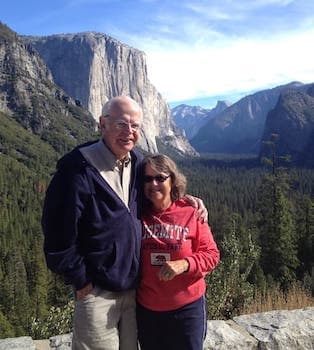
Curated with aloha by
Ted Mooney, P.E. RET
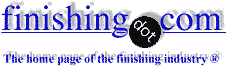
The authoritative public forum
for Metal Finishing 1989-2025
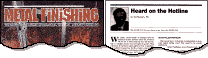
-----
Galvanic corrosion issues: aluminum and stainless steel
Q. I have an application were I have a 1/4" thick plate of aluminum in direct contact with a sheet of 304 Stainless Steel. Also I want to use an all aluminum pop rivet (both body and mandrel made out of aluminum)which will fasten the 1/4" thick plate with stainless steel. This application will see sea coast environment (but not an underwater application). Is there a chance of galvanic corrosion especially the pop rivets weakening out? I am looking for a quick solution. I looked for similar stainless steel pop rivets, but they are not available in the time frame I need to work with.
Saibal S [last name deleted for privacy by Editor]Operations Manager - Douglasville, Georgia
2004
2003
A. I think there's a 99 percent chance, Saibal, but maybe someone will offer encouragement.
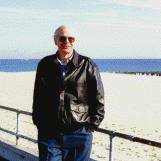
Ted Mooney, P.E.
Striving to live Aloha
finishing.com - Pine Beach, New Jersey
A. Ted is correct, check out the EMF series, you'll see that aluminum is more active than the stainless (iron) so it will corrode preferentially.
Paul Stransky- Putnam, Connecticut
2004
A. Dead certain for corrosion. You may be able to prevent it by putting an insulator between the two. Try neoprene or something similar. It must not adsorb any moisture however.
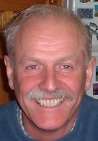
Trevor Crichton
R&D practical scientist
Chesham, Bucks, UK
2004
A. Epoxy paint the faying surfaces and pull the rivets wet (soaked, including inside) with zinc chromate primer. Not ideal but good enough for government work.
James H [last name deleted for privacy by Editor]- Jacksonville, Florida
2004
A. Aluminum in a seacoast environment is not a long term proposition. However, you may want to consider using stainless steel fasteners. The rate of galvanic corrosion is related directly to the ratio of cathode area (stainless) to anode area (aluminum). In other words a relatively small anode area like an aluminum pop rivet will be attacked much faster than a large one like the 1/4" plate. Good luck.
Fred D [last name deleted for privacy by Editor]high performance architectural metals - Cranberry Twp., Pennsylvania
2004
A. Try contacting High Energy Metals. They make metallurgically bonded structures of dissimilar metals, specifically for sea coast environments where corrosion due to dissimilar metals in contact is a threat.
Jim P [last name deleted for privacy by Editor]connector development - Wenatchee, Washington
2004
The explosive bonding sounds like a good method to bond dissimilar metals in some cases, Jim, but how does the fabrication method have any impact on galvanic corrosion? I thought it depended on factors (the emf difference between the two metals, a metallic connection, an ionic connection, and the relative surface areas) that have little to do with the connection method. What am I missing? What material would you explosively bond onto the aluminum pop rivets?
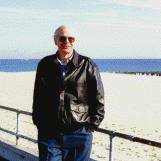
Ted Mooney, P.E.
Striving to live Aloha
finishing.com - Pine Beach, New Jersey
2004
Explosion bonding creates a covalent (metallurgical) bond between the dissimilar metals. There is no GALVANIC reaction because the metals behave as one. This does not mean that there will be no breakdown of, say, the aluminum in a corrosive environment. Secondary zincate or chromate should help.
Jim Petri- Melbourne, Florida
2005
2005
I think we're on different wavelengths, Jim: if Mr. Sengupta pop rivets an aluminum sheet to a stainless sheet with aluminum pop rivets it's not going to work :-)
Electroplating and galvanizing and some other metal finishing processes also can alloy metals together in the same way. The galvanic corrosion issue arises not in the alloy or the coating or the substrate, but if the substrate becomes exposed due to incomplete coverage, or a scratch through to the base metal because you then have a galvanic battery between two metals.
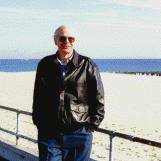
Ted Mooney, P.E.
