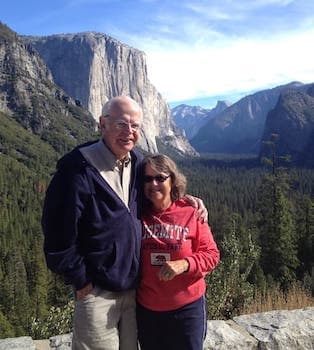
Curated with aloha by
Ted Mooney, P.E. RET
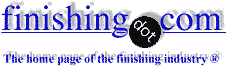
The authoritative public forum
for Metal Finishing 1989-2025
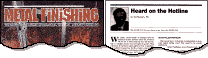
-----
Black oxide on stainless steel is rubbing off
Q. 1) What is the nature of the black oxide on stainless steel?
2) Is there any method, such as plasma or electrochemical methods, to increase the amount of chromium oxide - hydroxide content on the surface?
Thanks,
Diane Dang- Menlo Park, California
2001
2001
A. Diane:
I am not sure what you mean by the black oxide on stainless steel. Are you talking about a black oxide treatment, or are you talking about a "blackening" of the surface (dull gray) that can occur with the wrong procedure. It is not uncommon for this to happen with some grades of stainless with nitric acid passivation.
adv.
If you contact us we can determine the answer to your question.
You can significantly increase the Chromium oxide amount on the surface of stainless steel by correct passivation. We have seen chrome oxide: iron oxide ratios as high as 13:1 on some tests using CitriSurf passivation of 316L. Normal ratios are not that high, but higher than you can get with nitric acid.
Electropolishing before passivation will help to produce the optimum results. There are many systems available from vendors to the trade.
Regards,
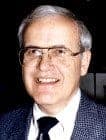

Lee Kremer
Stellar Solutions, Inc.

McHenry, Illinois
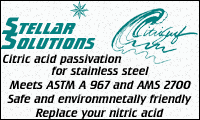
A. Hi. I would agree with Lee that if you can tell us more about your actual situation, we can probably be more helpful. There are many ways to get a black color on stainless steel if that (rather than avoiding a black color), is what you are trying to do: black nickel, black electroless nickel, zinc-iron with black conversion coating, black rhodium [adv: black rhodium plating solution on eBay or Amazon [affil links] , ruthenium plating, etc. And yes there are several black PVD coatings as well, including diamond-like carbon. But if your only concern is more chromium oxide-hydroxide on the surface, certainly black chromium plating would be a good way to go.
Regards,
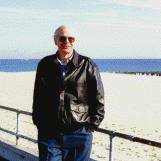
Ted Mooney, P.E.
Striving to live Aloha
finishing.com - Pine Beach, New Jersey
Red rust through black oxide on SS part
Q. During a recent investigation concerning the use of a black oxide process on a 304 stainless steel part, our department noticed red/orange spots on the surface of the part subsequent to 72 hours of ASTM B117 salt-fog. The salt spray test was run to confirm the proper passivation of a weld on the part. However, a phenomenon that appears similar to rust was observed in areas far removed from the weld.
It is our understanding that the black oxide process does not adversely affect the chrome oxide layer of the stainless steel and as such does not affect the natural corrosion resistance of the material. If this is a true statement, what are some possible sources of the spots and what can be done to eliminate this problem? At this point, I do not have any detailed information on process used to apply the black oxide.
Any insight into this issue would be greatly appreciated.
Mark Thomas- Oshkosh, Wisconsin
2002
A. Black oxide on stainless requires activation using a warmed acid prior to oxidizing. While this activation isn't intended to degrade the chrome oxide layer, making black oxide pass salt spray is tricky and generally requires some secondary sealing such as weak chromic acid dip or dry touch oil. The MIL spec for blackening stainless steel, namely MIL-DTL-13924 [⇦ this spec on DLA], Class 4, requires 96 hour salt spray minimum resistance when applied over austenitic steel (e.g. 304, 316, etc.). We routinely pass this requirement (however, these are not assemblies like yours which entrap the corrosive salt solution).
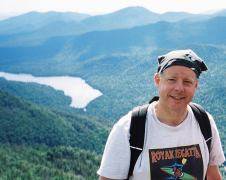
Milt Stevenson, Jr.
