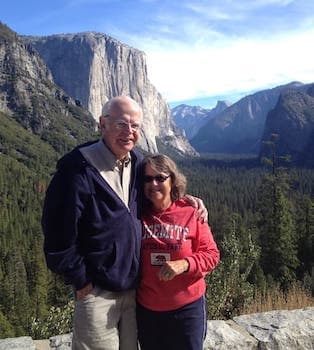
Curated with aloha by
Ted Mooney, P.E. RET
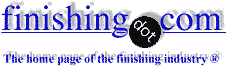
The authoritative public forum
for Metal Finishing 1989-2025
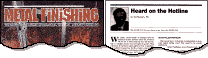
-----
Stannate (Tin) Plating Process
Q. What is a stannate process? I think it is also know as a 10-step process involving Tin and Cyanide. Who in the U.S. uses this process?
Thanks,
Brandon Hellenbrand- Fairburn, Georgia, USA
A. Hi, Brandon
The chemical symbol for tin is Sn. Practically, 'stannate' just means alkaline tin electroplating as opposed to acid tin plating (sometimes called stannous sulphate). There might be cyanide somewhere in the overall plating cycle, or in older versions of the stannate process but there need not be. Good luck.
Regards,
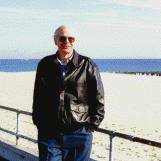
Ted Mooney, P.E.
Striving to live Aloha
finishing.com - Pine Beach, New Jersey
A. Let's read about the stannate process:
The Immersion Deposition Process, D.S. Lashmore, Aluminum Finishing Seminar,Vol II, St. Louis, MO, 30 Mar - 1 April, 1982, Aluminum Association, Washington, DC. and Pretreatment for Plating on Aluminum Using The Stannate Process, Jongkind and Seyb, ibid.
Related stuff for tin plating:
Control of Anodes in Alkaline Tin Plating, M&T Chemicals, Rahway, NJ, Technical Data.
Anode maintenance in the Alkaline Stannate Tin Plating Bath,
Lowenheim, Metal & Thermit Corp. New York, NY., reprinted from March 1951 issue of Metal Finishing.
Technical Bulletin, M&T Chemicals, Rahway, NJ, Alkaline Tin Plating with M&T Stannates


Tom Pullizzi
Falls Township, Pennsylvania
A. The stannate process is not going to make your aluminum adhesion problems go away.
Todd Osmolski- Charlotte, North Carolina, USA
Stannate process is too slow
Q. Does anyone have a process for speeding up the potassium stannate process using Tin and Potassium Hydroxide?
Mark McCaugheyMetals & Additives - Indianapolis, Indiana, USA
2007
A. Hi, Mark. I presumed the original inquiry was about a stannate plating process (alkaline tin electroplating) but the responses (from Tom regarding Lashmore's paper, and from Todd regarding adhesion) lead me to believe it might instead be about an alternative to zincate for preparing aluminum for electroplating (such as Atotech's Alstan process) -- but it's still not clear to me.
So now I have to ask which topic your stannate inquiry is about? :-)
Regards,
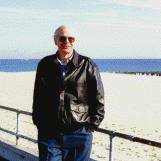
Ted Mooney, P.E.
Striving to live Aloha
finishing.com - Pine Beach, New Jersey
2007
Missing book pages about filming the anodes
Q. I've purchased the fourth edition of Electroplating Engineering Handbook ⇦ this on eBay, AbeBooks, or Amazon [affil links] and wouldn't you know, the exact page I need was misprinted with a different page. The publisher will not help me out. Can anyone summarize plating bath tables 25 and 26 for Tin (pages 256, 257)? Is there any mention of brighteners for Alkaline Tin (sodium Acetate?), and the purpose of "Filming" the anodes?
Larry SmithPlating Engineer - Tucson, Arizona, USA
2007
A. We sent you the missing pages, Larry. The acetate is mentioned, as is the necessity for filming the anodes -- but not why or how. That is covered in full detail though in the Garden State Branch AESF Electroplating Course Manual" in the "Tin Plating" chapter by F.A. Lowenheim. In brief, the anodes will dissolve as Sn+2 instead of Sn+4 if the anodes are not 'filmed' at high current density. Quoting Lowenheim:
"The only critical factor in operating stannate tin baths is the proper control of the anodes. With proper anode control, operation is easy and trouble-free; without proper anode control, good results cannot be obtained".
Good luck.
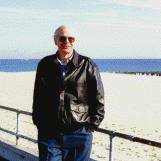
Ted Mooney, P.E.
Striving to live Aloha
finishing.com - Pine Beach, New Jersey
2007
Need Alkaline Tin Plating Process Chemistry
RFQ: Hi I am looking for supplier who can supply us the following chemical Alk Tin Plating with Stannates ( mix with Potassium Hydroxide)
We want to plate on Carbon steel material. product OCTG oilfield Coupling
Type of Plating ID plating and Thickness about 64 to 104 micron.
We used to buy the chemical in Singapore. Presently there is no company selling in Singapore
Please kindly advise us where we can buy.
plating shop - Singapore
March 26, 2009
Ed. note: This RFQ is outdated, but technical replies are welcome, and readers are encouraged to post their own RFQs. But no public commercial suggestions please ( huh? why?).
Volts low/Amps High in Stannate Tin Plating
Q. Hello,
I am manufacture of brass casting and do tin plating for for corrosion protection. We have been having problems with the tin anodes not holding the film. We film the anodes initially with a surge of 8-10 Volts and this starts the film, but shortly there after we will lose the film. We also have notice the amps are rather high 150 amps with the volt at 4-5. The solution is 10oz gal on the Stannate tin and the Sodium Hydroxide is 1.2 oz per gal. The anode to cathode is 2 to 1. What could cause the amps to increase with the volts so low?