Striving to live Aloha
finishing.com - Pine Beach, New Jersey
Q. My question pertains to the external swaging technique of fittings on tubing in aerospace applications. It is considered acceptable to swage 21-6-9 steel fittings on 6061-T6 aluminum tubing. Yet, this would appear to be a clear case of dissimilar metal contact, resulting in galvanic corrosion over time. I would like an explanation as to why this is, nevertheless, acceptable.
Zvi Burgaviation - Tel Aviv, Israel
2007
Q. Along the same theme - I am currently restoring my Land Rover Defender, which has an Aluminum body. I wanted to replace all of my external fasteners (which do touch the body) with Stainless Steel.
The previous OEM fasteners - either zinc or galvanized - rusted very quickly and the rust bled onto the painted aluminum surface. Can I still use the Stainless steel fasteners and create a barrier between the SS and the aluminum with Zinc or Galvanized washers? Any guidance would be appreciated.
- Delray Beach, Florida
January 20, 2008
A. Why can't you put a piece of rubber or fiberglass as a insulator so they don't touch.Use a sleeve for the bolt.
Tim Callanan- Belize City, Belize, Central America
January 24, 2008
Q. Ted, can you explain to my man with the land rover defender why he had the problem with the rivets.
Love your comments.
architectural metal and glass - Bensalem, Pennsylvania
February 19, 2008
A. I'll certainly be happy to try, Fred.
Picture a conventional dry cell battery still sitting in it's original packaging. The shell is made of zinc while the center rod is carbon/graphite. The two dissimilar materials are not touching each other, but there is an electrolyte, a salty liquid path between them (the black glop). Nothing is happening so far, and the battery will have a long shelf life.
Now take the battery out of the package and, with two pieces of wire, connect a flashlight bulb to the battery. We know that the bulb will light. Here is what is happening: electrons flow out of the negative pole of the battery (the zinc side), through the wire and bulb, causing it to light, and back to the positive pole (graphite) of the battery. Inside the battery, the zinc metal at the surface has become positively charged zinc ions (zinc atoms from which one or more electrons have been removed) and they dissolve and start traveling through the electrolyte glop and meet up with their electrons once again at the graphite rod and become metallic zinc once again, depositing on the carbon. There is a balance here that allows current to flow: the wire connection provides a path for the electrons, the salty glop provides a route for the positively charged zinc ions.
Note what was required for the battery to function: the two different materials for the two electrodes (zinc and graphite), an electrical path (the wiring) and an ionic path (the salty glop). You can also make a battery using aluminum for the negative pole, stainless steel for the positive pole, rainwater contaminated with road salt as the electrolyte through which ions can travel, and a physical connection between the aluminum and stainless for the electrons to travel. If you have all of those conditions you have a battery or a 'galvanic corrosion cell'.
If you can keep the aluminum from touching the stainless, as Tim C suggested, you have no path for the electrons and the corrosion stops, similarly to removing the wires from the battery. If you can keep the area totally dry and absolutely free of salt, you have no ionic path and the corrosion stops. But what usually happens with the stainless rivets in aluminum is you have everything you need for the aluminum to corrode away into the salt water as ions.
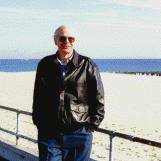
Ted Mooney, P.E.
Striving to live Aloha
finishing.com - Pine Beach, New Jersey
February 19, 2008
Q. If I am using stainless bolts threaded into aluminum parts can I prevent corrosion by putting Loctite on the threads and the heads of countersunk screws?
Ronald L Richardson- Conyers, Georgia
February 27, 2008
A. I would doubt that Loctite would give you a reliable isolation of the two metals because the threads may break through and touch, even if you are able to apply a pinhole-free layer. However, I have read sales claims from manufacturers of marine sealants that this approach works. I guess I'd say if it is for a personal item it is worth trying but if it's an engineering question for a product line, then no. Just an opinion.
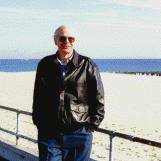
Ted Mooney, P.E.
Striving to live Aloha
finishing.com - Pine Beach, New Jersey
February 2008
A. I would suggest a product called ECK. This would be a perfect application for this product.
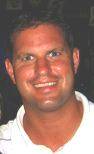
Richard Nay
- South Elgin, Illinois
April 3, 2008
Hi, Richard. My experience has been that not even gold plating will make aluminum pop rivets into a satisfactory fastener for stainless steel at all, let alone in the "seacoast environment" that Saibal S speaks of. If you were referring more specifically to Ronald R's posting, coatings of that sort do sound more promising.
Still, if you do sell your coating process to an aluminum pop rivet supplier, I'd love to track how it actually worked. Thanks.
Regards,
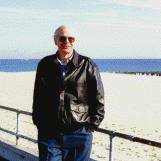
Ted Mooney, P.E.
