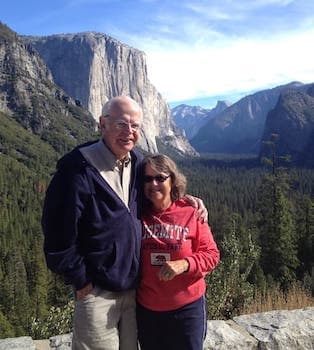
Curated with aloha by
Ted Mooney, P.E. RET
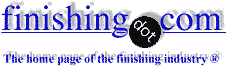
The authoritative public forum
for Metal Finishing 1989-2025
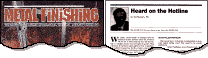
-----
Black Optical Coatings on Stainless Steel
Q. I have an application where we need to place a infrared absorbing black coating on 304 stainless steel. The coating needs to be able to survive a laser power density of about 2 kw/cm2 at the 1000nm wavelength. Do you have any ideas on where I can look for this information? Thanking you in advance.
sincerely
Mike DanielsonBattelle Northwest
1998
Q. Mike, we both seem to have a similar need. I am also looking for a heat absorbing (probably optical) black coating on st. steel that is relatively hard. I know that black chromium is used for solar heaters, and I wonder if black anodizing on aluminum would do the same.
Anyone else can comment on this topic?
Mandar Sunthankar- Fort Collins, Colorado
1998
Q. I am looking for information on "blackening" of 304 stainless steel. I am trying to increase the emissivity of 304 stainless steel by creating a dark, tenacious surface scale.
Bryan HinzieAdvanced Silicon Materials, Inc.
1998
Sorry, I have no idea of the emissivity or absorptivity ratings, but suppliers such as Heatbath offer black oxide coatings for stainless steels as well as carbon steels.
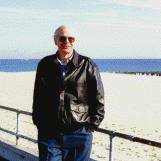
Ted Mooney, P.E.
Striving to live Aloha
finishing.com - Pine Beach, New Jersey
A. Ted I disagree with you; black oxide is no good for E and alpha. Black chromium is the best for this application. You can plate strike nickel on stainless steel, then bright nickel and then black chromium. The point is that this coating is not hard enough. Its wear resistance is not so good but optical properties are excellent.


Sara Michaeli
Tel-Aviv-Yafo, Israel
1998
A. Perhaps if you were to hard buff then color buff the stainless to a mirror finish and then perform a passivate and blackening process, you may achieve the optical properties desired?
Jeff Millsmetal finishing shop - Gorham, Maine
1998
A. The Handbook of Optics, M Bass editor, Vol 2 =>
has a chapter on black coatings (70 pages).
Also Yoder discussed a black coatings for stainless steel in the book Opto-Mechanical Systems Design [on Amazon affil links] . He says that 300 series can be "Black Passivated", and 400 series can be "chemically blackened", but I'm not sure what he means.
Morris KaufmanNational Solar Observatory, Sunspot New Mexico
1998
A. At one company where I worked we had a job which utilized lasers for timing devices which consisted of sheet brass cut into "gears". The laser needed to be completely absorbed by the teeth and then pass cleanly through the spaces between the teeth as the "gears" rotated at high speed. The coating we applied was a very high quality "black zinc", black chromate over an alkaline zinc ~.4-.5 mils thick. If one was to apply a woods nickel over the stainless, then "black zinc" over that, it might be worth a try.
Ward Barcafer, CEFaerospace - Wichita, Kansas
1998
A. We have had success using a commercially-available black spray paint called Krylon. It has high emissivity (at least in infrared region) and bonds well to metal -- in fact, it is used as a header paint for cars and as a bar-b-q paint. It can tolerate temps up to 1000 ° F. An even higher-temp. paint is VHT1500, which can tolerate a temp. of 1500 ° F, and this has only slightly lower emissivity. We have used both paints (which also come in a liquid, by the way) on 304, 310, and 316 stainless steels.
