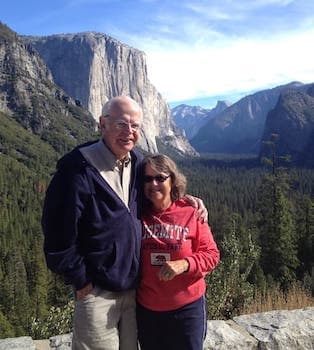
Curated with aloha by
Ted Mooney, P.E. RET
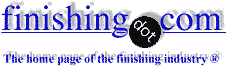
The authoritative public forum
for Metal Finishing 1989-2025
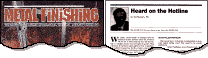
-----
Galvanic corrosion (electrolysis) Aluminum & Stainless Steel
Q. Hello all,
I have a few questions/concerns as it pertains to galvanic corrosion in regards to various surface finishes.
I'm looking to mate a Aluminum flanged connector between an Aluminum substrate & a Stainless fastener. This will be for an outdoors application, so galvanic concerns are warranted.
My question is in regards to the surface finishes & how they play into the galvanic pathway, as I am obviously trying to protect the Stainless from corroding the Aluminum.
Do I need to worry about any interactions between the connector's sacrificial plating & the outer metals, or is the only concern in separating the stainless/aluminum with a sacrificial plating?
Diagram of galvanic pathway comparisons:
1) Aluminum <-> Plating = Aluminum = Plating <-> Stainless
2) Aluminum <-> Aluminum <-> Stainless
Platings that I am considering: Nickel-PTFE & Zinc-Nickel
Thanks,
Matt
- Atlanta, GA
January 11, 2022
A. Hi Matt. If I am understanding you, your question is, when it comes to galvanic corrosion, whether only physical contact counts (your condition 1, with aluminum and stainless not actually touching each other because plating is between them) or whether electrical contact counts (your condition 2, because electricity will flow between all these metals). I think it's actually a bit of both, so let me start with a steel ship and a zinc anode to explain why ...
A steel hull sitting in salt water is fully immersed in a conductive electrolyte, so even though some steel area on the hull may be several feet from the zinc anode it remains protected because there is a metallic path for the electrons, and an electrolyte path for the ions, and those two paths are what is needed for galvanic currents to flow.
Your parts are metal in contact with each other, so the path for the electrons is complete in your case. But when objects are not immersed but merely partially wetted, a factor that might come into play is whether there is an electrolyte path. If you have a very thin tiny plated washer between stainless and aluminum, droplets of conductive electrolyte (salty water) will span from the aluminum to the stainless, providing an ionic path, and the plated washer is offering no help in my estimation. But if the plated item were a stand-off, significantly separating the stainless from the aluminum, it's far more likely that there is no electrolyte path from stainless to aluminum.
So my assumption would be that the intervening plated item is of no help on small close-fitting stuff where salt-laden water droplets connect the stainless to the aluminum anyway, but is of value on bigger stuff.
Luck & Regards,
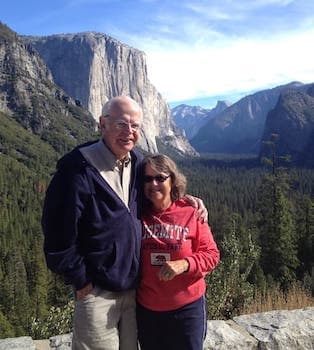
Ted Mooney, P.E. RET
Striving to live Aloha
finishing.com - Pine Beach, New Jersey
Q. Ted,
Thanks for the reply. That makes a good amount of sense in terms of separating parts -- I will definitely keep that in mind!
The gist of my original question pertains to the interaction of various platings though. In a bare Aluminum-Stainless joint, the concern would be the galvanic incompatibility between the two metals. However, if I have the Aluminum Zinc-plated (for example's sake), do I now need to worry about the galvanic interaction between the zinc plating & the stainless? Or is simply having a sort of sacrificial coating between the two original substrates enough?
-Matt
- Atlanta, GA
January 13, 2022
⇩ Related postings, oldest first ⇩
Q. I have a client contemplating thermal sprayed aluminium to his traveling screens at a power station. Would there be a galvanic or sacrificial action where aluminum is in contact with stainless steel in a wet environment?
Greg N [last name deleted for privacy by Editor]thermal spray - Victoria, Australia
1998
A. Aluminum and stainless steel are far apart enough in EMF to cause significant corrosion in a moist salt water environment.
