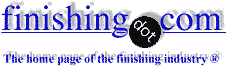
-----
Understanding Nitric Acid Passivation
Q. Can you please explain to me CHEMICALLY how and why Nitric Acid is a great passivator (over others)?
Melissa Burnett- Springfield, Oregon
2002
A. The nitrogen in HNO3 is in the +5 valence state. In reacting with the stainless steel, and releasing NO2 and NO, the nitrogen moves to a reduced valence state. If one element in a reaction is reduced, the conservation of electrons means that some other element is oxidized. Nitric acid, being both a strong acid for dissolving metals, and a powerful oxidizing agent, is ideal for oxidizing (or passivating) the surface of stainless steel.
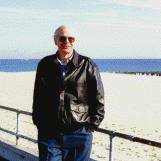
Ted Mooney, P.E.
Striving to live Aloha
finishing.com - Pine Beach, New Jersey
2002
A. Melissa: First of all, it is not true that nitric acid is a better passivator than others. There is MUCH data showing that our citric acid based formulations are superior in passivation to nitric acid. This is proven by the thousands of customers that are using it, including many major corporations around the world. It is true that nitric acid is an "oxidizing" acid, meaning that it oxidizes (valence wise) the surface of the steel. If things go wrong, you can release NO2, which is very dangerous. The best passivation of stainless steel is attained by removal of all exogenous materials and free iron and iron oxides from the surface, then chromium enriching the surface layer so that it can be oxidized in the air to form a good chromium oxide layer (the passive layer). The best results can be attained using formulations other than nitric acid, although nitric acid has worked for many years as the old standard in the industry.
adv.
Let us know if we can help you. Lee
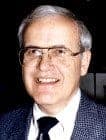

Lee Kremer
Stellar Solutions, Inc.

McHenry, Illinois
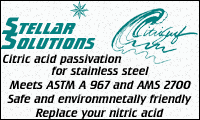
2002
A. Ted Mooney gave you the accurate theoretical explanation for "passivation" of stainless steel. I have been in the industry 53 years and hate the words activate and passivate. To the theory person, activate means reduce the oxides on the surface of the metal so that we can plate, phosphate, or bond something to the nascent surgically clean metal. The word passivate mean just the opposite, i.e., to OXIDIZE the surface of the metal.
In the case of "stainless steel", it is "stainless" because the nickel in/on the surface is control oxidized and will not further oxidize (corrode). To the average machine shop operator the passivation of stainless steel means to merely pickle out the iron from the surface and increase the area of nickel on the surface. For this definition many shops are now using citric acid to "passivate" - but all it does it remove the iron from the surface. citric acid does NOT oxidize the nickel. Complete passivation means to control oxidize the nickel in the surface -- this you do with a strong oxidizing agent like 50% Nitric Acid at room temp or 30% Nitric Acid at 120 °F. Sometimes a dichromate is added for some alloys - for more info go to ASTM and/or the Metal Finishing Guidebook.
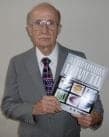
Robert H Probert
Robert H Probert Technical Services

Garner, North Carolina
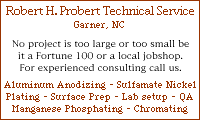
2002
Q. What about Nitric Acid's reaction and oxidative properties with non-metallics?
Melissa Burnett [returning]- Oregon
2002
A. Please visit www.finishing.com/faqs/sstpass.html for just the faqs, (ma'am!) about organic acids being formed, causing destruction of parts in the passivation tanks, and lots of other theories which have been suggested to explain this problem.