Thanks
mike
Manufacturer - St. Louis
September 22, 2010
September 24, 2010
A. You probably need to reduce the number of anodes to increase the anode current density and voltage. That should be all that is needed.
If that is not sufficient to get a good gold colored film, you may need to reduce the sodium hydroxide concentration a little with acetic acid
⇦ this on
eBay
or
Amazon [affil links] .
consultant - Cleveland Heights, Ohio
Filtration for alkaline tin plating bath
Q. We have a problem with sludge build up in our alkaline tin plating process and are considering a continuous filtering process to remove it. If we do will this:
1) Improve the quality of the plate?
2) Decrease the plating time?
3) Reduce the amount of tin used?
Also an answer as to "why" on all 3 questions would be most appreciated.
carbon brush manufacture - Greenville, South Carolina
November 4, 2010
A. Hi Larry. In his rather exhaustive coverage of Alkaline Tin Plating in the aforementioned "Garden State Branch AESF Electroplating Course Manual", Lowenheim never even mentions filtration. It is not necessary, but whether it should be employed is probably a matter of your Philosophy of Quality ... some shops feel filtration should be employed on all process tanks, and D.I. water used everywhere, and that failing to use these measures is old fashioned and loose. So, in answer to your questions --
1). Yes, it can improve the "quality of the plate" by insuring no particles are occluded.
2). No
3). No.
Regards,
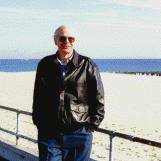
Ted Mooney, P.E.
Striving to live Aloha
finishing.com - Pine Beach, New Jersey
October 2013
Is stannate the answer to zincate adhesion issues?
Q. I am drawn back to Todd Osmolski's comments. Here's my situation.
I used the double zincate system to plate Mid P EN then finish off with rhodium plating on 2024 Al alloy. I have adhesion problem (about 10 %).
I've been told that replacing the first zincate step with an acidic tin immersion coating may help improve the adhesion problem. Or is adhesion problem on alloy 2024 just 'the nature of the beast'.
- Penang, Malaysia
November 11, 2010
A. If you add an alkaline nickel strike, at near room temperature and then go into the regular EN, I predict that your rejects will drop to a very low number (near zero) The ammonia
⇦ this on
eBay or
Amazon [affil links] smell is about the only drawback and the results are fantastic. With one short rinse, the slightly alkaline film of water helps to kick off the EN.
Note, if you do not have a heavy use of the strike, consider adding cooling or you will plate out on the tank during idle periods. It is quite active at temperatures around 75 °F.
- Navarre, Florida
November 11, 2010
Q. Thank you, James. Many commentators of this site are proponents of an alkaline EN strike. Does your statement hold true even if the regular EN is maintained at 1~3 MTO for zincated 2024 ?
SK Cheah- Penang, Malaysia
November 16, 2010
A. It certainly does. A big reason is that the alkaline EN strike does not eat off any (very little) of the surface of the zincate as the acid EN will do quite rapidly. 1-3 MTO's on EN is very expensive. The strike should allow you to go to 3-6 MTOs If you can load the EN tank to at least the minimum recommended surface area to be plated. Also, try to always have stuff in the tank as soon as it gets to temperature. Try to get the temperature down as soon as possible after the last part comes out. Cooling is great if you have it. I always saved my last water make-up for when the last part came out of the tank. Bad memory remembers it lowering the temp by 5 - 10F. Lowering the temp by 10F as soon as the last part comes out will probably get you an additional MTO as well as the nitric acid tank stripping is a lot easier.
James Watts- Navarre, Florida
November 16, 2010
James, thank you very much. That's a whole load of valuable information.
- Penang, Malaysia
November 17, 2010
Alkaline Tin Plate Build-Up Problems
Q. I have recently been trying to achieve an alkaline tin deposit at multiple mils thickness (1-2) that is uniform and will clean up to a bright, smooth finish when polished, per customer requirements.
The issues that are being encountered are that the deposit it is either too rough, and will yield a frosty appearance when polished in certain areas, or too pitted, and they will not polish out. We have been able to minimize the problems by plating at low CD, but it is still present to a degree.
We have done some testing with a new solution which shows that the nice finish is do-able, but not with our present bath. And even if we were to make up a new solution to process this work, we do not know what is causing the failure, and will not be able to prevent recurrence of the problem down the road.
So my question would be, are there known contaminants or tank controls which may cause what we are seeing? And are there any recommendations for how to control them?
Thanks!
Process Engineer - Dayton, Ohio, USA
September 19, 2013
A. Stannate plating baths are great for thin deposits, like 0.2-0.4 mils, but tend to become rougher and treed on thick deposits. To plate 1-2 mils and get a smooth deposit, you may have much better luck with an acid tin plating bath.
Lyle Kirmanconsultant - Cleveland Heights, Ohio
September 26, 2013
What is "Plating Grade" Sodium Stannate?
Q. What is the difference in Sodium Stannate Grades? I am working to a Boeing spec (BAC5717) and it states "Sodium Stannate - Plating grade or better".
Bob Fosterengineering - Chicago, Illinois
December 22, 2017
A. Hi Bob,
Plating grade Sodium Stannate usually refers to Sn assay ≥42% with all impurities (Pb, Sb, As, Fe, NO3, free alkali, etc.) sum up together ≤3% by wt.
Regards,
David
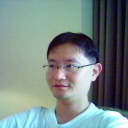
David Shiu
- Singapore
January 17, 2018
Q, A, or Comment on THIS thread -or- Start a NEW Thread