David Azevedo1999
A. Gentlemen: With regard to an infrared-absorbing coating for steel, I have successfully used Xylan 1010 polymer coating. Xylan is a paint-on liquid which is subsequently cured at temperatures no higher than about 275 ° C. It finishes at about 1 mil thick. It is similar to the "Teflon" non-stick coating on your frying pans. Xylan is manufactured by the Whitford Corp. [Frazer, PA] and is available at coating and plating houses everywhere.
Ken PlantWaters Corporation - Milford, Massachusetts
1999
A. Try AlTiN for a black coating.
Alan Smith- Lodi, California, USA
2007
Multiple threads merged: please forgive chronology errors and repetition 🙂
Matte black finish stainless
Q. We are trying to study Bose-Einstein condensate in an ultra-high vacuum (10 to the -10Tor) and are using lasers to cool the atoms. Our problem is reflection of the existing laser light on the inside of the UHV stainless steel chamber. Is there a matte black coating/finish that can be applied to stainless that won't outgas at ultra high vacuum?
Jeff VogtschallerUniversity of Wisconsin - Madison, Wisconsin
2002
![]() |
adv. ![]() Anna Berkovich Russamer Lab ![]() Pittsburgh, Pennsylvania ![]() 2002 A. Not sure if this will work but... Have you consider PVD coating of titanium carbide? Make sure the stainless surface is matte or bead blasted first. ![]() Michael Liu Taylor specialty stainless steel distributor - Dallas, Texas 2002 |
A. To reduce the reflections to closer to zero use an interference coating. This is a multilayer stack of oxides or nitride of alternating index of refraction and specific thicknesses. This type of coating can get your reflection down very low, if you laser is very high power then this coating needs to be put on a cold plate of some sort to absorb the heat.
How expensive this is depends on how much you want to reduce the reflection. Anybody doing optical coatings (and there is probably someone doing it at the university) could design a crude coating that could reduce your reflections 90%. To get better than that will take more layers, better designs, and better control of layer thicknesses. There are plenty of optical coating companies out there that could do this. Since the telecommunications market has tanked most of them have plenty of time to do this type of work.
Good Luck.
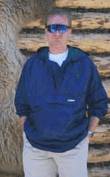
John Davis
- Berthoud, Colorado, USA
2002
2007
Q. I'm looking too. Here's an abstract I found... can you guys tell me if this is feasible for a backyard project?
Subject 141000 -- Solar Collectors & Concentrators; ; BLACK CHROME-- ELECTRODEPOSITION; SOLAR ABSORBERS-- BLACK COATINGS; ABSORPTIVITY; CHROMATES; CHROMIUM; CURRENT DENSITY; ELECTROLYSIS; EMISSIVITY; SOLAR COLLECTORS; SPECTRALLY SELECTIVE SURFACES; SUBSTRATES; SURFACE COATING; THERMAL DEGRADATION
Related Subject BLACK COATINGS; CHROMIUM COMPOUNDS; COATINGS; DEPOSITION; ELECTROLYSIS; ELEMENTS; LYSIS; METALS; OPTICAL PROPERTIES; OXYGEN COMPOUNDS; PHYSICAL PROPERTIES; SURFACE COATING; SURFACE PROPERTIES; SURFACES; TRANSITION ELEMENT COMPOUNDS; TRANSITION ELEMENTS
Description/Abstract A tetrachromate bath utilized for the electrodeposition of black chrome as a selective surface on nickel plated mild steel significantly reduced plating time.^Experiments were conducted with the tetrachromate bath consisting of 400 g/L of chromic acid, 60 g/L of sodium hydroxide, 7.5 g/L of barium carbonate for sulphate removal, 2.5 g/L of sucrose to produce trivalent chrome, and 0.5 g/L fluosilicic acid.^The mild steel plates were degreased in trichloroethylene, dried and derusted with 10 wt/vol citric acid ⇦ this on eBay or Amazon [affil links] for 2 min, rinsed and immersed in alkaline solution for 10 min, rinsed and nickel-plated at 3.5 A for 10 min, and rinsed and plated in the black chrome bath at 10 A and 20/sup 0/C.^Tests were also performed in which the electrolysis time, current density, solution composition, temperature, substrate, and anode material were varied.^Solar absorptance of the black chrome surface was within the 0.97 range and the thermal emittance was within the 0.1-0.2 range.^Increasing the concentration of fluosilicic acid in the bath to 1.0 g/L improved deposition uniformity, suitable optical properties were obtained with a charge current in the range 10-20 C/sq cm and a current density ranging 1000-3000 A/sq m. The deposits were stable in the air temperatures of 200/sup 0/C and vacuum temperatures to 300/sup 0/C, little degradation was observed after the plates were exposed to solar radiation for 12 months under stagnation conditions.^The deposits obtained were comparable to those achieved with other plating baths tested.