Tom Pullizzi
Falls Township, Pennsylvania
2002
A. The chemistry of the surface of stainless steel, since it is an alloy, is as difficult as the number of grades of stainless steel. Most grades of "stainless steel" do not contain nickel. The real world of "passivation" is an attempt to make the surface of stainless passive to corrosion, and the only real measure of how passive the surface is, is to test it for corrosion resistance.
I have been around the industry for 45 years and have been exposed to the wives tale that you have to use an "oxidizing acid" in order to passivate stainless steel. It is simply not true, as is proven by the test results of many major corporations around the world.
The degree of passivation is generally inversely proportional to the amount of iron in the surface layer. It is a LOT more complicated than that with the various grades. So we try to increase the percentage of chromium (and nickel if present) to form the toughest "passive" layer of chrome oxide (and nickel oxide) possible. The simple fact is that citric acid formulations, when formulated correctly, do a better job at that than nitric acid. This is proven by the corrosion tests and ESCA and AES tests run by our customers. Nitric acid works fine, and that is why it has been used for many years; but new technology has shown that it is not the best. Whatever your opinion on the method of passivation, the test data is the only important thing to companies who need corrosion resistant parts.
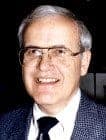

Lee Kremer
Stellar Solutions, Inc.

McHenry, Illinois
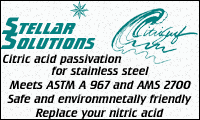
2002
If the test data is the only thing that's important, in which journals can we find it published, Lee? This subject has been debated in the abstract here so many times that it's getting silly :-)
opinion! Tens of millions of dollars are thrown away each year by the EPA funding endlessly repetitive "pollution prevention studies" for the metal finishing industry that consist of nothing but rearranging the pages of a hundred previous "studies". We all despaired of that nonsense decades ago and nobody ever even reads them. Yet here we have the critical question of whether citric acid based products can really replace dangerous and polluting nitric acid based products for stainless passivation, and nobody can point us to any EPA funded research at all?
C'mon EPA Administrator Christie Whitman! We know that what these "studies" are really about is just a game where the beltway bandits are awarded grants to repay them a hundred times over for their campaign donations, but can't you at least ask that they include some actual citric vs. nitric TESTING in return for these millions of dollars of foolishly spent tax money? :-)
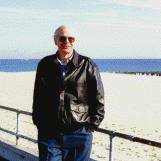
Ted Mooney, P.E.
Striving to live Aloha
finishing.com - Pine Beach, New Jersey
2002
A. A very good paper was published in Nature on the 14th Feb 2002 by the Department of Materials, Imperial College of Science, Technology and Medicine in London called "Why stainless steel corrodes". The results in the paper provides indirectly the answers how passivation works and may even provide the information needed to produce a better passivator and cleaner for Stainless Steel.
Steven Scarpin- Melborne, Victoria, Australia
2002
A. To throw in my two cents worth. Last time I did I was dead wrong. I based my assumption on Hex Chrome in HCl as valance 6 based on gut feel. Randy Fowler was on target. Here I based my option based on testing of one passivation method over the other in a humidity cabinet operated to ASTM spec. citric acid works better than Nitric acid for 17-4 pH. citric acid is the only method we could pass a trace sulfide test on 303 stainless steel. I have never damaged a part and the humidity cabinet test is at least the same for 400 series stainless steel using citric acid .
As to other sources I will look it up if anyone is interested but Cleaning Magazine did a very good article in about 1996 Citing Bauer and Laumer's work with citric acid . The test results are impressive.
Jon Quirt- Fridley, Minnesota
2002
A. Ted:
I do not know about EPA's millions spent to come up with more environmentally friendly answers. I can supply you with lots of data that we and our customers have obtained in testing. There are a number of problems, as always, in getting "independent" peer reviewed publications to print data.
First, 99+% of it is done by companies who want to get rid of the nitric acid, but are not exactly keen on telling all of their competitors how they did it.
Second, independent organizations like SAE, AESF, ASTM, etc. cannot print data using a trade name. Since we cannot give the complete details of our formulations it is usually impossible to print data except for just "citric acid ", which solves some problems but not all-- and there are a number of problems with just citric. There will be a presentation by Boeing at the August AESF Aerospace Meeting in Orlando on their tests showing how citric is better than nitric. This will be published as a paper from the meeting.
There is a larger study by a large Research Lab in Europe (NMI) funded by the surgical industry in Europe which is due to be published any day now. This study, again, shows the advantages of "@@@@@@@@" (I can't mention the name) over nitric acid and the reasons why it is better. I have seen the raw data, but the final report is near completion. This will be another independent paper.
There are other sources, and mounds of data using ESCA & AES data showing this. Give me a place to publish these using the trade names (because I can't say that citric acid by itself gives these results) and we will gladly publish it.
I am happy to talk to anyone about this, and have supplied some of this data to dozens of Finishing.com patrons who have contacted me requesting it after reading your site.
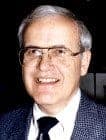

