickel will cause the fastener to sacrificially corrode. Thus it's usually not the right coating for a beginning hobbyist to apply if he is looking to add corrosion protection. If you want nickel plating, either buy nickel plated fasteners, or get very good at nickel plating :-)
Luck & Regards,
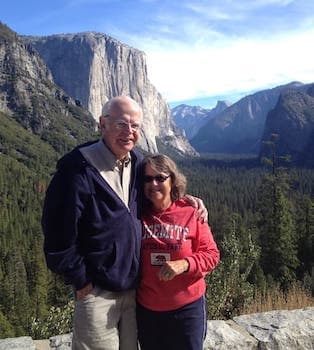
Ted Mooney, P.E. RET
Striving to live Aloha
finishing.com - Pine Beach, New Jersey
October 2021
Q, A, or Comment on THIS thread -or- Start a NEW Thread