Syracuse, New York
2002
Q. Thank you Mr. Stevenson for your response. In your response, you mention that "the activation is not intended to degrade the chrome oxide layer." However, if a 304 part can now only go 96 hours in salt spray until red rust it would appear that that is exactly what happens. In my salt spray test, however, the apparent corrosion has not progressed any further despite several hundred hours of additional salt spray. Is the apparent detrimental effect of the activation somehow temporary? Does the 304 material eventually re-passivate such that corrosion is once again prevented? Once again, any insight into this phenomenon would be greatly appreciated.
Thanks,
Mark Thomas [returning]- Oshkosh, Wisconsin
2002
A. Hi Mark. Maybe you sent the wrong pic or I accidentally swapped it, but I don't see a black finish. And, although I see a little tannish tone, I don't see rust. Regardless, the fact that no further deterioration took place despite several hundred hours of testing is strong evidence towards an assertion that the parts have indeed not failed the salt spray test:-)
ASTM B117 says nothing about what constitutes failure. Do you claim compliance with some spec? That's what guides the interpretation. If no specs pertain, then some other specs like the MIL-DTL-13924 [⇦ this spec on DLA] quoted by Milt might offer you some guidance about how you might look at the situation, but I'd probably call it an acceptable blush rather than rust :-)
Regards,
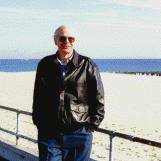
Ted Mooney, P.E.
Striving to live Aloha
finishing.com - Pine Beach, New Jersey
Multiple threads merged: please forgive chronology errors and repetition 🙂
Q. We are have been using a stainless steel handle w. black oxide finish on our electronics assemblies. Recently we have had batches of these handles come in with the black oxide finish rubbing off and the handle looking splotch-y. Based in what I know about black oxide finishes they should be more robust than this however I have recently heard that this problem can happen with cold-process black oxide.
Is this normal?
Thanks.
Steve Ferranti- Dallas, Texas
2002
![]() |
A. Hi Steve. I'm not sure whether you are implying that your vendor switched to cold blackening or not, but yes, that can lead to smutty, marginally adherent coatings. Cold blackening is not true black oxiding; rather, it's the deposition of a black selenium-based compound. These are your parts, and your plater should not have carte blanche to change the process applied to your parts. I suggest that you find out what he was doing formerly, and what he is doing now ... and that you write a spec that makes him or another shop do it the old way. You also need to check that the grade of stainless steel hasn't been changed. If you are just buying standard parts from a catalog and have no control over the specs, you may have to find another supplier :-) Luck and Regards, ![]() Ted Mooney, P.E. Striving to live Aloha finishing.com - Pine Beach, New Jersey 2002 A. This is common with cold blacks. It can also happen with hot blacks for stainless, especially if the surface is not properly activated. Steve Loudermilk- Springdale, Arkansas 2002 |
Q. I would like to know how to "Blacken" stainless steel chemically? It will not react to parkerizing. I heard that a Sodium Dichromate or Potassium Dichromate Dip will work. Is this the only way besides painting it. I want to keep the restoration of firearms historically correct but perhaps up to date. I am mainly involved with Zinc Phosphate and Manganese Phosphate coatings.
Thank you,
Chris ConlonFirearm Restoration - Avon, Indiana
2004
A. Cold black for SS:
1 lit H2SO4(1,55 gm/cm3)
Na2Cr2O7..........13 gms
temp.18-25 °C, 5-10 min.
Good luck!
Goran Budija- Cerovski vrh Croatia
2004
Need Sodium and Potassium DiChromate
RFQ: [Where to get] Sulfuric Acid H2SO4 Sodium DiChromate Na2Cr2O7 Potassium DiChromate (to blacken stainless steel parts)
Chris Conlon [returning]Firearm Restoration - Avon, Indiana
2004
Ed. note: This RFQ is outdated, but technical replies are welcome, and readers are encouraged to post their own RFQs. But no public commercial suggestions please ( huh? why?).