Striving to live Aloha
finishing.com - Pine Beach, New Jersey
April 4, 2008
March 1, 2009
Gentlemen, many thanks for sharing your knowledge and experience. You solved my little problem, ss fixing to alloy mast on my chums yacht.
regards
Andrew
Just retired - Plymouth, UK
Q. Do you see issues with using threaded bronze valve on stainless steel pipe? They are closer on the potential scale than aluminum and stainless, but still are different enough that I am concerned. These are going to be in a harsh/humid environment. thanks!
Stephanie Cook- Newport News, Virginia
May 6, 2009
Q. I'm an inspection engineer in a petroleum refinery company in Egypt
I want to ask about the possibility of galvanic corrosion inside jet fuel tank for internal parts assemblies in the following 2 cases:
1- aluminium flanges with stainless steel bolts & nuts
2- stainless steel cable welded on external surface of aluminium pipe
refinery - Egypt
April 6, 2010
A. Hi, Sami. The general principals discussed here are that aluminum and stainless steel are not actually galvanically compatible because they have significantly different potentials, but the passivity of both can reduce the problem to non-problematical for non-critical applications if the area of the aluminum is greater than the area of the stainless steel (stainless fasteners on aluminum architectural features usually aren't a significant problem, but aluminum pop rivets on stainless steel sheets would be).
So I would expect that stainless fasteners on aluminum flanges would not be a significant issue. Stainless wire welded to aluminum pipes, however, sounds a bit problematical to me because there is no opportunity at all for electrical insulation, and the welding process will probably generate several different types of areas that lack any passivation.
Regards,
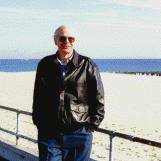
Ted Mooney, P.E.
Striving to live Aloha
finishing.com - Pine Beach, New Jersey
April , 2010
Q. Many thanks to all the contributions, they have been most informative, however back to me, I have a situation in roof location on a major London train terminus where I have a few 100 no 3 x 50 mm wide aluminium trims to install as glass retainers, these to be fixed with a stainless steel screw, we are currently proposing the use of an aluminium washer with EPDM seal to weatherproof the fixings. What are your thoughts re corrosion and long term aesthetics. Design life is 10 years min.
Martyn Smith- Dunstable, Bedfordshire, United Kingdom
June 29, 2010
Thanks James H. This is a great thread. I have been trying to answer this question for a long time for aluminum spars and stainless pop rivets that are heavy load bearing (application is sailing). The epoxy paint is a great idea. However, I am going to use plastic from a milk jug as a spacer, then soak the pop rivets as you said.
- Montauk, New York
August 31, 2010
Q. I am constructing some window awnings and before I commence the project I wish to establish some facts. Are Aluminium and stainless steel 304 screws compatible metals in an external environment?
Pete MattssonHouse renovation hobbyist - Brisbane Australia
February 23, 2011
Q. Reading on Aluminium used in conjunction with Stainless steel. I'm a technician in the telecomm industry and come in contact with many different manufacturers' equipment meant for use outside, the casings manufactured from Aluminium or aluminium castings with all the bolts and nuts always stainless steel. I'm always wondering how is it that the industry doesn't know about dissimilar metals especially aluminium and stainless forming aluminium oxide at a very fast rate. We throw away so many pieces of working electronics due to broken casings. The aluminium flakes so badly it resembles a popular breakfast cereal and the stainless steel bolts just totally seizes inside the aluminium. If the guys installing equipment remembers they put some Copperslip paste/grease on the bolts' thread, that does seem to help, although I don't know for what duration of time before it will still form aluminium oxide. Then a question: if you sit with these bolts seized in the aluminium, any suggestions on how to dissolve the oxide and get the two separated?
Andre BothaTelecommunication - Cape Town South Africa
September 9, 2011
Q. My question is, for protection of metal to metal contact between two different metals, say "steel & Aluminum", which one is better
A. Neoprene barrier
B. Polysurlyn barrier
- Jubail, Saudi Arabia
June 12, 2012
A. Hi Khalid.
To prevent galvanic corrosion the only thing necessary is to electrically isolate the two metals. For that, neoprene or polysurlyn, or almost any type or thickness of plastic will do fine.
However, the purpose of Polysurlyn (as I understand it) goes well beyond simple electrical isolation: it is intended to be a waterproof, weatherproof coating to prevent the elements from reaching the metal at all.
Regards,
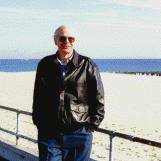
Ted Mooney, P.E.
Striving to live Aloha
finishing.com - Pine Beach, New Jersey
June 13, 2012
(you are on the 1st page of the thread) Next page >
Q, A, or Comment on THIS thread -or- Start a NEW Thread