An alternate that might work is nickel aluminide. I really like the metallographic results from a small system from TAFA. Beautiful laminar coating. virtually no porosity. It is a dual wire system. Miller has a big one but is too big for most work unless you are doing aircraft carrier anti-skid on the decks.
I would try one and see how it worked. If it worked okay for several weeks, do them all.
James Watts- Navarre, Florida
Q. I was wondering if you could describe in 50-100 words galvanic action in metals, in general terms. I'm currently studying and cannot find any info describing what takes place in this process.
Much appreciated, Thank you.
Christopher C [last name deleted for privacy by Editor]- Gold Coast, Q,ld, Australia
1998
A. Sure, Christopher.
Picture a dry cell battery. The battery consists of two different metals: the shell, which is the negative pole, is made of one metal (for example, zinc); the rod is made of a different more noble metal (for example, carbon) and is attached to the positive pole. In between the rod and the shell is a conductive gel or glop. For the battery to provide electricity (for you to use it), you have to connect wires that provide a metallic path from negative to positive that electrons can follow.
What happens is electrons travel from the negative pole, through the wire to the positive pole. This leaves a deficit of electrons at the negative pole. Some of the atoms of the negative pole (zinc shell) have thus been converted from metallic (neutrally charged) state to positively charged ions which dissolve into the solution and migrate through the glop and reach the carbon rod. The positively charged ions meet the electrons, which reduce the ions back to metallic state, i.e., the zinc plates out onto the carbon rod. At some point all the metal from the shell dissolves, or the rod gets completely coated with metal from the shell, so there is now only one metal exposed instead of two, and the battery is "dead".
Dissimilar metals in a device comprise such a battery regardless of whether we want them to or not. If you have two different metals, and they are sitting in salt water or another conducting liquid, you've got a battery. If you now provide a metallic path between the two metals (either a piece of wire or just bolting them together), the battery is "running", i.e., the more active of the two metals is corroding.
Luck and regards,
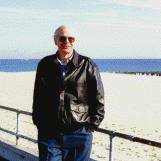
Ted Mooney, P.E.
Striving to live Aloha
finishing.com - Pine Beach, New Jersey
Multiple threads merged: please forgive chronology errors and repetition 🙂
Do you know if there is galvanic action between stainless steel and aluminum?
Udom Hungspruke- Newark, New Jersey
2002
![]() |
2002 I was intrigued by this question, and thought I would add my 2 cents: It's difficult to make a precise determination as to the potential for galvanic corrosion in your particular application without knowing the exact alloys involved, and the environment that the materials will be subjected to. I would have to say that there is a good chance that you will experience corrosion in the aluminum component. The fact that you are using stainless does not, in other words, prevent this phenomenon. Scott Dupre- Fall River, Massachusetts YES ! Go to the electromotive series in any high school chemistry book. ![]() Robert H Probert Robert H Probert Technical Services ![]() Garner, North Carolina ![]() |
A. Everyone is beating around the bush! This is a terrible combination with only (perhaps) magnesium and gold in contact worse. Steel and stainless in contact with aluminum historically were coated with cadmium which galvanically is quite close to aluminum. If cad isn't available or permitted, zinc-nickel plating has been touted by Boeing and others as a suitable cad replacement. Another alternative, albeit expensive, would be aluminum plating or ion vapor deposited aluminum on the stainless steel member. Look for processes Alumiplate and/or Ivadize for aluminum deposition processes. Galvanically speaking .... GOOD LUCK!
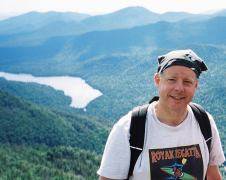
Milt Stevenson, Jr.
Syracuse, New York
2002
Stainless steel street rod uses aluminum rivets. What now?
Q. I am planning a street rod chassis built out of 5052 or 3003 aluminum sheet. I would like to make the outer portion of the frame from stainless sheet (likely 304). The two metals would be riveted with solid aircraft rivets (alum) and bonded with 3M structural adhesive .
I understand that there are serious issues with galvanic corrosion between these two types of metals. Any suggestions on method and material to use for a sacrificial anode? Could the anode simply be wired to the stainless steel, or is every point of contact (rivet) a separate galvanic connection. Periodically changing the anode bar would not be an issue if that solves the problem. Any help would be greatly appreciated.
Just a bit of clarification... The car will basically be a monocoque construction. The main "rails" will consist of rectangular boxes made from formed inner and outer sections. The inner section will be aluminum, and the outer section will be stainless steel. The title to the post made it sound like only the rivets would be aluminum. Don't know as it makes any difference, just wanted to clear that up.