Lee Kremer
Stellar Solutions, Inc.

McHenry, Illinois
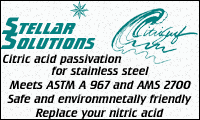
2002
2002
A. Thanks, Steven, I see the abstract at www.nature.com/nsu/020211/020211-6.html and it sounds not only very interesting, but truly significant.
Jon, I appreciate the report of your test results; and, yes, damage to parts by nitric acid passivation is indeed widely reported. The article you reference is apparently Balmer, Kenneth B., and Martin Larter. "Chelants Prove Practical for Cleaning and Passivation of Stainless Steel Parts." Precision Cleaning Magazine, no. 27-29 (November 1994); thanks. However, this is the kind of sales-oriented, vested-interest article "that don't impress me much" with its references to "fuming, suffocating...very toxic ... severe tissue burns ... serious consequences ... strongly adherent and potentially corrosive phosphate salts..." and not a single negative word about citric acid , which is "normally approved for discharge directly into the local sanitary sewer system". Sorry, but they need to learn the principle of "damn the competition with faint praise" because I consider this article worthless sales spin :-)
Lee, my first response above was in reply to what I interpreted as a student science question about how oxidizing acids work. I was explaining why nitric acid will oxidize materials while other acids like hydrochloric will not. I was not attempting to defend nitric acid over citric acid for the commercial passivation of stainless steel. I hate nitric acid!
My personal "gut feel" (as Jon puts it) is that proprietary citric acid passivation is a better answer than nitric acid most of the time and perhaps all of the time. However, I want to see objective testing by people without vested interests, and I do not accept your second point. There is plenty of precedent for objective, peer-reviewed, research into the efficacy of proprietary metal finishing solutions. Different journals handle the treatment of brand names in different ways, but I can point you to dozens of objective published tests of proprietary chromating solutions and brighteners, proprietary alternatives to phosphating, etc. in the metal finishing literature -- even specs like AMS 2488 written around a proprietary process. I look forward to those Boeing and NMI reports--thanks!
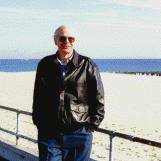
Ted Mooney, P.E.
Striving to live Aloha
finishing.com - Pine Beach, New Jersey
A. Hi Melissa!
Re your query about the effect of nitric on non-metallics, ah, that depends on the temperature, on the concentration and on which of the MANY acid resistant thermoplastics are used and, most important, on the welding thereof.
But for the record, when a pharmaceutical grade nitric is further ENHANCED to achieve a purity of 0.0009% or less, the tank containing it is made of plastic. Any metal would contaminate the nitric. I can't give you the Company's name (am not allowed to by finishing.com precepts) except to say it is in Canada and on Vancouver Island.
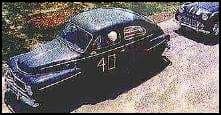
Freeman Newton [deceased]
(It is our sad duty to advise that Freeman passed away
April 21, 2012. R.I.P. old friend).
2002
A. Hi guys,
I'm a metallurgist by trade, but an expert by no means. I do have 12 years experience in corrosion and more specifically, the last 10 years of working as an engineer for several medical device companies in Manufacturing, R&D, and Supplier Quality where I've worked with dozens of machine shops and Metal Injection Molding Shops. This citric vs. nitric thing comes up ALL the time. Primarily because citric is cheaper from our suppliers' standpoint. My experience has been that citric does just as good of a job as nitric most of the time, but not ALL the time. There are two conditions where I have seen that citric is inferior to nitric acid passivation and I have seen both of these conditions with this issue on numerous parts at three different companies. The first is if you are trying to passivate a metal injection molded (MIM) part. The gate location of a MIM part is highly susceptible to lower corrosion resistance, I think primarily because it's a relatively rougher surface that may not get all of the appropriate pre-passivation cleaning and post-passivation neutralization that it should. The gate is like a big pit and traps contaminants inside. The MIM metal we were using was 17-4 PH SS. The other instance that I have seen dozens of times where we tried and tried to make citric passivation work, was in laser marked stainless steel. It didn't matter if it was laser marked 304, 316L, 410, 420, or 455. Now that's not to say that achieving passing results with citric acid passivation is impossible. It's just that the time and effort required to work out all of the bugs was not worth the dollar savings vs. nitric. On both the MIM parts and the laser marked parts (sometimes alpha-numeric for identification, and sometimes inch long circumferential depth marking bands), 3 rounds of laser, cleaning, and passivation process optimization were not enough to get passing results with citric. We then changed to nitric and passed testing on the first try.
Rule of thumb is - test for your specific part to prove it out and don't assume anything!
- San Jose, California, USA
January 27, 2011
Thanks for a great posting Dwayne!
Regards,
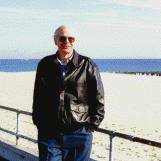
Ted Mooney, P.E.
Striving to live Aloha
finishing.com - Pine Beach, New Jersey
Must food tanks be passivated, or is alkaline & acid cleaning enough?
To prepare a brand new tank just received in the food plant, is it necessary to passivate with nitric or can we simply clean it with an alkaline cleaner and then a phosphoric cleaner? The tank is not part of a system.
Lorry BoeFood plant Sanitation Tech Rep - Madera, California, USA
August 15, 2014
A. Lorry,
Necessary according to whom? In my experience, companies usually have a policy requiring passivation, or perhaps that's based in some FDA requirement that I don't know the details of. If you don't want to passivate and you're not concerned about corrosion, then there's no particular industry rule I'm aware of that says you have to.
However, if you plan to clean with phosphoric acid, you may as well just use a citric acid based formulation instead, and then you will be passivating.
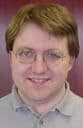
Ray Kremer
Stellar Solutions, Inc.