Thanks - maybe it's intelligible to you fellows.
Jim hardyengineering - williford, arkansas, USA
A. Hi Jim. Chrome plating is done with chromic acid. In your abstract, 40 percent concentration. Chromic acid is H2CrO4 -- that is, hexavalent chromium. Factories which do this process require medical monitoring of the employees, continuous testing of the ambient air for contamination, daily logging of the surface tension of the solution, exhaust ventilation and highly efficient fume scrubbing, and much more. Further, nobody can even count the millions of dollars already spent trying to clean this stuff out of wells and aquifers.
In my opinion it's not something for the backyard. But see our FAQ on Chrome Plating for a little more info on what it involves. Good luck.
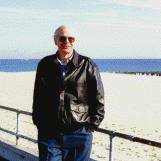
Ted Mooney, P.E.
Striving to live Aloha
finishing.com - Pine Beach, New Jersey
2007
A. Results 1 - 10 of about 552 for "black chrome" emissivity. (0.29 seconds) --from Google
High absorption at solar wavelengths, low emission at terrestrial temperatures! Black Chrome is Magic!
- San Jose California
July 7, 2008
A. Reaching high absorptivity and low emissivity in 'selective treatment' has been the focus in the solar industry for more than thirty years and the best results for different substrates can be found in the 'Solar Thermal Systems' by Dr. Felix A. Peuser. For instance, 'anodizing' speeds up oxidation on metal alloys which creates a form of 'ceramic' type insulating barrier which prevents thermal conductivity. Nickel deposit adding a black chrome has worked well but check out the Acktar Black Coating, it's the most efficient coating right now on the market, 99 % absorptivity and low emissivity.
Francois Lalive- Montreux, Switzerland
February 19, 2011
? Hi, Francois. Thanks for the info and the reference! However, "Acktar" is just a brand name for a whole series of coatings and I don't see information on their website about what it is. Are we talking about black chrome, or ultra high surface area electroless nickel, or paint, or what? Thanks.
Regards,
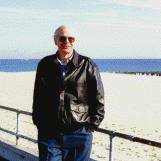
Ted Mooney, P.E.
Striving to live Aloha
finishing.com - Pine Beach, New Jersey
February 21, 2011
A. ACKTAR is an Israel Company who has developed a nanotechnology high absorbing coating deposit on narrow and thin strips to be sonically welded, I suppose, on copper serpentine type absorbers...for doing it yourself, it's out of the question. I would go back to your usual absorbing silicon base paints such as the Solkote or the Thurmalox solar paint. We also found out that black polyester powder coating works well for low budgets! Many new powder coatings are coming out now with new black absorbing enhanced powders. Check it out! All other 'higher absorbing selective coatings' by electrolytic deposit is quite expensive to do.
Francois LALIVE [returning]- Montreux, Switzerland
April 19, 2011
A. You can black anneal stainless steel with a Yag laser. The black finish has a high IR absorbing quality and the finish is not a coating it is an oxidization of the surface. Most laser marking business with a YAG 1064nm laser can apply this type of finish. We use a laser pulse rate of 40 khz on highly polished S/S as this seems to provide the blackest mark without altering the surface finish.
Paul CopelandN. G. Brown & Associates - Melbourne Victoria Australia
February 23, 2016
Q, A, or Comment on THIS thread -or- Start a NEW Thread