Ray KaufmanInstructor - Latrobe, Pennsylvania
November 19, 2008
A. Hi, Ray. Regardless of galvanic corrosion issues due to the connection of aluminum to stainless or anything else, aluminum should always receive some sort of surface finish. Anodizing would be ideal from a corrosion resistance standpoint but can bring some metal fatigue issues with it. Chromate conversion coating should be good, either left bare or preferably painted.
I cannot promise no galvanic corrosion, and would suggest that you insulate to the extent practical with dielectric material or special sealants as the book knowledge goes. But I can say that experience seems to show that galvanic corrosion between stainless and aluminum is usually nowhere near as severe as it may appear at first blush from looking at their electrochemical potentials. This may be because both stainless and aluminum have a reasonably good tendency to self passivate. Stainless fasteners are widely used on anodized aluminum structures such as helicopter platforms, building railings, and so on. Please see letter 27167 and follow the link for some apparent assertions that galvanic corrosion in many instances is not a problem.
It is not the stainless that will corrode, but the aluminum, so that is what would have to be sacrificially protected with magnesium anodes. But, because this is a car rather than a boat, the anodes would only be effective while the car was soaking, drenching, wet :-)
You might look into active (electronic) anodic protection systems. I have no experience with them, but some say they work. Good luck.
Regards,
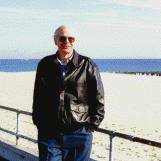
Ted Mooney, P.E.
Striving to live Aloha
finishing.com - Pine Beach, New Jersey
Thanks Ted.
I will look into the electronic anode protection. I'm glad you brought up the point about the metal needing to be wet for the anode bar to work. Makes sense, but I hadn't thought about needing the electrolyte in the picture...
- Latrobe, Pennsylvania, USA
December 21, 2008
![]() |
A. You'll only have a problem if wet for significant time. Dry, there will be no galvanic corrosion. ![]() Jeffrey Holmes, CEF Spartanburg, South Carolina A. In the same way that the sacrificial anode will only work while the car is wet, so the primary corrosion mechanism that you are seeking to prevent, will also only operate while the car is wet. ![]() Bill Reynolds [deceased] consultant metallurgist - Ballarat, Victoria, Australia We sadly relate the news that Bill passed away on Jan. 29, 2010. |
Hi Jeffrey.
SNAP!
Regards,
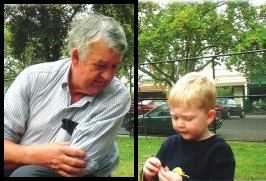
Bill Reynolds [deceased]
consultant metallurgist - Ballarat, Victoria, Australia
We sadly relate the news that Bill passed away on Jan. 29, 2010.
Multiple threads merged: please forgive chronology errors and repetition 🙂
A solution to galvanic corrosion with aluminum and stainless?
Q. I have a cast aluminum housing (alloy 380) with a 17-4 ph ss body bolted into it. After a salt spray and humidity test (this is an item for the Navy) it became apparent that I have a galvanic corrosion problem.
I am attempting to develop a recovery plan here. Looks like I need to electrically isolate the aluminum housing from the stainless steel components in the assembly.
I was thinking of anodizing the housing but am not sure if I should use type II or type III and if I need to seal the housing after the anodize. Which would give the best electrical isolation? I would then powder coat the housing. I am hoping that this process coupled with using fasteners coated with Teflon will resolve the problem.
Any advice is appreciated. The unit must withstand a 96 hour salt spray test (5%) and a humidity test of about the same length.
product designer - Sunbury, Ohio, USA
June 16, 2010
![]() |
A. Why not plate the bolt with aluminium? Klaus-Martin Hentrich- Engelskirchen, Germany A. The best solution is to hard anodize and teflon impregnate the housing and to cadmium plate the bolts. Unfortunately you run into problems with RoHS compliance because of the cadmium, but if it is for use by the Navy this should not be a concern. You do not need to paint the housing afterwards, the hard anodizing will resist prolonged salt spray better than paint. - Ramat Gan, Israel |
A. Pretreatment followed by powder coating of the aluminium housing and Teflon/other non-conducting material coated bolts could avoid the galvanic corrosion problem.
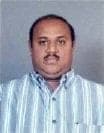
T.S.N. Sankara Narayanan
- Chennai, Tamilnadu, India
(ed.note: The good doctor offers a fascinating blog, "Advancement in Science" )
June 27, 2010
Q, A, or Comment on THIS thread -or- Start a NEW Thread