McHenry, Illinois
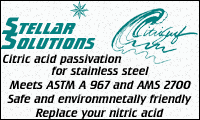
September 19, 2014
Q. What is the difference between Nitric 1 and Nitric 4 passivation?
Mark SutherlinMedical device Mfg. - Indianapolis indiana US
October 9, 2019
A. Mark,
Depends on which standard you are talking about. The old military passivation standard QQ-P-35B had six sets of process parameters (bath concentration, time, temperature, etc.) called "types", labeled with Roman numerals Type I to Type VI.
The next revision, QQ-P-35C, removed Types I, III, IV, and V, while adding Types VII and VIII. The C revision lasted for a while, then QQ-P-35 was cancelled and replaced by two separate but similar standards.
ASTM A967 took the four QQ-P-35C types (II, VI, VII, and VIII) and renumbered them as Nitric 1 to Nitric 4, plus a new Nitric 5 to allow process parameters not listed to be used as long as the parts pass the acceptance test.
AMS2700 brought back the removed types from QQ-P-35B, for a total of eight, still labeled as "Types" but with Arabic numerals now, so Type 1 to Type 8, under Method 1. (As opposed to Method 2, for citric acid , which is not subdivided into types.)
Since you say "Nitric 1 and Nitric 4", I presume you are referencing A967, but you should confirm that and then acquire a copy.
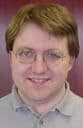
Ray Kremer
Stellar Solutions, Inc.

McHenry, Illinois
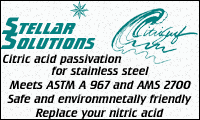
October 15, 2019
Q, A, or Comment on THIS thread -or- Start a NEW Thread