A. Hi, Chris. You should be able to find distributors of metal finishing chemicals in our Directory or the yellow pages of a nearby city or on google. But you do need to know, in case you don't, that Goran's posting is intended for professionals who have received Haz-Mat training.
Dichromate (chromate, chromic acid, hexavalent chromium) are toxic and carcinogenic materials. And once you open them you become legally responsible for them forever no matter how much you pay to dispose of them (EPA 'Cradle to Grave' regulations designed to address midnight dumping). Most people have heard of Erin Brockovich and the attention being given to hexavalent chromium, so read up before you buy the stuff :-(
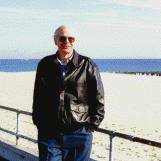
Ted Mooney, P.E.
Striving to live Aloha
finishing.com - Pine Beach, New Jersey
Black Oxide on Stainless: Smut residue problem
2005Q. As a small gunsmithing shop, I have recently been attempting Hot Black oxide on Stainless Steel: Barrels, Frames, small parts, etc. Mostly 416 type SS.
While my attempts have been producing a deep rich and uniform color, There is a significant amount of black residue(smut)left on the parts that must be wiped off during reassembly. The smut seems to lessen as the post treatment(water displacing oil)is wiped dry. But seems to reappear once a more suitable gun oil is applied for exterior corrosion protection.
Process being used:
Brownell's Oxynate 84
⇦ this on
Brownells affil link]
(similar to Heatbath's PX5) - 5 lb salts - 1 gal water boils at 245 °F
Media blast - 100 gt Al Oxide - desired matte finish
Dicropan cleaner
Water rinse
muriatic acid
⇦ this on
eBay or
Amazon [affil links] dip - 2-5 min.(smutting occurs with or without this step)
Water rinse
Hot dip Black Oxide -
Water rinse
Blow dry
Water displacing oil
Thanks in advance for any helpful replies.
- Gardnerville , Nevada USA
Black Oxide on stainless finish WITHOUT sulfur
Q. My company currently uses black chromium plated stainless (type 304 and 316) parts for experiments, but would like to replace this with a less expensive and more robust black oxide process. The blackening is for optical absorption, such as laser dumps, laser baffles, and spectrometer view backgrounds. The parts are in a ultra-high vacuum and often get up to 350 deg C. The problem is that tests have shown that the black oxide parts contain traces of sulfur that "outgas" in the vacuum and sulfur is extremely problematic to our experiments. It seems that the "activators" that are used prior to the blackening salts use sodium bisulphate. Is there a black oxide process for stainless steel that is sulfur free? What happens if the activator is not used prior to using the salts?
Thank you.
- San Diego, California
2006
Can 15-5 PH Stainless H900 be Black Oxide Coated
Q. We are building a prototype for a military application, and would like the appearance of the final prototype to be black in color. Most of our exposed stainless parts are 15-5 PH age hardened to condition H900. Looking through MIL-DTL-13924
[⇦ this spec on DLA] (Coating, Oxide, Black for Ferrous Metals), section 6.3.4 states that corrosion resistant steels of MINIMUM 17% Chromium and 7% Nickel can be black oxide coated, but does not specify if stainless steels of lesser concentration can be black oxide coated. My question is, will the black oxide treatment work successfully on 15-5 PH stainless steel?
Thank You
Prototype Designer - New York, New York
April 29, 2008
A. The trick in the mil spec is that all stainless steels, austenitic, martensitic and PH can be black oxided, however, the spec also requires Class 4 black oxide on stainless steel to be able to withstand 96 hours of salt spray which is why they've limited it to austenitic grades with particular chrome contents (i.e. those that are capable of passing the corrosion resistance requirement). Fact is that once the natural occurring protective layer (i.e. passive layer) is removed, the stainless is rendered active enough to accept black oxide, however, there are very particular methods of activation depending on the nature of the alloy being blackened and the conventional black oxiding baths for steel will not work.
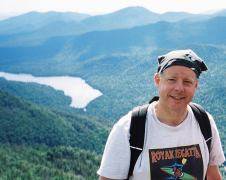
Milt Stevenson, Jr.
Syracuse, New York
May 18, 2008
(you are on the 1st page of the thread) Next page >
Q, A, or Comment on THIS thread -or- Start a NEW Thread